
Fercometal, based in Valencia, Spain, has been in business for more than 50 years. Started by Don Federico Rodríguez Súarez, the company is now run by his sons, Federico and Fernando. The third generation of the family—Federico’s daughters—also are involved in the family business of buying, processing and selling scrap metal.
Fercometal specializes in nonferrous, including aluminum, copper, brass, bronze, stainless steel, lead and zinc. A recent expansion featuring equipment from the Italian company Bano Recycling Srl is allowing Fercometal to process more copper- and aluminum-bearing scrap than it was able to previously.
Fercometal’s Marlene Rodriguez, Federico’s eldest daughter, says the company’s previous experience with Bano’s equipment led it to reach out to the company’s Sales Project Manager Laura Minotto when Fercometal was interested in expanding its capabilities. She says the solution Bano proposed fit Fercometal’s needs “perfectly,” resulting in the company moving forward with new equipment from Bano without any further shopping around.
Bano’s equipment offers versatility and robustness, with each plant being tailored to suit the specific needs of its customers. The system at Fercometal includes a preshredder and two lines: one to liberate composite material and recover steel and zorba/zurik, and a second line to recover and refine the liberated material from the first line.
The low-speed, single-shaft preshredder is used for voluminous material, such as armored and underground cables and radiators. The versatile system means material processed by the preshredder can be sent to either the vertical mill or directly to the refining plant for further processing.
The preshredder defines the size and shape of the material for subsequent processing, Bano’s Minotto says. “The size must be homogeneous, and the shape must be as flat as possible to allow efficient sorting and proper treatment in the following steps.”

Bano’s preshredder features a hydraulic transmission, allowing it to easily handle contaminants and a diverse range of difficult materials. “It is very reliable,” she adds.
Minotto says the vertical shredder is key to the process because it liberates the metals contained in complex infeed material.
At Fercometal that material includes, electric motors, aluminum radiators with copper and polyvinyl chloride- (PVC-) jacketed cables, Rodriguez says. Before the installation of the new Bano equipment, Fercometal was unable to process these materials, she adds.
Bano’s vertical shredder is flexible enough to handle these various materials, liberating the metals within. “With the Bano vertical mill, we are able to obtain excellent disintegration and liberation of composite material to obtain high-quality products and reduce losses to a minimum,” Minotto says.
The machine features a unique design that includes a cutting chamber that opens hydraulically. The vertical shredder operates clockwise and counterclockwise for balanced wear, has a modular rotor configuration and electronic speed adjustment.
The refining line includes Bano’s vertical turbo mill, which replaces the granulator and refiners used in traditional systems, Minotto says. “Granulators are the weak point of the refining and cable lines,” she says. “We have developed a machine that can resist contaminants, assuring a longer life time and avoiding production losses.”

An added benefit of the vertical turbo mill is that stainless steel particles processed through the machine become slightly magnetic because of the fiction and impact and can be sorted using a high-gauss magnet.
Minotto adds, “The vertical and the horizontal tubo mills are the key machines of the refining system.” She says these machines enable the plant to process the liberated motors, auto shredder residue and other difficult materials.
After the vertical turbo mill, Fercometal has installed magnets and eddy current separators from Steinert, based in Germany, as well as air tables and densimetric separators supplied by Bano.
The Fercometal system can process as much ass 2,000 tons per month, depending on the number of shifts the company runs, producing zorba and zurik, but also clean copper granules in two different sizes, aluminum and steel.
The global pandemic delayed the startup of Fercometal’s new equipment, so the company is still in the process of fine-tuning. “At the moment, we are still making tests with the product and regulating the equipment so we can provide the best quality,” Rodriguez says, though she seems confident in the equipment and Fercometal’s abilities.
“The experience has been very good,” she says. “We are in contact with Laura … who helps us with everything we need.”
Rodriguez adds, “We have a very good relationship with Bano. In the future, we do not rule out buying more machinery of this brand, and, if that were the case, it would mean that we are growing, and that is good.”
Get curated news on YOUR industry.
Enter your email to receive our newsletters.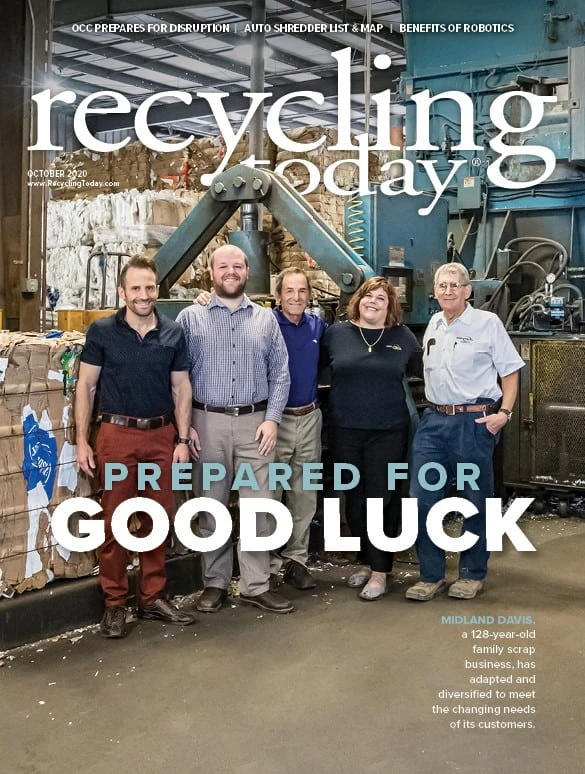
Explore the October 2020 Issue
Check out more from this issue and find your next story to read.
Latest from Recycling Today
- Republic Services, Blue Polymers open Indianapolis recycling complex
- Altilium produces EV battery cells using recycled materials
- Brightmark enters subsidiaries of Indiana recycling facility into Chapter 11
- Freepoint Eco-Systems receives $50M loan for plastics recycling facility
- PET thermoform recycling the focus of new NAPCOR white paper
- Steel Dynamics cites favorable conditions in Q1
- Hydro starts up construction in Spain
- Green Cubes unveils forklift battery line