
The United States iron and steel foundry sector is a major consumer of ferrous scrap. According to Tom Teske, vice president at East Jordan, Michigan-based EJ Americas, ferrous scrap made up 85 percent of foundry feedstock in 2021 and now is between 90 to 95 percent. The sector relies heavily on ferrous scrap from end-of-life vehicles, consumer products and prime steel recovered from manufacturers.
American metal casting facilities recycle 14 million tons of ferrous scrap annually, according to the Schaumburg, Illinois-based American Foundry Society (AFS). This is a substantial volume considering American steel production in 2023 tapped out at 80 million tons, consuming around 70 million tons of ferrous scrap. Globally, the Brussels-based World Steel Association (Worldsteel) says foundries consume 70 million tons of ferrous scrap annually.
However, Brian Began, vice president of metalcasting services at AFS, says intermittent supply chain issues and labor shortages are the two biggest challenges facing foundries nationwide. He adds that the supply chain challenges resulted from upstream processes being offshored over several years.
“Most mining is not done in the U.S. or North America, so materials need to travel long distances,” Began continues. Manufactured products supporting foundries also have been migrated offshore. Distribution within the U.S. is not an issue, but the problem lies in the elongated lead times and the lack of flexibility that comes with long-distance trade arising from offshoring.
Like other manufacturing segments across the U.S., foundry demand has been a challenge.

In the AFS March 2024 Metalcasters Quarterly Outlook Survey, a third of respondents said their company’s sales trended lower over the last 90 days. Meanwhile, 56 percent of participants felt demand for castings was among the top challenges their foundries faced, up from 36 percent in the November 2023 survey and overtaking the previous key challenge of labor shortages.
Wisconsin-based Waupaca Foundry, one of the biggest in the market with a production capacity of 1.4 million tons and an annual recycling capability of 2.2 million tons, has seen its nationwide foundry presence drop from seven in 2021 to five currently. The most recent loss was its foundry in Tennessee, which was idled in 2022.
Metal Technologies, based in Auburn, Indiana, also closed Hibbing Foundry in Minnesota in March, blaming rising electricity and ferrous scrap prices.
Metalcasting plants in the U.S. decreased from 1,871 in 2015 to 1,719 in 2023 and are forecast to fall to 1,709 by 2028. This is a steep decline from the 2,900 operational facilities in 2000, a sign of headwinds in the broader domestic manufacturing sector.
Many companies in the metalcasting sector are small and medium enterprises that cannot compete with larger brands, a U.S. Department of Energy report revealed. This also has led to consolidation in this industry as larger foundries can capitalize on economies of scale and greater purchasing power, leading to the rapid acquisition of smaller players.
For example, Charlotte Pipe and Foundry Co., a major foundry player, acquired Wisconsin-based Neenah Foundry in July 2022, while EJ Co. Foundry bought the Alhambra Foundry in May of the same year.
Shane Kramps, vice president at Surrey, British Columbia-based Reliance Foundry, doubts any foundries will be built in Canada soon. Reliance Foundry itself used to be owned by Neenah Foundry. He notes that American foundries see their Canadian counterparts as nonconsequential, hence, cross-border trade remains subdued. Any benefits from the price advantage offered by Canadian foundries are offset by the high costs of freight to U.S. customers.

Labor issues also must be sorted to tap into available capacity. Began notes the available workforce is not overly keen on joining foundries, which poses a problem for top management. According to the Metalcasters Quarterly Outlook Survey, 53 percent of respondents cited labor shortages as one of the industry’s top three concerns.
However, foundries are cautiously optimistic about the future. Around 40 percent of the metalcasters surveyed by the AFS in March had a positive outlook for the next 12 months compared with 29 percent who said business would turn negative.
The opening of new foundries also has improved the industry’s sentiment. Last year, Charlotte Pipe opened a new cast iron foundry in Oakboro, North Carolina, that can recycle 150,000 tons of ferrous scrap annually, making it one of the largest new facilities of its type recently built in the country.
Canada’s foundry sector has a smaller piece of the North American regional pie, Kramps says. However, he is confident the sector shows promise as demand has increased from Canadian buyers. Some suppliers also are helping foundries reduce costs by producing in other regions.
Metalcasters also seek novel technologies and processes to boost production and operational efficiencies. Artificial intelligence (AI), for instance, is transforming the steel industry, and metalcasters also can stand to benefit.
Began agrees that foundries are investing in AI, with an active AFS committee investigating potential use cases of this emerging technology. The industry is cautiously optimistic about its potential, with some companies emerging ahead of others in adoption. But, Began stresses that the underlying infrastructure must be set up before the industry can really embrace AI.
Get curated news on YOUR industry.
Enter your email to receive our newsletters.
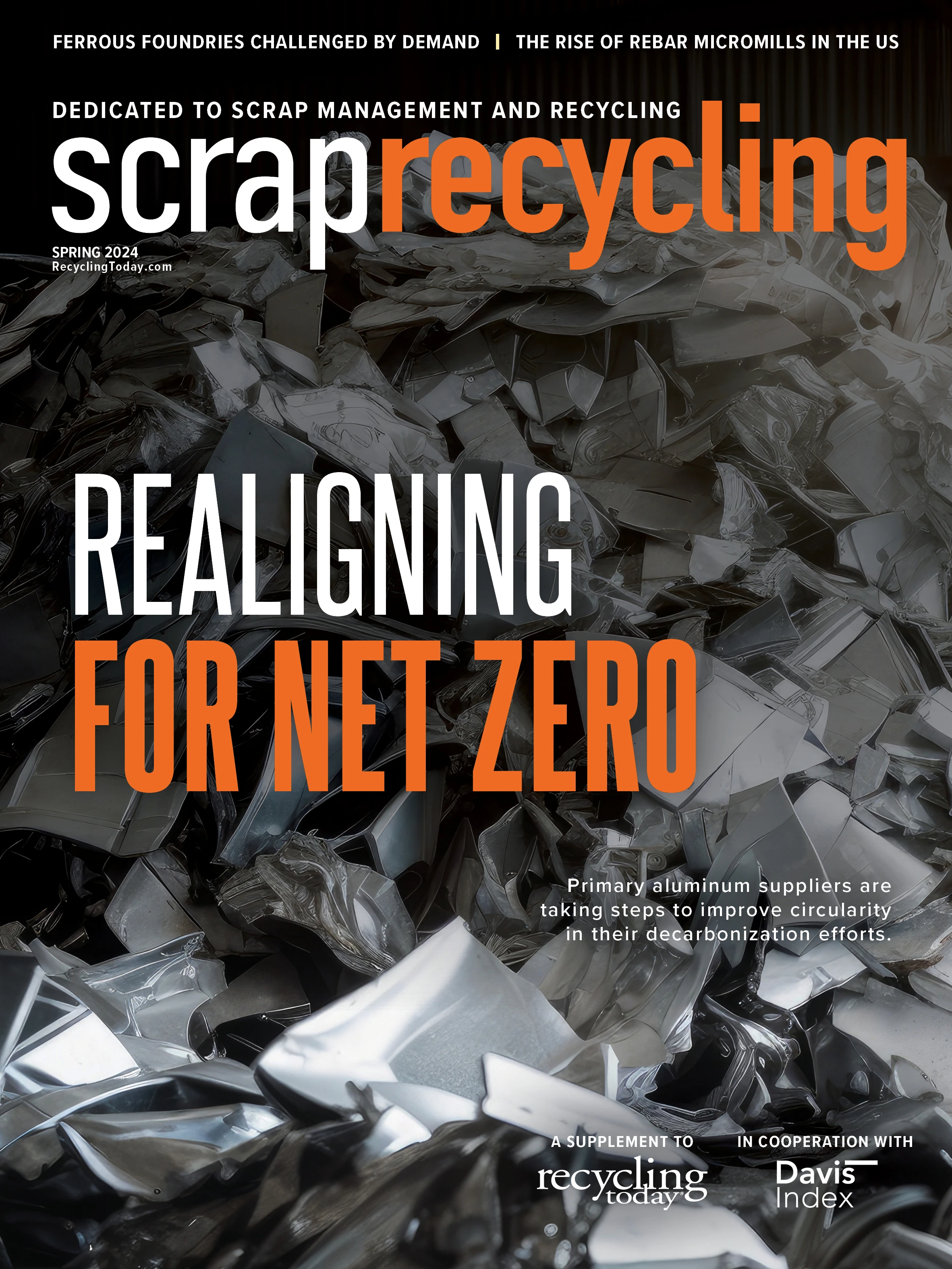
Explore the Spring 2024 Scrap Recycling Issue
Check out more from this issue and find your next story to read.
Latest from Recycling Today
- AF&PA report shows decrease in packaging paper shipments
- GreenMantra names new CEO
- Agilyx says Styrenyx technology reduces carbon footprint in styrene production
- SABIC’s Trucircle PE used for greenhouse roofing
- Hydro to add wire rod casthouse in Norway
- Hindalco to invest in copper, aluminum business in India
- Recycled steel price crosses $500 per ton threshold
- Smithers report looks at PCR plastic’s near-term prospects