As mill brokers have been paying higher and higher prices for ferrous scrap, exporters, shredder operators and scrap dealers have scrambled to harvest enough scrap to fill all orders.
With industrial scrap generation static or declining in many parts of the country, these efforts have focused on obsolete scrap, such as auto hulks, appliances and demolition scrap.
Even though much of this scrap eventually reaches a shredding plant, efficient handling and shipping practices also mean that much of it will be compressed first—creating a competitive market for baler manufacturers.
REAPING THE HARVEST.
As scrap prices have pushed well beyond $100 per ton and stayed there for several months, dealers have become willing to reach out to salvage yards and other generating sites in more remote areas.Similarly, dealers have noticed a return in the peddler trade, as potential scrap scavengers who waited through the down markets are paying attention again. "Every time we increase prices $10 on the scale, we can see the scrap coming from that much farther out in the Maine woods," comments Peter McAvoy, president of Industrial Metal Recycling, Oakland, Maine.
Industrial Metal Recycling operates several balers, shears and loggers (and combination machines) from Sierra International Machinery Co., Bakersfield, Calif. The company has traditionally used a lot of portable machinery to process scrap at clean-up sites; at appliance collection centers; and from auto salvage yards. Industrial Metal Recycling sells processed scrap to a variety of domestic and overseas consumers.
As the scrap market has heated up, manufacturers such as Al-jon Inc., Ottumwa, Iowa, have seen revived interest in their baling and flattening equipment. Al-jon President Kendig Kneen also has noticed that the renewed interest is focused on higher-volume machines, such as auto loggers, that can produce a denser, transportable package.
"Having been in this business for 40 years, when we started some dealers were using Sherman Tanks or whatever they had on hand to flatten cars," says Kneen. "But now, auto hulks are being transported 300 or even 3,000 miles, which the car logger allows you to do."
Kneen says an auto logger such as Al-jon’s 580 model shapes the scrap into a configuration that allows it to stack efficiently inside a rail gondola car or other transport container, such as a dump trailer. "The density doesn’t necessarily change, but the configuration allows you to put as much as 80,000 pounds of scrap into a dump trailer," Kneen notes.
Al-jon continues to sell scrap metal compressing equipment to a client base that includes auto dismantlers and smaller dealers who go on site to service them, but the company is also seeing shredding plant operators reaching out to the dismantling segment to secure feedstock in the form of baler logs made from auto hulks.
"These machines are in demand to access larger volumes of material for these large shredding plants," says Kneen. "These larger recyclers are seeking greater volumes of scrap farther away from their shredders."
For dismantlers who wish to continue preparing their own scrap, Al-jon now offers its ELV (end-of-life vehicle) system, which includes a system to extract fluids and pull out harvestable components from an auto hulk before it is compressed by the attached logger. "One experienced operator on one of these can process a car in less than five minutes," says Kneen.
Another manufacturer tapping into the portable baling market is Iron Ax Inc., Wadley, Ga. The company, which started as a maker of mobile shears for cutting scrap, is now making the Iron Pack Baler, a portable machine (weighing just 75,000 pounds) that can convert auto hulks and white goods into logs or bundles.
The Iron Pack Baler can be configured in tandem with a material handler for loading and includes a catch pan to collect fluids that drain during baling.
And for those recyclers feeding shears or balers with larger appetites, companies such as Sierra; Harris (through its time-tested Harris Press & Shear line), Peachtree City, Ga.; Lefort USA, St. Louis; Vezzani USA, Peachtree City, Ga.; Metso Recycling, Cedar Rapids, Iowa; and Moros/North America, Louisville, Ky.; continue to introduce and upgrade new models.
SHREDDER BOUND.
A more recent twist on the demand for ferrous scrap balers involves the creation of a scrap grade, usually referred to as soft shredder logs, specifically designed for further processing at a shredder plant.This grade or form of scrap has helped create a renewed market for baler/loggers as a way to prepare collected scrap for shipment to auto shredder plants.
"Logs are now more acceptable to operators of the large shredders," says John Sacco of Sierra International Machinery.
Speaking at an ISRI event held in 2003, Sacco said that baler/loggers that can be transported fairly effortlessly on flatbed trailers are being used in areas that are somewhat distant from the nearest shredder yard as a means of preparing obsolete scrap for shipment to a shredder. As noted earlier, scrap in this form "can increase the trailer weight," he remarked, compared to shipping loose or flattened scrap.
He cited several reasons why some recyclers would rather create logs that are shipped to shredder plants rather than preparing a grade for direct shipment to a steel mill.
Logging can compress more material in a given time period compared to baling (though perhaps not as densely), another reason why recyclers are able to ship more material. From a cash flow viewpoint, recyclers who ship to a shredder rather than a consuming mill will probably be paid more quickly by the shredder operator, and a load is less likely to be rejected by a shredder operator compared to a mill, Sacco commented.
Preparing material for further processing at a shredder plant also provides a home for material that may previously have been packaged as number two heavy melt—a grade that many recyclers find is facing a dwindling demand scenario.
Al-jon’s Kneen notes that if material is being prepared as shredder logs, it is important to prepare the logs at the density preferred by the receiving shredder plant. "Of great importance to a car logger is the ability to correctly meter the density of the material," he remarks. "There are a number of different shredder types out there ranging from 200 to 6,000 hp. Each of them wants a uniform density in the product they are buying," says Kneen, adding that the preferred density varies from shredder plant to shredder plant.
And North American cargo securement standards that began taking effect last year provide one additional boost to logging.
"Logs shipped on a flatbed don’t need the four-sided confinement systems," says Kneen. "Logs are not subject to the same scrutiny as flattened autos. The Department of Transportation has not singled out baled cars as it has flattened cars."
While shredder plants may be chewing through more ferrous tonnage than ever, the need for compression in the ferrous market has by no means diminished.
The author is editor of Recycling Today and can be contacted via e-mail at btaylor@RecyclingToday.com.
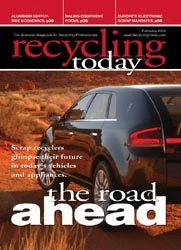
Explore the February 2004 Issue
Check out more from this issue and find your next story to read.
Latest from Recycling Today
- Aqua Metals secures $1.5M loan, reports operational strides
- AF&PA urges veto of NY bill
- Aluminum Association includes recycling among 2025 policy priorities
- AISI applauds waterways spending bill
- Lux Research questions hydrogen’s transportation role
- Sonoco selling thermoformed, flexible packaging business to Toppan for $1.8B
- ReMA offers Superfund informational reports
- Hyster-Yale commits to US production