For more than 80 years, the Highiet family and Modesto Junk Co. have provided scrap recycling services to Modesto, Calif., and the surrounding Stanislaus County/San Joaquin Valley region.
Founded by Alex Highiet in 1920, the company has remained at its original downtown location for 85 years, occasionally adding small parcels of adjacent land to grow to its current size of more than two acres. In 1995, the company built a new two-story office structure (replacing the old barn-like structure that was in place since 1920) and compatible warehouse space and redesigned its outdoor area for a more efficient layout.
But any additional land has been more than outpaced by increasing volume growth over the years, meaning the company must always manage its production and shipping processes wisely to prevent bottlenecks.
Current company President Harvey Highiet and Director of Operations Jeff Highiet, Harvey’s son, credit their three high-production baling lines for keeping the Modesto Junk Co. efficient and competitive.
MULTIPLE MARKETS. A remarkable facet of Modesto Junk Co.’s business is that it provides an array of scrap metals services for ferrous and nonferrous markets while also acting as an authorized handler of California Refund Value (CRV) beverage containers.
"We buy all types of non-hazardous ferrous and nonferrous metals, including copper, aluminum, brass, radiators and stainless steel, plus the popular and typical ferrous items, such as appliances (hazmat must be removed prior), black iron, structural steel and automotive scrap," says Jeff.
The small location hosts a 35,000-square-foot CRV service station with five buyback scales that can handle 500 or more daily customers bringing in their CRV bottles and cans.
The CRV business has helped familiarize the public with Modesto Junk Co. as a buyer of other materials. "We don’t just take cans and bottles from the public; they bring in siding and other types of scrap," notes Jeff.
Jeff’s father Harvey admits he had to be convinced the equipment would pay off for the firm. "It was absolutely a difficult step for me; there was a lot of money involved," he says. "But there is no question it was absolutely a necessary and vital thing to do. It made us more efficient and allowed us to increase our production."
The systems have also allowed fourth-generation family member Keith Highiet to concentrate on the trading and management aspects of the business. "You have plenty of other skills to learn in the scrap business, so having this automation helps take away from some of the attention to processing," he notes
Jeff’s daughter Alexis works at the company providing phone support and assistance to the cashiers. His daughter Janine is attending law school.
To handle the high-volume and diverse stream of materials, the Highiets have set up the three baling lines in three different sections of their property.
WINNING TRIFECTA. Jeff says the company operated for its first 75 years with little automation. "We really didn’t start to move into the 20th century until around 1995, when we got our first baler-conveyor system," he says.But Jeff and Harvey were so pleased with the productivity of the 500-ton baler/shear/logger they purchased from Harris Waste Management Group, Peachtree City, Ga., that they have since moved their operations quickly through the 20th century and into the 21st.
The company’s current operations involve running three largely automated baling lines handling separate components of its business: The Harris 500 handles ferrous scrap; a Harris Centurion handles nonferrous scrap; and a Harris Badger bales the plastic bottles and aluminum used beverage containers (UBCs) from the CRV stream.
The 500-ton Harris 2000 model machine "gave us the power and incentive to buy any and all types of ferrous items; this machine can handle it—it’s a strong machine that weighs about 275,000 pounds."
As the CRV business increased from modest origins in 1989, the company first purchased one (and then more) small vertical balers and CP Manufacturing can densifiers. Modesto Junk Co. purchased a baler made by Excel Manufacturing, St. Charles, Minn., in 1997, which still serves as a back-up baler today, as do the small vertical balers if they are needed.
An increasing volume of incoming material, combined with a lack of warehouse space, keeps Modesto Junk Co. on the fast track in terms of the quality of the equipment it deploys. "We’re now handling two-and-a-half times as much material as we were back in 1999," Jeff says.
Keith says, "It might seem that we have more equipment than we need, but because of our small property, we have to address incoming material immediately each day. Downtime for even one or two days here is something we have to address right away."
Working with Karl Schmidt & Assoc., Commerce City, Colo., Modesto Junk Co. set up a combination conveyor/storage system that allows the Harris Badger to alternate between baling plastic bottles and aluminum UBCs.
Setting up the baling lines has radically changed the way Modesto Junk Co. does business. "Having this kind of machinery helps you manage your yard professionally," Jeff says. "It lets you maximize your space and keeps your yard looking clean, with stacked bales rather than loose piles."
The author is editor of Recycling Today and can be contacted via e-mail at btaylor@gie.net.
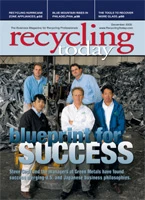
Explore the December 2005 Issue
Check out more from this issue and find your next story to read.
Latest from Recycling Today
- Author predicts spike in silver’s value
- SWANA webinar focuses on Phoenix recycling collaboration
- Domestic aluminum demand up through Q3 2024
- IntelliShift honored at IoT Breakthrough Awards
- Ace Green Recycling finalizes plans for battery recycling site in India
- Ambercycle, Benma partner to scale circular polyester
- NIST database aimed at increasing textile recycling
- ILA, USMX announce tentative agreement