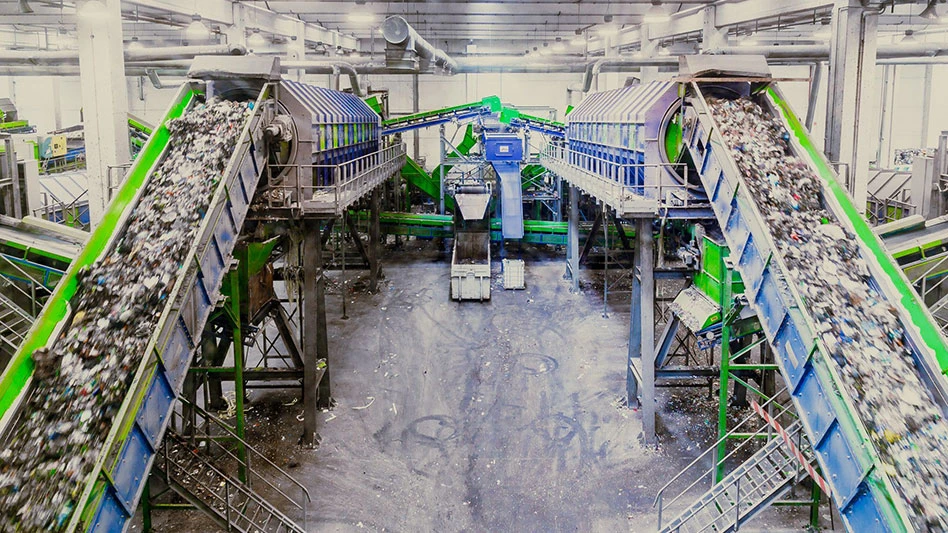
Photo courtesy of Dunlop
In the fast-moving and competitive world of recycling and waste management, the durability and efficient performance of conveyor systems can be critical factors in productivity and cost management. Every time a conveyor belt needs to be repaired or replaced means cost, not only in terms of the direct costs but also lost production time. Of all the many industries where conveyors play an integral role, none has a bigger range of demands and challenges than the recycling and waste industry. Despite this, a surprising lack of understanding remains about the technical aspects of such a crucial component and how and why the performance of one conveyor belt can differ so enormously from another. The result is that belt selection is too often based on promises and prices that ultimately become false economies.
Read on to learn about the number of destructive forces that are exerted on rubber conveyor belts used in recycling and waste plants and how to select belts that require significantly less maintenance and provide considerably longer working life.
Oil resistance
A high proportion of waste, particularly household waste, contains chemicals and various forms of oils, resins and greases. Almost without exception, these substances have a seriously detrimental effect on the performance and life expectancy of rubber conveyor belts. The recycling industry spends millions of euros every year buying, fitting, repairing and replacing conveyor belts. Sadly, much of this expenditure is wasted simply because the conveyor belts being supplied are not as resistant to oil as they should be.
Oils, resins, fats and greases that damage rubber originate from two distinct sources. Vegetable oil is the most predominate source and is defined as all forms of oil (and resin) that is derived from flora and fauna. The other primary source is mineral oil, which usually is a liquid byproduct of refining crude oil to make gasoline and other petroleum products. Mineral oil is composed mainly of alkanes and cycloalkanes, which are related to petroleum.
It is important to bear in mind that the kind of swelling and distortion caused by different oils and resins can have a marked difference. Despite this, many manufacturers only offer one type of oil-resistant rubber, which is commonly designated as MOR, or moderate oil resistance.
When any kind of oil penetrates the rubber covers of a conveyor belt, it causes the rubber to soften, swell and distort. Although this is often a gradual process, it leads to various problems.
The first negative effect is a dramatic decrease in the ability of the rubber to withstand abrasive wear. This is why low-priced belts with inadequate oil resistance wear down more quickly than premier-grade belts. As the rubber continues to soften, it also steadily loses its tensile strength while also becoming more prone to cutting, ripping and tearing.

In the next stage, the rubber begins to swell and distort. This causes steering and handling problems along with a serious reduction in the elongation at break (the amount of stretch before the belt snaps). A common symptom of this is recurring splice joint problems.
Research has revealed that organic waste is the largest component of household waste (69 percent). Surprisingly, plastic represents less than 11 percent. Household waste, therefore, contains very high levels of vegetable oils and resins, which have an extremely detrimental effect on the performance and life expectancy of the rubber conveyor belts that carry the material from one processing stage to the next. A wide variety of chemical-based domestic products such as household cleaning agents, bleach and other potentially damaging chemicals also can be found in the material stream. Fortunately, good quality oil-resistant rubber should provide sufficient protection against such chemicals.
Oil-resistance test methods
Two oil-resistance test methods are recognized, both of which involve almost identical test procedures: ISO 1817 and the comparable, slightly less elaborate but very stringent American ASTM ‘D’ 1460. In these test, samples of rubber are immersed in the relevant test liquid for a specific time. Changes in the geometry and dimensions of the specimen caused by absorption are then measured when the samples are removed.
Rather surprisingly, ISO or DIN (Deutsches Institut für Normung) international performance standards for oil and grease resistance do not exist. This means that in the absence of actual performance standards, manufacturers and traders can claim the belt they supply is sufficiently oil-resistant for its intended use. To make things worse, an element of deception can be present concerning the matter of test methods.
Some of the biggest manufacturers of belting in the world, primarily those in Asia and Europe, use the DIN 22102 G (DIN G) when referring to oil-resistant belting. This can be misleading because no firm requirements, test methods or limits specific to oil-resistant belting are associated with DIN 22102 G. The letter ‘G’ is simply used to denote some form of resistance against oil or grease, but it is NOT an indication of the actual level of oil resistance. This is a classic example of how some manufacturers and traders use a test method reference number to create a false sense of security even though, in truth, it is meaningless with respect to actual performance.
Rip-and-tear resistance
When conveying materials such as scrap metal and demolition debris, for example, the ability of belts to withstand the forces that cause rip, tear and impact damage often is more important than any other physical attribute. A rip is best defined as what happens when a sharp object punctures the belt and cuts it lengthwise as the belt is pulled against the trapped object. In contrast, a tear is what happens when a section of belt is pulled apart in opposing directions. Tearing also includes the spreading of initially small damage or punctures that can develop into a catastrophic rip.

The most common misconception is that fitting belts with thicker outer covers and/or an increased number of plies will help. Belts that are too thick for the design of the conveyor can cause new problems, such as excessive rigidity (lack of troughability) and steering and handling difficulties. The same applies to increasing the tensile strength. The harsh reality is that unless the inner carcass and outer covers are engineered specifically to resist ripping, tearing and impact, then simply using more of the same material will not provide the solution.
Another course of action when faced with repeated damage is to opt for low-grade, sacrificial belts. The sentiment seems to be that it is not worth paying good money for a belt that probably sooner rather than later will be ripped from end to end. For me, this attitude does not make economic sense because it invariably results in a great deal of waste, avoidable stoppages and unnecessary cost.
Cheap belts are low-priced for a very good reason, which is that they have been made using poor-quality materials. Low-grade belts lack the necessary durability and are damaged easily. When you add up the cost of incessant patch repairs, splice repairs, replacement belt after replacement belt with the invisible uninvoiced cost of the lost production while all those unplanned stoppages are taking place, the true cost is several times higher than the price of the original belt. The fact is that when ripping and tearing are problems, the most practical and economical solution is to fit a conveyor belt that has a carcass that has been engineered for the purpose.
Engineered for the task
The big advantage of specialist fit-and-forget belts is that they have highly engineered internal fabric plies that have three or more times the resistance to ripping and tearing compared with other conventional heavy-duty belt constructions of similar tensile strength. Combined with premium-grade rubber covers, these belts are proven to provide up to four or five times longer operational life. Their initial buying price will be higher, and many would say they are too expensive, but their lifetime cost is proven to be substantially less than conventional belts.
The biggest cause of rapid belt cover wear is because low-grade economy rubber has been used. Suppliers could claim that their rubber meets the required standards for abrasion resistance (maximum volume loss in cubic millimeters under ISO 4649or DIN 53516 test conditions). However, in reality, the wear resistance might only be borderline at best or, as is regularly found during laboratory testing, inadequate.
It is important to bear in mind that the ability of a belt cover to withstand wear does not arise from its abrasion resistance alone because it also depends on the cover rubber’s overall strength and its resistance to cut and tear propagation. If that resistance is low, then a small, seemingly insignificant area of damage in the cover easily could increase in size given the continuous material loading and the relentless flexing around the drums and pulleys. In time, this damage will spread and link up with another area of damage. Consequently, small areas of damaged rubber effectively are cut out from the surface rather than being worn thinner.
The invisible destroyers
Two other much less well-known and inescapable factors have an influence on the operational lifetime of all rubber conveyor belts: ozone (O3) and ultraviolet (UV) light. Contrary to common misconception, the damage they cause is extensive and not limited to higher altitudes or sunny climates. UV degradation is particularly relevant to recycling plants because so many conveyors are in buildings and illuminated by fluorescent lighting.
The damage caused by O3 and UV light is almost entirely preventable if special additives are used in the creation of the rubber compound. Unfortunately, these additives are regarded by the producers of economy conveyor belts to be an avoidable cost.
Fire safety
The increasing number of fires at waste and recycling facilities around the world is a growing concern, exacerbated, of course, by the surge in the use of combustible lithium-ion batteries. Nowhere does the difference in performance between one conveyor belt and another have more potentially serious consequences.
The importance and complexity of the subject matter mean that it needs to be treated in isolation rather than as part of a general overview. In the meantime, Dunlop provides helpful guidance.
Price is what you pay. Cost is what you spend.
It is fair to say that the ‘headline price’ of an item usually has the biggest influence on the purchasing decisions we make. In business, it is most often budgetary constraints. However, selecting a conveyor belt because it is ‘competitively priced’ compared with other offers can be a very costly mistake. Ironically, a big price difference is the first warning sign that a belt is unlikely to be up to the required standard.
Thanks to technological advances, the effectiveness and value of modern-day conveyor belts should be measured over several years rather than just a year or two. In fact, in the recycling industry, we are seeing more examples of belts that only last a few months and, in some cases, only a matter of weeks before needing replacing. My message to all conveyor operators is that you should never accept that it is not possible for a belt to last many times longer than is currently being achieved.
The decline in operational lifetime has been accompanied by the increased use of low-grade imported belting. Ironically, this actually strengthens the case for selecting conveyor belts on a ‘whole life’ cost basis rather than simply the ‘headline’ price. Although there will always be pressures to reduce expenditure, belts that need frequent repair and replacement have exactly the opposite effect. Conveyor belts that will stand the test of time invariably prove cheaper in the long run.
After spending 23 years in logistics management, Leslie David has specialized in conveyor belting for over 17 years. Rob van Oijen, manager of application engineering for Dunlop Conveyor Belting in The Netherlands provided technical and professional assistance in writing this article.
Get curated news on YOUR industry.
Enter your email to receive our newsletters.
Latest from Recycling Today
- ReMA opposes European efforts seeking export restrictions for recyclables
- Fresh Perspective: Raj Bagaria
- Saica announces plans for second US site
- Update: Novelis produces first aluminum coil made fully from recycled end-of-life automotive scrap
- Aimplas doubles online course offerings
- Radius to be acquired by Toyota subsidiary
- Algoma EAF to start in April
- Erema sees strong demand for high-volume PET systems