
Recycling equipment industry veteran Bob Pfeffer has helped recommend, sell and install numerous balers to generators and recyclers of scrap metal, including units that will perform their work on-site at a stamping plant or other point of generation.
Pfeffer currently serves as product manager of shears and balers for the western North American market for Finland-based Metso Metal Recycling. He previously served a long tenure with Georgia-based equipment maker Harris.
In his roles with these companies over the years, Pfeffer has seen how a number of different factors come into play when matching up the right baler for an in-plant (point of generation) application. He also has observed and collected information on the “dos and don’ts” of operating a baler in such a setting regarding the critical aspect of machinery maintenance.
In the following interview, Pfeffer offers his insights on these topics and others pertaining to the placement and performance of metals balers on the factory floor and at other points of scrap generation.
Recycling Today (RT): What level of volume of scrap generated weekly or daily triggers the need for a baler to be placed at an industrial site?
Bob Pfeffer (BP): Production volumes can vary extensively in industrial applications. You could see production ranges from 1,000 tons per month to 10,000-plus tons of scrap generated monthly. The need for a baler may be driven by volume reduction and densification for handling and shipping or for increasing densification for charging a furnace.
RT: What types of facilities most often trigger this need? (Stamping plants? Assembly plants? Steel service centers?)
BP: Industrial applications vary, and there are many applications. Stamping plants utilize balers for clips, skeletal cuts and reject material. Metso has numerous balers located in major automotive plants all over the world.
Aluminum can producers typically utilize these balers for the trim and rejects produced from the can lines. Steel mills or foundry operators utilize these balers for densification of material for furnace charging to create more even heats. Facilities that produce copper, aluminum, brass and other ingot grades often have them on-site for the same reason. I’ll also mention that Metso has a line of chip, shavings and turnings briquetters that are sold to industrial accounts for the same reasons as above.“Lack of maintenance is the single biggest reason for baler downtime. If all proper maintenance procedures are performed as required, balers will perform to their projected life spans and longer.”
RT: Who is involved in selecting and paying for a baler in this case? Do the plant operator and the scrap company typically need to agree on how to proceed?
BP: The majority of industrial applications are internal purchase decisions with input from facility owners, managers, facility engineers and purchasing groups. The majority of these purchasers would buy the baler directly to control the flow of the material.
Normally, a scrap company would just be buying the material baled from an industrial account that has the baler.
RT: How do you determine the style and size of baler for a specific location?
BP: For industrial applications, we are primarily discussing a triple-ram baler as the baler of choice. Most industrial applications require this kind of machine to provide the most efficient bale density. These balers incorporate a built-in shear system that can shear off excess material, minimizing material preparation.
In selecting the correct baler, consideration must be given to production requirements, materials to be baled, hours of run time, facility space available, electrical requirements and degree of automation required.
One main consideration is the electrical power consumption of the baler, especially in an industrial application running 24/7. For example, you can have two balers producing about the same number of bales, but one baler is drawing 30 percent more electrical energy than a baler that has a more efficient system. This may not seem like a large number on one eight-hour shift per day, but when you triple the run time, it can add up to several hundred thousand dollars over the life of the baler.
RT: What are some of the “footprint” considerations when deciding to choose between a smaller baler (less floor space) versus a larger one that will densify material faster (and thus also save floor space)?
BP: Good question. If it is a new facility, we generally have plenty of room for the baler system. However, our most common applications are in existing facilities, where space is usually at a premium. We try to select the baler with optimum performance for the facility and find ourselves squeezing in the baler to an existing spot (if it is a baler replacement) or trying to carve out space for a new baler location. We have balers installed above grade, partially below grade or completely below grade, depending upon building height limits or feeding methods. We always strive to meet production needs with the correct size baler for the customer.
RT: Who is typically responsible for operating the baler? How about maintaining it and replacing wear parts?
BP: Facilities typically have their own operational crews for the baler operation. The majority of industrial accounts want a fully automatic system, which would usually require either a weigh hopper system or a remote control, so an operator does not have to operate the baler manually. We do recommend that the facility does have authorized personnel in the baler area to keep an eye on the baler and immediate area for safety reasons.
Facilities typically also have in-house maintenance personnel to take care of the minor baler maintenance. For larger issues or equipment relines, facilities usually go to outside contractors, such as the baler manufacturer, for service.
At Metso, we offer a full range of services from complete maintenance of the baler to quarterly or annual inspections. We also offer operator and maintenance training courses as needed.
RT: What sort of life span can be expected for a baler operating long hours at one of these locations? What factors affect the lifespan?
BP: A reputable, quality-designed triple-ram baler typically has a lifespan of 25 to 30 years in a single-shift application. I personally have seen balers aged from 30- to 40-plus-years-old running every day. Again, in some industrial applications the baler sees very light duty and can outlast any projections.
As far as factors that affect this, my answer is maintenance, maintenance, maintenance! Lack of maintenance is the single biggest reason for baler downtime. If all proper maintenance procedures are performed as required, balers will perform to their projected life spans and longer. If maintenance is ignored, you can adversely affect baler performance, structure and operating systems, shortening the baler’s life.
“The need for a baler may be driven by volume reduction and densification for handling and shipping or for increasing densification for charging a furnace.”
If the baler is properly sized, the customer should be aware of the limits of the baler and know the list of unrecommended materials that could damage the baler if processed.
RT: You mention how unrecommended materials can cause damage. What are some of the noteworthy examples you have seen of inappropriate materials entering a baler that have caused catastrophic damage?
BP: Unacceptable material can consist of oversize material that is either too big or too thick for the baler. Hazardous material, such as sealed tanks, reservoirs, gas cylinders, etc., also clearly is unacceptable.
One specific example was with a customer baling stainless steel. I found a 4-inch-by-6-inch-by-3-foot stainless solid bar in one of the customer’s bales. He could have damaged the shear knife or inflicted structural damage by point-loading the bale chamber. Point loading is defined as applying too much force or mass at a single point.
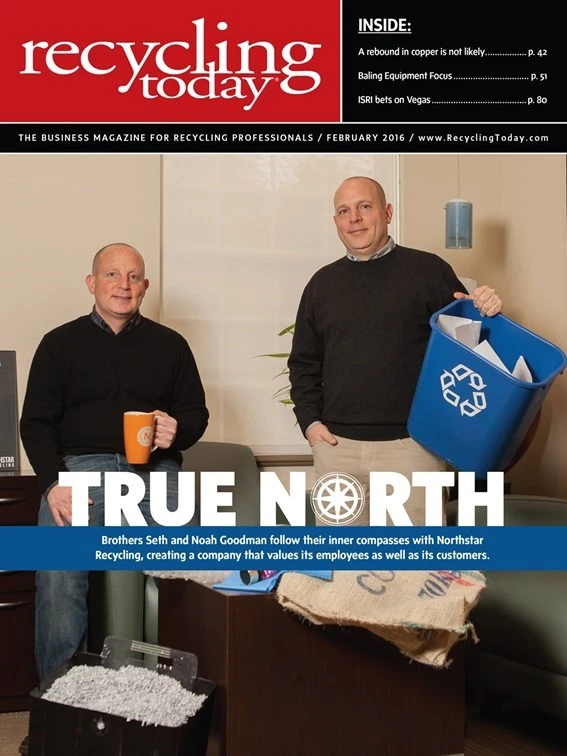
Explore the February 2016 Issue
Check out more from this issue and find your next story to read.
Latest from Recycling Today
- LumiCup offers single-use plastic alternative
- European project yields recycled-content ABS
- ICM to host colocated events in Shanghai
- Astera runs into NIMBY concerns in Colorado
- ReMA opposes European efforts seeking export restrictions for recyclables
- Fresh Perspective: Raj Bagaria
- Saica announces plans for second US site
- Update: Novelis produces first aluminum coil made fully from recycled end-of-life automotive scrap