As single-stream recycling continues to grow in popularity, more material recovery facilities (MRFs) are turning to optical sorting technology to help produce marketable bales of sorted materials. Effectively sorting material has become more critical in today’s market, with prices for recyclables decreasing and consumers becoming more particular about material quality.
According to Eileen Berenyi of Governmental Advisory Associates, Westport, Conn., 160 single-stream MRFs were operating in the U.S. in 2007, an increase of 90 MRFs compared to 2003. In addition to mechanical screens, magnets, eddy-current separators and hand pickers, an increasing number of these MRFs also employ optical technology to aid in the sorting of commingled recyclables. According to suppliers of optical sorting equipment contacted for this feature, the technology can increase recovery of recyclables, such as PET and HDPE, while also delivering a purity rate of up to 99 percent.
EVOLVING TECHNOLOGY
Optical sorting technology has evolved since it was first incorporated into MRFs earlier this decade. "In general, the optical sorters have become more robust to withstand the MRF environment, more versatile and available in larger machine widths to handle the demand for increased volumes in the large mega-MRFs," says Felix Hottenstein, sales director of MSS Inc., Nashville, Tenn. MSS is a subsidiary of CP Manufacturing Inc., National City, Calif.
John Thomsen, engineering manager, National Recovery Technologies (NRT), Nashville, says many of the improvements to optical detection systems have been a result of improvements in electronics, such as computer processing speed and optical detection components. Eugene, Ore.-based Bulk Handling Systems (BHS) markets NRT optical sorting equipment to MRFs.
MAINTENANCE CONCERNS Optical sorting units require little preventive maintenance (PM), says Alex Wolf, sales engineer for Germany- and Norway-based TiTech, which is distributed in North America by Lubo USA, Stamford, Conn. He adds that the units’ operating costs are "very" low. "Optical sorting equipment consists of electronics and conveying," says John Thomsen, engineering manager, National Recovery Technologies, Nashville, Tenn. "The conveying requires the same PM that other conveyors do. The detection equipment requires much less; it could perhaps be compared to the amount of PM devoted to lighting and other industrial controls," he says. Wolf says that with around-the-clock operation, only 10 percent of a unit’s air valves would need to be replaced every two months. A unit’s optical parts require cleaning, which can vary from once per day to once per month, depending on how moist and dirty the processed material is, Wolf says. Intelligent mechanical dirt protection has been added to TiTech units in the last few years, reducing the frequency between cleanings. Felix Hottenstein, sales director, MSS Corp., Nashville, says, "The sensors themselves don’t require much preventive maintenance besides regular cleaning of the sensor window, which protects the electronics from being exposed to the outside material and environment." He adds, "Most issues arise if the maintenance crew fails to keep up with the cleaning of the sensor surroundings."
Just as with digital cameras, the resolution offered by the cameras used in optical sorting units has improved in the last five years, which allows the units to take more measurements of the material they are sorting, says Alex Wolf, sales engineer for Germany- and Norway-based TiTech, which is distributed in North America by Lubo USA, Stamford, Conn. The units TiTech produces today have a resolution that is 14 times higher compared to the units produced four or five years ago, he says. "What that means for the customer is that they have a higher recovery and higher purity as well," Wolf adds. It also makes it possible to sort smaller particles.
Thierry Oudart, international development manager for Pellenc Selective Technologies, based in France, says ternary sorting allows MRFs to sort multiple materials, such as PET (polyethylene terephthalate) and HDPE (high-density polyethylene), at the same time, increasing the unit’s payback. With ternary sorting, a single optical sorter performs a positive sort for PET and HDPE, sending these items in different directions, while it negatively sorts the rest of the material on the conveyor belt.
Pellenc optical sorting units are distributed in North America by Machinex Industries Inc., Plessisville, Quebec.
MRF systems suppliers also are incorporating track, or bi-channel, sorting into the design of single-stream systems that feature optical sorting technology, which can increase the versatility of the system by intelligently diverging material without the need for multiple optical sorting units. Track sorting commonly employs a 6-foot wide conveyor belt that is split into two sections. A 6-foot wide optical sorting unit is suspended above the conveyors. Using bi-channel sorting, MRFs can sort two to four materials using the same optical sorting unit, Oudart says, noting that this is particularly useful for small to mid-size MRFs that may not be able to invest in multiple optical sorters.
"Instead of having two 3-foot wide units with separate conveyors sorting different materials, you can just have one 6-foot wide optical unit and conveyor with a divider in the middle," Wolf says of track sorting. "The left part of the conveyor can handle totally different material and do totally different sorting tasks than the right part—all done by programming of the optical unit."
When properly integrated into a single-stream MRF, optical sorting equipment can offer a number of efficiencies, including higher purity, improved throughput and a lower processing cost per ton, according to sources.
OPTICAL INTEGRATION
NRT’s Thomsen says optical sorting is best used in addition to mechanical processes. "For example, various screening processes can (and should) be used to derive a stream of mixed containers, such as plastic bottles, metal cans, etc.," he says. "Optical sorting can then be used to perform further separation on such a stream."
Hottenstein says few differences exist among the sensors used in optical sorting units; rather, the foremost difference comes down to which supplier can provide the best overall system. "Many of our jobs are retrofits," he says of MSS, "and there is an awful lot of thinking to be done in order to integrate an optical sorter into the system. Several other auxiliary components may be required to prepare the material for optical sorting and possibly perform some other functions that require upgrading in the facility." He adds, "This value engineering is what counts for customers."
MRF operators can assist system suppliers in the design of their sorting systems by providing them with details on the volume and type of material they commonly process, the number of hand sorters employed at their facilities and the common problems they encounter, as well as their overall goals for their systems. Oudart says it also is helpful if the MRF operator provides details regarding their end users’ specifications.
While the return on an investment in optical sorting will vary by MRF based on the incoming material stream and the tonnage, Thomsen says the minimum volume required for economical operation is approximately 1,000 pounds per hour.
He adds, "The investment return will greatly vary according to the situation at each recycler, because some process streams are more valuable than others, and the gain in value due to sorting will also vary." Thomsen continues, "…a poorly sorted bale of material may increase only slightly in value when better sorted. However, in a weak market, the poorly sorted material may not have a buyer at any price, whereas the better sorted bale can be sold."
Hottenstein says, "The required volume is directly coupled with the goals of the customer." However, he adds that ROI can be less than three years for many operations, and possibly less if a MRF runs two shifts.
"Even low volumes can justify an investment [in optical sorting equipment] because of the development of ternary and bi-channel solutions," Oudart says. "The typical ROI can be from a few months to three years depending on the size of the plant, volume and the investment."
In a 25-ton-per-hour plant, Wolf says optical sorting of PET generally pays off. He says MRFs processing 12 tons per hour can benefit from adding optical sorting for PET. However, he stresses that volume requirements and ROI vary by facility based on incoming material. "In the end, once an optical sorter is put in correctly, it improves the processing cost per ton by quite a lot. It doesn’t matter what kind of application it is used for then, be it cleaning up of ONP (old newspapers), sorting PET or HDPE or even aseptic."
PURER PLASTICS
Optical sorters are typically used in single-stream MRFs for recovering and sorting PET from the rest of the material stream. By adding optical sorting units, MRFs can recover 90 percent to 95 percent of the PET in their incoming material stream, TiTech’s Wolf says. "No one tries to sort PET manually anymore."
OPTICAL OPTIONS Infrared (IR) spectroscopy, which includes near-infrared as well as mid-infrared radiation, is commonly used in optical sorting units to identify and sort different materials, such as PET (polyethylene terephthalate) bottles from those made of PLA (polylactic acid) or PVC (polyvinyl chloride). Near-infrared spectroscopy also can sort plastic containers from the other material collected through single-stream programs. Optical sorting units also employ visible light to discern color and can be used to sort natural, or clear, objects from colored objects, says John Thomsen, engineering manager, National Recovery Technologies, Nashville, Tenn. "Two examples of this are the separation of clear and colored PET and the separation of natural and colored HDPE (high-density polyethylene)," he says. "This is a very versatile application and is usually lower cost than IR methods," Thomsen says. With IR spectroscopy, the portion of the spectrum used depends on the properties to be detected, he says. "IR is more expensive, but is very useful to distinguish among substances that are very similar in the visible spectrum." While both methods can be flexible and calibrated to perform different sorting tasks, the rest of the processing line at the material recovery facility (MRF) also has a role to play. Thomsen says in a given installation "a machine is frequently justified and purchased for a specific task, and we notice that the task rarely changes over the years. The entire process line is often less adaptable to change than is a particular optical sorting machine that is part of the process line." Optical sorting units also can incorporate metal detection technology based on induction to sort metals with high recovery rates about 97 percent, says Alex Wolf, sales engineer for Germany- and Norway-based TiTech, which is distributed in North America by Lubo USA, Stamford, Conn.
According to Hottenstein, generally 10 percent of the material collected through single-stream programs is plastic containers, while fiber makes up 70 percent. PET generally accounts for 40 percent to 50 percent of the plastic containers.
He adds that the number of PET bottles in the recycling stream has increased, though their weight has decreased because of lightweighting efforts by manufacturers. This makes sorting by hand more challenging in existing MRFs where space is limited.
If a MRF is able to replace three people on a single shift by incorporating an optical sorting unit, Hottenstein says the option becomes interesting to MRF operators. Not only can the overall PET recovery rate improve through the use of optical sorting units, the purity of the recovered material also tends to be higher because the optical sorter can better distinguish PVC (polyvinyl chloride) or PLA (polylactic acid) containers from PET containers than the human eye.
Adding optical sorting generally improves the quality of the end products and leads to a much more consistent yield compared to hand sorters, Wolf says.
"In the past, high recovery was more important than purity, so a process might have been designed to recover 99-plus percent at 90 percent purity," Thomsen says. "In today’s depressed markets for recovered materials, the high recovery rate is still important, but the purity needs to be high in order for the recovered material to be marketable. With proper techniques, 99-plus percent purity is achievable."
Wolf adds that some MRF designs double sort the sorted plastics, reducing the need for manual labor even more.
In addition to using optical sorting technology for PET, MRFs may sort HDPE optically as well, Hottenstein says. "Because those bottles are large, heavy and easy to sort, it generally takes a larger volume to justify an optical sorter for HDPE," he adds.
Some MRFs also employ optical sorting to improve recovery and purity of ONP and OMP (old mixed paper). "The manual labor component to clean up the ONP and OMP is still very significant in most MRFs, and by adding optical sorting the operators can improve the quality and consistency of the products," Hottenstein says.
In today’s challenging environment, quality and consistency may provide MRFs with the edge they need to continue moving the bales they create from the commingled material that is delivered to their tipping floors each day.
The author is managing editor of Recycling Today and can be contacted via e-mail at dtoto@gie.net.
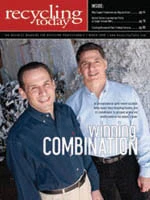
Explore the March 2009 Issue
Check out more from this issue and find your next story to read.
Latest from Recycling Today
- Lindner shredders prepare Brazilian plastic for recycling
- China ups steel output while other nations cut back
- ReElement, Posco partner to develop rare earth, magnet supply chain
- Comau to take part in EU’s Reinforce project
- Sustainable packaging: How do we get there?
- ReMA accepts Lifetime Achievement nominations
- ExxonMobil will add to chemical recycling capacity
- ESAB unveils new cutting torch models