The focus in the secure document destruction industry is on the front end, providing customers with the security and service they expect from such a vendor. But secure destruction professionals often have an eye toward the back end, as well, as they are producing a saleable commodity in the form of shredded paper.
However, paper mills have been known to bemoan the quality of the shredded paper they receive, citing the material’s contaminants and lack of uniformity as the primary problems.
As a former information destruction professional, Sheldon Green-span knows the problems associated with marketing shredded paper to mills and paper recyclers. Green-span, formerly of Canada-based Eco-Shred, heads up Hanaar Corp., Mississauga, Ontario. The company markets the Hanaar System, which uses optical sorting technology to separate shredded paper by color and grade.
LAB RESULTS Mississauga, Ontario-based Hanaar Corp., developers of the Hanaar System, an optical sorting system for shredded paper, will open a demo lab and test facility in the greater Toronto area by Labor Day of this year. "It’s a big step for us," says the company’s Sheldon Greenspan. The facility will include a complete Hanaar sorting system as well as a shredder, so the company can bring in shredded and unshredded paper for processing. In addition to offering testing for prospective customers, the plant will also offer sorting to companies that do not produce the volume needed to economically install the Hanaar System at their own facilities.
The Hanaar System incorporates equipment manufactured by Key Technology of Walla Walla, Wash. (www.key.net.). Key Technology specializes in manufacturing automated technologies for processing food, plastics and other specialized products. "They are the world leaders in food sorting and food producing equipment and technologies," Greenspan says.
Together, Greenspan and Key have quietly been working on the Hanaar System for more than five years, Greenspan says. "I don’t know of any other technology that can do what we do," he says of the resulting sorting system.
Greenspan recently spoke about the Hanaar System at the 2007 National Association for Information Destruction (NAID) Annual Conference, which was April 10-13 in Orlando, Fla., and he talked with Recycling Today about the system’s potential.
SYSTEM SETUP. Greenspan prefaced the comments he made during his NAID session by saying that a company must process at least 400 to 500 tons per month to justify the expense of the Hanaar System. Processing speeds with the system may be slower than most companies are comfortable with, but Greenspan said that "by slowing down a little, you can get more on the sale end." A 20 percent reduction in processing speed can increase an operation’s yield and decrease wear and tear on its equipment, he added.
Operations with the goal of getting material through the system as quickly as possible are not the system’s ideal users, according to Greenspan. "With that mindset, it’s difficult to implement our system."
The Hanaar System is designed for plant-based shredder operators. It requires 1,500 square feet of plant space, and buildings with higher ceilings are preferred, according to Greenspan.
The system is composed of an air compressor that uses instrument-quality dry air, conveyors, Hanaar’s proprietary buffer, fluffer and ISO-flow systems, the sorter itself and an "accepts" and "rejects" container, all of which can be installed between the shredder and baler of an existing system, Greenspan says. He also recommends a dust control system, not because the process itself generates dust, but because it liberates the dust that is created during the shredding process.
The Hanaar System requires a cross-cut shred with a minimum size of 1.2 millimeters (1/20th of an inch) as opposed to a strip shred, which could cause problems with tangling and winding. "The more consistent the shred is, the better our system performs," according to Greenspan.
The shredder style also affects the system’s performance and must be considered prior to installation, and the system must be calibrated accordingly. Each different style of shredder has its own "shred personality," Greenspan says, that behaves differently within the system. For instance, hammermills produce a light and fluffy shred, while pierce and tear shredders produce a denser shred, Greenspan said, and the shaker system would have to be adjusted with that in mind.
"We are working hard on being compatible with as many shredders as possible," Greenspan says, though he adds that the company has not yet tested the output from all the mobile shred trucks on the market. The company is gaining experience with shred trucks manufactured by Shred-Tech and Vecoplan, he says. Pierce-and-tear and rotary shredders are the shredder types the Hanaar System is focused on serving, Greenspan says.
The Hanaar System’s buffer serves to meter and feed the shredded material to the fluffer, which breaks the chunks of shredded material to optimize the spread of those shreds onto the ISO-flow device. The ISO-flow device removes the dust and small particulate material, such as staples, from the shredded paper, Greenspan says. From here, the paper goes into the sorter, which can be calibrated to sort the material based on different criteria. "It’s important to understand what you are starting with and what you want to finish with," Greenspan says.
"It is our intention to make it simple to integrate into existing operations," he says of the Hanaar System.
SYSTEM MAINTENANCE. Once the Hanaar System in installed, the keys to its proper operation include keeping it clean and not over-feeding it, Greenspan says.
The company also offers a service package that includes preventative maintenance.
Keeping the lenses on the optical sorter clean is an important maintenance consideration. Greenspan said that lenses typically need to be wiped down once every four hours, when running. However, if processing material from a grinder, the lenses may need to be cleaned more frequently because of the dust.
THE END RESULT. According to Greenspan, a document destruction firm can realize a number of advantages by adding optical sorting equipment like the Hanaar System to its operation.
Greenspan said the Hanaar System can help document destruction firms eliminate sorting labor, which can offer a security advantage, but it can also help a company improve its relationships with the mills it supplies by helping shredding operations to produce a consistent grade that corresponds to SWL (sorted white ledger)/CPO (computer printout).
With an infeed consisting of 80 percent white office paper to 20 percent colored paper, Greenspan said the Hanaar system can successfully sort 73 percent of the white fiber.
He adds that a document destruction firm can see sell its sorted shredded paper as SOP, realizing as much as a $100-per-ton increase in prices, which does not take into account the labor savings realized by adding the Hanaar System to its operation.
The system’s sorting parameters can also be adjusted to create packs that are unique to a particular mill. Groundwood can also be targeted using the system, though this would involve additional modifications to the layout and camera system, Greenspan added.
"The objective is to strengthen your relationship with your mills by improving quality and removing a significant level of dirt," Greenspan said. "Mills love quality. Quality pays, and so does consistency."
The author is managing editor of Recycling Today and can be reached at dtoto@gie.net.
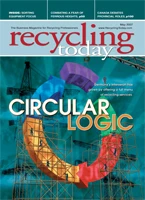
Explore the May 2007 Issue
Check out more from this issue and find your next story to read.
Latest from Recycling Today
- Nucor receives West Virginia funding assist
- Ferrous market ends 2024 in familiar rut
- Aqua Metals secures $1.5M loan, reports operational strides
- AF&PA urges veto of NY bill
- Aluminum Association includes recycling among 2025 policy priorities
- AISI applauds waterways spending bill
- Lux Research questions hydrogen’s transportation role
- Sonoco selling thermoformed, flexible packaging business to Toppan for $1.8B