The flow of scrap paper into your operation has been increasing steadily within the last year. Lately, you have noticed your closed-end horizontal baler hasn’t been keeping up with the new volume and your staff is spending more of their time tying bales.
Maybe it’s time to upgrade to a higher-production baler, such as an extrusion-style baler?
Or perhaps your operation has been unable to use one of your two-ram balers to its full capacity and you are considering downsizing to an extrusion baler to save on operating costs.
Whether you are upgrading to a larger machine or downsizing to better fit your operation’s needs, it is imperative to select your extrusion baler carefully, because the wrong one can have a negative effect on production.
CONSIDER THE SIGNSTom Sustersic, president of Gateway Recycling in Cleveland, says recyclers should upgrade to an extrusion-style baler if they’re debating whether to hire another employee to assist in tying off the bales. "If your guy is spending 15 minutes per hour tying off bales, then you should consider purchasing an extrusion baler with auto tie," Sustersic says.
With closed-end balers, recyclers are limited in the volume and type of material they can process because the balers lack an extrusion chamber and the bales they produce must be tied manually. An extrusion-style baler can alleviate this problem, as it is designed to produce continuous bales and facilitates switching between various types of material without risking contamination.
Extrusion balers are also known for their speed and their ability to produce heavier bales compared to closed-end horizontal balers. "Some single-ram, extrusion-style balers can produce up to 40 tons of bales per hour," says Lee Cornell, recycling market manager for Firstar Fiber in Omaha, Neb. "Larger and heavier bales mean less handling per bale."
Unlike closed-end balers that produce a fixed bale size, extrusion balers can produce bales that can be adjusted to meet specific weights and lengths, says Tony Metauro, COO of Metro Waste Paper Recovery Inc., Toronto. "Changing bale lengths enables our forklift operators to cube-out whatever shipping unit they are loading, whether it is rail cars, 20- to 53-foot trailers or 20- to 40-foot export containers," Metauro says.
Another sign that it might be time for a recycling operation to upgrade its baler is if the company’s current balers have difficulty handling the facility’s throughput or if the balers are producing bales that are ungainly to handle.
If domestic mills using van trailers are the primary buyer, Cornell says a recycler can use an extrusion baler to load these bales more quickly because of the bales larger size and weight.
Recyclers also agree the right time for an operation to purchase an extrusion baler depends on its monthly tonnage and how much capital the company has to spend on a baler. "Someone with a lot of capital producing 300 tons a month can purchase a extrusion baler even though they don’t really need it," says Mitch Davis, vice president of Midland-Davis Corp, Moline Ill. "But if you’re producing 1,500 to 3,000 tons a month, you better have an extrusion baler, unless you want to be working 24 hours a day," he adds.
COMPARISON SHOPPINGRecyclers should take into account their incoming material when purchasing an extrusion baler. Recyclers say extrusion balers are best suited for materials such as paper and cardboard, but they can also bale materials such as plastic bottles and beverage cans.
Cornell adds that while extrusion balers can bale all types of paper, they tend to perform better on OCC (old corrugated containers), ONP (old newspaper) and SOP (sorted office paper) than on magazine or coated book. He says paper packing operations that produce and export a number of various paper grades may want to forego an extrusion style baler and move straight into a two-ram baler. Two-ram balers are designed to handle larger and bulkier materials, such as large cardboard, plastics and aluminum.
"Many paper processors use two-ram balers if they do a lot of export," Cornell adds. "Bales from a two-ram baler are a consistent size and weight and can cube out an export container more fully."
Metauro agrees that OCC and mixed paper are probably the easiest grades of paper to bale with an extrusion model, but he adds that with a fluffer (paper conditioner) the balance of the paper grades can be baled just as easily.
Recyclers should take three factors into consideration when shopping for their next baler, Gateway’s Sustersic says. These are size and type of incoming material as well as the volume processed per hour.
Considering these three factors helped Sustersic when he purchased his two single-ram, auto-tie extrusion balers and two-ram baler. With three facilities in Cleveland, Toledo and Lima, Ohio, Gateway handles scrap paper and corrugated packaging and provides secure document destruction services.
The extrusion baler Gateway uses in the confidential destruction room is sized for shredded material, featuring a 30-inch hopper and a maximum capacity of seven tons per hour. The extrusion baler in the recycling room is sized to handle high grades of paper and is equipped with a 60-inch-by-50-inch hopper. The company’s two-ram baler is used to compact bulkier grades of paper and plastics.
"We sized the machines according to our production rate, staying well aware of electrical power needs and costs, which allow our company to make environmentally responsible decisions," Sustersic says.
It is also important to note that not all recyclers are looking to purchase an extrusion baler to increase their processing capabilities. Keith Ristau, president of Far West Fibers, Portland, Ore., says the company currently uses two-ram balers to process materials such as cardboard, newspaper, metals and plastics. However, he says that when it comes time to purchase another baler for the company, the extrusion baler’s cost effectiveness appeals to him. "The three biggest benefits of an extrusion baler are it puts out more tons per hour, uses less energy and makes bales that are easier to ship," Ristau says.
Midland-Davis has not only considered downsizing from a two-ram baler to an extrusion baler, but has actually made such a switch at the company’s Moline facility. Davis says factors that led the company to make such a change include the extrusion baler’s speed, the fact that it ties bales lengthwise and contains a side ram that makes it easier to load cardboard, which is what the company spends three-quarters of a typical day processing.
PRICE CHECKWhile extrusion balers are more expensive to purchase than vertical and closed-door horizontal balers, recyclers say they recoup the additional cost by being able to handle multiple materials and produce bales of varied lengths.
Ristau says that while extrusion balers are more expensive, they generally are also more efficient and faster than vertical and closed-door models. "Recyclers have to weigh out how much more they are willing to pay to gain these efficiencies," he suggests.
When it comes to actual baler pricing, Metauro says recyclers with smaller volumes of incoming material can purchase machines closer to the production range they require and pay accordingly, thus making this type of baler less costly. He also says for recyclers producing at high levels (greater than 8 tons per hour) the cost starts to be slightly less than or the same as that of a two-ram baler.
Firststar’s Cornell says extrusion-style balers also make up for their higher initial cost over time in a number of ways, including:
• Using less wire per bale;
• Requiring less maintenance than balers with more moving parts;
• Consuming less energy in light of
their lower motor size;
• Lowering an operation’s staffing re-quirements in light of increased throughput; and
• Lessening the cost of rebuilds.
Ristau says extrusion balers generally require less maintenance and incur less wear and tear than two-rams. To keep them operating efficiently, recyclers suggest preventive maintenance, such as periodically changing or flipping the blades and inspecting the wire tie mechanism daily.
"It is also crucial for recyclers to maintain a tight shear gap—around 1/8 inches," Cornell says. "If this gap gets larger, it can cause the baler to work harder, shearing paper in the chamber. This can cause the baler to split and cause parts to be out of alignment," he adds.
The author is assistant editor of Recycling Today and can be contacted at kmorris@gmail.com.
WANT MORE?
Enter your email to receive our newsletters.
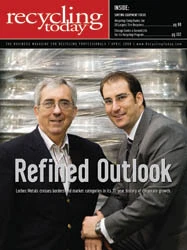
Explore the April 2008 Issue
Check out more from this issue and find your next story to read.
Latest from Recycling Today
- Athens Services terminates contract with San Marino, California
- Partners develop specialty response vehicles for LIB fires
- Sonoco cites OCC shortage for price hike in Europe
- British Steel mill’s future up in the air
- Tomra applies GAINnext AI technology to upgrade wrought aluminum scrap
- Redwood Materials partners with Isuzu Commercial Truck
- The push for more supply
- ReMA PSI Chapter adds 7 members