
Since installing an auto shredder in 2004, Mansfield, Ohio-based Milliron Iron & Metal Inc. has undergone a number of upgrades to its downstream recovery system that were designed to improve the volume and purity of nonferrous metals recovered from its shredded material.
The company’s most recent upgrade, which at the time of this interview in mid-November was in the final stages of commissioning, will allow Milliron Iron & Metal to process its auto shredder residue (ASR) fines for the first time since installing its auto shredder.
Regarding this recent upgrade, Milliron Iron & Metal President Grant Milliron says processing ASR fines is a necessary step for auto shredder operators as margins become tighter. “You have to mine all the nonferrous you can from the ASR,” he says.
Milliron says the benefits of increased recovery of nonferrous metals from ASR fines are twofold. “For every pound we can take out of there, we are not taking that to the landfill,” he says. Not only does Milliron Iron & Metal avoid the costs associated with landfilling this material, the company also makes money from selling the metals it recovers.
A series of upgrades
Milliron Iron & Metal’s Texas Shredder model TS 98/104 auto shredder processes from 18,000 tons to 20,000 tons per month, Milliron says. He describes the shredder’s infeed material as consisting of 40 percent cars and 60 percent “miscellaneous sheet.”
Milliron says his company sources its auto shredder feedstock from within Ohio as well as from neighboring states. “We have a very good network,” he adds.
The company’s original nonferrous recovery system was installed at the same time as its shredder and includes eddy currents and sensor sorting technology.
Within a few years of installing this original nonferrous recovery system, Milliron Iron & Metal began expanding its downstream nonferrous sorting capabilities. In 2009, the company added a dry media plant equipped with X-ray and optical sorting technology.
The next major upgrade was commissioned in 2013 and involved the installation of an ICW (insulated copper wire) recovery plant.

Milliron says, “We’ve done a lot in a few years,” adding that each installation allowed the company to extract that much more value from the feedstock it had already paid for. “Every time you put this through equipment, you are going to recover metal and upgrade your pricing.”
Milliron continues, “You can install one nonferrous recovery building and think you are doing a very good job. Then you could add a redundant recovery building, and you would be surprised how much you are missing.”
Using its dry media plant, Milliron Iron & Metal is further processing the zorba produced by its downstream sorting system to make furnace-ready products, he says.
Going deeper
Now, Milliron Iron & Metal is in the final stages of commissioning a RecoverMax Fines Process from Best Process Solutions (BPS), Brunswick, Ohio.
This installation will give the company four different processes designed to maximize the recovery and purity of nonferrous metals: a nonferrous recovery system, a dry media plant, the ICW system and the RecoverMax Fines Process, which is designed to recover metal pieces sized greater than 1 millimeter.
The heart of the fines recovery process is the RecoverMax Separator from BPS, which claims to separate metal from glass and rocks with a purity in excess of 98 percent. A final step separates high-copper zorba into a 90-plus copper and precious metals fraction to be sold as a refinery-grade product, according to the company.

The installation also includes a primary system before the BPS system that features a large trommel gas drier to get the moisture content of the ASR fines down from 20 percent to 12 percent, Milliron says. This aids in the removal of the light fraction, or fluff balls, using an aspirator and a cyclone from Germany-based Yost. Then two magnets from Steinert, with U.S. offices in Florida, remove ferrous solids and ferritic dirt before the remaining material is conveyed to the RecoverMax system, which Milliron refers to as the “polishing system.”
He says, “We knew there was metal in the microfines because we had tested our material at other manufacturers’ facilities.
“We tried our best to evaluate what was the best purchase to get the best recovery; we did our due diligence,” Milliron continues. “We like to do our homework on every system that we are going to buy. You have to do careful evaluation before you make a commitment to these kinds of dollars.”
Milliron says he purchased the RecoverMax because it produced “the cleanest product of anything I have seen,” adding that by appearances it is 98 percent metal.
Before running tests processing Milliron Iron & Metal’s material with the RecoverMax, Milliron thought he had found the system he was going to purchase, he says. “It was less money, but the recovery was not as good,” compared with the RecoverMax process, he adds.

Milliron Iron & Metal will produce two finished product sizes using its RecoverMax System: a very fine 0-to-4-millimeter size and a 4-to-12-millimeter size, he says. “The small fraction will go to a refinery directly, and the other is going to be like a zorba with a heavy concentration of copper within the aluminum,” Milliron says. “We will be able to extract a lot of that copper from that portion and end up with a very fine, clean what I call microfine zorba—we will never get all of the copper from it, but we will get a large majority of it. And that is a very interesting part of this project.”
The company will be producing a No. 2 copper grade, a refinery grade and a zorba grade. Milliron says consumers may want all three sizes in one package or particular packages based on size; he is not yet sure. “We have planned ahead that we can develop three different products here going to three different refiners,” Milliron adds.
From shopping through to commissioning, he says a year-and-a-half will have passed. “I wrote the check in January 2016.” Manufacturing and installation required 11 months, Milliron says, with a majority of that time spent in engineering.
Milliron Iron & Metal began the initial startup of the system in November, and by mid-month Milliron says the company is not yet operating at full production. “In another month, it will be,” he adds, which will be late December.
Milliron says he evaluated a number of factors beyond the system’s recovery capabilities, including durability and maintenance and staffing requirements.
“One of the luxuries is that the polishing part can be operated with two people,” he says.

The system also requires a “lighter degree” of maintenance compared with some of the other available options, Milliron says, noting that chutes and screens will need to be cleaned prior to startup and greasing will need to be performed daily.
Running the numbers
Milliron says his company plans to operate its ASR fines recovery system for one shift initially, though he has not ruled out running two shifts in the future.
Milliron Iron & Metal initially plans to process material it has been stockpiling since it ordered the equipment in January, he says. At some point, the company may begin buying third-party material, Milliron says, adding that he’s already received calls from other processors who want to know if he is buying material.
“You have to have large tonnage to justify this expense,” Milliron says of the microfines recovery system.
If the company solely processes its ASR fines, Milliron says he expects a three-year return on investment “because we had a jump start on the total cost. We had extra floor space in our media building, plus we had extra capacity with our dust collection system and our oversized air compressor, ample primary electricity and under-roof storage for the waste destined for landfill.”
Early indicators are positive, Milliron says. “We are very pleased looking at the metal recovery. The end product is everything I thought it would be based upon the preliminary startup.”
Get curated news on YOUR industry.
Enter your email to receive our newsletters.
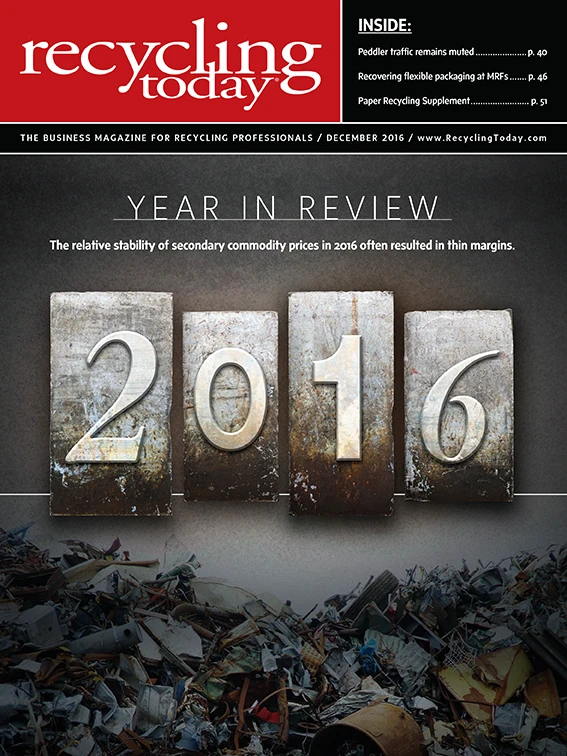
Explore the December 2016 Issue
Check out more from this issue and find your next story to read.
Latest from Recycling Today
- AF&PA report shows decrease in packaging paper shipments
- GreenMantra names new CEO
- Agilyx says Styrenyx technology reduces carbon footprint in styrene production
- SABIC’s Trucircle PE used for greenhouse roofing
- Hydro to add wire rod casthouse in Norway
- Hindalco to invest in copper, aluminum business in India
- Recycled steel price crosses $500 per ton threshold
- Smithers report looks at PCR plastic’s near-term prospects