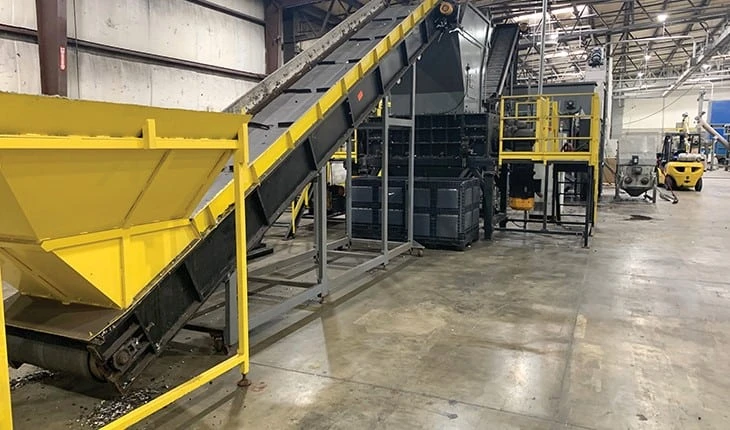
Photo courtesy Plastics Recycling Inc.


Electronics shredder residue (ESR) has long bedeviled plastic recyclers, but the decision to invest in dedicated sorting technology for that difficult material is paying off for Plastic Recycling Inc. (PRI) in Indianapolis.
PRI started its new ESR sorting line in October and was processing 6,000 pounds per hour as of June, running four 24-hour shifts per week. The goal is to significantly increase throughput and to offer manufacturers of electronic products in the U.S. a true circular economy solution for their plastic.
ESR, which is the material that remains after electronics scrap is shredded and the valuable metals are removed, still contains a great many small pieces of metal and other impurities, but the biggest problem is that every bale or box of it contains a wide range of polymers, says Brandon Shaw, PRI marketing manager.
“We basically have the whole chain,” he says of PRI’s processing capabilities. “Plenty of companies can do the sorting but they don’t have the compounding knowledge that we have, and they have to rely on someone like us to buy their clean flake.
“We go all the way downstream from the e-waste shredder back into a pellet. That is our competitive advantage,” Shaw says. “A lot of companies have failed when they tried to do this because they had to rely on the market to dictate pricing. We can take that factor out of the equation.”
Shaw says PRI will expand from running ESR for four days per week to seven days as soon as labor is available. PRI also is looking at starting satellite plants in the Southeast and West to do initial processing of ESR that can then be shipped to Indianapolis for final processing.
PRI decided to invest $2 million to start recycling ESR when it recognized an opportunity to take advantage of a low-cost feedstock stream that traditionally had been exported.
“With all the restrictions on moving waste to other countries, we saw opportunity in a big glut of material that was going to have to stay domestic,” Shaw says. “We saw an opportunity to feed our extruders. We have a big demand for recycled PS [polystyrene] from our existing customers.”
Amendments to the Basel Convention on the Control of Transboundary Movements of Hazardous Wastes and their Disposal that went into effect Jan. 1 has caused most electronics scrap to stay in the country where it is generated. Prior to Jan. 1, much of the electronic scrap from the U.S. was sold to companies in Asia. Earlier, China’s crackdown on scrap imports disrupted markets for that material.

PRI’s sorting goal is to extract four polymers it can use—acrylonitrile butadiene styrene (ABS), PS, polypropylene (PP) and polyethylene (PE)—from the 13 to 15 polymers typically found in ESR. Extracting 50 percent of useful material from each load is the target. The other 50 percent is currently waste, but the company says it hopes it can eventually find markets for that, as well.
PRI brings in shredded material and first puts it through another shredder, then removes the metal. Next comes a series of three tanks for density separation. The next step is a proprietary technology that creates a half-inch regrind that is free of labels, felt, rubber, wood, dust and other contaminants. Next is a series of six dryers and electrostatic separation. The material also goes through a color sorter, if needed.
The output is white, black or gray ABS, PS, PP and PE flakes.
The new sorting line uses grinders from Cumberland, Vecoplan and SSI shredders, Gala dryers, Bunting magnetic removal equipment and an optical color sorter from AMVT.“Each box that comes out of here is 98 percent pure,” Shaw says.
PRI’s recycling plant is 150,000 square feet and is called the State Avenue facility. The clean flake is transported to PRI’s nearby 550,000-square-foot Rockville Road compounding plant, where it is blended or modified for a specific customer’s order, then extruded and turned into pellets. “We can make material from 10 percent to 100 percent recycled content,” Shaw says.
PRI has eight extrusion lines. Additionally, a 90-millimeter twin-screw from Coperion was added as part of the ESR expansion.
The plastics recovered on the ESR line are going into resin compounds for many of PRI’s customers, which primarily manufacture consumer products.
The company is working through the process of getting resin containing plastics recovered from ESR certified for use in electronics. “It is new,” says Josh Barrick, business development director at PRI. “It is a process to get things approved at these OEMs. We are working through that, and we are working on some certifications for our material.”
Some of the plastics recovered from the ESR material also find their way into plastic cores for the paper industry. PRI owns a company called Recycling Technology Inc. that has 18 profile lines running that product nonstop. Barrick says adequate feedstock is available within a 300-mile radius of Indianapolis, plus there is plenty more feedstock in other parts of the country.
Barrick estimates about 55 million tons of end-of-life electronics are generated every year worldwide. About 12 percent to 13 percent of this material is collected and recycled. The U.S. produces about 20 percent of the world total, or about 11 million tons per year. The electronics scrap companies that collect it mostly are interested in reclaiming and reselling the metal.
“Only about 20 percent of e-waste is plastic, and that includes a bunch of different mixes,” Barrick explains. “That is something we can collect and turn into pellets” with the new processing line.
PRI’s business model is to run trial batches of ESR material supplied by an electronics recycler, then decide on a price based on the yield of useful plastics in the batch. PRI then guarantees that price unless the useful yield declines.
Resin demand is strong, and PRI is running at full capacity, Barrick says.
Throughput of the ESR line could be doubled with a small investment in additional machinery, Shaw says.
As of June, the company is closing on the sale of a larger building in Cowpens, South Carolina, to expand an operation it purchased two years ago. A second 150,000-square-foot building also is being considered for the State Avenue site in Indianapolis.
Part of the growth is to accommodate a growing business in recycling appliance scrap, primarily refrigerators and washing machines.
“We want to offer a circular economy solution for these companies as well,” Shaw says.
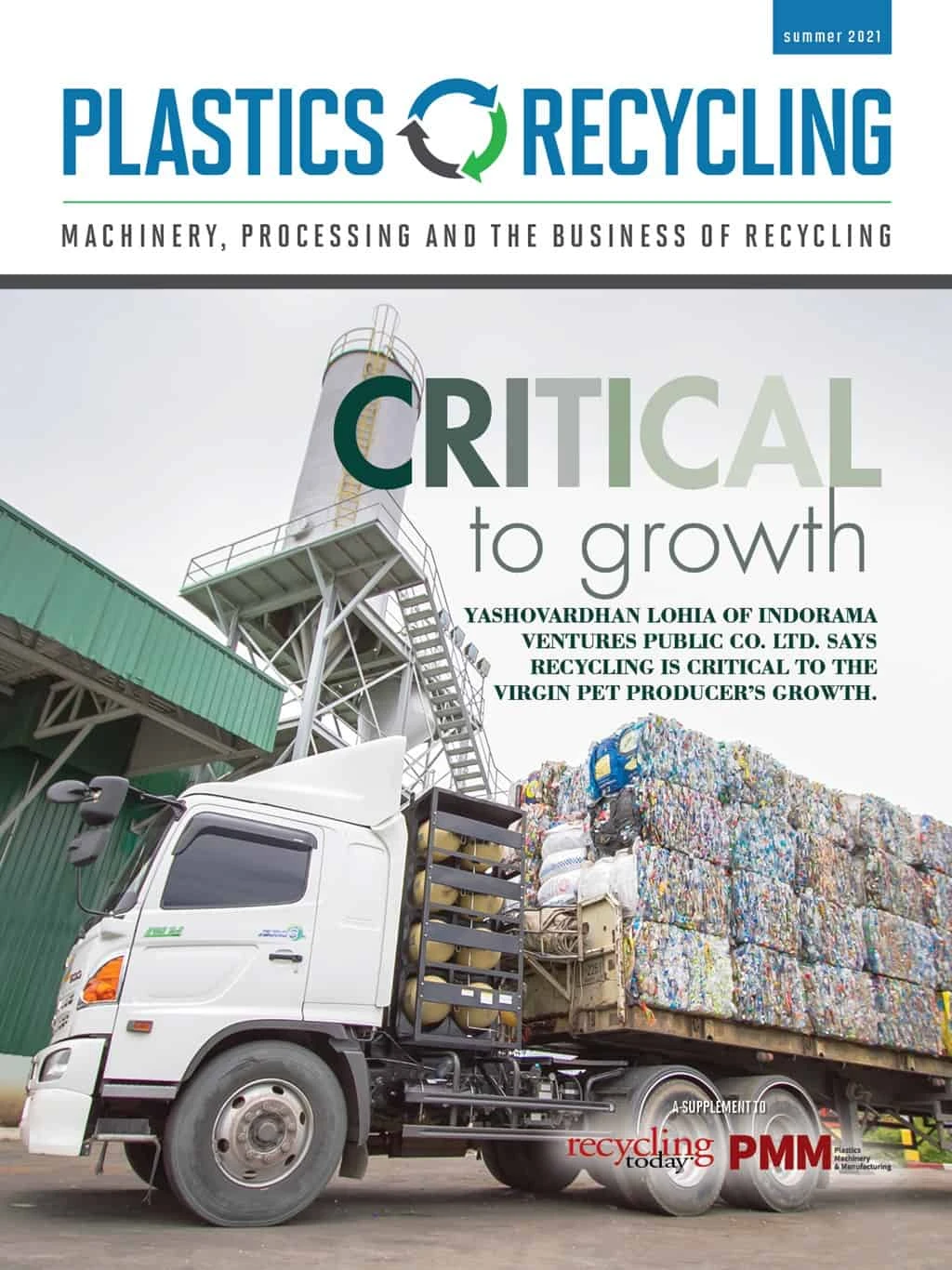
Explore the Summer 2021 Plastics Recycling Issue
Check out more from this issue and find your next story to read.
Latest from Recycling Today
- Astera runs into NIMBY concerns in Colorado
- ReMA opposes European efforts seeking export restrictions for recyclables
- Fresh Perspective: Raj Bagaria
- Saica announces plans for second US site
- Update: Novelis produces first aluminum coil made fully from recycled end-of-life automotive scrap
- Aimplas doubles online course offerings
- Radius to be acquired by Toyota subsidiary
- Algoma EAF to start in April