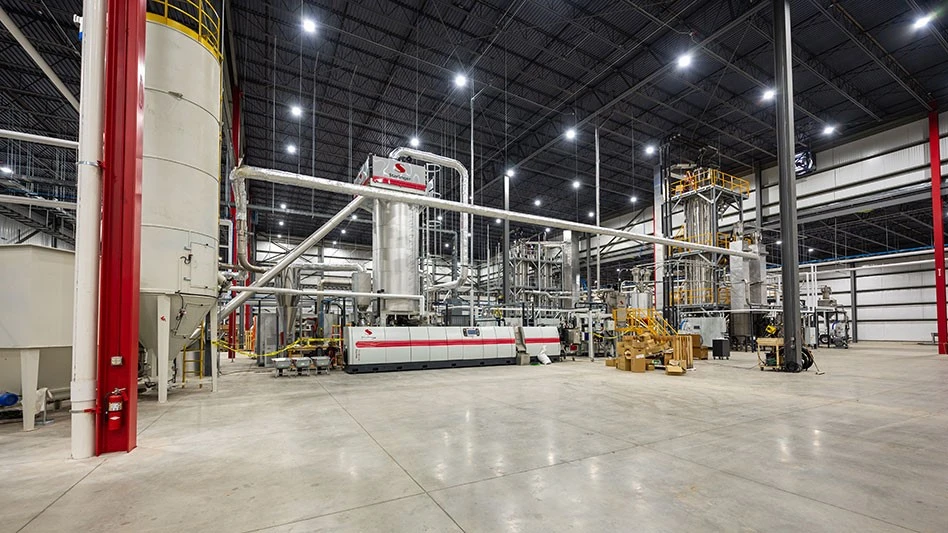

Evergreen Plastics, now known simply as Evergreen, was founded in 1998 as a division of Mentor, Ohio-based Polychem LLC, which rebranded as Greenbridge last year. Soon after its founding, Greenbridge says it gained a reputation for having a broad line of poly-ester, polypropylene and cord strapping.
As it grew, the company saw the need to establish a recycling division—Evergreen—to produce recycled polyethylene terephthalate (rPET), ensuring a steady supply of 100-percent-recycled PET for its portfolio of strapping and cord products while also creating new markets for rPET and other recycled materials.
In 2021, Evergreen expanded from a single location in Clyde, Ohio, to four locations across North America following the acquisitions of the former UltrePET plant in Albany, New York, the former CarbonLite plant in Riverside, California, and Novapet in Amherst, Nova Scotia, making it one of the largest PET recyclers and rPET producers in North America. Now, with the recent expansion of its Clyde facility, Evergreen has its sights on becoming the largest rPET facility in the world.
Continued growth
Evergreen announced in April 2021 it was undergoing a $22 million expansion to double its food-grade rPET processing capacity from approximately 40 million pounds annually to 80 million pounds annually. Originally, the site was intended to produce feedstock for Greenbridge, but the decision to pivot came in response to increased global demand for recycled content in plastic packaging.
“We made a decision to change that model completely and make it a high-end, food-grade rPET pellet manufacturer,” Evergreen CEO Omar Abuaita says. “We spent an awful lot of money, not just really expanding organically but also upping the quality level of the existing two [extrusion] lines. “

The upgrades were funded in part by a $5 million investment from the American Beverage Association and the Ohio Beverage Association in partnership with New York City-based Closed Loop Partners. Half of the investment is from the American Beverage Association in partnership with Closed Loop Partners through the Every Bottle Back initiative, and the other half is from Closed Loop’s Infrastructure Fund.
“America’s beverage companies are carefully designing our bottles to be 100 percent recyclable, and we want them all back so they can be remade into new bottles, as intended,” Megan Daum, vice president of sustainability at the American Beverage Association, Washington, said at the time the organizations announced the investment. “Increasing the use of postconsumer-recycled material in our bottles is a top priority of our industry, which is why we’re making critical investments in recycling infrastructure, like we have done with Evergreen. Public-private partnerships like these are essential in driving solutions to close the loop on our bottles and reduce the use of new plastic.”
Initially, the Clyde facility’s expansion included the construction of a 54,000-square-foot building to house four high-volume extrusion lines, which increased its processing capacity to 11.8 billion PET bottles to produce 113 million pounds of food-grade rPET annually, and the company built in some extra room for an additional two extrusion lines if needed.
In an interview with Plastics Recycling in late August, Abuaita confirmed that Evergreen has ordered both additional extrusion lines after securing enough supply to fulfill its increased customer demand.
“We don’t promise customers supply that we cannot fulfill,” he says. “We wait until we secure the raw material. Once we have security of supply of raw material, we’re more than able and willing to write the check for another line or another greenfield facility—whatever it is.
“Our customers would love for us to double our footprint and double our throughput,” Abuaita adds. “We’d love to do that as well, and we’re willing and able, but until we have security of supply, we don’t do it. That’s not our style.”
Evergreen offers rPET resin in pellet and flake formats, both clear and green. With the addition of two extrusion lines—bringing Clyde’s total to six—the facility will have the ability to produce up to 173 million pounds of food-grade rPET annually. Abuaita says the upgraded capacity at the Clyde site makes it the largest rPET facility in North America in terms of actual production.
The company is not sacrificing quality for quantity, either.
“We added underwater pelletization as well as SSP [solid-state polycondensation] to those two lines, so now that brings it up to the absolute highest quality level you can get in rPET,” Abuaita says. “In addition to that, we added two new lines, [built] a brand-new building for it—a [near] 60,000-square-foot building that we commissioned July 22—and those two [additional] lines … more than doubled the plant facility in terms of throughput of food-grade, FDA- [U.S. Food and Drug Administration-] approved rPET.”
What makes the Clyde facility particularly unique, Abuaita says, is that it started by processing B-grade curbside material supplied by material recovery facilities (MRFs). Through its partnership with Louisville, Colorado-based Amp Robotics, Evergreen has installed robotic sorters (15 total throughout all its facilities), optical sorters and artificial intelligence to increase the quality of its feedstock.

“[We get sent] a lot of junk, and we’re constantly looking at technology to help us take out that junk,” Abuaita says.
“They cut their teeth on the most difficult stuff you could sort through and recycle, so there’s nothing that anybody could throw at the Clyde facility that they haven’t gone through,” he adds. “Folks are loving the fact that even though 20 years ago they were already [sorting] B-grade material, we’ve helped them with robots, with optical sorters, with the absolute latest and greatest technology, and they’re just eating it up and loving it.”
Strategic partnerships
Before taking over as CEO of Evergreen, Abuaita was the CEO of Greenbridge (then Polychem). He says Evergreen would send flake to Greenbridge, which would make strapping. “We changed that model completely,” Abuaita says. “We said, ‘These are going to be two separate companies.’”
The rebrand from Polychem to Greenbridge also allowed Evergreen to become its own company as he says the divisions were separated legally and financially. “Part of that strategy was to really transform [Evergreen] into a premier rPET resin producer in North America.”
That transformation began with what he calls a “massive” investment in the Clyde facility, which included the underwater pelletizers and SSP reactors for its two existing extrusion lines to ensure the highest quality standards, as well as the additional four lines.
The strategy also includes growth through acquisition, first with the facility in Riverside, then Albany and finally Nova Scotia, allowing Evergreen to address growing PET supply concerns by tapping into the supply of PET bottles across North America.
Abuaita says supply concerns are the “No. 1 issue” in the plastics recycling industry, but Evergreen has modeled itself to stay ahead of the game. He says the company has cultivated many great relationships with suppliers and adds, “We pay a premium over index to make sure that we have security of supply. We’ve always treated them well.”
Partnerships through initiatives such as Every Bottle Back with the American Beverage Association, the Ohio Beverage Association and Closed Loop Partners came about as investors saw Evergreen’s strategy unfold. Abuaita says the company’s plan already was in place, adding, “Other folks loved what we were doing and approached to invest, so it was after the fact.”

The next steps
Evergreen continues to eye acquisitions to grow its North American footprint and is looking for investments to continue its organic growth, too. Abuaita says the only factor holding the company back is the availability of raw material.
“The minute we figure out a way [to address that], we are heavily, heavily looking at the Southeast,” he says. “We are working with a number of municipalities, MRFs, states … to see if we could secure the raw material.”
As supply becomes more secure, Evergreen is looking beyond North America to expand its operations globally.
“The next stage for us is going to be international,” Abuaita says. “We’ve been [in the industry] for over 20 years, so we’re not one of those flash-in-the-pan sort of things. Our reputation speaks for itself. … We have extremely high standards in terms of quality [and] service, and we don’t promise anything that we can’t deliver. We don’t build in hopes that the raw material comes; we secure the raw material and we build—whether it’s new lines or new plants.”
Get curated news on YOUR industry.
Enter your email to receive our newsletters.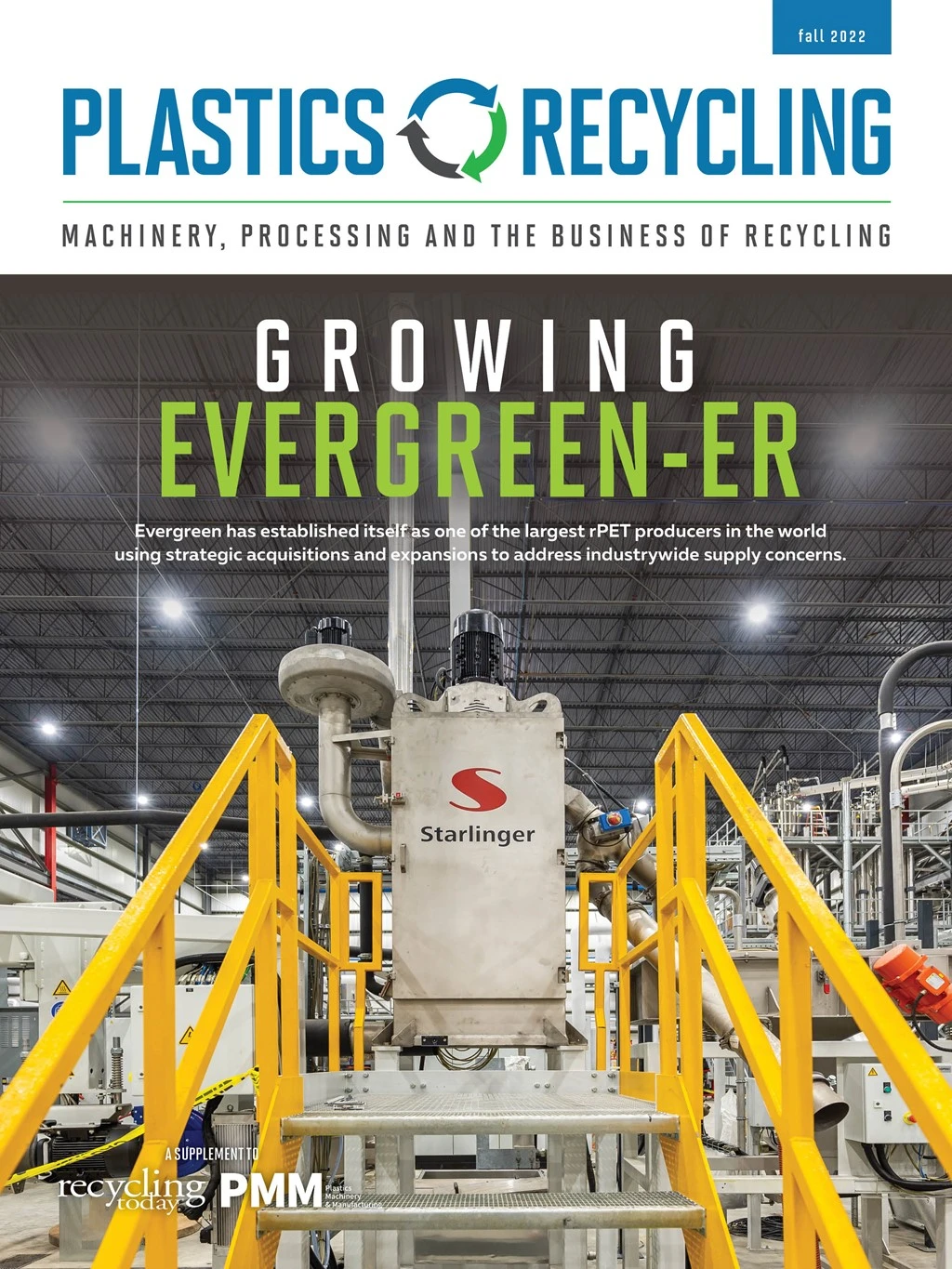
Explore the Fall 2022 Plastics Recycling Issue
Check out more from this issue and find your next story to read.
Latest from Recycling Today
- Altilium produces EV battery cells using recycled materials
- Brightmark enters subsidiaries of Indiana recycling facility into Chapter 11
- Freepoint Eco-Systems receives $50M loan for plastics recycling facility
- PET thermoform recycling the focus of new NAPCOR white paper
- Steel Dynamics cites favorable conditions in Q1
- Hydro starts up construction in Spain
- Green Cubes unveils forklift battery line
- Rebar association points to trade turmoil