Today, a demolition contractor can purchase many different types of equipment and attachments that are specifically designed for demolition work.
This chapter describes primary heavy equipment, support equipment and specialty equipment for demolition.
EXCAVATORS
The most common method of demolition now employed by the industry in North America is the use of crawler excavators equipped with a grapple or bucket and thumb attachment. These machines come in sizes of 5 tons to over 100 tons gross weight and can use several different types of booms and attachments to demolish a wide variety of structures.
Many excavators are equipped with a “quick mounting and release” mechanism that permits the operator to change attachments in a matter of minutes.
With the addition of another boom section known as a “third member” in the excavator boom, heights of over 100 feet can be reached. These excavators are in a class of machine known as “high-reach demolition machines” and are in the 30-ton to 150-ton class.
Using a shear, concrete pulverizer, concrete cracker or other attachments, a 10-story building can literally be “chewed” apart. These machines are replacing, to a large extent, the use of cranes to reach buildings and other structures of up to 10 stories.
A very important point in working with a high-reach demolition machine is to ensure that the machine is always operating over a very stable and reasonably level surface. The operator must have a good field of vision and usually works with a spotter who can signal as necessary, or a video camera can be mounted on the boom tip to give the operator a clear view of the work.
It is also important to operate the machine in such a manner as to keep the angle of the main boom within the limits of the machine capacity to prevent unbalancing. Water spray nozzles can be installed near the attachment to control dust and to allow the operator to see what he or she is doing in real time.
Smaller excavators are used extensively for floor-by-floor demolition techniques and for a variety of selective demolition requirements. Attachments commonly used with excavators include the following:
- Shears for cutting metal and concrete;
- “Crackers” used for fracturing heavy concrete;
- Impact hammers to break concrete not easily fractured by jawed attachments;
- Universal processors for breaking concrete into small pieces and shearing rebar;
- Breakers for breaking heavy concrete;
- Grapples for demolition and handling bulky debris; and
- Magnets.
CRANES
Without the use of modern cranes, many types of demolition projects would be far more difficult. There are no cranes manufactured strictly for the demolition industry. Cranes using wrecking balls must be classified as “duty cycle” cranes and allow the ball to free fall. Such tasks may include the following:
- Demolishing a building using a wrecking ball that may weigh 1,500 to 5,000 pounds;
- Lifting small equipment for use in high-rise and interior demolition;
- Demolishing a building with a clamshell bucket (to a large extent, the clam bucket has been replaced by the excavator and grapple attachment); and
- Lifting down sections of structures and equipment.
Cranes of all types are rated by their lifting capacity with a defined length of boom and a radius of lift. For example, a crane rating of 100 tons may be defined as the load limit of that particular crane with 60 feet of boom at a distance of 15 feet from the center of gravity of the crane to the point of attachment of the load.
Every crane must have a lifting chart that shows safe operating ranges available to the operator so that overloading can be prevented.
Lift capacity for a crane also varies depending on the position of the boom in relation to the tracks or outriggers that support the machine. For a tracked crane, the highest capacity is over the front of the tracks. As the boom is moved to the side, the crane is not able to lift as great a load without tipping.
Other factors that should be taken into consideration when planning a heavy lift are the effect of wind, any amount of swing in the load, the hoisting speed and the impact of stopping a lift abruptly.
A 50 percent safety factor is advised for all demolition lifts because of the influence of these factors coupled with the unknowns that complicate the weight estimated for materials to be lifted.
It is always better to have excess lift capacity because once a demolition lift is started it is usually not possible to reconnect the load to the structure.
The variety of cranes commonly used in the demolition of buildings and other structures may include the following generic types.
- Mobile Cranes – Mobile cranes are mounted on a chassis supported by rubber tires and can have three to eight axles. These cranes are widely used in the demolition industry and come in a variety of configurations and capacities. The mobile crane used for demolition has a lattice-type boom. Mobile cranes with hydraulic booms are used only for lifting tasks. The ease of moving these cranes from site to site makes them ideal for small demolition projects.
- Crawler Cranes – These cranes are mounted on a platform known as a “car body” and supported by two crawler-type track assemblies. Crawler cranes are usually used for long-term projects where the cost of mobilization is relatively minor compared to the overall project cost. These cranes are fitted with lattice-type booms and most are in the 100- to 250-ton capacity range.
- Rough Terrain Cranes – These cranes are mounted on frames supported by four or more large tires that are designed to maintain the stability of the crane when traveling over uneven ground. This type of crane is ideally suited for lifting equipment at industrial sites and removing structures and equipment in rough terrain.
- Tower Cranes – The familiar tower-type cranes found on most high-rise construction projects are also used for handling demolition materials and lifting small equipment when demolishing high-rise buildings at locations where explosives cannot be used.
LOADERS AND FORK LIFTS
Both track loaders and rubber-tired wheel loaders are used in the demolition business, with each machine having unique capabilities.
Loaders are used primarily for moving demolition materials and loading trucks or drop boxes. However, loaders are also used to wreck low-rise buildings.
Small loaders, mostly of the skid-steer type, are extensively used for moving materials, cleanup duties and for demolition with small shears and hammers.
There are several varieties of forklifts used for material handling at demolition sites. Following are forklifts that are typically found on demolition projects:
- Rough terrain, four-wheel drive forklifts with an extendable boom for handling material from the ground to elevated work areas (for example, to place tools on the second or third floor of a building);
- Pneumatic or hard rubber-tired standard forklifts for moving and loading materials; and
- Skid-steer loaders with removable forks for operating in buildings or on site.
SORTING AND RECYCLING
For a well-managed demolition project, the sorting of materials produced in the demolition process has become a very important sub-task of the overall demolition process.
An effective way to sort demolition materials is to demolish the building or structure so that the various classes of materials can be efficiently separated.
Sponsored Content
Still relying on manual sorters?
Let AI do the heavy lifting. Waste Robotics delivers reliable, high-performance robots tailored for complex waste streams. They require minimal maintenance, are easy to operate, and are designed to boost your recovery rates. Smarter sorting starts with the right partner. Waste Expo Booth #1969 & REMA #2843
Click here to see our robots in action!Debris sorting is accomplished during the demolition process using an excavator equipped with a grapple. In this process, the excavator operator can separate the construction materials as the demolition progresses. This process is most effective when the building is primarily constructed of wood and masonry materials.
For steel and concrete construction, this process works well with two excavators. One is usually equipped with a shear or concrete cracker to cut or break the building components, while the second excavator is equipped with a grapple to grab and place materials in sorted piles. Electromagnets can be used to pull ferrous metal from the debris.
Editor’s Note: The above text is an edited excerpt from Demolition: Practices, Technology and Management, the new textbook published by Purdue University Press in cooperation with the National Demolition Association. Those interested in purchasing the book can do so at www.demolitionassociation.com.
DEMO BY THE BOOK |
Created in partnership with the National Demolition Association, Demolition: Practices, Technology and Management is a new book by Richard J. Diven and Mark Shaurette available from Purdue University Press, West Lafayette, Ind. The book’s promoters say it is “an invaluable reference resource for anyone involved in demolition projects, particularly students of construction management and engineering.” According to a news release promoting the book, the demolition industry has become more complex, requiring a combination of project management skills, legal and contractual knowledge and engineering skills. Co-author Richard J. Diven has nearly 40 years of experience in the demolition industry as a manager at demolition company ICONCO between 1964 and 2000 and then as founder of R. J. Diven Consulting LLC, Coeur d’ Alene, Idaho. Co-author Mark Shaurette is an assistant professor in building construction management at Purdue University, West Lafayette, Ind. He was previously president of Meridian Homes Inc. and a vice president at Ryan Homes, Reston, Va. More information on the book can be found at www.thepress.purdue.edu. |
Get curated news on YOUR industry.
Enter your email to receive our newsletters.
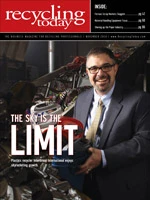
Explore the November 2010 Issue
Check out more from this issue and find your next story to read.
Latest from Recycling Today
- ReMA board to consider changes to residential dual-, single-stream MRF specifications
- Trump’s ‘liberation day’ results in retaliatory tariffs
- Commentary: Waste, CPG industries must lean into data to make sustainable packaging a reality
- DPI acquires Concept Plastics Co.
- Stadler develops second Republic Services Polymer Center
- Japanese scrap can feed its EAF sector, study finds
- IRG cancels plans for Pennsylvania PRF
- WIH Resource Group celebrates 20th anniversary