Shoreway Environmental Purchases BHS Single-Stream System
Bulk Handling Systems (BHS), based in Eugene, Ore., has signed a $15.7 million contract to design, manufacture and install single-stream and mixed commercial processing equipment for a new material recovery facility (MRF) at the Shoreway Recycling and Disposal Center in San Carlos, Calif. The MRF, which is scheduled to open in January 2011, is managed by the South Bayside Waste Management Authority (SBWMA), San Carlos. South Bay Recycling (SBR), a joint venture between Community Recycling, Sun Valley, Calif., and Potential Industries, Wilmington, Calif., will operate the system.
According to a press release from BHS, its system was chosen after an extensive application and selection process. “BHS was ultimately selected as being the most capable equipment manufacturer for the SBWMA’s sorting system specifications and needs,” SBWMA officials say in an Oct. 8 press release announcing the contract approval.
“The system incorporates the latest in screening, optical and air separation technologies and is designed to maximize the recovery of marketable commodities, yielding minimal residual material and reducing disposal costs,” according to BHS. It has a rated operating capacity of up to 45 tons of material per hour.
The Shoreway facility serves as a central location for receiving, transferring and/or processing all solid waste, recyclables, yard trimmings and food scraps collected in the SBWMA service area.
SBWMA officials describe the BHS system as the “key component” in the overall plan to transform the Shoreway Recycling and Disposal Center into the Shoreway Environmental Center. The SBWMA is promoting the new facility, which includes an environmental education center, as “a national model for sustainable building practices and innovative recycling and material handling operations.”
“We have filled in the last remaining piece to our Shoreway master plan capital improvement effort with approval of an agreement with BHS,” says Kevin McCarthy, executive director of the SBWMA.
“All of us at BHS are extremely excited to be working with the team at SBWMA,” says Steve Miller, president of BHS. “Our design engineers have developed a system that will be among the most technologically sophisticated in the world and will place the member communities of the SBWMA district at the forefront of recycling.”
Brian Moura, SBWMA vice chair and assistant city manager for San Carlos, says, “Approval of the SBR and the BHS agreements marks another important milestone in SBWMA’s ongoing work to upgrade and modernize solid waste collection and operation of the Shoreway Center. It is also estimated to boost recycling by an additional 15 to 20 percent, which will have a major effect on improving the environment and addressing the region’s climate change and green program goals.”
BHS is a manufacturer of recycling processing equipment, supplying the solid waste, recycling, wood products/compost and waste-to-energy industries.
Yaffe Purchases Auto Shredder From Wendt
The Yaffe Cos., based in Muskogee, Okla., has announced plans to purchase an auto shredder for its Fort Smith, Ark., facility. The shredder, a Wendt 80 x 115, will replace a smaller auto shredder the company currently operates at the site.
Yaffe originally considered rebuilding the 74 x 104 mill shredder that it had been operating for more than 20 years. However, after considering its options, the company says it opted to replace the mill in light of the benefits and overall cost of installing a new facility.
“We believe most companies fall into two basic groups–those that are trying to get through today and those that are planning for tomorrow. Our business has continued to grow, and we saw this as an opportunity to better position ourselves for the future,” says Sean Yaffe.
Mark Ridall, business development manager for Wendt, Tonawanda, N.Y., says that the mill is presently under construction and should be ready by the second quarter of 2010.
Ridall notes that the shredder’s custom size allows Yaffe to increase its throughput without significant extra costs. “The mill provides more capacity, more robustness to handle heavier materials and more throughput,” Ridall says.
“The real benefit,” Ridall notes, “is that when the market returns they [Yaffe] can really crank it up.”
REM Adds Ohio Baler to Distributor Network
Recycling Equipment Manufacturing Inc. (REM), Priest River, Idaho, has appointed Cleveland-based equipment sales and service company Ohio Baler Co. as its premier distributor in the states of Ohio, Michigan, Kentucky, New York and Indiana.
Ohio Baler provides system integration and applications for the recycling, waste and product destruction industries as well as sales of new and used equipment, installation and service.
Mike McChrystal, president of Ohio Baler, says, “We are pleased to be representing equipment from Recycling Equipment Manufacturing. They have been building high-quality equipment and custom systems for more than 31 years and provide exceptional customer service and support to their dealer network. At Ohio Baler, we look forward to building a successful partnership with REM Inc. and providing our customers with the highest quality equipment and customer service for many years to come.”
REM offers full-service design and manufacturing of material recovery facilities, sorting lines, disc screens and feed conveyors in steel-pan, chain-belt, slider-bed and roller-trough designs. The company also has a full line of can crushers, glass breakers, can buying systems, EPS compaction equipment and hydraulic tippers in many styles.
Mark Blankenship, president of REM Inc., states, “We are looking forward to a continuing solid relationship with Ohio Baler, knowing their great reputation for customer service will blend well with our commitment to building quality equipment. Both companies bring valuable resources to the table, and this will translate into great benefits for our customers going forward.”
More information on Ohio Baler is available at www.ohiobaler.com, while additional information on REM is available at www.remfg.com.
U.S. Shredder Scores Downstream Contract
The U.S. Shredder and Castings Group, Trussville, Ala., has announced that it will be supplying what it calls “its most extensive shredder downstream to date” in Mexicali, Mexico.
The U.S. Shredder downstream system currently being installed at the Deacero facility is “designed and built to efficiently and effectively process the ferrous and nonferrous metals after a 120-inch shredder,” according to a U.S. Shredder news release. Monterrey-based Deacero processes scrap and produces steel.
The news release also states that the system will incorporate “a state-of-the-art magnetic separation system” designed to “remove up to 99 percent of all nonferrous metals from the fluff stream, not including some insulated cable.”
Because of Mexicali’s hot, arid climate, the system also was designed with what U.S. Shredder calls “special conveyors with covers and transition areas designed to minimize the dust created as the material is processed.”
The system’s metals recovery equipment includes magnetic drums, trommels and screens, eddy currents, “DSRP” units to recover small ferrous pieces and air-sensor technology to recover additional metal such as stainless steel that might not be recovered by the eddy currents.
IESI Mckinney Starts Up MRF
IESI McKinney, McKinney, Texas, has begun operation of its 15-ton-per-hour Bollegraaf single-stream sorting system.
The Bollegraaf system, supplied by Van Dyk Baler Corp., Stamford, Conn., features Lubo OCC, ONP/French and fines screens for sorting ONP (old newspapers), OCC (old corrugated containers), glass, PET (polyethylene terephthalate), colored HDPE (high-density polyethylene), natural HDPE and aluminum and ferrous metals.
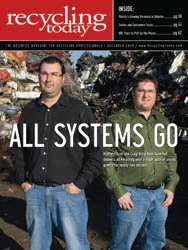
Explore the December 2009 Issue
Check out more from this issue and find your next story to read.
Latest from Recycling Today
- Ferrous market ends 2024 in familiar rut
- Aqua Metals secures $1.5M loan, reports operational strides
- AF&PA urges veto of NY bill
- Aluminum Association includes recycling among 2025 policy priorities
- AISI applauds waterways spending bill
- Lux Research questions hydrogen’s transportation role
- Sonoco selling thermoformed, flexible packaging business to Toppan for $1.8B
- ReMA offers Superfund informational reports