
Routeware adds RubiconSmartCity, RubiconPro to its portfolio
Routeware Inc., a Portland, Oregon-based developer of integrated technology solutions for the waste and recycling industry, has acquired Wastech Inc., owner of the RubiconSmartCity and RubiconPro platforms.
With its acquisition, Routeware says it now offers “best-in-class, purpose-built platforms for both waste haulers and municipalities, strengthening the company’s position as the category leader in technology solutions for the waste collection industry.”
Routeware CEO Paul Rafalowski says the combination of platforms is another important milestone in Routeware’s drive to “transform” the waste and recycling industry.
“This is an incredibly exciting time for us as we welcome the customers, people, partnerships and technology associated with RubiconSmartCity and RubiconPro to the Routeware family,” Rafalowski says. “Our missions, what we do and the outcomes we’re driving for our customers could not be more aligned. This combination will be truly transformational for our industry.”
Product offerings include the recently launched Elements, which is specifically designed for waste collection operators. The addition of RubiconSmartCity and RubiconPro to the Routeware portfolio provides specially designed capabilities for municipalities and local governments with a full breadth of functionality of waste collection operations, street sweeping and snow removal.
By acquiring the Rubicon platforms, Routeware says it offers its municipal customers the ability to reduce costs and improve service offerings and overall safety. The company adds that the acquisition further highlights its commitment to investing in its product offerings to better serve its customers and to provide seamless continuity and support to nearly 1,500 municipal customers using its solutions.
“The alignment created by this transaction will be transformational to both Routeware and its expanding family of products, as well as for local governments and waste haulers who are in pursuit of operational excellence,” says Stephen Goldsmith, former mayor of Indianapolis, professor of urban policy at the John F. Kennedy School of Government at Harvard University and director of Data-Smart City Solutions. “The data, technology and best practices available through these products are essential for efficient and effective waste and recycling collection.”
In early May, Lexington, Kentucky-based Rubicon sold its fleet technology software as a service business to Wastech, an affiliate of major share-holder and private investment firm Rodina Capital of Florida.
According to the Rubicon news release announcing the sale to Wastech, the company’s fleet technology unit powers heavy-duty fleet operations in more than 100 cities, including Houston, Phoenix, Miami, Atlanta and Kansas City. At the time of that sale, Rubicon also noted that six of the top 10 cities by population were using the RubiconSmartCity product to improve the safety and effectiveness of their core municipal operations and save taxpayer dollars.
Liebherr opens Missouri facility
Liebherr USA Co., a Newport News, Virginia-based manufacturer of earthmoving equipment, has invested in a new Kansas City, Missouri, location to serve as a mobile crawler spare parts warehouse to more efficiently distribute parts throughout the region.
The 12,000-square-foot warehouse holds about 2,300 stocked spare part line items, with more than 5,000 line items expected to be stocked once the facility is fully converted.
The project started in early 2024 with the installation of racking within the warehouse, and the warehouse began receiving and shipping out orders a month later. Kansas City will serve as one of four locations parts are distributed to once they arrive at the main warehouse in Newport News.
“This significant investment in the expansion of the spare parts distribution network shows Liebherr’s further commitment to providing the best service to our customers in the Midwest,” says Arnold Burger, general manager of customer service for Liebherr’s Mobile and Crawler Cranes unit.
With many Liebherr machines being used to construct wind turbines for the prevalent wind industry in the Midwest, the company identified the benefit of having a warehouse located closer to the region. Having parts more readily available will help reduce downtime and better service machines and customers in the area, Liebherr says.
“When people choose to expand their fleet with Liebherr, they deserve a strong partner that can provide them with reliable and efficient service when they’re in need,” says Anthony South, spare parts business manager for the Mobile and Crawler Cranes division.
Customers can see the price and availability of parts in their areas through the MyLiebherr online portal, allowing access to local service contacts, machine manuals, ordering and status of spare parts.

Motion to open Houston repair shop
Motion Industries Inc., a Birmingham, Alabama-based distributor of maintenance, repair and operation replacement parts and a provider of industrial technology solutions, has opened a new Motion Repair & Services location at 10710 Sharmon Rd. in Houston.
The new shop, dedicated to repair and services, features a full suite of CNC and manual machine tools, lifting capacities to 30 tons and state-of-the-art diagnostic and testing equipment within its 75,000 square feet. The space allows for the receipt and cleaning of repairable assets physically separated from repair processes to facilitate best practices regarding contamination. Additionally, new offices and conference space allow for customer meetings and training.
Factory-trained technicians focus on mechanical, fluid power, process pumps, packaged solutions and field services. The facility’s formal quality program and factory certifications for repair processes help ensure customers receive the best value, the company says.
“Our customers can access this single source for parts supply, repair and services from a world-class provider,” says Ed Van Hell, group vice president of Motion Repair & Services. “We hope those who have not done business with us yet will consider how beneficial this can be in time and value. We would welcome a conversation.”
“Services rendered from this new shop will enable Motion to deliver more holistically on our vision—to be the preferred industrial solutions provider,” Motion President James Howe adds.
He says the company’s investment in the site strengthens its total value proposition and reflects its confidence in its staff and commitment to serving the Houston market and beyond.
In addition to the new Houston facility, Motion operates more than 45 repair and service centers throughout the United States, Canada and Mexico.
With annual sales of more than $8 billion, Motion is a leading industrial distributor of more than 19 million parts and supplies, including bearings; mechanical power transmission products; electrical and industrial automation components; hose, belting and gaskets; hydraulic and pneumatic components; process pumps; industrial and safety products; seals and accessories; and material handling products and solutions. Motion is a wholly owned subsidiary of Atlanta-based Genuine Parts Co.

Matium offers online plastics trading platform
Matium, a Denver-based online trading platform focused in part on recyclable and recycled-content plastics, says it has helped connect more than 400 companies that have traded some 75,000 tons of materials via its digital services.
The company, founded in 2021 by its CEO and former plastics trader Bailey Robin, says it increases the efficiency of supply chain companies through a “user-friendly” material management platform that simplifies and automates complicated and redundant manual tasks.
Robin learned about the plastics sector during a stint selling recycled plastics for Bach Polymers, a plastics brokerage based in Annapolis, Maryland. There, the Matium founder says, he built a 10 million pounds-per-month book of plastics trading.
Matium was created as a startup by Robin with the help of his cousin, Alex Lambrides, who has a background in developing corporate content management systems and websites.
Matium is working with sellers, traders and buyers throughout North America by providing a “user-friendly platform recyclers can use on their phone or laptop to manage all the day-to-day tasks that keep them from building their businesses.”
In a market where brand owners, packaging producers and other manufacturers are seeking recycled-content plastic, Matium says its platform standardizes and streamlines material offers from trusted partners so procurement teams can buy materials confidently and efficiently.
Matium has received endorsements from several companies in the plastics sector, including an executive with Austria-based global plastics producer and recycler Borealis AG.
“The whole North American region needs something like your platform—I’m a true believer of your platform; there is nothing like you guys in the market,” says Jose Luis Chavez, a Texas-based director of business development with Borealis.
The company has collected similar endorsements from several other plastics and recycling firms, including Arkansas-based recycling company 3 Rivers Plastics, Canada-based EnergiPlast, Michigan-based PolyFlex Products Inc. and Costa Rica-based KUPP America.
Robin says the existing plastics trading market allows some companies to profit and others to lose from what he describes as “the waste and opacity of commodity markets.”
He says Matium is his attempt to create a sustainable supply chain using collected data to create a more efficient and competitive infrastructure for trading.
On its website, Matium reports “aggressive” plans for growth beyond plastics in the next 12 months and that “the future for the company and its network is one of abundance.”
Steelwrist opens new office in US

Sweden-based construction, demolition and metal recycling attachments maker Steelwrist AB has opened a new North American headquarters facility in Newington, Connecticut.
The company inaugurated its new headquarters in late spring at a ceremony attended by U.S. Sen. Richard Blumenthal of Connecticut, executives from the Association of Equipment Manufacturers and Steelwrist dealers and customers.
“I am very excited to have inaugurated our new headquarter in Newington, which marks a new chapter in Steelwrist’s support to the North America market,” says Richard Aulin, vice president for the Americas region at Steelwrist.
With the new facility in place, Steelwrist says it has the capacity to continue its growth journey in North America.
According to Steelwrist, tiltrotators are placed above other excavator attachments and designed to allow those attachments to rotate 360 degrees and to swivel by as much as 45 degrees to all sides.
“This inauguration represents a significant step forward for Steelwrist in North America, and with the new facility we can continue our exceptional growth trajectory and even better serve our customers and dealers in the region,” Steelwrist CEO Stefan Stockhaus said at the event.
“It was a pleasure to host Sen. Richard Blumenthal and explain the efficiency improvement potential that our products can bring to the U.S. construction industry.”
Steelwrist entered the North American market in 2017 and established its first location in Berlin, Connecticut, around that same time.
The new headquarters in Newington, only a few miles from Berlin, is more than five-times larger, and Steelwrist says its increased capacity and improved infrastructure will position the company to continue leading innovation in the tiltrotator market while supporting the needs of its North American dealers and customers.
Steelwrist says contractors in North America that operate excavators are seeking to increase the efficiency and versatility of their investments.
“The penetration of tiltrotators is growing rapidly in the region,” the firm adds. “In recent years, Steelwrist has experienced strong growth, with tiltrotator sales increasing at a high speed.”

AMCS purchases Qv21 Technologies
AMCS, headquartered in Limerick, Ireland, has acquired Qv21 Technologies, an Austin, Texas-based provider of fleet management and logistics software as a service (SaaS) solutions for short-haul, bulk commodity transportation. Terms of the transaction were not disclosed.
Founded in 2009, Qv21 Technologies enables short-haul and bulk commodity trucking companies of all sizes to increase operational visibility and improve overall efficiency, AMCS says in the news release about the purchase. With a mission to enable “Logistics Without Barriers,” Qv21’s The Logistics Framework (TLF) software streamlines business processes from order to invoice. Backed with robust data management, workflow automation and analytics capabilities, Qv21 ensures organizations control their operations while boosting savings and profit margins.
The fleet management and logistics solutions by Qv21 Technologies, along with its North American footprint and focus on bulk material transportation, are highly complementary to the AMCS Platform, benefiting customers of both organizations, AMCS says, adding that the purchase allows it to expand the capabilities of its platform, enabling resource-intensive industries to achieve their sustainability goals faster, more efficiently and profitably.
AMCS says this acquisition paves the way to realizing several synergistic opportunities, specifically, aiding organizations in the long-haul transport of bulk commodities that can support a more circular economy. With Qv21, AMCS can provide organizations with a solution for a more structured, efficient approach to resource use and improved waste management, translating to meaningful progress toward their sustainability goals, according to the company.
“The strategic addition of Qv21 Technologies signifies a crucial advancement for AMCS, reinforcing our position at the forefront of performance sustainability,” AMCS co-founder and CEO Jimmy Martin says. “This partnership provides tremendous opportunities, specifically for companies engaged within bulk material transportation, to reach their sustainability goals faster. The features that Qv21 brings to the table serve to enhance our capabilities at AMCS, strengthening our ability to support our clients’ drive towards enhanced resource management, greater efficiency, sustainability, growth and profitability.”
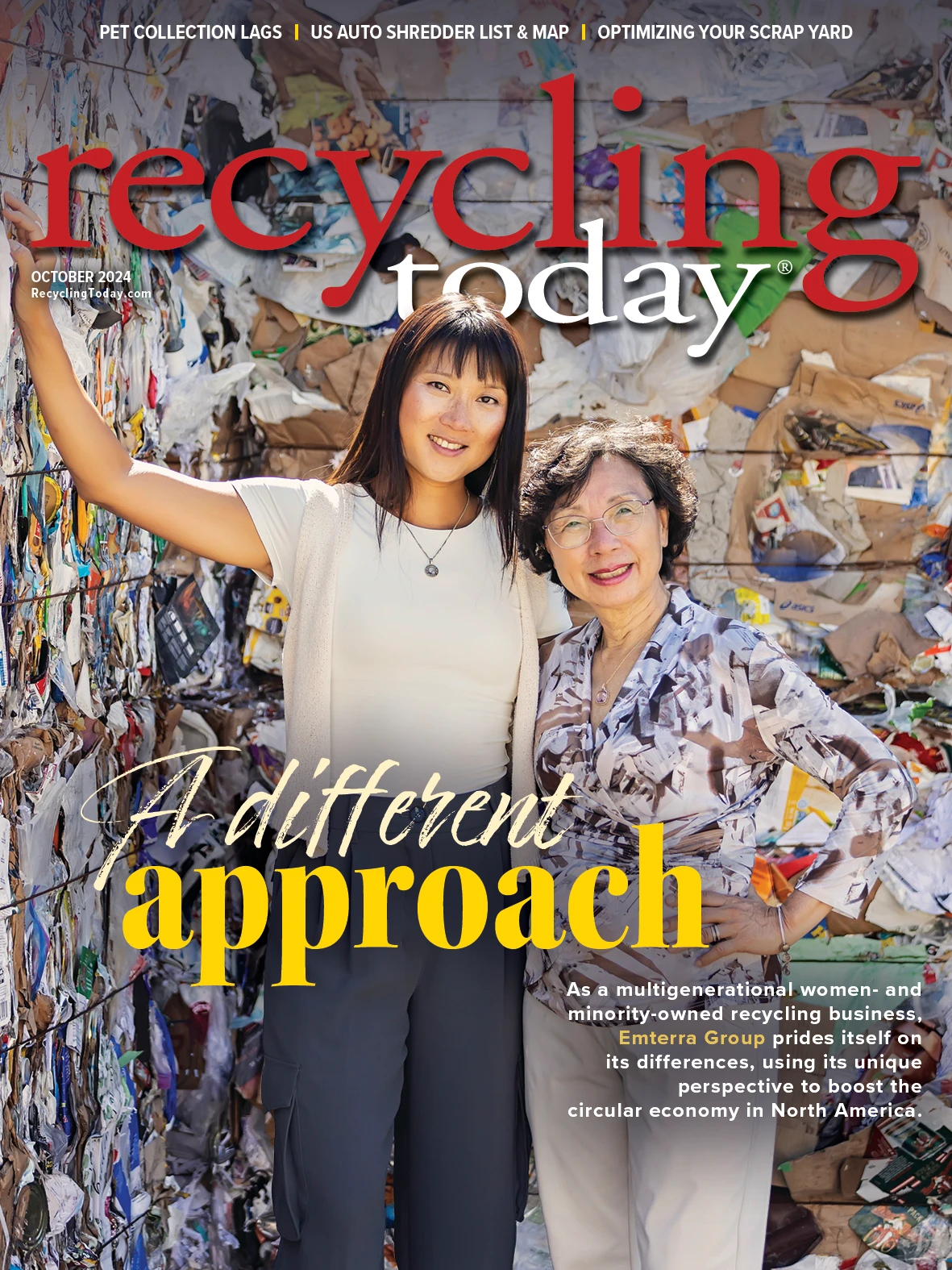
Explore the October 2024 Issue
Check out more from this issue and find your next story to read.
Latest from Recycling Today
- Japanese scrap can feed its EAF sector, study finds
- IRG cancels plans for Pennsylvania PRF
- WIH Resource Group celebrates 20th anniversary
- Ecobat touts commissioning 3 LIB recycling plants in a year
- NWRA: NIOSH cuts a step in the wrong direction
- Novelis announces plant closures
- ABTC reports production increase at LIB recycling facility
- ReMA contributes comments in Commerce Department investigation into copper