
NWRA names CP Group Innovator of the Year
CP Group, headquartered in San Diego, has been named the National Waste & Recycling Association’s (NWRA) 2022 Innovator of the Year for its patented OCC (old corrugated containers) Auger Screen.
This award recognizes “recycling equipment designers and manufacturers that successfully challenge and advance recycling sector operations. It celebrates innovation in design and manufacturing that increases the effectiveness or efficiency of recycling equipment and operations,” the Washington-based NWRA says.
The auger screen is a nonround anti-wrapping, anti-jamming machine that does not require an upstream presort and creates finished OCC product. Because the screen is cantilevered, all wrapping materials screw off the end, minimizing maintenance and cleaning, CP Group says.
The screen fractionates out the smaller material stream, so sorters only see the larger stream, which improves safety by reducing exposure to sharps. CP Group says the patented nonround attribute of the auger flights creates the agitation needed to produce clean OCC.
The machine prototype design was completed in 2017, and the first machine was manufactured in 2019. After months of testing, the prototype machine was installed in the Waste Connections Ecosort facility in Eugene, Oregon, which processes commercial material, and the machine still is running today.
The first residential material recovery facility (MRF) began using an OCC Auger Screen for the direct and final screening of OCC in late 2021. The Metro Waste Authority (MWA) MRF in Des Moines, Iowa, is the first high-volume, single-stream MRF in North America to operate without a presort or postsort station.
“The screen, located at the front of the system, captures more material, decreases contamination, significantly reduces maintenance downtime and eliminates the presort, making the process safer and much more effective,” MWA Executive Director Michael McCoy says.
Over the past several years, CP Group says it has invested in its production capabilities to keep pace with growing demand. With this specialized flight-forming machine and CP’s manufacturing capabilities, CP fulfills orders in-house, which includes the production of the patented OCC Auger Screen that creates the material agitation needed to produce a clean OCC end product.
Columbia Steel Castings to close
Columbia Steel Castings Co., Portland, Oregon, says it will close its plant and all its facilities in Portland, with closure-related employment separations expected to begin Oct. 22 or within two weeks thereafter.
Columbia Steel manufactures a variety of steel and iron parts for basic industry, including wear parts for metal and waste shredders. The company was founded in 1901 and ultimately was acquired by Hobart M. Bird, whose descendants continue to operate Columbia Steel.
In a letter dated Aug. 22 sent to employees by Columbia Steel President and CEO Martha B. Cox, she writes, “It is with deep sadness I need to inform you of the plan to close Columbia Steel by the end of this year. I understand the impact this will have on our hard-working employees and their families. The Bird family priorities have always been first to employees, then retirees, vendors, customers and our environmental responsibilities. Unfortunately, our efforts to secure a new owner or financing for Columbia Steel have not come to fruition.”
Cox writes that the effects of offshore competition that often is government subsidized, supply chain disruptions, COVID-19-related restrictions on sales travel, increased state and local environmental regulations, fees on energy-intensive industries and the inability to hire and retain sufficient employees to produce castings at a sustainable level, even after pay increases, have contributed to the decision to close the 121-year-old company.
She adds, “While Columbia Steel will continue to seek additional financing and to have discussions with various companies about purchasing its facilities and maintaining operations, there is no guarantee that this will happen.”
The company also sent a letter dated Aug. 22 to Rachel Soto, interim rapid response coordinator at the Oregon Dislocated Worker Unit Office of Workforce Investments at the Oregon Higher Education Coordinating Commission, about the closure and employee terminations as required by the Worker Adjustment and Retraining Notification (WARN) Act.
According to the letter to Soto, the plant closure is expected to be permanent, and 225 employees will be laid off.
Recycling Today reached out to Columbia Steel for information on the company’s ability to fulfill orders prior to the closure but has not received a response.
Lindner moves into new headquarters

Shredding and recycling equipment maker Lindner Recyclingtech GmbH has moved into its new 14,000-square-meter (about 150,000-square-foot) corporate headquarters complex in Spittal/Drau, Austria.
“The high global demand for Lindner’s quality products made it necessary to expand the plant and the team,” the company says.
Lindner says it focused on automation and robotics, the associated quality assurance, process optimization in assembly and extending the company’s own manufacturing capabilities with the new plant.
Lindner owner and CEO Manuel Lindner says, “The [energy] crisis has further reassured us that this is the right path. The disrupted supply chains have also shown how important it is for us to manufacture as many components as possible in our own production. Only by investing in our own manufacturing capabilities, robotics, automation and flow production can we ensure the quality of our products and reliable delivery times in the future.”
Michael Lackner, managing director at Lindner, says, “We want our new headquarters to be perfectly equipped for future requirements and be well-positioned to maintain high quality standards and meet the increasing demand for our machines. The production area in the new plant has doubled, which means that we are ideally equipped to cope with the increasing capacities.”
He continues, “It is just as important to us that we offer our employees a modern workplace. By using automation and robotics, we can make work more comfortable. Heavy physical work, such as mounting machines, is no longer necessary. Instead, the task is focused on the proper operation of the robots. We are also significantly expanding our team, which means that we are currently taking on 100 new employees.”
A three-story office building also is part of the new complex. Lindner says “a great deal of importance was attached to the use of environmentally friendly building materials and sustainability” throughout the campus when building the complex.
Wendt installs downstream system in Canada

Wendt Corp., based in Buffalo, New York, has commissioned a nonferrous metals sorting system at Dartmouth Metals Ltd. in Dartmouth, Nova Scotia. The equipment maker says the installation of the system “represents part of Dartmouth’s growth strategy to recover a greater percentage of nonferrous metals, opening additional markets for the valuable material.”
Wendt Corp. describes Dartmouth Metals as a third-generation, family-operated business with roots tracing back to the 1960s. In 1979, Peter Giberson founded what is known today as Dartmouth Metals Ltd., with his son, Dave Giberson, joining the company full time in 2003.
The nonferrous sorting plant Wendt provided features a tumbleback feeder, trommel screen, fines eddy current separator, J-box and a Wendt/Tomra Finder sensor unit. The plant also incorporates Dartmouth Metals’ two existing eddy current separators. The equipment was installed and commissioned in June.
Dartmouth previously had been running its automobile shredder residue (ASR) through its two eddy current separators, leaving some other nonferrous metals uncaptured.
“We were shipping away our nonferrous materials to a friendly local competitor, but we knew what we were missing,” Dave Giberson says.
Dartmouth Metals had its ASR sampled several times and found it should have been getting 11 percent to 14 percent metallic recovery but was achieving only 6 percent recovery with its original setup. “We were missing half of the material we could have been recovering,” Dave Giberson says. “When the door closed for shipping our fluff material without sorting it properly, we knew it was time to invest.”
Dartmouth says it expects to recover that last 6 percent to 8 percent of metals, which includes zorba fines, zurik and copper wire, with the new system. The company also attributes the new system with increased labor savings and attracting higher levels of talent.
“The Wendt system modernizes our yard and has made it a more appealing place to work,” Dave Giberson says.
Terex acquires ZenRobotics

Terex Materials Processing (MP) has acquired the assets of ZenRobotics Ltd., a Helsinki-based company that designs and creates robots that sort recyclables using proprietary artificial intelligence (AI) software.
ZenRobotics will retain its name and become a Terex brand, with the unit reporting to Tony Devlin, who leads the Terex MP environmental businesses, according to a news release issued by Terex Corp., Norwalk, Connecticut.
ZenRobotics was started in 2007, and the company began using AI-based robots to sort recyclables in 2009, which led to the introduction of the ZenRobotics Recycler in Helsinki. In 2015, ZenRobotics launched its Heavy Picker, which is designed to sort bulky construction and demolition (C&D) debris. The company expanded into China and the U.S. market in 2016.
ZenRobotics’ Heavy Picker is equipped with sturdy arms, various sensors and AI. Terex says it provides “a simple, unstaffed sorting process and makes waste sorting more accurate, safe and profitable.”
Its other offerings include the Fast Picker, a high-speed sorting robot designed for maximizing material recovery. It is compactly designed for easy integration into existing processes and conveyors in material recovery facilities and increases profits by enabling fully automated sorting and higher output purity, Terex says. ZenBrain is the company’s AI for sorting robots that has advanced recognition ability and autonomous decision-making.
Terex is active within global waste markets through Terex Ecotec, Terex CBI, Terex Fuchs and Terex Recycling. ZenRobotics will add to the Terex portfolio in global waste, where it will continue to be operated as a stand-alone business while also benefiting from MP’s broader market presence, Terex says.
“ZenRobotics is an exciting, modern company that lends itself perfectly to our preexisting environmental expertise, and their ethos of making a circular economy more possible aligns perfectly with our goals and targets for the future of Terex MP,” Devlin says. “We’re excited to see the many ways that we can apply this technology and what potential this acquisition can bring Terex MP with the application of this technology.”
ZenRobotics CEO Jarmo Ruohonen adds that “being part of the Terex MP team will give ZenRobotics more global opportunities to grow.”
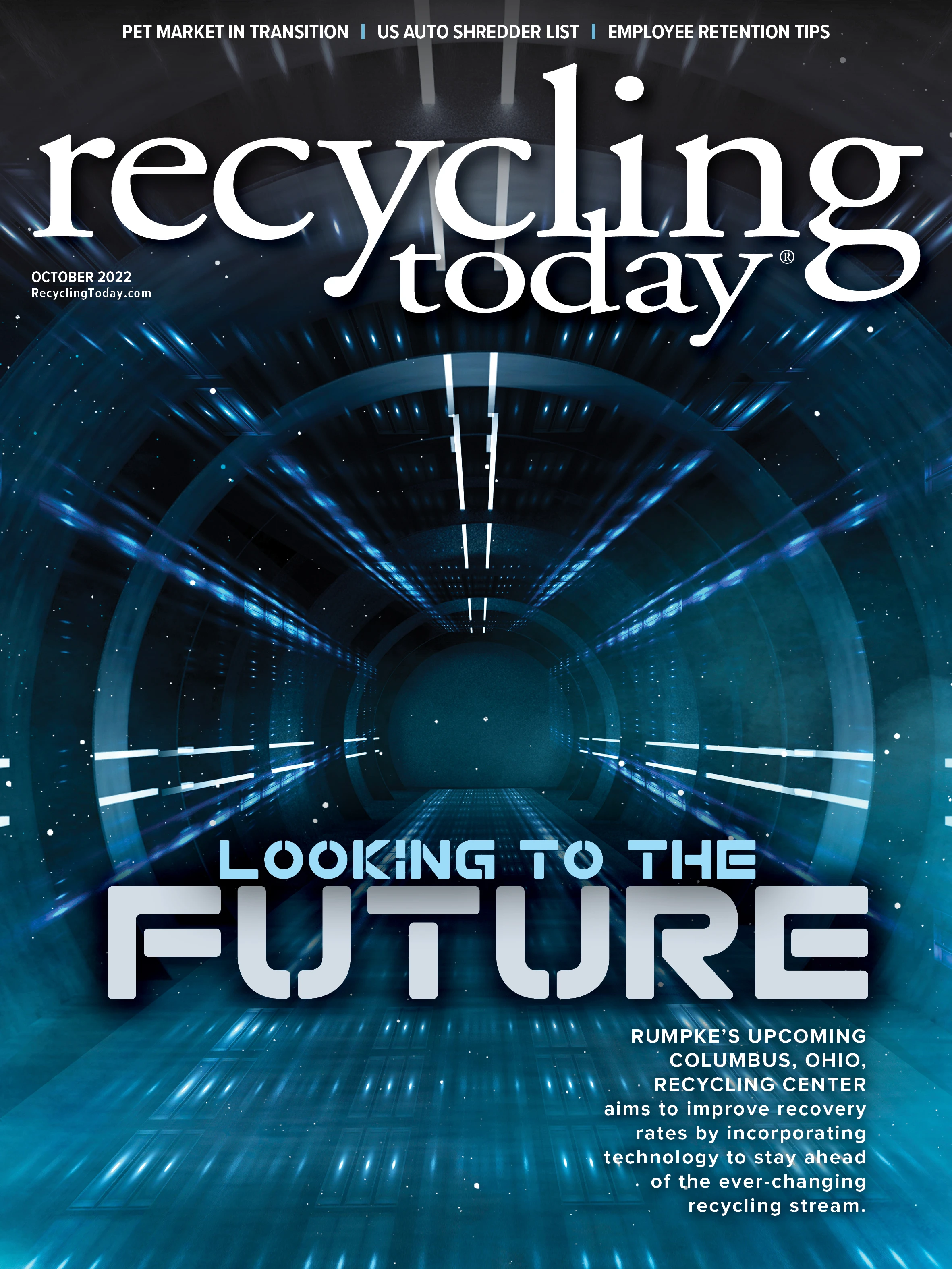
Explore the October 2022 Issue
Check out more from this issue and find your next story to read.
Latest from Recycling Today
- OnePlanet Solar Recycling closes $7M seed financing round
- AMCS launches AMCS Platform Spring 2025 update
- Cyclic Materials to build rare earth recycling facility in Mesa, Arizona
- Ecobat’s Seculene product earns recognition for flame-retardant properties
- IWS’ newest MRF is part of its broader strategy to modernize waste management infrastructure
- PCA reports profitable Q1
- British Steel mill subject of UK government intervention
- NRC seeks speakers for October event