
MerQbiz updates BaleVision platform
MerQbiz, an analytics company based in El Segundo, California, that serves the recovered paper supply chain, has launched a new generation of its Bale Vision quality assessment and analytics product suite. The launch includes data products that provide deeper insights into quality and procurement to inform buyers and sellers on quality and cost factors related to recovered paper, the company says.
The initial analytics dashboards launched in 2019 show the contamination breakdown of each paper bale measured, along with fiber yield, material cost per ton and landed cost per ton. Building on this foundation, MerQbiz says it has expanded the solution’s modeling capabilities to find correlations between supplier performance, location data, contamination type, return on investment and other actionable information.
Examples of new features include:
- supplier ranking dashboards in which the buyer can view side-by-side comparisons of supplier costs and yields;
- contamination rankings that reveal types of contamination (i.e., moisture, plastic, ash) by supplier and location;
- capabilities that allow the product to be localized based on currency, language and customs;
- deductions reports that look at individual probe readings and suggest cost adjustments for high-contamination bales;
- impact dashboards that enable users to calculate their return on investment for fiber sales or procurement; and
- a scenario planning tool that uses historical data to recommend a purchase plan per supplier and the projected financial and environmental impact.
“At its core, BaleVision is a data engine that aggregates and analyzes data points from a variety of sources—customers, industry databases, weather experts, government entities—giving users valuable insights,” says John Fox, president and CEO of MerQbiz. “As we continually add data collected through on-site audits, integrate external datasets and improve the usability of our dashboards, the system becomes ever more powerful and smarter for our customers,” he adds.
According to MerQbiz, the new releases use outside datasets, including market pricing indexes, real-time fuel prices for logistics calculations and weather data across geographic regions. These data are instrumental in helping customers gain a clearer picture of their recovered paper quality and costs, the company adds.
MerQbiz says it offers multiple options for the setup and release of customer data related to recovered paper supply and procurement. Chris Brandsey, chief product officer at MerQbiz, says the company works with each of its customers to determine the best approach.
MerQbiz’s BaleVision platform was constructed using Amazon Web Services and Amazon’s Relational Database Service to ensure system stability, security and data privacy, according to the company.
MerQbiz is a sole venture of German equipment company Voith GmbH.
Steinert test center equipped to serve metal recyclers

Cologne, Germany-based Steinert says the metal sorting line at its new test and development center in Pulheim, Germany, near Cologne, officially went into operation Sept. 22.
“By opening the new building, the company is trebling its testing capacity, allowing it to be more flexible in responding to customer demands,” the company says.
Steinert hosted a webinar during its opening event, where guests could participate in live question-and-answer sessions.
Steinert plans to host another seminar on “how to separate nonferrous metals and sorting heavy metals to the maximum.”
According to Steinert, the online webinar will answer questions about separating nonferrous metals produced through shredding processes and in incineration bottom ash, improving aluminum quality and separating heavy metals in individual fractions.
Before the end of the year, the company says it plans to introduce additional sorting lines for recycling and mining applications at the Pulheim facility so it can “better achieve its aspiration of ‘test before you buy’ and can respond with ever-more accuracy to the sorting aims of extraction, purity and profitability for each sorting task.”
“The processing sequence deployed in the [test] sorting systems is the same as that used in a real industrial plant,” says Peter Funke, Steinert Group CEO.Lindner cites results from its fire prevention system
Austria-based equipment maker Lindner-Recyclingtech GmbH says a continuous, process-related monitoring system it has developed to scan the surface temperature of materials on moving conveyors “has proven to be highly successful in combating potential fire hazards and actively improving safety in facilities that produce solid recovered fuels (SRF).”
Lindner’s Fire Prevention System (FPS) contains optical sensors designed to constantly monitor the temperature of material on conveyor belts and can automatically trigger a water sprinkling system to cool overheated particles in the material stream. The early detection of hot spots means “most hazards are identified at the start of a thermal reaction, keeping the required amount of water low,” according to Lindner.
Mayer Recycling GmbH, Upper Styria, Austria, has been using the system and collecting data since mid-2019. The data “clearly demonstrate the benefits of this sophisticated technology,” Lindner says.
On average, more than 350 overheated particles in the material stream are detected per month at Mayer. Of these, approximately 10 percent were deemed too hot for further processing, triggered the alarm and were manually removed.
Of the removed materials, around 70 percent were batteries that already were undergoing a chemical reaction. The remaining system triggers were “coolable materials, such as metal particles that got too hot after shredding,” according to Lindner.
The company says it developed FPS to address the growing risk of fires, which it calls “one of the most pressing recent issues in the mechanical processing and conversion of waste into SRF.” This risk is caused predominantly by “a constantly increasing number of lithium batteries” in waste and recycling streams, according to the firm.
Lithium-ion batteries, found most commonly in mobile phones but also in any number of small appliances or communication devices, have grown in popularity. They often are discarded in materials streams that end up in waste transfer stations, SRF plants, electronics recycling and material recovery facilities and as automobile shredder feedstock.
The widespread presence of the batteries means “the risk of fire [has] increased exponentially during mechanical processing” of materials at all these types of facilities, Lindner says.

Industrial Service Solutions division forms several new partnerships
The Recycling Technologies division of Industrial Service Solutions (ISS), Houston, has formed a new partnership with Taurus America to provide sales, service and parts for Taurus’ line of recycling equipment that includes ferrous shears, balers, logger-balers and preshredders.
Sponsored Content
Labor that Works
With 25 years of experience, Leadpoint delivers cost-effective workforce solutions tailored to your needs. We handle the recruiting, hiring, training, and onboarding to deliver stable, productive, and safety-focused teams. Our commitment to safety and quality ensures peace of mind with a reliable workforce that helps you achieve your goals.
According to a news release from ISS, this new relationship will help Taurus America to increase its position as a leader in heavy-duty recycling equipment to the scrap metal industry.
Sidney Wildes, president of Taurus America, says the two companies have a “combined 100 years plus of experience in the recycling industry.”
Taurus America is the exclusive provider for sales, service and support for the Taurus product line. Taurus America is headquartered in Georgia and offers a 90,000-square-foot machine shop and parts warehouse that provides production and assembly capabilities along with electrical assembly and installation.
“ISS Recycling Technologies continues to add quality products, service and support for a wide range of offerings in the recycling industry. Through our partnership with Taurus America, we’ve added another proven line of recycling equipment to our offerings,” says Bill Tigner, vice president of ISS Recycling Technologies.
Additionally, ISS has entered into an agreement with Marcelo Davila of Monterrey, Mexico, who will offer sales representation for ISS Recycling Technologies in Mexico and Central America.
“Davila brings vast operational and commercial knowledge to our recycling division,” Tigner says.
Prior to partnering with ISS, Davila served more than 15 years in the procurement and purchasing departments for Deacero, a steel producer based in Monterrey, and as a project manager for Deacero’s scrap shredder operations. He has a Bachelor of Science in industrial engineering from Monterrey Institute of Technology.
ISS supplies and supports automobile shredders, motors and drive systems, castings and wear parts that include design, engineering, service and turnkey installation for complete scrap recycling facilities. ISS provides equipment and services across a range of industry applications and expertise in multiple equipment types, which offers a bundled solutions approach. With 45 locations nationwide, the company offers field services, fully equipped service shops and supply shops with available parts.
Get curated news on YOUR industry.
Enter your email to receive our newsletters.
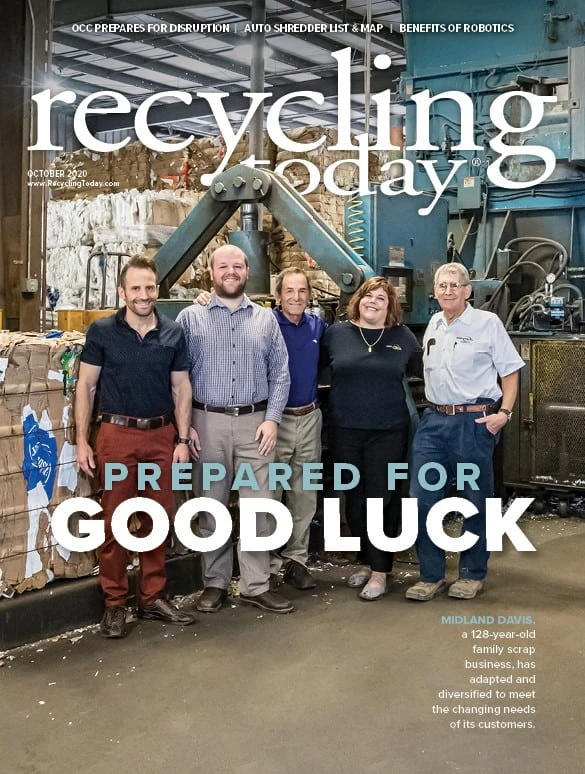
Explore the October 2020 Issue
Check out more from this issue and find your next story to read.
Latest from Recycling Today
- Toppoint Holdings expands chassis fleet
- Lego creates miniature tire recycling market
- Lux Research webinar examines chemical recycling timetables
- Plastics producer tracks pulse of wire recycling market
- Republic Services, Blue Polymers open Indianapolis recycling complex
- Altilium produces EV battery cells using recycled materials
- Brightmark enters subsidiaries of Indiana recycling facility into Chapter 11
- Freepoint Eco-Systems receives $50M loan for plastics recycling facility