CP Group begins Fiberight installation

Earlier this summer, the CP Group, headquartered in San Diego, broke ground on the installation of the material recovery facility (MRF) that will comprise the front-end system for Fiberight’s waste processing and refining facility that features Fiberight’s first full-scale biofuels and biogas processing systems.
Serving 115 municipalities, the 144,000-square-foot Hampden, Maine, facility will feature technologies from CP Group for recovering recyclables and preparing residual waste for further processing on-site.
The MRF’s processing system features a CP trommel screen with bag-opening knives, a steel-disc CP OCCScreen, the new nonwrapping CP Auger Screen used to size material in place of a traditional scalping screen, two CPScreens for 2D/3D separation, the abrasion-resistant CP Glass Breaker to remove glass and fines and four optical sorters: Two MSS Cirrus PlasticMax optical sorters will recover polyethylene terephthalate (PET) and high-density polyethylene (HDPE), one MSS Cirrus FiberMax optical sorter will sort and clean fiber and one MSS Cirrus will be used as a scavenger optical sorter to recover remaining commodities.
“The system is a blend of traditional and new equipment to provide Fiberight with flexibility for changing markets with extremely low-maintenance and durable machines,” says Terry Schneider, president and CEO of CP Group.
Fiberight’s proprietary anaerobic digestion and biogas technology converts organic waste to biofuel and refined bioproducts. Residual waste at the facility will be processed by Fiberight’s technology, upgrading the municipal solid waste (MSW) residue into industrial bioenergy products. Fiberight anticipates a landfill diversion rate of up to 80 percent of incoming material, the CP Group says in a news release announcing the installation.
By designing the plant to be adaptable to future market trends, this facility will be well-suited to handle changing market conditions, particularly because it is capable of upgrading mixed paper to pulp-based products, the equipment supplier says.
Installation of the MRF will take slightly more than three months to complete, the CP Group says, with a forecasted system startup date in the fourth quarter of 2018.
Andritz acquires ASKO
Austria-based equipment and technology company Andritz has signed an agreement to acquire ASKO Inc., Homestead, Pennsylvania. The deal includes ASKO’s wholly owned Dutch subsidiaries, ASKO Emera V and ASKO BV.
Andritz supplies plants and equipment for the metalworking and steel industries, hydropower stations, the pulp and paper industry and for solid and liquid separation in the municipal and industrial sectors.
ASKO is a manufacturer of knives and wear parts used in the metals industry, including in metals recycling baling and shearing applications.
The deal is expected to be complete before the end of the third quarter of this year.
“The combination of ASKO’s broad line of industrial knives and wear parts and Andritz’s global position and engineering leadership reinforces the partners’ strategies to provide advanced technology services and maintenance products to the global metals industry,” says Bill Rackoff, president of ASKO. “Both companies’ business strategies are based on delivering technical solutions that enhance customer value. The result of coordinating with Andritz’s global resources and talented metals team creates expanded opportunities for ASKO’s customers and associates.”
Heinz Autischer, Andritz Metals Global business area manager, comments, “With ASKO, we acquire a highly reputable company [that] will be very complementary and broaden our service offerings globally.”
Metso to relocate its recycling business factory in Denmark
Metso has decided to relocate its waste recycling business to a new factory and office facility in Denmark. The company says part of the relocation costs will be funded by selling the current property and estate in Horsens, Denmark. Metso says it has received a firm purchase offer from a local developer.
Metso’s current property is located within Horsens, and the company says developers are constantly seeking options to develop the area.
“We have now an opportunity to relocate our business to a logistically more suitable industrial area and offer the current property to be developed for other purposes,” says Uffe Hansen, president of the recycling business area for Metso.
The transaction is subject to final approval of the area’s development plan by the Horsens City Council. According to Metso, the new facility will likely be ready in 2020.
Metso’s recycling business provides equipment and services for mechanical treatment of metal scrap and solid waste. This business segment has about 100 employees. In total, 800 Metso shredders are in operation globally.
International Baler releases ‘European style’ auto-tie baler made in the USA

International Baler Corp. (IBC), Jacksonville, Florida, has begun producing its ATX auto-tie baler series, which it describes as a high-volume, “European style” baler for material recovery facility (MRF) and municipal solid waste (MSW) applications. The company says it is the first manufacturer to offer this class of machine manufactured in the United States, providing “a domestic alternative to the high cost and extended lead time of overseas shipping, parts and service.”
Designed for high-production applications, the ATX auto-tie baler is ideal for single- and dual-stream recycling facilities, large fiber processors and municipalities where speed is a necessity, according to IBC. The ATX is capable of processing more than 60,000 cubic feet of material per hour, with throughputs of up to 50 tons per hour.
The baler features a triple-motor 225-horsepower flooded suction power unit and a roller platen that is designed to be robust and to ride easily inside the chamber on solid steel ball-bearing rollers, the company says. It is equipped with a 10-inch (5,000 PSI) main bore cylinder to achieve optimal bale density, while a jam-clear stamper is designed to minimize downtime.
IBC says it has designed the ATX with longevity in mind using a solid-plate, keyed construction frame and heavy-duty hydraulics. The fully lined chamber features replaceable AR-450 liners that bolt into the machine to reduce downtime associated with conventional plug-welded liners during replacement.IBC says it plans to bring the ATX to market at a competitive price point and lead time.
More information is available by calling 800-231-9286.
International Truck expands HV and HX series
International Truck, headquartered in Lislie, Illinois, has announced the standard availability of air disc brakes for the International HV and HX series models. The HV507, HV607, HV513 and HV613 models, and the HX515, HX520, HX615 and HX620 models now feature Bendix ADB22X air disc brakes as a standard offering.
The Bendix ADB22X disc brake from Bendix Spicer Foundation Brake LLC, Elyria, Ohio, is designed with quicker pad replacement and longer pad life.
Redesigned from the inside out, the HV series features the Diamond Logic electrical system for the automation of tasks and interlocks. Both HV and HX series trucks feature power options like the International A26 engine.
Steinert LSS line sorting system separates multiple aluminum alloys
Steinert, a Cologne, Germany-based supplier of magnetic and sensor-based sorting technology, says its LSS line sorting system enables the separation of multiple aluminum alloys from presorted aluminum scrap with a single detection using a LIBS (laser-induced breakdown spectroscopy) sensor.
LIBS is a technology used for elemental analysis. By default, the calibration methods stored in the measuring device analyze the concentrations of the alloy elements copper, ferrous, magnesium, manganese, silicon, zinc and chromium, Steinert says.
The sorting of alloys involves first separating the shredded material mixture in such a way that the material is fed past the laser so that the laser pulses hit the surface of the material. This causes tiny particles of material to evaporate. The emitted energy spectrum is recorded and analyzed simultaneously to detect the alloy and the specific alloy components of each individual object, according to the company.
Different materials are detected in the first part of the machine; compressed air valves then shoot these materials into different containers in the second part of the machine, depending on their elemental composition.
Steinert says an aluminum recycler in Europe will be the first company to install this technology.
BHS system poised to purify paper in Norway

Norsk Gjenvinning (NG), based in Oslo, Norway, has selected Bulk Handling Systems (BHS), Eugene, Oregon, to supply NG’s new paper recycling system.
Scheduled to be operational in the first quarter of 2019, the system will process 22 tons per hour and run three shifts to process approximately 132,000 tons annually. The NG system will include Max-AI VIS (Visual Identification System) units designed to monitor the quality of outbound paper.
The Oslo facility also includes BHS’ latest technology designed to maximize NG’s paper quality. Six optical sorters from National Recovery Technology (NRT), Nashville, Tennessee, and four Max-AI AQC (Autonomous Quality Control) robotic sorters contribute to a highly automated process, allowing NG to run multiple shifts with what BHS calls a minimal variable cost increase.
NG will be able to analyze product quality in real time with its two Max-AI VIS units and the Total Intelligence Platform. Those units ensure NG that the system is creating highly pure paper, BHS says. With NRT and Max-AI technologies reporting material compositions through the Total Intelligence Platform, NG’s operators will gain valuable analytics to track, analyze and share with customers, the supplier says.
“The level of automation and technology is astounding and will help us achieve new levels of throughput and quality,” says Frode Karlsen, NG’s head of the Oslo-region.
He adds, “We are very eager to receive the equipment and start production as soon as we can next year.”
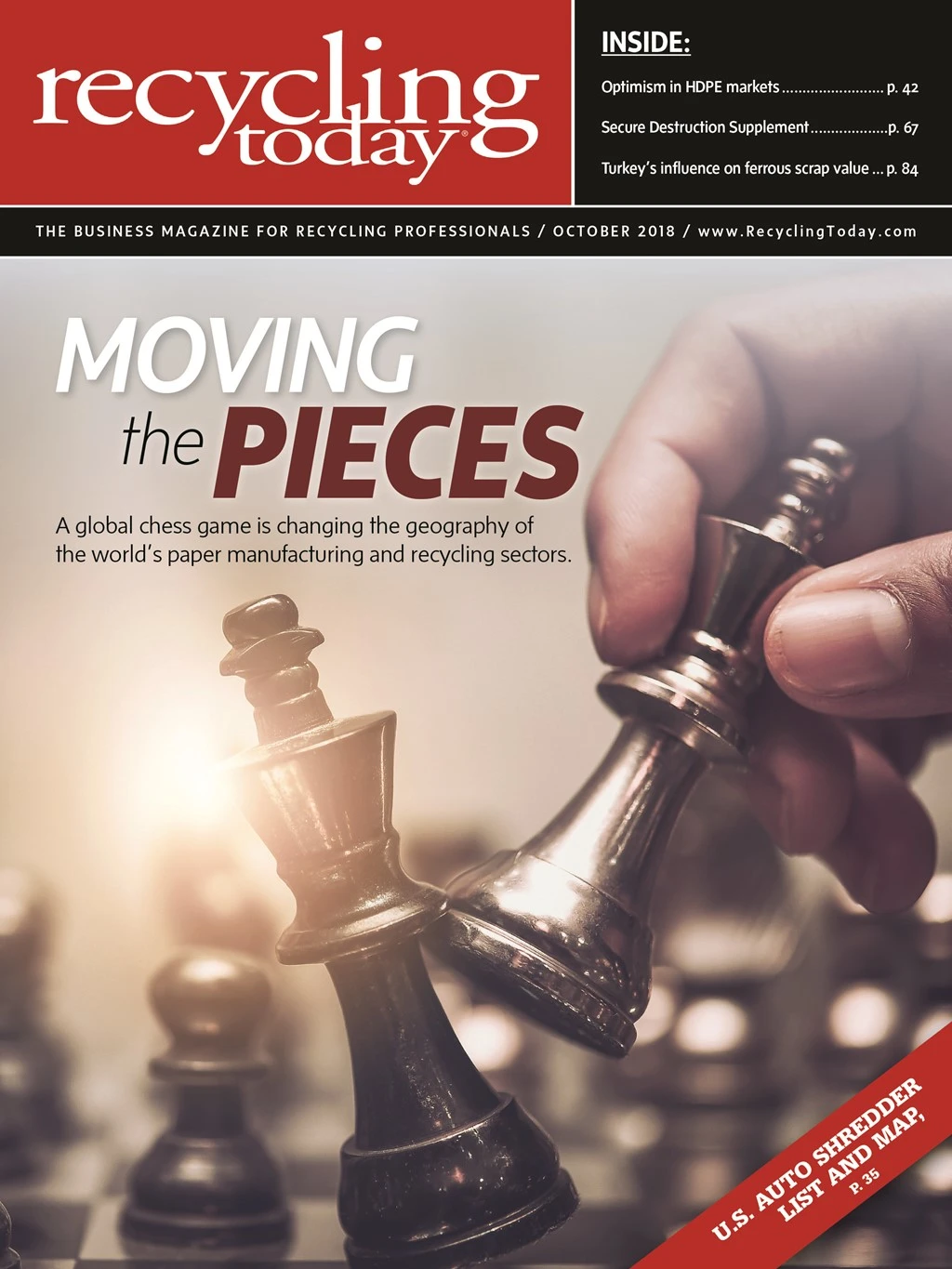
Explore the October 2018 Issue
Check out more from this issue and find your next story to read.
Latest from Recycling Today
- NWRA announces 2025 Driver of the Year, Operator of the Year winners
- The Scrap Show: Nanci Schuld of FE Trading Group LLC
- Call2Recycle Canada partners with RLG to advance battery collection
- Report delves into recovery opportunities for food-grade polypropylene
- Reimagining Supplier Payments in Metal Recycling: A Digital Leap Forward
- STEINERT Lithium Battery Detection and Removal from Waste Streams
- Driving the Future: Innovations in Waste & Recycling Technology
- Robin Wiener recognized for recycling leadership