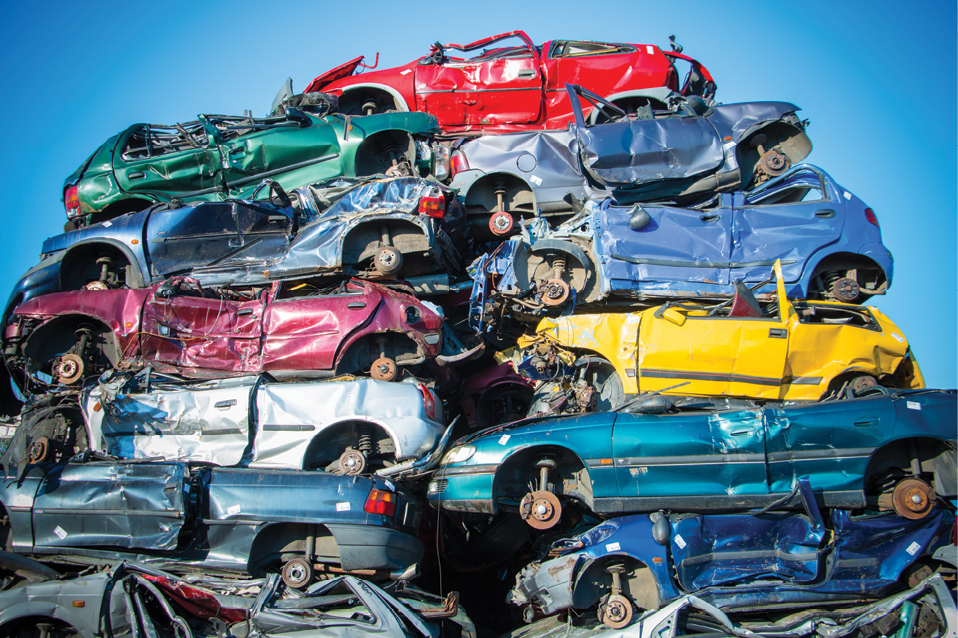
Greenwave launches AI expansion of Scrap App
Greenwave Technology Solutions Inc., a Chesapeake, Virginia-based metals recycler, has launched an artificial intelligence- (AI-) powered expansion of its subsidiary, Scrap App.
Greenwave launched Scrap App in September 2023, describing it as an optimized pricing tool for scrapped vehicles.
The company says Scrap App’s AI operator enables it to autonomously provide real-time quotes for scrap cars, schedule vehicle pickups and handle customer inquiries. This automation reduces operating costs, enhances scalability and improves customer experience, according to Greenwave.
The company operates 13 metal recycling facilities across Virginia, North Carolina and Ohio, supplying steel mills and other industrial partners. Greenwave says it plans to expand Scrap App into the top U.S. markets by the end of the year.
“Scrap App’s AI technology is redefining the junk car industry,” Greenwave CEO Danny Meeks says. “This innovation not only enhances operational efficiency but also positions us as a leader capable of scaling rapidly in a high-growth market,” he adds.
“We’re building Scrap App to create a smoother and more efficient scrapping experience for both scrappers and businesses,” Meeks said at the time of Scrap App’s launch.
“If Scrap App gains widespread adoption, we intend to charge a fee for every transaction it facilitates—along with monthly recurring listing fees.”
In early February, Greenwave announced Scrap App was adopted by one of the largest buyers of junk cars in the U.S.
Industrial Resin Recycling installs MAS extruder system
Industrial Resin Recycling Inc. (IRR), a Howell, Michigan-based full-service recycler of postindustrial and postconsumer plastics, recently completed a $2.5 million installation of a MAS twin-screw extruder system at its extruding facility in Fowlerville, Michigan.
The company says it expects the equipment upgrade to increase the facility’s compounding capacity by more than 40 percent.
The extrusion system developed by Austria-based MAS is used to process different plastics fractions, such as materials of the lowest bulk density, mill materials, flake, new products and fibers. Additives, filling materials and fibers can be added directly via the feed opening without complicated and high-maintenance side dosing.
In a news release announcing the equipment upgrade, IRR says this advanced technology improves not only sustainability but also circularity.
Along with the startup of the extrusion system in Fowlerville, IRR is in the process of setting up a shredder-feeder-extruder combination at its facility in Piedmont, Alabama, that the company expects will expand its postconsumer recycling business. The location processes nonwovens, film and carpet.
Founded in 1995, IRR is a full-service, ISO 9001-certified recycler primarily serving the Midwest and Southeast regions of the United States. The company processes approximately 35 million pounds of plastic per year.
IRR sources plastics such as polyethylene, polypropylene, polystyrene, polycarbonate, polyvinyl chloride, nylon and more from industries that include automotive, houseware, health care, consumer products and carpeting, among others.
IRR’s three facilities perform different functions. At its Howell headquarters, it shreds, grinds and float-sinks materials; in Fowlerville, it extrudes material and operates a comprehensive testing laboratory; and in Piedmont, it shreds, grinds, float-sinks and extrudes plastics.
IRR also offers programs to recycle cardboard, pallets, steel, aluminum, copper and brass.
In addition to its recent upgrades, the company operates eight shredder-grinder combinations, four grinders, two float-sink wash lines, seven extruders, four high-capacity blenders and two complete laboratories.
IRR also has several silos and the ability to work with railcars.
It maintains a full fleet of trucks in-house that allows it to ensure timely collection of materials.
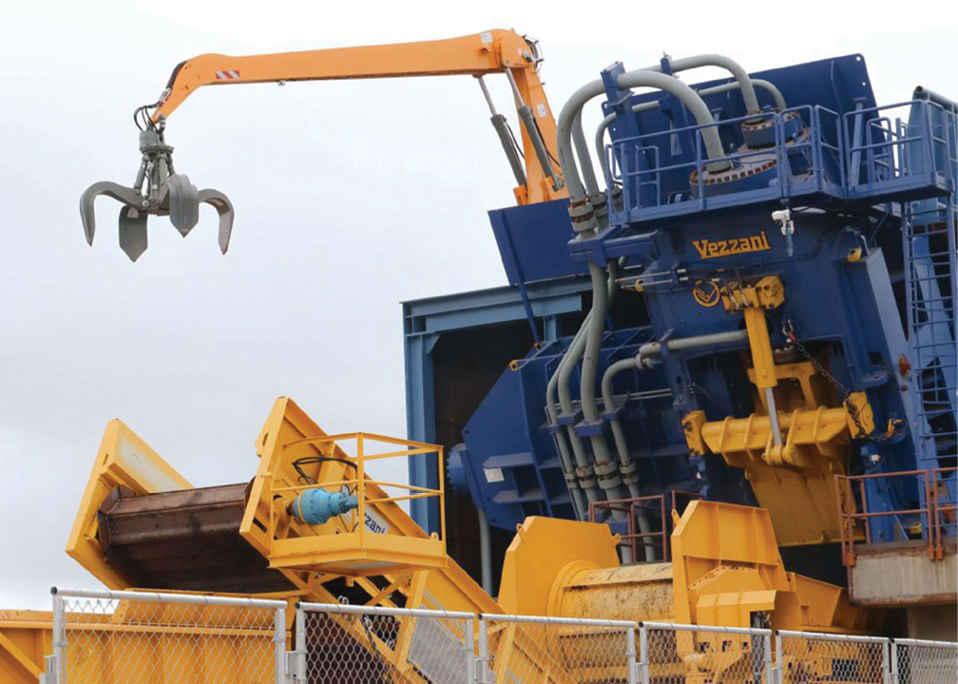
Sims announces investments in Virginia facility
Sims Metal, a business unit of Australian company Sims Ltd. with sizable operations in North America, has invested $20 million to upgrade its metals recycling facility in Chesapeake, Virginia.
The investments in eastern Virginia include a new Vezzani shear, a STAR downstream shredded metals sorting plant and a planned connection to the freight rail system.
“By utilizing electric power, the newly installed Vezzani shear at Sims Metal is projected to reduce energy consumption, and consequently greenhouse gas emissions, by 80 percent compared to previous methods,” says Michael Henderson, chief operating officer in North America for Sims Metal. “This aligns with our efforts to help our customers undertake more energy-efficient, lower-emissions metal manufacturing.”
In a late 2024 LinkedIn post, Sims Metal also reports building an advanced indoor maintenance facility to better service equipment without compromising the environment or employee safety.
Another major investment has been made in the metals sorting system found downstream of the Sims auto shredding plant in Chesapeake.
“The STAR Plant, a groundbreaking innovation in metal recycling, is exclusively available in North America,” Henderson says.
“This advanced technology separates copper and aluminum metal particles as small as a grain of sand, significantly minimizing landfill waste and extending the lifespan of valuable metal resources, ensuring their continued availability for critical American manufacturing supply chains.”
In January, the Virginia Department of Rail and Public Transportation (DRPT) approved a $750,000 grant under its Rail Industrial Access Program to Sims Metal for work to be done at the Chesapeake location.
During its January meeting, the DRPT voted to award the grant, which will assist in connecting the facility to the freight railroad network.
Sims Metal in Chesapeake imports ferrous and nonferrous recycled metals and exports sorted metals to steel mills, which DRPT says contributes to the sustainability and efficiency of the recycling industry in Virginia.
Get curated news on YOUR industry.
Enter your email to receive our newsletters.

Explore the March 2025 Issue
Check out more from this issue and find your next story to read.
Latest from Recycling Today
- ReMA opposes European efforts seeking export restrictions for recyclables
- Fresh Perspective: Raj Bagaria
- Saica announces plans for second US site
- Update: Novelis produces first aluminum coil made fully from recycled end-of-life automotive scrap
- Aimplas doubles online course offerings
- Radius to be acquired by Toyota subsidiary
- Algoma EAF to start in April
- Erema sees strong demand for high-volume PET systems