Stadler, Krones supply Republic’s Polymer Center in Las Vegas

Stadler Anlagenbau GmbH
Stadler Anlagenbau GmbH, in collaboration with fellow Germany-based technology provider Krones, has designed and installed much of the equipment at the new Republic Services Polymer Center in Las Vegas.
The facility processes plastic bottles, jugs and containers to produce recycled-content plastic materials ready for use in new packaging, according to Stadler. The site has been designed to produce more than 50,000 tons per year of recycled-content resin products.
The facility receives plastics collected by Republic Services in the western United States to recover PET, which is converted into recycled PET (rPET) flakes that can be turned into new bottles and polyolefins suitable for use in new bottles, jugs and containers. The facility sorts and processes baled materials on either a PET or mixed plastics line. Each line has a capacity of five tons per hour.
Materials fed into the PET line undergo mechanical separation and the identified PET material is cleaned of ferrous particles. A Stadler STT2000 ballistic separator sorts the material into rolling, or 3D, flat and fines fractions.
The fractions go through sensor-based sorting with near-infrared (NIR) sorters. Caps, rings and the flat fractions go to compactors. The 3D fractions are directed to a Stadler Label Remover to undergo that process. The clear PET, caps and rings are directed to the Krones washing line, which granulates and cleans the material, while the colored PET is compacted into bales.
On the mixed plastics line, mechanical separation sorts the infeed into fines and sieve overflow, with the latter further separated into light and heavy fractions. The heavy fraction is sorted into four polyethylene (PE) products—natural, white, red/orange/yellow and other colors—and two polypropylene (PP) products—natural/white and other/color.
PET is sorted out of the remaining material and sent to the PET line. The products of the mixed plastics line are conveyed to storage bunkers where a semiautomatic feeding program allows for materials to be discharged by grade to be fed into the baler, Stadler says.
Recology opens new California MRF
The Recology Sonoma Marin business unit of San Francisco-based Recology opened its new material recovery facility (MRF) in Santa Rosa, California.
Recology says the MRF reflects its efforts to shift the waste industry from traditional waste management to resource recovery, “in pursuit of a world without waste.”
The MRF, which opened Jan. 29, will process mixed recyclables from 13 communities in Sonoma and Marin counties in California and is predicted to achieve a recovery rate of 85 percent for materials collected. Recology says that would mark an improvement from the previous facility’s 75 percent rate.

“This plant gives customers peace of mind that the recyclables they put in their blue bin will be properly recycled,” Logan Harvey, the senior general manager of Recology Sonoma Marin, says.
The new plant cost $35 million and took 10 months to build. It measures 85,000 square feet and includes 109 conveyor belts, with the combined length of the conveyors measuring 1.58 miles.
The MRF has a projected capacity that is nearly three times more than the previous facility—up to 400 tons per day compared with 150 tons previously.
Recology engaged recycling equipment manufacturer Machinex, Plessisville, Quebec, to help design, fabricate and install the system.
Recyclables are separated by hand and by automated equipment.
Seven optical sorters use infrared light and air nozzles to sort materials and remove contaminants. They send clear plastic water bottles one way and colored detergent bottles another. A spinning magnet picks up steel cans and sends them to a conveyor belt leading to a high-density baler. An eddy current separator repels aluminum cans in another direction.
Employees on the “last-chance line” grab any plastic bottles that make it past optical sorting machines.
“The system is designed to ensure that the recyclable material we collect has multiple opportunities to get separated and recycled,” Harvey says.
Shred-Tech’s 3R-Machinery forges distribution alliance

& Manufacturing
Raleigh, North Carolina-based 3R-Machinery, a business unit of Shred-Tech, has forged a collaboration arrangement with Screenpod Design & Manufacturing, headquartered in Northern Ireland.
The joint entity is an exclusive partnership for distribution in North America. “3R-Machinery will be distributing the Screenpod range of density separation, dust control and recycling machines, many of which will complement the current 3R-Machinery lineup and enrich our green initiative,” says Shred-Tech, which is based in Canada.
Established in 2013, Screenpod produces a range of recycling and waste sector products, including dust cannons and the PortaVac and Airvac equipment lines.
“We are thrilled about this partnership and the potential it holds for revolutionizing waste management,” says Allen Hyman, business manager of 3R-Machinery. “By combining our expertise with Screenpod’s cutting-edge solutions, we aim to set new industry standards, build new and lasting relationships and contribute significantly to a more sustainable future.”
Screenpod Sales Manager Leon Connolly adds, “This collaboration is a testament to our shared vision of advancing material processing solutions globally. We are excited about the impact our joint efforts will have on the industry, promoting efficiency, innovation and responsible waste management practices.”
The companies say the arrangement enables the integration of 3R-Machinery’s robust waste management equipment with Screenpod’s advanced material separation technologies. Clients will benefit from a comprehensive suite of solutions for waste handling and reduction processes, improved recycling efficiency and minimized environmental impact.
3R-Machinery distributes Shred-Tech shredding and recycling equipment. Screenpod, in addition to dust control and vacuum equipment, offers trommel screens, picking stations and flotation separators.
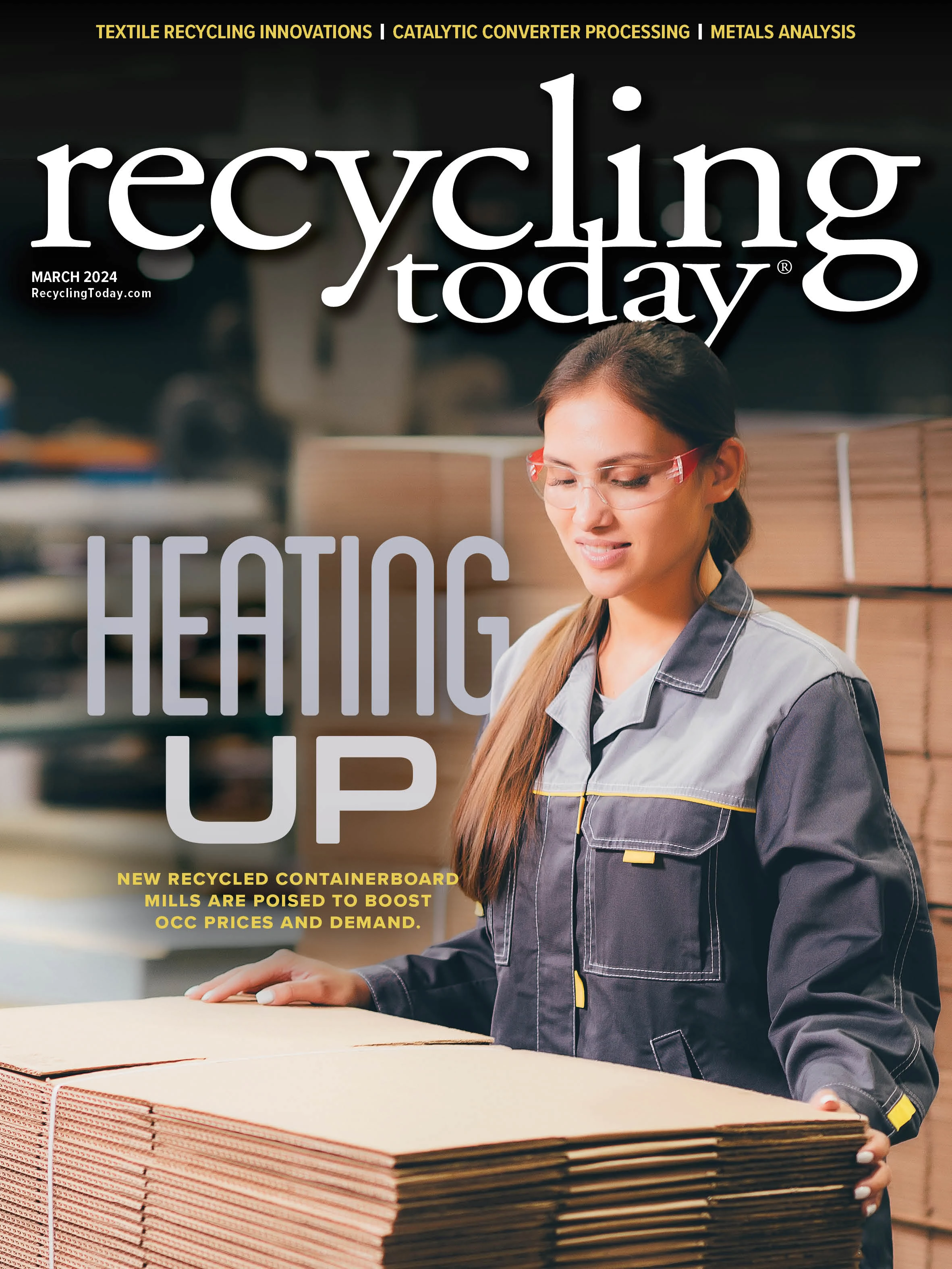
Explore the March 2024 Issue
Check out more from this issue and find your next story to read.
Latest from Recycling Today
- Steer World offers PEX plastic recycling machine
- New recycling grant program launches in Massachusetts
- Tire Recycling Foundation names executive director
- Dock 7 named 2025 Exporter of the Year at New Jersey International Trade Awards
- Waste Connections reports ‘better than expected’ Q1 results
- Commentary: How EPR is transforming the packaging industry
- Acerinox names new North American Stainless CEO
- Greenwave closes 2024 books with red ink