Waste Management upgrades Elkridge, Maryland, MRF

Houston-based Waste Management’s Kit Kat Road material recovery facility (MRF) in Elkridge, Maryland, recently installed anti-wrapping screens from Van Dyk Recycling Solutions (VDRS), Stamford, Connecticut.
The 50-ton-per-hour system processes 1,000 tons per day and operates around the clock, according to a news release from VDRS, leaving little time for maintenance. Cleaning the old screens took too much time and manpower and ate into the time needed for other maintenance.
However, the nonwrapping screens, which can be retrofit into any system, can reduce cleaning time by 90 percent, with customers reporting cleaning times of 10 minutes per shift, according to VDRS.
The company replaced six screens in the retrofit. Four Non-Wrapping 440 screens replaced four existing ONP (old newspapers) screens, and two new commingled screens (with an updated design) replaced two existing commingled screens.
Each screen was upgraded from a 2,540-millimeter (8.3-foot) width to a 3,040-millimeter (10-foot) width. The system, which is rated for 50 tons per hour, frequently processes more than 60 tons per hour, and the extra width of the screens offers flexibility to further increase tonnage in the future.
More information on VDRS is available at www.vdrs.com.
JCB receives Pillar of the Industry award

JCB, with North American headquarters in Savannah, Georgia, was honored with a Pillar of the Industry award by the Association of Equipment Manufacturers (AEM), headquartered in Milwaukee. The award reflects the company’s work to improve the business environment for the equipment manufacturing industry, its advocacy for promanufacturing solutions and its participation in AEM’s I Make America grassroots program.
“With a new Congress and administration in Washington this year, equipment manufacturers did a better job than ever at communicating our industry’s priorities to our elected leaders,” says Dennis Slater, AEM president.
“As a leading construction and agricultural equipment manufacturer, we’re grateful at JCB for the opportunity to promote policies that support manufacturing jobs and help America’s manufacturers to compete on the global stage,” says Richard Fox-Marrs, president and CEO of JCB North America.
“And we’re especially proud to have supported AEM’s I Make America campaign, which has struck a chord with our state and federal leaders and our workforce and helped remind all Americans that a strong manufacturing base is a national asset to be valued,” he adds.
More information on JCB is at available on the company’s website at www.jcb.com.
Stadler expands North American parts and service facility

Integrated recycling system provider Stadler America LLC, based in Colfax, North Carolina, says it has again expanded its parts and service facility to demonstrate its commitment to customers throughout North America.
“With our rapidly growing customer base, it was imperative that we expand to meet their needs,” says Marty Kennedy, Stadler America chief operating officer. “The volume of inquiries for advanced system designs and Stadler core components that we’re receiving has been nothing short of amazing. We see this investment as part of the work being done to prepare ourselves to meet continued growth in customer demand.”
Stadler opened its North American headquarters, parts facility and technical support center in March 2016. This expansion will double the company’s parts inventory and expand the availability of its technical support team, the company says.
“We understand how important providing after-sales support is, not only in word but also in action,” says Nico Sherwood, after-sales program director for Stadler America LLC. “This commitment grows our parts inventory considerably. Combined with our U.S.-based support staff and after-sales team, it’s a demonstration of the importance Stadler places on supporting our customers. We want customers to know that they can rely upon us long after they place an order with us.”
Stadler America is part of Germany-based Stadler Anlagenbau GmbH. Visit www.w-stadler.de for more information.
Komatsu Southwest adds Sennebogen material handlers to its equipment lineup

Komatsu Southwest, Albuquerque, New Mexico, which serves that state and West Texas, is adding material handlers from Sennebogen LLC, Stanley, North Carolina, to its flagship line. Komatsu Southwest President Grant Adams has been leading a program to grow the company’s scope of equipment and services.
“We’ve always enjoyed success working with industry leaders, and we’re very pleased to have Grant and the Komatsu Southwest team representing us in the region,” Constantino Lannes, president of Sennebogen LLC, says.
Adams says he had planned to add Sennebogen to his product mix from the beginning. Prior to taking his appointment to open Komatsu Southwest, he held senior positions with other Sennebogen dealers on the East Coast.
“When I came out west, I knew that Komatsu and Sennebogen were a great fit,” Adams says. “I started a dialog with Constantino right away.”
In addition to supporting current Sennebogen customers, Komatsu Southwest plans to build its business in scrap, recycling and waste facilities, quarries, log yards and sawmills, demolition and pipe-handling applications for the oil and gas industry.“With Sennebogen’s support and training programs, we are investing very heavily in factory training for all of our staff,” Adams says. “We’ll also have a Sennebogen product specialist on our sales team to assist our representatives in advising their customers on their material handling applications.”
Visit www.sennebogen-na.com and http://komatsusw.com for additional information.Rigaku upgrades KT Series handheld LIBS analyzers
_fmt.png)
Rigaku Analytical Devices, Wilmington, Massachusetts, says its previously released hand-held laser-induced breakdown spectroscopy (LIBS) metal analyzer has been improved and is faster than before.
The KT-100S is an upgrade to the KT-100 LIBS analyzer, which was released in September 2015. The KT-100S expands the use of hand-held LIBS to more difficult applications, such as recycling, fabrication, aerospace, automotive and refineries, especially for the analysis and separation of most nonferrous alloys, according to Rigaku.
The company says its KT Series analyzers enable accurate alloy identification in industrial environments.
Designed to fill the performance and feature gaps of traditional analysis methods, such as hand-held X-ray fluorescence, Rigaku says the KT-100S offers more convenient, on-the-spot identification of the most difficult alloys. By incorporating a second-generation spectrometer that produces higher throughput and better resolution, the user can expect better detection limits and the ability to analyze more alloys. This includes better precision for low-alloy steels, stainless steels and high-temperature alloys and the added detection of lithium, according to the company.
Another benefit to users is that because the KT Series of hand-held LIBS analyzers uses a laser excitation source, minimal to no regulatory licensing is required, says Rigaku Analytical Devices. This also eliminates X-ray radiation exposure.
“We are committed to continuously improving our hand-held analytical capabilities,” says Bree Allen, president at Rigaku Analytical Devices. “We built a solid reputation for hand-held LIBS with the launch of our KT-100 analyzer in 2015, and now the KT-100S will exemplify the same innovation and quality the Rigaku brand is known for.”
Rigaku says additional key features of the KT-100S include:
- ease of use because of the analyzer’s ergonomics and the simple software interface;
- light element and base alloy analysis with a two-to-four-second analysis time;
- MIL-STD 810G certification;
- long battery life.
More information on the KT-100S is available at www.rigaku.com/KT100S.
NASCO-OP declares 2017 dividend
National Association Supply Cooperative (NASCO-OP), New Philadelphia, Ohio, has declared a 1.3 percent patronage dividend for 2017.
The dividend, which is calculated on purchases members or associates of the recycling industry purchasing cooperative have made for the year, further reduces the purchase price of their supplies and equipment, according to NASCO-OP Manager Bob Bedard.
“In today’s increasingly competitive marketplace, the need for NASCO-OP is greater now than ever before,” he says.
“Cooperatives give members and users of all sizes the purchasing clout of an entire industry while still maintaining their independence,” Bedard continues. “The success of the organization is power through cooperation. Just consider the negotiating leverage when members pool their purchases of one item, say conveyor belts, through NASCO-OP. With the united needs of that size of a group, NASCO-OP members are in the position to accept only the best value from belt manufacturers.”
Additional information on NASCO-OP can be found at www.nascoop.com.
Quebec MRF upgrades equipment with Machinex to improve quality
Machinex Technologies, Plessisville, Quebec, has completed an equipment upgrade to the Récupération Mauricie material recovery facility (MRF) near Trois-Rivieres, Quebec. The purpose of the upgrade was to increase the system’s efficiency and the quality of the sorted material.
Machinex incorporated new equipment into the existing MRF. Additions include a ballistic separator to separate packaging from mixed paper and two optical sorting units, one of which sorts contaminants from mixed paper and the other separates plastics into three categories: polyethylene terephthalate (PET), high-density polyethylene (HDPE) and mixed plastics.
The old corrugated containers (OCC) separator has been replaced by a new generation model, which Machinex says reduces wrapping of plastic film around the components.
Most of the glass fragments are removed at the beginning of the sorting line with the addition of a glass separator, and a Machinex eddy current separator removes aluminum cans.
“We are very proud to have realized this project of modernization at Récupération Mauricie, because it is a long-time customer for Machinex with whom we built a relationship of trust,” says Pierre Paré, Machinex Group CEO. “The added high technologies will allow Récupération Mauricie to increase its productivity but [also] especially to improve the quality of its products.”
Daniel Cassivi, managing director of Group RCM and Récupération Mauricie, says he was impressed with Machinex’s team. “Throughout the project, we felt that people at Machinex were in control of the situation, which was confirmed by the resumption of the activities without delay according to the initial planning. We lived a positive experience at every level.”
Cassivi adds, “After only one week of operation, the upgraded system can produce a quality fiber good enough to sell to China, according to one of our brokers.”
Machinex, www.machinextechnologies.com, is a developer of sorting, waste management and recycling technology. It has designed and installed more than 350 turnkey facilities in partnership with leading MRFs in Canada, the United States, Europe and Oceania.
In the early 1980s, Machinex says it became the first company in Canada to design and manufacture machinery for MRFs.
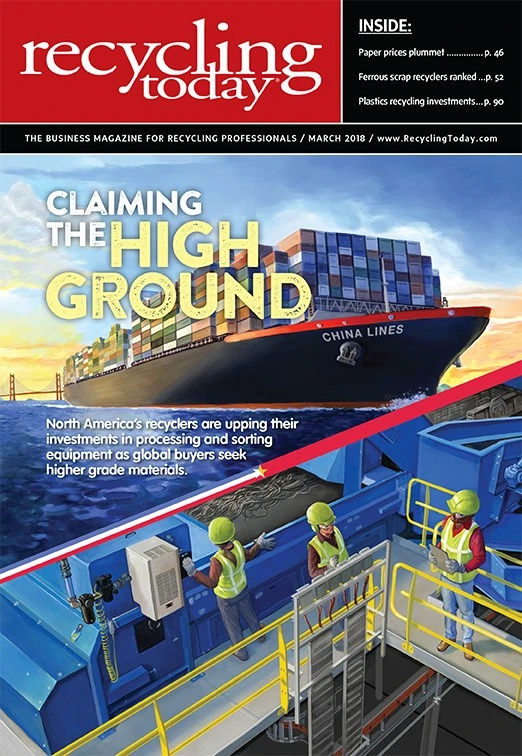
Explore the March 2018 Issue
Check out more from this issue and find your next story to read.
Latest from Recycling Today
- New copper alloy achieves unprecedented high-temperature performance
- Gränges boosts profits and sales volume in Q1 2025
- RMDAS April figures show recycled steel price setback
- Steer World offers PEX plastic recycling machine
- New recycling grant program launches in Massachusetts
- Tire Recycling Foundation names executive director
- Dock 7 named 2025 Exporter of the Year at New Jersey International Trade Awards
- Waste Connections reports ‘better than expected’ Q1 results