Erema reports demand for plastic film recycling systems

Ansfelden, Germany-based equipment maker Erema has reported a 100 percent sales increase in its most recent fiscal year for its Intarema K automatic processing and recycling system for plastic film edge trim.
The company indicates that by the end of March 2018, more than 40 of the Intarema processing systems will have been shipped in the previous 12 months—twice as many compared with the previous financial year.
According to Erema Business Development Manager Andreas Dirnberger, the fact that customers are concentrating more on the recycling of clean edge trim can be explained largely by the increasing demand for high-quality film products and the associated expansion of production capacities.
“The material alone accounts for around 80 percent of the manufacturing costs of flexible packaging,” says Dirnberger. “If you consider the usual edge trim figure of around 10 percent in blown film manufacturing, recycling is a must-have in terms of cost efficiency.”
The edge trim that accumulates in production can be transferred directly from the blown film plant—without pre-shredding—to make high-quality scrap material. According to Dirnberger, 100 percent of the scrap material can then be put back into the production process.
Manfred Goellner, head of process engineering at Germany-based Hosokawa Alpine, one of the largest producers of blown film plants in the world, comments, “We expect a recycling system to work with absolute reliability and fully automatically. This is why we have a machine built by Erema in use in our in-house technical center and also recommend that our customers count on the Intarema K.”
While the Intarema K is available to OEM (original equipment manufacturer) customers such as Hosokawa Alpine as part of standardized system packages, there also is high demand for the system among end customers, says Erema.
“We have been using fully automatic edge trim processing systems from Erema for many years, not least because the payback period for the compact systems is very short,” says Ferdinand Mikesch, head of
The Intarema K can be used to recycle several types of clean plastic scrap, according to Erema, including PE (polyethylene) mono- or multilayer films; PE films with PP (polypropylene), PA (polyamide), EVOH (ethylene vinyl alcohol) or EV (ethylene vinyl); and breathable films, such as PE with calcium carbonate.
For more information, visit www.erema-group.com.
Liebherr expands Virginia headquarters, distributor network

Liebherr International AG, the family-owned construction machinery and earthmoving equipment manufacturer with U.S. headquarters in Newport News, Virginia, has announced its $45 million investment to expand its Newport News facility.
The new expansion will include the construction of three new buildings on 28 acres adjacent to Liebherr’s current manufacturing facility. Once completed, the new facilities will total more than 251,000 square feet and will be occupied by Liebherr USA Co. The expansion will offer space for Liebherr USA’s new headquarters and administrative building, a production and workshop facility and a warehouse and distribution building. Construction is expected to begin in July 2018 and will be completed by summer of 2020.
“Since 1970, our continued success and commitment to customers in the United States has always been at the forefront of everything we have done and continue to do,” Torben Reher, managing director of Liebherr USA, says. “This expansion underlines our commitment and further strengthens our position in North America to deliver sustainable long-term growth and to offer exceptional and consistent experience to customers across the United States.“

In other company news, Liebherr USA Co.’s Construction Equipment division has expanded its dealer network by adding State Machinery & Equipment Sales Inc. The Kenner,
“I am proud of and excited about this new opportunity with Liebherr USA Co. Construction Equipment division,” Ed Renton, president of State Machinery, says. “State Machinery looks forward to great success in this market with such quality products.”
Since 1989, State Machinery has served New Orleans and surrounding communities with new, used and rental heavy equipment.
“We are thrilled about our new partnership with State Machinery,” says Peter Mayer, managing director of Liebherr USA Construction Equipment. “Their exemplary customer service and extensive knowledge of Liebherr parts
For more information, visit www.liebherr.com and www.statemachinery.com.
BHS expands its Max-AI product line

The Max-AI AQC (Autonomous Quality Control) product line from Bulk Handling Systems (BHS), Eugene, Oregon, has expanded with the release of the AQC-2 for paper sorting applications. Max-AI technology employs artificial intelligence (AI) to make material identification and selection decisions, while robotic sorters carry out the sorting.
The AQC-2 features two robotic sorters and is designed for belt widths of up to 72 inches. It complements the earlier release of the AQC-1, BHS says, which has been used to sort containers and contamination in plastics and metals and to recover high-value items from residue.
The AQC-2 recovers cardboard, containers and plastic film and removes contamination to create a clean news product, BHS says. The AQC-2 complements BHS’ Tri-Disc technology and optical sorters from National Recovery Technologies (NRT), Nashville, Tennessee.
BHS says the level of automation possible with Max-AI technology can lower operating costs while adding production and quality capabilities that surpass manual sorting.
BHS also has announced the launch of technology to provide material recovery facility (MRF) operators with what it describes as “unprecedented levels of information about their business.”
The Total Intelligence Platform monitors and tracks throughput, uptime, downtime, material composition, motor amperage and performance data from optical sorters and Max-AI-powered equipment. It even provides operators with information external to the recycling system but vital to operational success, including inbound and outbound weights, bales shipped and bales on hand by commodity, BHS says.
Visit www.bulkhandlingsystems.com for more information.
Get curated news on YOUR industry.
Enter your email to receive our newsletters.
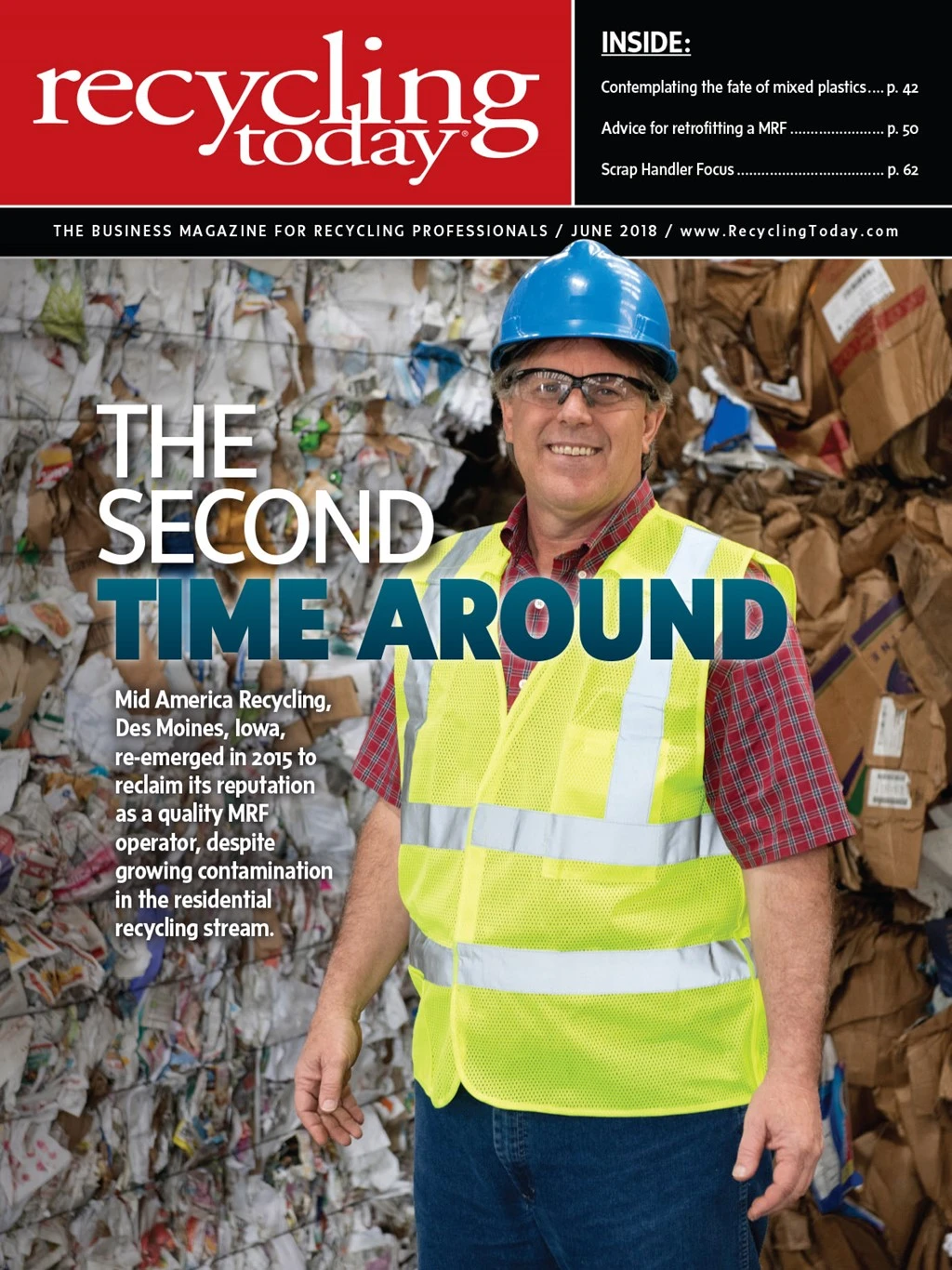
Explore the June 2018 Issue
Check out more from this issue and find your next story to read.
Latest from Recycling Today
- Toppoint Holdings expands chassis fleet
- Lego creates miniature tire recycling market
- Lux Research webinar examines chemical recycling timetables
- Plastics producer tracks pulse of wire recycling market
- Republic Services, Blue Polymers open Indianapolis recycling complex
- Altilium produces EV battery cells using recycled materials
- Brightmark enters subsidiaries of Indiana recycling facility into Chapter 11
- Freepoint Eco-Systems receives $50M loan for plastics recycling facility