Gerdau invests $10 million in nonferrous scrap separation system
Steelmaker Gerdau of Brazil is planning a $10 million project to upgrade the nonferrous scrap separation system at its steel mill in Whitby, Ontario. The company says planning for the project is currently underway, with construction slated to begin in the first half of 2016.
Gerdau has contracted with Italy-based Danieli Centro Recycling (DCR) to upgrade its Whitby nonferrous scrap system.
The technology for the new system allows Gerdau to sort and extract nonferrous scrap metal that is not used in the steelmaking process. The nonferrous metals, such as aluminum, copper and stainless steel, can be separated from the scrap steel mix and recycled or sold to be used in other manufacturing processes.
When the system is fully operational, Gerdau says it will be able to process nearly 40 million pounds of nonferrous scrap material annually.
Alan Lamb, vice president and general manager of Gerdau’s Whitby mill, says, “This investment will significantly increase the amount of ferrous and nonferrous materials we’re able to recover and ultimately recycle and we feel provides an opportunity for growth that will allow Gerdau to remain globally competitive.”
The Whitby mill uses ferrous scrap steel from end-of-life vehicles and other sources, which is melted and produced into merchant bar quality products and reinforcing steel used in a variety of applications, including major commercial buildings, freeways, bridges, parking garages and other concrete structures throughout North America.
Republic Services’ Southern Nevada Recycling Center features equipment from CP Group
San Diego-based CP Group and Phoenix-based Republic Services Inc. unveiled what they describe as a “state-of-the-art” recycling center in a November 2015 grand opening ceremony. The grand opening welcomed more than 450 attendees to tour the facility and education center.
_fmt1.png)
The 110,000-square-foot Southern Nevada Recycling Center has been dubbed by Republic Services as “the largest and smartest residential recycling center in North America.”
Site development constructed by Cambridge Cos., Griffith, Indiana, and equipment installation by CP Group was completed in 12 months, from the groundbreaking in November 2014 to the grand opening at the end of 2015, CP Group says. CP Group engineered the residential and commercial single-stream processing system, capable of processing 2 million pounds of recyclables daily, or 70 tons per hour. This capability is expected to double recycling capacity throughout Clark County, Nevada, the company says.
The facility features two 35-ton-per-hour sorting lines for operational flexibility, according to a news release issued by CP Group. Republic is able to process material on one or both lines and can bypass certain parts of the system when processing different material types.
While the center largely will process residential recyclables, it also has the ability process commercial and industrial streams. This built-in flexibility allows the system to adapt as the composition of the recycling stream evolves, according to CP Group.
“There are scales through the system,” Terry Schneider, president and CEO of CP Group, says. “[The incoming tonnage] can be calculated on a constant basis.”
The system also can process material quickly. “In 30 minutes, we can process as much recycling as 155 households will generate in a year,” says Len Christopher, general manager for postcollection at Republic Services.
Caterpillar, Lefort form marketing agreement
Caterpillar Inc., Peoria, Illinois, and Lefort North America LLC, West Palm Beach, Florida, have entered into an exclusive marketing agreement to supply Lefort hydraulic shears and balers commonly used in scrap metal recycling. Lefort North America is a distributor for shear and baler manufacturer Lefort, based in Belgium.

The Lefort products, available in stationary and portable versions, will be sold exclusively by Cat dealers in the United States and Canada.
The companies say the vision for this agreement is to combine the strength of Cat’s distribution network with Lefort’s innovative design and precision engineered products.
“We are pleased to be working with Lefort to meet customers’ portable and stationary shear and baler needs,” says Denise Johnson, vice president of material handling and underground division, Cat.
Founded in 1947, Lefort says it manufactures machines in the company’s Belgium factories using state-of-the-art engineering and design methods. Lefort’s North American headquarters is located in West Palm Beach. This company’s North American headquarters also serves as the parts distribution center for the U.S. and Canada.
Sense2Sort and Austin AI strike sensor sorting alliance
Sorting technology firms Sense2Sort/Toratecnica S.L., Igualada, Spain, and Austin AI Inc., Austin, Texas, have announced they “have joined forces to provide the marketplace with the most advanced and most comprehensive product offering possible.”

The two companies say their alliance has been spurred by changes in the marketplace requiring shredded nonferrous metals products with purer chemistry than that of the zorba grade.
“Everyone is aware of the need to recover more metals with more specificity from zorba and other nonferrous scrap metal streams, such as e-scrap and bottom ash,” Sense2Sort and Austin AI write in the news release announcing their alliance.
“It is clear that the future is dim for those who wish to simply sell zorba as is and [who] rely on end users to perform the final cleanup stages either premelt or in-melt,” the companies continue. “This change is happening now in the secondary aluminum smelting industry as the market for aluminum scrap is much stronger than for that of zorba.”
The combined product lines of the two companies comprise an array of devices and systems, including X-ray fluorescence (XRF), X-ray transmission (XRT), laser-induced breakdown spectroscopy (LIBS), near infrared (NIR), terahertz- (THZ-) based black plastics sorting, induction sensor sorting (ISS), CCD (charge-coupled device) color sorting and robot picking technology.
The two companies say they also will work with supply partners to “provide complete, turnkey process lines” that can include conveyors, hoppers, shredders, sieves, magnets, eddy current separators, compressed air devices and dust control technology.
Additional information about the product lines of both companies can be found at www.sense2sort.com and at www.austinai.com.
Get curated news on YOUR industry.
Enter your email to receive our newsletters.
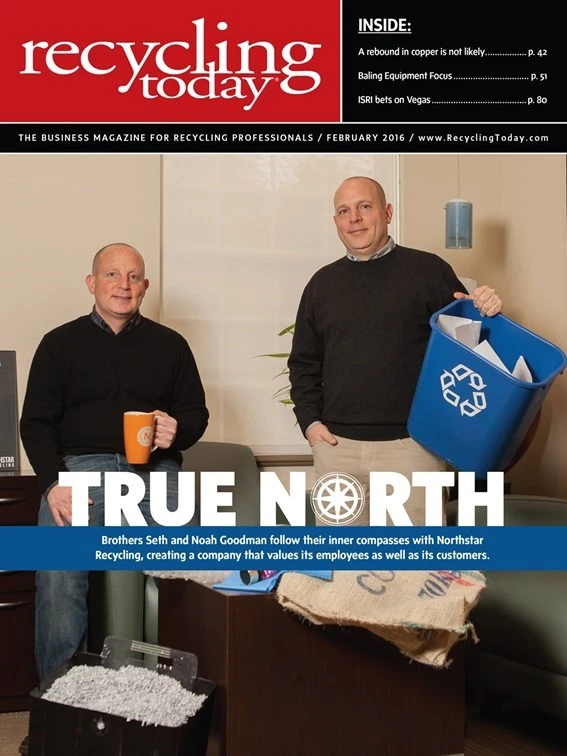
Explore the February 2016 Issue
Check out more from this issue and find your next story to read.
Latest from Recycling Today
- Enfinite forms Hazardous & Specialty Waste Management Council
- Combined DRS, EPR legislation introduced in Rhode Island
- Eureka Recycling starts up newly upgraded MRF
- Reconomy Close the Gap campaign highlights need for circularity
- Nickel carbonate added to Aqua Metals’ portfolio
- EuRIC, FEAD say End-Of-Life Vehicle Regulation presents opportunity for recyclers
- Recyclers likely to feel effects of US-China trade war
- BCMRC 2025 session preview: Navigating battery recycling legislation and regulations