21st Century Programming Releases Spanish Version of ROM
21st Century Programming, based in Long Beach, Calif., has announced the release of a Spanish language version of its Recycling Operations Manager (ROM) software.
ROM Recycler Spanish edition has been designed for use interchangeably in English and Spanish.
“Language barriers are a huge issue in the recycling industry,” says George Kane, co-founder of 21st Century Programming. “Virtually every day we hear from customers and potential customers concerned about their workforce being able to utilize computer technology because of the language barrier caused by a Spanish speaking workforce interfacing with English software,” he comments.
The new version of ROM has been designed to address such scenarios, the company says. “A scale operator can view all of his or her screens in Spanish, while at the same time a management user can run reports and do data analysis on the system and a trader can be trading on the system in English,” says programming director David Kane, also a co-founder of the company. “We’ve designed the software so that it can run entirely in Spanish, entirely in English or mix the two to meet specific operational needs,” he adds.
ROM software has been designed to meet the needs of large, medium and small recycling operations, according to the company. 21st Century Programming describes ROM as “a fully integrated system that streamlines operational, accounting, trading, scrap purchase reporting and many other features.”
More information on 21st Century Programming and its ROM software can be found at www.21stCenturyProgramming.com.
Sennebogen LLC Hosts Open House
Sennebogen LLC hosted an open house March 11 at its new North American headquarters in Stanley, N.C. The company also used the event to commemorate its 10-year anniversary. The event was designed to showcase the company’s new parts warehouse and technical training center.
Guests included Sennebogen customers, dealers and local dignitaries.
In addressing the group, Erich Sennebogen Jr., managing director of parent company Sennebogen Maschinenfabrik GmbH of Straubing, Germany, said the company had purchased some 33 acres to be able to accommodate anticipated future growth.
“Our original manufacturing facility in Straubing became landlocked by adjacent development, which prevented expansion. We want to ensure we are not in that position in the future and, therefore, when we planned this facility, we purchased enough land to accommodate future growth,” Sennebogen said.
He and Sennebogen LLC President Constantino Lannes also shared the history of the company’s development in North America and its focus on providing machinery built with Sennebogen quality but outfitted for the American market.
Sennebogen is a multi-national company with manufacturing plants in Straubing and Wackersdorf, Germany, and in Balatonfüred, Hungary. The firm has subsidiaries in the United States and in Dubai, United Arab Emirates.
Colorado Recycler Installs Auto Shredder from Metso Texas Shredder
American Iron & Metal Co. Inc. has selected a Metso Texas Shredder TSH100 model for installation at its newest location in Belen, N.M.
According to a news release from Metso Texas Shredder, the 100x116 shredding system will include an infeed conveyor, downstream equipment and controls from Metso Texas Shredder and SGM Magnetics Corp. The power source will be a 5,000-horsepower, DC shredder drive system from Quad Plus of Joliet, Ill.
The new shredding plant will have a capacity of 250 tons per hour and is expected to be operational by early fall of 2010, according to Metso Texas Shredder.
American Iron & Metal, based in Pueblo, Colo., currently operates shredding and recovery plants in that city and in Colorado Springs.
“Our decision to go with Texas Shredder was based on over a decade of exceptional service and support that Texas Shredder has provided us in the shredding field,” says Jim Warren, owner of American Iron & Metal. “We also believe that Metso’s new TSH series is the future for shredding plants,” he adds.
More information on San Antonio-based Metso Texas Shredder can be found at www.metso.com/texasshredder.
Eriez Announces Lift Magnet Refurbishment Program
Eriez, a separation systems manufacturer based in Erie, Pa., has introduced its Lift Magnet Certification and Refurbishment Program through its five-star service center.
“If you need new magnets [or] need to have your current magnets repaired, certified or completely rebuilt, Eriez has a solution for you,” says Dave Hansen, customer service manager for the company.
“Eriez’ lift magnets are built in compliance with ASME (American Society of Mechanical Engineering) B30.20 standards,” Hansen adds. “Through our inspection program, we check your magnets to ensure they remain in compliance.”
According to the company, Eriez’ refurbishment procedure includes inspection of the lift magnet surface and resurfacing of poles (if needed), inspection of all other parts, replacement of any missing parts, repair/replacement of all damaged parts, replacement of warning labels and capacity markings and load testing and certification.
Every magnet repaired by Eriez is returned with a “certificate of compliance” guaranteeing that the repairs and the load test of the serviced magnet comply with ASME B30.20, according to the company.
Additionally, Eriez certified repairs come with a one-year “As New” warranty. Also, customers can receive 20 percent off their first certification, according to the company.
More information on the Eriez Lift Magnet Certification and Refurbishment Program is available at http://service.eriez.com.
U.S. Shredder Unveils New Shredder Model
U.S. Shredder, Trussville, Ala., will unveil its latest shredder model at the Institute of Scrap Recycling Industries Inc. (ISRI) 2010 Annual Convention in San Diego this coming May.
According to the company, “The [new] shredder was designed specifically to compete with 60/85 models in regard to price and production, but that is where the comparison ends.”
According to U.S. Shredder, “The rotor provides up to 30 percent more hammer impact and [is] 12 percent wider [and] provides advantages in the thickness of scrap that can be shred; the efficiency of the motor; and the longevity of the shredder itself.”
Company president Bill Tigner says, “The strength and durability of our rotor will eliminate many of the maintenance and service issues associated with smaller, lighter shredders.”
He continues, “Our new shredder will give operators advantages they have not had to date. The gap between the 60/85 and 80/104 models no longer exists.”
Tigner says U.S. Shredder engineers worked closely with the company’s fabrication team “to build a bigger, heavier shredder with a design that allows the shredder to be built at the cost of the lighter competitive models.”
The shredder will typically be offered with a DC 2,300-horsepower drive system but can be provided with larger systems. U.S. Shredder says it also provides “state-of-the-art controls, hydraulics and long-lasting castings” with its shredders and has the option of adding an “efficient, cost-effective downstream” system.
More information is available by phoning (205) 999-7670.
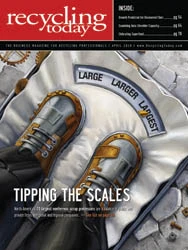
Explore the April 2010 Issue
Check out more from this issue and find your next story to read.
Latest from Recycling Today
- Freepoint Eco-Systems receives $50M loan for plastics recycling facility
- PET thermoform recycling the focus of new NAPCOR white paper
- Steel Dynamics cites favorable conditions in Q1
- Hydro starts up construction in Spain
- Green Cubes unveils forklift battery line
- Rebar association points to trade turmoil
- LumiCup offers single-use plastic alternative
- European project yields recycled-content ABS