Javelin moves to larger facility
Javelin Manufacturing, headquartered in Fort Wayne, Indiana, has moved to a new, larger facility in that city designed to allow the company to provide recyclers with a wider range of equipment beyond its original eddy current separators.
“We understand the challenges material recovery facilities and e-scrap recyclers face,” says Jason Miller, Javelin vice president of engineering.
“For years, we have produced the strongest eddy current magnets in the industry,” he continues. “Our new products are manufactured with the same top quality expected.”
In addition to manufacturing eddy current separators, Javelin now offers ultra-high-gauss holding magnets, suspended magnets, magnetic head pulleys and mobile units. The company says it can customize solutions, build onto existing systems and offer specialized service packages.
Javelin Manufacturing began producing eddy current separators in 2010.
Eriez offers expanded testing services

Eriez, Erie, Pennsylvania, a company that designs, develops, manufactures and markets magnetic separation, metal detection and materials feeding, screening, conveying and controlling equipment, now offers expanded lab-scale testing services for recycling companies. Eriez’s testing is performed at the company’s Central Test Lab in Erie.
Common recycling tests involve recovering copper wire/fine zorba from auto shredder residue (ASR) fines, separating minus-2-inch zorba into twitch and zebra and recovering fine aluminum and copper from wire chop and stainless steel recovery from fine zurik packages.
“After processing customers’ materials on the recycling equipment, we can determine recovery rates and make judgments on material grade,” says Chris Ramsdell, Eriez recycling equipment product manager. “With these recovery and grade figures, we can often help the customer determine equipment payback periods to support their investment.”
Eriez also can map out potential process flows, mix and match equipment and determine recovery rates based on a machine’s location in a process flow.
CieTrade launches cloud software for paper brokers, scrap traders

The software company cieTrade Systems, Stamford, Connecticut, has introduced a new business-to-business cloud software solution for small-to-medium-sized recycling enterprises called CieTrade.net. The new service offers an alternative to costly desktop hardware, giving users the flexibility to work from anywhere and to increase productivity by avoiding clunky spreadsheets and tedious workarounds.
“Studies have shown that the overall cost of cloud software is 55 percent less than comparable on-premise applications. CieTrade.net was developed as a cost-effective way to help commodity traders by offering a specialized solution that meets the dynamic demands of their industry,” says David Haber, CEO at cieTrade Systems. “CieTrade.net is designed around a ‘buy/sell’ ticket concept with the sales and cost components of each shipment on a single form, with projected margins, making it exceptionally intuitive.”
The new platform includes a number of key features for scrap and paper stock traders, such as built-in tools for logistics tracking, automated shipping and billing documentation, email integration with customizable message templates and support for attaching third-party documents and photos with each shipment. Haber claims the most valuable benefit is the gross profit reports, critical for effective decision-making and managing the contribution of sales reps for commissions. It also offers real-time accounting integration to eliminate double-entry.
Pricing for CieTrade.net starts at $375 per month for a three-user license.
To learn more about the cloud software, or to register for a free trial, visit http://cieTrade.net.
J.P. Mascaro & Sons selects Van Dyk Recycling Solutions

Audubon, Pennsylvania-based J.P. Mascaro & Sons, a family-owned waste service company with facilities across eastern Pennsylvania and New Jersey, has opened the doors to its first single-stream recycling facility. Located in Birdsboro, Pennsylvania, the facility is called TotalRecycle Inc. and is operated by the third generation of the Mascaro family. The 75,000-square-foot facility services waste haulers, municipalities, residents and businesses and operates at 35 tons per hour.
The facility contains the latest technology provided by Van Dyk Recycling Solutions of Stamford, Connecticut. Two Lubo screens first separate OCC (old corrugated containers) and glass, with the glass moving on to a Walair glass cleanup system that creates four fractions. Three additional Lubo screens separate fiber from containers, kicked off by Lubo’s new Anti-Wrapping ONP screen, a 12-foot-wide screen with 440 stars. The stars incur virtually no wrapping, even after hours of operation, according to Van Dyk. Cleaning and maintenance time are reduced to less than 10 percent of that of traditional star screens, the company adds.
A total of four Tomra (TITECH) Autosort 4s recover any remaining fiber and separate all plastics. A Bakker overbelt magnet and eddy current recover ferrous and aluminum cans, respectively. The system is capped off by a Bollegraaf HBC-120S single-ram baler that is capable of baling all commodities accepted at the facility, Van Dyk says.
A virtual tour of this facility is available at https://vdrs.com/videos.
Van Dyk Recycling Solutions is the exclusive distributor of Bollegraaf, Lubo and Tomra equipment throughout North America.
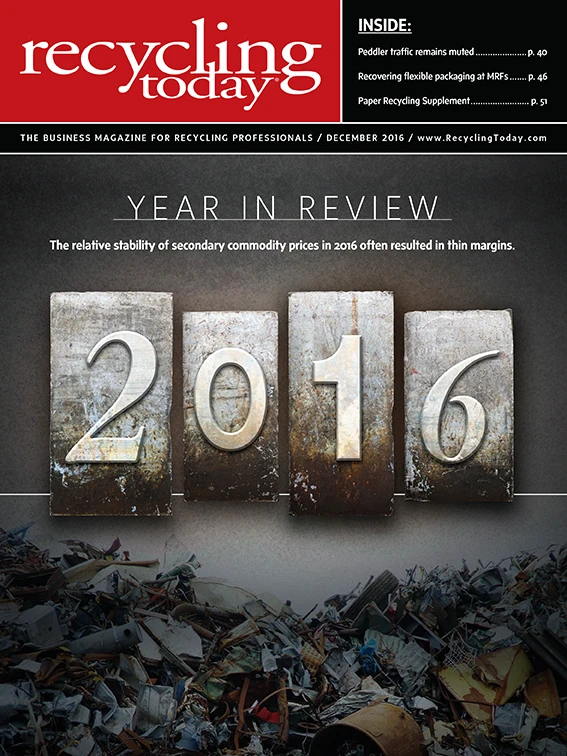
Explore the December 2016 Issue
Check out more from this issue and find your next story to read.
Latest from Recycling Today
- AF&PA report shows decrease in packaging paper shipments
- GreenMantra names new CEO
- Agilyx says Styrenyx technology reduces carbon footprint in styrene production
- SABIC’s Trucircle PE used for greenhouse roofing
- Hydro to add wire rod casthouse in Norway
- Hindalco to invest in copper, aluminum business in India
- Recycled steel price crosses $500 per ton threshold
- Smithers report looks at PCR plastic’s near-term prospects