
Eriez opens test center
Sorting equipment maker Eriez says it has boosted its ability to offer materials sorting testing services for the recycling industry at its Central Test Lab (CTL). The CTL is located at the company’s Wager Road plant in Erie, Pennsylvania.
Eriez says the majority of test work for recycling applications focuses on magnetic separation of ferrous and nonferrous materials. Test equipment used most frequently by recycling industry customers includes eddy current separators, magnetic drum separators, suspended permanent magnets and electrostatic separators.
The company says test procedures can be customized for each customer and can involve materials such as zorba, twitch, zebra, zurik and other mixed shredded metals, plus auto shredder residue fines, wire choppings and polyethylene terephthalate flake contaminated with aluminum.
“After processing customers’ materials on the recycling equipment, we can determine recovery rates and make judgments on material grade,” says Chris Ramsdell, a recycling product manager with Eriez. “With these recovery and grade figures, we can often help the customer determine equipment payback periods to support their investment,” he adds.
After lab testing, the company says it can map out potential process flows, mix and match different pieces of equipment and determine recovery rates based on where a particular piece of equipment will be located in a process flow.
“Our experience has shown we can provide reliable and accurate predictions for plant-scale results based on our lab-scale tests,” Ramsdell says.
AMCS Group updates software platform for waste, recycling industry
AMCS Group, Limerick, Ireland, has updated its AMCS Platform for the waste and recycling industry. According to a news release from the company, this marks the second upgrade to its platform so far this year.
In February, the AMCS Platform 8.2’s launch focused on companies gaining efficiencies. The company’s latest release, AMCS Platform 8.3, is designed to make companies work more quickly with more automation and enhanced integration capabilities, according to AMCS Group.
AMCS Platform 8.3 provides users with a number of updated features, according to the company:
- a new reporting and analytics work center;
- a process optimized and redesigned contract management and pricing engine; and
- a transformed materials management work center with redesigned and optimized inventory management, production shifts and material sales capabilities.
As well, the new REST API feature provides businesses with secure and reliable integration services of processes and data between on-premise, cloud and third-party applications within the AMCS Platform, the company says.
“AMCS Platform guarantees waste, recycling and resource companies a strong foothold to proactively anticipate future development,” says Elaine Treacy, global product director at AMCS. “With the integrated solutions, AMCS Platform is contributing to the key value drivers of our customers and the industry, which are around increasing revenue growth, margin expansion, operational efficiency and sustainability while at the same time reducing costs.”
She adds, “For instance, brand new in the AMCS Platform 8.3 are the self-service reporting capabilities, the AMCS Datamart and AMCS Platform Connectivity, providing greater insight into businesses as well as delivering connectivity and integrations based on industry standards. The new release demonstrates that the platform is built for change and innovation to increase the competitive edge of waste and recycling companies.”
AMCS Group says its AMCS Platform offers fully integrated and software-as-a-service-based end-to-end solutions to manage all operations, including municipalities, commercial and industrial, construction and demolition and recyclable commodities.
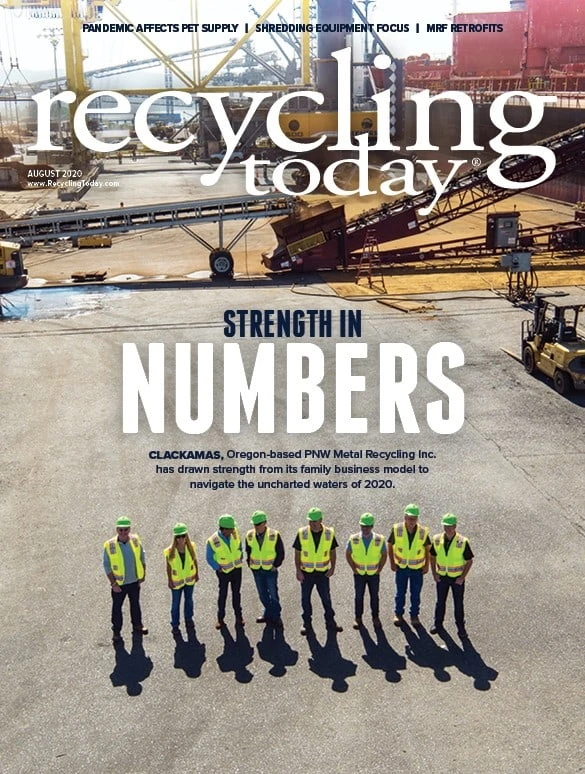
Explore the August 2020 Issue
Check out more from this issue and find your next story to read.
Latest from Recycling Today
- ReMA opposes European efforts seeking export restrictions for recyclables
- Fresh Perspective: Raj Bagaria
- Saica announces plans for second US site
- Update: Novelis produces first aluminum coil made fully from recycled end-of-life automotive scrap
- Aimplas doubles online course offerings
- Radius to be acquired by Toyota subsidiary
- Algoma EAF to start in April
- Erema sees strong demand for high-volume PET systems