
Sennebogen invests in new service center
Sennebogen, based in Straubing, Germany, has announced it is building a new customer service center in Bavaria, Germany.
The $28 million center, set to be completed by the end of 2020, will feature two office buildings, service halls and a spare parts warehouse built on nearly 940,000 square feet of land, the company says.
The spare parts warehouse will have space to store 5,300 pallets and 37,400 small parts containers, Sennebogen says, and will feature technology designed to optimize logistics.
Sennebogen says spare parts sales, customer service and rentals from Sennebogen Vertriebs GmbH & Co. KG will be offered at the new service center. Its location at the intersection of two major highways also provides ease of accessibility for rented and used machines.
The new space will free up areas in Sennebogen’s other nearby locations, the company says, and will be used to expand production.
Sennebogen says building the center will generate about 50 new jobs in the region. About 100 employees will move from Sennebogen’s nearby locations to staff the new one.
LBX opens Customer Experience Center
LBX Co. LLC, Lexington, Kentucky, hosted a grand opening for its new Customer Experience Center June 13. The facility is on 25 acres in Citation Business Park on Remington Way in Lexington. Company officials say the operation accommodates customer experience programs, including dealer training and product demonstrations, in addition to community events.
“Today marks the culmination of a vision that started several years ago,” says Eric Sauvage, president and CEO of LBX, “a vision to better support our dealers, our customers, our employees and our community with our state-of-the-art 23,000-square-foot LBX Customer Experience Center. We are all very excited and already have a full calendar for the 2019 usage of our new facility with product and service training, customer demonstration days, clinic tests and philanthropy events.”
Lexington Mayor Linda Gorton, State Sen. Ralph Alvarado, State Rep. George Brown Jr. and area business leaders attended the grand opening, LBX says. Bob Quick, president and CEO of Commerce Lexington, emceed the event.
LBX makes Link-Belt hydraulic excavators, scrap handlers, demolition equipment and forestry equipment.

ZWS opens new recycling facility
Zero Waste Solutions LLC (ZWS), Rochester, Massachusetts, has opened a 103,000-square-foot recycling facility that will accept residential and commercial waste streams as well as single-stream and source-separated recyclables.
New Bedford, Massachusetts-based ABC Disposal Service Inc. and New Bedford Waste Services LLC are sister companies to ZWS.
ZWS says it worked with San Diego-based CP Group to equip the facility with the latest sorting technologies to recover recyclables, allowing the facility to produce sought-after commodities.
“We are very pleased to announce that after a very long process, our Zero Waste Solutions recycling plant is now opened and processing materials into salable commodities,” ZWS President and CEO Michael Camara says.
The new ZWS recycling facility has been equipped with a variety of new recovery technologies, including screening systems, magnets, eddy currents to target aluminum and optical sorting systems, that are designed to automatically separate incoming recyclables into a variety of commodity categories.
“Combining the capabilities of our network of transfer stations and vast hauling operations as well as ZWS’ advanced recycling technologies, we will be able to develop extremely efficient recycling operations,” Camara says. “These advanced recycling technologies will allow us to improve our ability to process a larger percentage of materials, which can then be recycled, reused and diverted from disposal. We have installed the most technologically advanced separation equipment available to achieve the highest recycling rates.
“We are very proud opening one of the most technically advanced recycling facilities in the world and a great asset for Massachusetts,” Camara concludes.
Sweed Turbo Mill recovers copper from low-yield wire
Sweed, Gold Hill, Oregon, has released the Turbo Mill to help nonferrous scrap processors separate copper wire from the plastic surrounding it.
According to a news release from Sweed, the company noticed an increasing number of inquiries about low-yield copper wire. Sweed says it decided to design and manufacture a machine that could address the gap its customers were experiencing. The new design, which is sturdier, allows operators to further adjust the process.
The Turbo Mill beats the material around, tumbling it over to pulverize any remaining insulation, Sweed reports. The friction rips the plastic away from the copper wire, which is turned into tiny pellet-like pieces. In this shape, the balled copper flows freely like fine sand, allowing it to separate easily from the plastic; straight fine wire will nest and entrap plastic, making it difficult to separate effectively.

“Our Turbo Mill effectively and efficiently processes No. 2 copper wire and other fine wire, making it easier to separate,” says Chris Salyer, engineering director at Sweed. “Before it hit the market, the primary source for customers in the United States for a turbo mill was through international manufacturers.”
Also, Sweed’s Turbo Mill provides benefits in the copper liberation process. “Because it makes the balled copper easier to separate from the plastic, the Turbo Mill increases copper recovery,” Salyer says.
The recovered copper also has increased purity because the process that removes it from the plastic ensures that the two materials are completely separated.
“It increases your processing capability,” Salyer says of the machine. “Without a Turbo Mill, in our entry-level chopping line, someone might use an eighth-inch screen, which allows for 1,500 to 2,000 pounds of processing per hour. With a Turbo Mill, you can use a larger 3/16-inch or ¼-inch screen, which more than doubles your throughput and lets you process 4,000 to 5,000 pounds of material every hour.”
The line ranges from 40 horsepower to 150 horsepower and can integrate into any existing system, Sweed says.

Continental renames urban waste transport tires
Continental, a South Carolina-based automotive supplier and tire manufacturer, has renamed its commercial waste transport tires and retreads to provide clarity. The new nomenclature is descriptive and easy to use, ensuring tire dealers and fleets can pinpoint a tire’s application and usage at a glance, the company says in a news release.
The new name spells out the vehicle classification, axle configuration and application for which the tire was designed. For instance, the Conti HAU 3 WT is a heavy truck tire designed for all-position use in urban applications for waste transport. It is available as a new tire in 315/80R22.5 load range and as a retread in 210-to-280-millimeter widths.
The four-rib tread pattern with zigzag grooves resists high scrub, and the extra sidewall protection delivers resistance to curbs and cuts, Continental says. Its tread compound provides mileage and heat reduction, while the bead design offers durability and resistance to brake heat. The tire was available under the new name in May.
The ContiTread HDU 3 WT is a heavy truck pattern designed for drive axle use in urban applications for waste transport. It is available as a retread in 210-to-280-millimeter widths. The variety of widths ensures the retread can accurately fit all major casing sizes available on the market.
The 32/32-inch tread depth and open-shoulder tread design offer traction, while notches prevent heat buildup, Continental says. It is anticipated to be available under the new name starting in August.
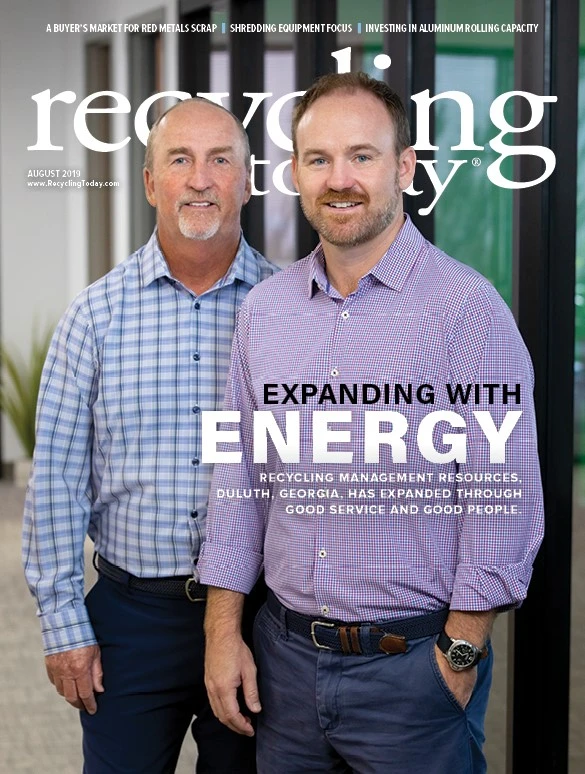
Explore the August 2019 Issue
Check out more from this issue and find your next story to read.
Latest from Recycling Today
- Nucor receives West Virginia funding assist
- Ferrous market ends 2024 in familiar rut
- Aqua Metals secures $1.5M loan, reports operational strides
- AF&PA urges veto of NY bill
- Aluminum Association includes recycling among 2025 policy priorities
- AISI applauds waterways spending bill
- Lux Research questions hydrogen’s transportation role
- Sonoco selling thermoformed, flexible packaging business to Toppan for $1.8B