Caglia Environmental expands use of robots, AI to PET recovery

Using funding from The Recycling Partnership’s PET Recycling Coalition, Caglia Environmental, a recycling company based in Fresno, California, has installed an artificial intelligence- (AI-) guided robot from EverestLabs to sort polyethylene terephthalate (PET).
Caglia Environmental was one of 12 businesses and organizations in North America to receive a PET Recycling Coalition grant.
With the grant, Caglia installed RecycleOS-powered robotic sorters developed by EverestLabs, Fremont, California, at its Cedar Avenue Recycling and Transfer Station (CARTS) material recovery facility (MRF) that can identify and sort PET into three streams—bottles, thermoforms and pigmented/opaque—placing them into three separate bunkers.
“The Recycling Partnership is excited to work with CARTS as they implement a bold and replicable new system for PET recycling,” says Adam Gendell, director of Material Advancement at The Recycling Partnership, headquartered in Washington. “Being at the forefront of separating PET into specialized streams is a proactive leap towards the bigger and broader recycling landscape that extended producer responsibility (EPR) will bring to California and the industry.”
Caglia Environmental says its ability to sort clear PET bottles, thermoforms and pigmented/opaque PET into separate streams significantly will improve the recycling process and output quality. This retrofit represents the first time a MRF has consistently targeted each of these three product types as separate commodities, according to a news release about the installation, and will serve as a benchmark for MRFs seeking to do this type of targeted sorting in the future.
Caglia previously installed EverestLabs’ technology to help recover aluminum cans. That installation was funded through a financing model developed by the Can Manufacturers Institute (CMI), Washington.
“Our family has been dedicated to providing waste and recycling services to the Fresno community for over 80 years,” says Richard Caglia, owner of Caglia Environmental. “This advancement in our facility represents not just a technological leap but a continuation of our longstanding commitment to environmental responsibility and community service. We are proud to set a new standard for recycling in the region and hope to inspire others to follow this path.”
CMI provided financing for a two-year lease on a robot that was placed on the last-chance line at the CARTS MRF with funding from Ardagh Metal Packaging and Crown Holdings. In return, Caglia agreed to share 50 percent of the revenue generated from the used beverage cans (UBCs) collected by the robot. Caglia estimates, based on previous analyses, that EverestLabs’ robot could capture 32,000 pounds of UBCs per year that otherwise would have gone to landfill.
“EverestLabs is delighted to extend our partnership with Caglia Environmental to increase PET recovery under The Recycling Partnership’s grant from their PET Recycling Coalition,” EverestLabs founder and CEO JD Ambati says. “The Caglia team saw right away that RecycleOS-powered robotics and data dramatically improved their bottom line on their last-chance line. This overwhelmingly positive experience has led to the expansion of robots on their PET line. We are excited to work with Caglia’s forward-thinking leadership on AI and robotics solutions that drive their recovery and revenue growth while addressing labor challenges.”
Buddy launches B2B scrap metal marketplace

New Zealand-based scrap metal trading platform Buddy has launched a marketplace for business-to-business (B2B) metal recycling that connects buyers directly with sellers.
“Most trades are currently conducted using disparate systems and manual processes, creating errors, wasted resources and a myriad of business risks for recyclers,” Buddy co-founder Stuart Kagan says. “What’s more, most marketplaces out there are ‘managed.’ They anonymize both sides of the transaction, buying for as low as possible and selling for as high as possible. This doesn’t create a pathway for sellers and buyers to build relationships with their counterparties.”
Buddy claims it is the first platform for scrap recyclers, by scrap recyclers and aims to support the metal recycling market’s transition from manual to digital procurement processes. It matches sellers with appropriate buyers and ensures users are vetted.
Buddy says buyers across 19 different countries have registered, including those in South Korea, China, India, Vietnam, Dubai and Germany.
The app launches in North America, Australia and New Zealand this month. Buddy is exhibiting at the Institute of Scrap Recycling Industries Convention and Exposition in Las Vegas this month and at the Bureau of International Recycling World Recycling Convention and Exhibition planned for Copenhagen, Denmark, in May.
Providing members with access to structured data, Buddy says it enables real-time analysis with its customizable dashboard and allows recyclers to use parameters including pricing, shipping costs and ratings and reviews to access the viability of each trade.
Buddy has partnered with global integration partners for freight, foreign exchange, trade finance and market data and was built in partnership with Australia-based venture studio Paloma.
The app supports trades on any incoterms and payment terms and supports negotiation between counterparties.

Danieli releases new line of shears
Italy-based Danieli has released a new line of incline shears. The company says the line was created to help steel mills produce metals for recycling to meet their melt shop requirements.
The DIS inclined scrap shear is a gravity feed shear that can yield more than 330 cutting cycles per hour and features hydraulic engineering.
According to Danieli, the DIS line can deliver dense scrap through its heavy-duty, side-squeeze block and serrated design, applying four to five times the compression force of horizontal shears. Danieli says the shears’ cutting length control mechanism, or sizing door, solves problems associated with poor cutting length control and overflowing scrap.
The quick-blade-change system allows operators to take out one set of blades while still in their blade seat, something Danieli compares with a modern shaving razor. A new seated blade set can be slid into place using the hydraulic blade-changing system, which the company says keeps technicians away from the shear throat while avoiding the heavy lifting associated with blade changes. The main cylinder is oversized and contains a coating on the rod, seals and bushings.
The DIS series shear is available with either 2,000 or 1,600 tons of cutting force and is best suited for facilities not requiring the production of bundles and bales, the company says.
Get curated news on YOUR industry.
Enter your email to receive our newsletters.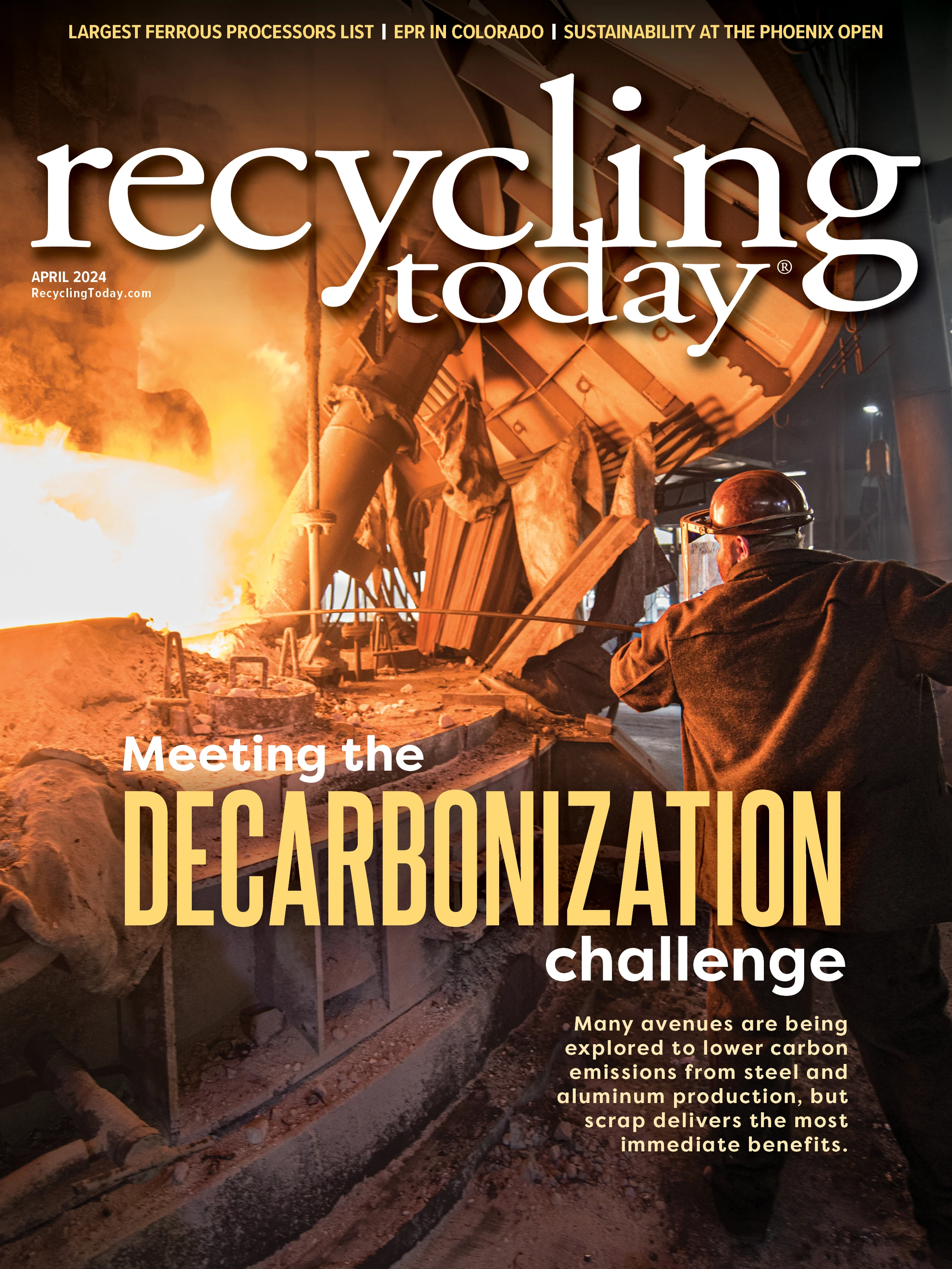
Explore the April 2024 Issue
Check out more from this issue and find your next story to read.
Latest from Recycling Today
- Athens Services terminates contract with San Marino, California
- Partners develop specialty response vehicles for LIB fires
- Sonoco cites OCC shortage for price hike in Europe
- British Steel mill’s future up in the air
- Tomra applies GAINnext AI technology to upgrade wrought aluminum scrap
- Redwood Materials partners with Isuzu Commercial Truck
- The push for more supply
- ReMA PSI Chapter adds 7 members