CieTrade Systems adds features to its cloud-based software
CieTrade Systems Inc., a Stamford, Connecticut-based provider of business software for paper stock brokers, scrap dealers and recyclers, has added three new features to its cloud-based software, cieTrade.net: inventory control, material processing and bar coding scanning.
The company says its inventory module offers a solution for commodities such as paper stock rolls/sheets or recycled material, giving users the ability to track material, either in bulk lots or as individual items, with each product having its own weight and attributes.
CieTrade.net uses a landed cost valuation for accurate gross profit reporting, provides traceability for quality assurance and claims handling and calculates commissions, the company says.
The converting module includes bar code scanning and yield loss tracking and capitalizes production costs into a firm’s output stock or finished goods. It also applies warehouse storage charges or other costs to inventory.
Udom Motayasiri, vice president of cieTrade, says the original goal of cieTrade.net was to help brokers and exporters control margins and improve business insight. “We did this with a unique design that intuitively matches purchases and expenses directly with commodity sales, so that brokers can easily see their actual costs, sales and margins. Now, with our new inventory module, we’ve extended this vital capability beyond trading by providing landed cost valuations, cost allocation tools and the ability to track individual inventory items, which are critical capabilities that are often missing from other cloud inventory solutions.”
Wieland Copper Products installs Metso Lindemann EtaPress III baler
Pine Hall, North Carolina-based Wieland Copper has installed a new Lindemann EtaPress III 33 -1250 baler for processing copper scrap generated by its operations. The company manufactures semifinished products used in the plumbing, industrial and technical tube industries.
Nathan Garret, Wieland Copper project engineer, describes the EtaPress III baler as a high-quality, high-production, energy-efficient machine.
“Working with Metso sales was a great experience,” he says. “They helped us find a baler solution that satisfied our production and technical requirements that also fit within our budget.
“Also, the spare parts availability and technical support in the U.S. was a major plus,” Garret adds.
Metso provides equipment, systems and services for the fragmentation, compaction and separation of metal scrap. Through brands that include Lindemann and Texas Shredder, Metso has been a part of the metal recycling industry for more than a century.
More information on Finland-based Metso’s solutions for metals recycling is available at www.metso.com/metal-recycling.
Schnitzer Steel rents to purchase Lefort towable shear/baler/logger
Schnitzer Steel, headquartered in Portland, Oregon, has rented to purchase a .SB 660A towable shear/baler/logger from Lefort America.
The .SB 660A towable is part of Lefort America’s newest product line covering the scrap metal recycling market. Schnitzer will use the machine at its multiple locations in Puerto Rico.
Lefort America, the U.S. subsidiary of Belgium-based Lefort, is based in West Palm Beach, Florida.
_fmt.png)
Schnitzer Steel chose the machine for its mobility and high-production capabilities, which will improve operations at the company’s yards in Salinas, Bayamon and Ponce, Puerto Rico, according to a news release issued by Lefort.
Lefort America’s recent partnership with Caterpillar Inc. facilitated the commissioning by extending help through its local Puerto Rico dealer, Rimco CAT, San Juan, Puerto Rico.
Two Lefort America technicians were present during commissioning of the towable shear/baler/logger. They trained Schnitzer operators on proper machine use and maintenance.
Lefort quotes one of the technicians present at the installation that took place Feb. 1, 2017, as saying, “This machine is unlike anything we’ve ever seen before. The computer and sensor systems are the best out there.”
“The versatility and how well this machine can process materials really makes this equipment stand out,” says Angel Aponte, field supervisor for heavy equipment with Rimco CAT.
Partnering with Caterpillar, Lefort parts and products are distributed and serviced by most Caterpillar dealers in the U.S. and Canada. Rental options are available, as is financing through CAT Financial, subject to approval.
More information about Lefort equipment is available from the Lefort America website at www.lefortamerica.com.
Ely Enterprises becomes Harris dealer
Ely Enterprises Inc., Lorain, Ohio, has announced it has been appointed by Cordele, Georgia-based Harris to be its distributor in Ohio, western New York, western Pennsylvania, southern Michigan and northern Kentucky. Ely Enterprises offers the Harris/IPS line of equipment, factory parts and service.
Previously a Harris dealer for 18 years, Ely Enterprises President and founder Ken Ely Jr. says he is excited to re-establish the company’s relationship with Harris. “We are very pleased to be rejoining the Harris team after more than a decade of separation,” he says. “The change in leadership and culture within Harris is both refreshing and exciting.”
Ely Enterprises can be reached at sales@elyent.com or at 216-252-8090.
US Shredder and Castings Group to market Fire Rover systems

The U.S. Shredder and Castings Group, Miramar, Florida, has entered into an agreement with Southfield, Michigan-based Fire Rover to market its proactive fire suppression system to the North American scrap industry.
U.S. Shredder President Bill Tigner says, “We had a very good customer that we were doing a turnkey installation for on a nonferrous plant after a catastrophic fire. We knew of the Fire Rover because one of our other nonferrous plant customers had installed the system, and it had recently extinguished a fire at their plant. We immediately contacted Fire Rover to see if a joint marketing effort made sense for both of us. We now offer the Fire Rover to the entire North American scrap industry. In our opinion, if anyone has ASR (auto shredder residue), the Fire Rover is a small investment. We offer it as an option on every nonferrous plant or upgrade we install.”
An on-site consultation or live demonstration can be scheduled by contacting U.S. Shredder through the company‘s website at http://usshredder.com/contact.
The U.S. Shredder and Castings Group offers scrap shredders, control systems, downstream systems, nonferrous recovery and air systems, as well as shredder castings, service, engineering, construction and installation to the worldwide scrap industry.
OnTerra Systems introduces multiroute features for RouteSavvy software
OnTerra Systems, Denver, a software developer, has introduced new features to its RouteSavvy route planner software package. The new features are designed to streamline the process of optimizing routes for multiple vehicles.
Sponsored Content
Labor that Works
With 25 years of experience, Leadpoint delivers cost-effective workforce solutions tailored to your needs. We handle the recruiting, hiring, training, and onboarding to deliver stable, productive, and safety-focused teams. Our commitment to safety and quality ensures peace of mind with a reliable workforce that helps you achieve your goals.

OnTerra Systems says its “cluster into new folders” function allows fleet managers to take a folder of planned locations and automatically organize the locations into smaller geographic groups. This allows the user to plan stops in the same area, optimizing for the most efficient route and minimizing drive time and distance, saving costs associated with time, labor and fuel.
A second feature of the software is “multiple routes,” which allows users to create, store and visualize multiple routes, each depicted in a different color, on the same map. By using different colors, fleet and operations managers can visually review multiple routes, identify locations that could be more efficiently grouped into another route and re-assign specific stops to a more appropriate route to increase efficiency.
The third enhancement is a “change stop order” feature, which allows users to move a stop from one position to another without using up/down arrows. According to OnTerra, the feature is useful for managing larger routes.
All three of these new functions offered by RouteSavvy are designed to streamline the route-planning process for businesses and organizations with multiple vehicles, OnTerra says. RouteSavvy’s new multiroute functions are designed to streamline and speed up the process of planning and optimizing routes, saving time.
“The new multiroute functions are significant enhancements to RouteSavvy that will help our customers optimize routes more quickly and efficiently,” says Steve Milroy, OnTerra Systems’ president and founder. “In addition, these significant enhancements to the RouteSavvy route planner tool underscore our ongoing commitment to RouteSavvy and our customers’ success.”
Caterpillar moves global headquarters to Chicago area
Caterpillar Inc. has announced it will locate its global headquarters and a limited group of senior executives and support functions in the Chicago area later this year and has reaffirmed the ongoing importance of its presence in Peoria and central Illinois.
A limited number of senior executives will move into leased office space beginning in 2017. Once the new location is fully operational, Caterpillar says it expects about 300 employees to be based there, which includes some positions relocated from the Peoria area.
“Caterpillar’s board of directors has been discussing the benefits of a more accessible, strategic location for some time,” says Caterpillar CEO Jim Umpleby. “Since 2012, about two-thirds of Caterpillar’s sales and revenues have come from outside the United States. Locating our headquarters closer to a global transportation hub, such as Chicago, means we can meet with our global customers, dealers and employees more easily and frequently.
“We value our deep roots in central Illinois, and Peoria will continue to be our hometown. The vast majority of our people will remain in this important region, where we have many essential facilities and functions,” Umpleby continues. “The new location is also an opportunity to add to our talented team while improving the productivity of our senior leaders.”
As a result of continuing challenging market conditions and the need to prioritize resources to focus on growth, Caterpillar says it will not build the previously announced headquarters complex in Peoria. The current headquarters building will continue to be used for the company‘s offices.
Over the last five years, even while facing these challenging conditions, Caterpillar, along with its employees and retirees, has contributed more than $60 million to support thousands of families, organizations and programs across Central Illinois. The company will continue its philanthropic support and deep civic involvement in the Peoria area.
Peoria Mayor Jim Ardis says, “As mayor, I never want jobs moving out of the city. However, the overwhelming majority of Caterpillar employees and their families based in the Peoria area won’t be impacted by this decision. I’m pleased Caterpillar continues to call Peoria its hometown.”
Get curated news on YOUR industry.
Enter your email to receive our newsletters.
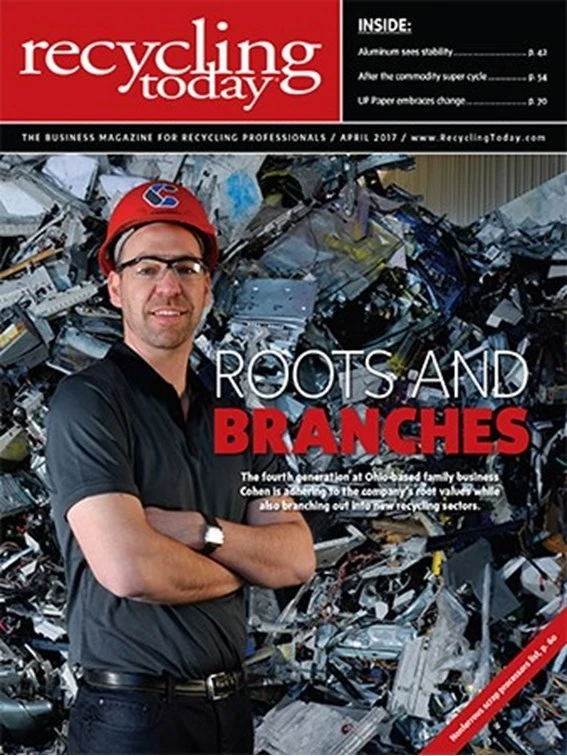
Explore the April 2017 Issue
Check out more from this issue and find your next story to read.
Latest from Recycling Today
- Toppoint Holdings expands chassis fleet
- Lego creates miniature tire recycling market
- Lux Research webinar examines chemical recycling timetables
- Plastics producer tracks pulse of wire recycling market
- Republic Services, Blue Polymers open Indianapolis recycling complex
- Altilium produces EV battery cells using recycled materials
- Brightmark enters subsidiaries of Indiana recycling facility into Chapter 11
- Freepoint Eco-Systems receives $50M loan for plastics recycling facility