Efactor3 to Serve Recycling, Waste-to-Energy Markets
Hartmut Bendfeldt, former president of Weima America, has formed Efactor3 in Charlotte, N.C.
The company has an exclusive agreement with Weima Maschinenbau GmbH, Ilsfeld, Germany, to market complex two- and three-stage systems for the recycling and waste-to-energy markets. Efactor3 also will offer pre-shredding and granulating equipment.
As a turnkey supplier, Efactor3 supplies conveying and separation equipment, systems integration and installation.
More information about the company is available by calling (704) 944-3232 or by visiting www.efactor3.com.
Karl W. Schmidt & Associates Expands Offerings
Karl W. Schmidt & Associates Inc. (KWS), Commerce City, Colo., has announced its cooperative agreement with Germany-based BRT GmbH. The agreement allows KWS to offer screening, bag opening, perforating and metering equipment to be integrated into its systems for the processing of single-stream, C&D, scrap wood and refuse dervived fuel (RDF) materials.
"This partnership with BRT and its screening and material processing equipment fills out the KWS offerings to best serve our markets," says Jeffrey Van Galder of KWS.
"KWS pioneered its automated sorting technologies (ASTEC) in the early ’80s," he continues. "Now, with the full range of modern cutting-edge sorting and size-reduction equipment and a flexible ‘can do’ customer interface, we believe we are bringing a new concept to market."
More information is available at www.karlschmidt.com.
Thermadyne Industries Introduces Victor Bulldog Torches
St. Louis-based Thermadyne Industries has introduced its Bulldog line of heavy-industry scrap torches under its brand name Victor.
Victor, a leader in gas equipment and pressure control products, offers a complete line of Bulldog torches for numerous scrapping needs. The torches are designed to serve the scrap, demolition and construction trades. The torch is lightweight, durable and designed for use with natural gas or propane, based on feedback from end users, the company says. Bulldog torches have high-flow capacities, yet are light in weight for continuous use.
"We wanted to build a torch that would meet the needs of the scrapping industry, which is a growing field and requires durable products," says Randy Niederer, marketing manager for Victor.
Eddie’s Welding Supply, Stafford, Texas, is Thermadyne’s largest distributor of Bulldog torches and a major supplier of equipment to the scrapping industry, the company says. Eddie’s Welding Supply has sold more than 350 torches in 2008 alone, the company adds.
"The Bulldog line of torches is the best scrap torch in the industry," says Eddie Grossman, owner of Eddie’s Welding Supply. "We have seen consistent growth month after month for these torches since we began offering them last year."
ATM Recyclingsystems Offers HSM Series Briquetting Presses
Austria-based ATM Recyclingsystems, a leader in metal sorting technology, offers a full range of HSM Series briquetting presses, with models ranging from half a metric ton to 7.5 metric tons in capacity.
The presses are offered with three different filling variants according to the free-flowing property of the material. An inclined feeder or a two-step feeder permit the presses to process both grinding sludge and drilling swarfs.
The press’s solid welded construction allows it to be used for heavy continuous operation, according to ATM Recyclingsystems. Each machine can be operated manually or automatically.
All presses have a graphic operator panel with visualization of all process sequences and can be integrated into fully automatic production lines. Remote maintenance and system adjustments can also be performed.
In the process of forming a briquette, up to 99 percent of the oil and water content is extruded, according to ATM Recyclingsystems. Lubricant oils that are extracted can be reused, quickening an operation’s return on investment.
More information about ATM Recyclingsystems’ HSM Series briquetting presses is available by calling (604) 935-4865 or by visiting www.atmrecyclingsystems.com.
Eriez Introduces Eddy Current Metal Separators
Eriez Magnetics, Erie, Pa., has introduced its newest eddy current metal separators. The separators are designed to remove nonferrous metallic particles from plastics, glass cullet, electronic scrap, automobile shredder residue (ASR), boiler bottom ash, spent foundry core sand, municipal solid waste (MSW), commingled recyclables, urban wood waste and mixed metals.
Eriez’ eddy current separators are available with Eriez’ vibratory pan feeder, Rare Earth magnetic drum and a belt conveyor for processing different infeed materials.
Eriez’ eddy current separators are designed with low-energy or eccentric weight drives and are available with feed widths of up to 60 inches.
More information is available at www.eriez.com.
Bollegraaf Expands Processing Capacity
Bollegraaf Recycling Machinery, Netherlands, has announced that it has provided the equipment and built the largest commingled material recovery facility (MRF) in the United Kingdom. The facility, built for Greenstar U.K., is in Aldridge, U.K., and has been operational since April.
The plant can reportedly process up to 250,000 metric tons of recyclables per year. Material to be handled includes both mixed and sorted recyclables, including all forms of paper and cardboard, plastic and glass bottles, steel and aluminum cans and wood.
The recycling system installed by Bollegraaf includes a starscreen system from, Lubo Systems, that are used instead of drum/rotorscreens.
Bollegraaf Recycling Machinery also has announced the mechanization and automation of its entire production process for sorting systems and balers in a new production hall in Appingedam, Netherlands. The company will use an automatic production process using plasma cutting machines and welding robots.
Northshore Manufacturing Expands Facilities
Northshore Manufacturing, a Two Harbors, Minn., manufacturer of attachments and other equipment for the scrap, recycling and waste management industries, has been approved for a low-interest loan of $500,000 by the Iron Range Resources Board.
The loan, added to financing the company has received from several other financial institutions, has allowed the company to invest between $3.5 to 4 million to expand its operations.
John Anderson, with Northshore, says the expansion project, slated to be completed by February 2009, will add around 50,000 square feet to the company’s operations, more than doubling its overall size.
Anderson notes that the expansion will allow Northshore Manufacturing to bring its operations under one roof, keeping manufacturing together while making the company 100 percent self sufficient.
The expansion project also will allow Northshore to have a separate facility for its attachments business.
Ohio Plant Produces First Lindemann Shear
The first Lindemann LIS Scrap Shear assembled in North America has been completed at Metso Minerals’ new facility in Brunswick, Ohio.
Tim Conway, a Metso Recycling vice president of sales and marketing, says two other LIS Scrap Shears are nearing completion, with one to be finished in December, and the other to be finished in the first quarter of 2009.
The new facility, near Metso Minerals’ existing engineering and manufacturing facility in Brunswick, has a total crane capacity of 80 tons and is expected to double the fabrication capacity of Metso Minerals’ Ohio operations.
The LIS can process up to 20 tons per hour, according to Metso, and is available in stationary or semi-mobile configurations.
Steco Introduces Scrapper Container Loader System
Steco, Enid, Okla., a division of Blue Tee Corp. that manufactures transfer and dump trailers, has introduced its Scrapper container loader.
The Steco Scrapper container loader is designed to safely and quickly load shipping containers to their maximum capacity, without causing damage to the containers’ walls or floors, according to the company.
The two-part system includes the transfer trailer base and the container packer/loading sleeve (CL unit). Scrap material is loaded into the CL unit and then transferred to the container.
The Steco Scrapper travels on its own transport trailer and requires no special setup at the job site. Since it is self-contained with its own diesel-powered unit to drive its hydraulics, it can be moved to wherever it is needed. The shipping container is placed directly behind the transfer-base trailer so its floor and the trailer floor are at the same height.
The Scrapper container loader comes with an integrated scale so the operator can monitor the load to match the maximum weight capacity of each container. Once the desired weight is reached, the operator then activates the controls to hydraulically insert the CL unit into the open side of the shipping container.
Another control pushes the contents out with a push-blade assembly that is built into the CL unit itself. The CL unit is backed out as the contents continue to empty. Since the materials are simply pushed sideways into the shipping container, the container itself sustains no impact damage, the company says.
Once the CL unit is empty, the operator retracts the push-blade assembly and then extracts the entire container packer unit back onto the transfer base trailer.
More information is available by calling (800) 627-8326.
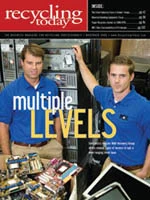
Explore the November 2008 Issue
Check out more from this issue and find your next story to read.
Latest from Recycling Today
- NWRA announces 2025 Driver of the Year, Operator of the Year winners
- The Scrap Show: Nanci Schuld of FE Trading Group LLC
- Call2Recycle Canada partners with RLG to advance battery collection
- Report delves into recovery opportunities for food-grade polypropylene
- Reimagining Supplier Payments in Metal Recycling: A Digital Leap Forward
- STEINERT Lithium Battery Detection and Removal from Waste Streams
- Driving the Future: Innovations in Waste & Recycling Technology
- Robin Wiener recognized for recycling leadership