
AMERICAN BALER INTROS NEW HYDRAULIC VALVE
American Baler, Bellevue, Ohio, has a new high-flow hydraulic logic valve available for its 20- and 30-hp balers.
According to the company, when used in conjunction with a manifold block and screw-in cartridge control valves, the new logic valve is designed to replace the existing subplate and directional spool valves.
The new unit contains fewer components and is designed to improve efficiency by providing enhanced flow characteristics and reducing heat generation. "While competitive high-flow logic valves contain bolted-on caps with up to seven seals that are prone to external leakage, American Baler reduces the external seals to one, greatly reducing potential leaks," the company says in a press release.
The new logic valve is available on new balers only and cannot be retrofitted to existing systems.
More information is available online at www.americanbaler.com.
REDESIGNED GRANUTECH LOGGER DEBUTS
Granutech-Saturn Systems, Grand Prairie, Texas, has re-introduced its MAC L3600 Logger with some major design enhancements, according to the company.
"If ever there was a time a scrap recycler could benefit from a logger, this is it," says Jack West, Granutech-Saturn’s executive vice president. "A logger’s benefits—the ability to create either logs or bales out of loose material that, left unprocessed, has little value—loom large in today’s market. The L3600 is designed to capitalize on that, while at the same time, eliminating some of the traditional shortcomings a logger can bring."
Designed to combine high production with low maintenance and ease of use, the L3600 provides operators with the ability to adjust throttle levels and bale density from inside the cab. With the flip of a switch the operator can select any of three different bale densities. Material handling and loading are assisted by a four-tine grapple-equipped boom offering 360-degree continuous rotation.
Powered by a 166-hp John Deere engine (rear mounted for easy maintenance access), the L3600’s baling chamber measures 70 inches wide by 90 inches deep by 192 inches long to keep production levels up. At 90 inches, the chamber is lower than many comparable designs to offer better operator visibility during processing, according to the company.
"For years, we’ve had customers who have been asking us to give them the same reliability and production in a logger to which they’ve become accustomed with their Big MAC flatteners," says West. "Redesigning and reintroducing the L3600 is our answer to them."
More information on Granutech’s L3600 is available at www.granutech.com.
RIVERSIDE ENGINEERING ANNOUNCES NEW BUSINESS STRUCTURE
Riverside Engineering Inc., San Antonio, Texas, has announced a new business structure that involves spinning off Riverside Products, Moline, Ill.
According to a jointly issued press release, the companies "will work collectively to provide focused solutions to the recycling industry."
Riverside Engineering will focus on shredder design, fabrication, controls and downstream systems, while Riverside Products will focus on wear parts production and rotor design.
"Knowing the needs of our customers has led to the creation of this business structure and allows Riverside Engineering and Riverside Products to concentrate on our areas of expertise and provide the focused responses that our customers demand," the press release states. "Both companies will work closely together to serve the recycling industry with new ideas and solutions."
Recently, Riverside Engineering has installed several M-Series shredders and Double Feed Roll Systems that are supported by the company’s Cruise Control automation features and H2Pro Water Injection Systems.
Riverside Products has introduced the "Revolution" series of rotors, which reduces energy costs and wear, according to the company. Riverside Products is also capable of custom designing rotors to meet its customers’ needs.
Additional information is available online at www.riversideengineering.com and www.riversideproducts.com
STANLEY LABOUNTY SHARPENS ITS EDGE

Stanley LaBounty, Two Harbors, Minn., has introduced an automated blade lubrication system designed to significantly reduce maintenance and to enhance shearing performance.
The new line of shears, called the MSD Saber-Lube Series, will be presented to demolition contractors at the National Demolition Association show in Nashville in late March and at the Institute of Scrap Recycling Industries Inc. (ISRI) Annual Convention in Las Vegas in early April.
The company says its field testing has shown that the automated lubrication system accomplishes several goals:
• Doubles blade life;
• Cuts build-up welding time on the affected jaw areas in half;
• Reduces downtime by two weeks or more per year;
• Converts blade friction to usable cutting power (an increase of up to 8 percent);
• Increases component life, as less welding means less heat build-up cycles;
• Reduces noise; and
• Facilitates removal of wear parts.
A news release from Stanley LaBounty also claims that the new shears feature smoother hydraulics, "with an overall cutting process that is smoother and reduced shock loading throughout the shear and excavator."
The MSD Saber-Lube Series also incorporates other key features of the Stanley LaBounty MSD Saber Series in addition to the patent-pending lubrication system.
More information on the new product line can be found on the company’s Web site at www.stanley-hydraulic-tools.com.
STM TO UNVEIL NEW EQUIPMENT LINES
Schuler Technologies & Machinery (STM), Ueberlingen, Germany, plans to unveil a line of scrap shears, balers, pre-shredders and shredders to the North American market, according to a press release from the company
STM touts a combination of direct scrap industry involvement through the Schuler family’s multi-generational scrap processing operations and recycling machinery design through its alliance with recycling equipment veteran Werner Oberlander. According to STM, "This unique combination of experience and the desire to provide modern, efficient equipment yields a company uniquely qualified to meet the needs of the modern scrap recycling marketplace."
Additional information about STM’s machinery as well as partnership inquiries can be directed to company principals Christine Schuler and Ben Kebil, who can be contacted through the company’s Web site at www.
schuler-tm.com.
WENDT ANNOUNCES SHREDDER SALES
Wendt Corp. of Tonawanda, N.Y., has sold the first machines from its Heavy line of shredders.
Camden Iron & Metal and Sturgis Iron & Metal both purchased a 130 Heavy shredder—the largest mill available offering the greatest throughput capabilities found in the industry, according to Wendt.
The shredders feature an 8,000-hp motor, a four-arm spider rotor and downstream solutions featuring two magnet stands with two 60-inch-by-96-inch axial pole mags, two 72-inch-wide Z-Box air systems, four picking conveyors and two radial stacking conveyors.
Heavy shredders are available with motors ranging from 6,000 to 10,000 hp and are capable of processing 300 tons per hour of ferrous scrap. The units provide more than three times the striking force of a typical 98x104 shredder, according to Wendt.
The Heavy shredder line creates a new sizing standard—82, 106 and 130—within the industry based on the ideal relationship between hammer size and available motor RPM, according to a press release from Wendt.
All the shredders measure 115 inches wide inside the shredder walls and have a free flowing 97 inches of working width inside the feed chute and hammer swing.
Wendt also has announced the sale of another Heavy shredder to the PSC Metals Inc. facility in Canton, Ohio. PSC purchased a Wendt 106 Heavy shredder to replace its 1970s-vintage 96104 Hammermill shredder.
The main reason PSC cites for selecting Wendt was that the equipment offers a shredding philosophy similar to the Hammermill shredder it replaces, incorporating a four-arm spider rotor and an adjustable cutter bar.
PSC also purchased ferrous and nonferrous downstream solutions. The ferrous downstream system uses two 60-inch-by-84-inch Steinert axial pole mags, a Z box and dual 60-w picking conveyors. The nonferrous system features a tumble back feeder, square trommel, Bivitec Screen, three Wendt eddy current separators and a 96-inch Wendt/SSE Finder.
More information is available at www.wendtcorp.com.
NEXGEN CHANGES CONVEYOR LINE NAME
NexGen Baling Systems has changed the name of its conveyor line to EZ-Trax Conveyors from NexGen Conveyor Systems.
The company decided to change the name of its conveyor line to help differentiate it from its baling line, according to a press release from NexGen.
EZ-Trax Conveyors are custom engineered to handle a variety of bulky materials and scrap handling applications. The conveyors are available in light-duty sliderbed, heavy-duty hinged steel belt, combination belt, N-pan and trough styles. NexGen offers a number of widths and various inclines.
In addition to conveyors and balers, NexGen also offers complete turnkey MRF systems that include conveyors, balers, platforms, sorting lines and sorting bins.
More information on EZ-Trax Conveyors from NexGen is available online at www.ez-trax.com or at www.nexgenbalers.com.
NexGen is a division of Vernon, Ala.-based Marathon Equipment Co., a maker of waste handling and recycling equipment.
VECOPLAN ANNOUNCES SERVICE CENTER NETWORK

Archdale, N.C.-based Vecoplan LLC, a maker of recycling and waste shredding and grinding equipment, has announced its establishment of a North American network of factory-trained and certified service representatives.
"This network, along with a multi-million dollar OEM parts inventory, ensures that the 1,500-plus Vecoplan shredder and grinder customers in North America receive prompt and effective attention when in need of these services," according to a news release from the company.
The formal network activation began at a technical training seminar in November at Vecoplan’s facility in Archdale. Approximately 40 individuals earned certification as authorized Vecoplan service representatives, expanding the company’s technical support team of nearly 30 staff members and independent representatives. The training included protocol for system start up, basic maintenance procedures and advanced shredder repair/rebuild for plant-based shredding equipment and systems as well as for Vecoplan’s mobile shredding systems.
"We now have strategic service centers in most key trading areas in North America. California, Minnesota, Massachusetts, Florida, Georgia, Montana, North Carolina, Pennsylvania, Tennessee, Texas, Wisconsin, Ontario and Quebec are among the most recent centers activated," Mark Craver, customer service manager for Vecoplan, says. Vecoplan’s Archdale service team services other states and regions, while a network of representatives coordinated through Vecoplan GmbH in Bad Marienberg, Germany, services customers in Europe, Australia and Asia.
In addition to the service network and the parts inventory housed at Vecoplan’s central parts distribution center, the company offers standard warranties, preventive maintenance contracts, corporate parts programs, rebuild services, telephone customer support, modem-based process monitoring and troubleshooting, guaranteed next-day delivery (on most parts), preferred customer discounts, lifetime guarantees on some components, operational training programs and after-hours support.
IXL MACHINE TO MAKE, SERVICE LSI SEPARATORS
Holland, Mich.-based IXL Machine Shop Inc., a division of Louis Padnos Iron & Metal Co., will manufacture and service LSI Air-Less Metal Separators.
Henry A. Wiltschek Inc., Stoney Creek, Ontario, is the North American distributor of the Air-Less Metal Separators, which have previously been manufactured only in Germany by LSI Electronics.
More information on LSI Air-Less Metal Separators is available online at www.hawiltschekinc.com or at www.lsi-electronics.com.
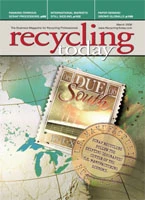
Explore the March 2006 Issue
Check out more from this issue and find your next story to read.
Latest from Recycling Today
- US ferrous market exhibits upward pricing pressure: Davis Index
- Glass Packaging Institute applauds regulation change
- Engcon adds to Tiltorotator line
- Paper recycling is focus of two January webinars
- Disruption likely for material flows in mid-January
- Blue Whale Materials to expand Oklahoma lithium-ion battery recycling plant
- CARI names new president and CEO
- Interzero revamps leadership structure