SIERRA ADDS SAFETY SENSOR
Sierra International Machinery Inc., Bakersfield, Calif., has introduced a safety sensor system that can be added to balers to help prevent severe injuries.
The Safetech System is being offered on the Macpresse line of balers sold by Sierra in the U.S., and can also be retrofitted onto existing baler infeed conveyors.
The system consists of a sensor and receiver system. A sensor is affixed to the Safetech Tag Belt, worn by the worker or workers feeding material onto the conveyor. A Detector Loop containing a receiver is mounted above the conveyor. If the worker should fall onto the conveyor, a signal from the Tag Belt will be received by the Detector Loop, automatically shutting down the conveyor and baler.
"Unlike other systems, Safetech protects workers who are unconscious or injured, even if no one else sees what happens," Sierra literature promoting the Safetech System states.
Machines sold by Sierra in the U.S. also contain the keyed locking system where the main key must be removed after the baler is shut down in order to gain access to the maintenance keys. The system also prevents the baler from being started back up by the operator or maintenance crews until all maintenance keys are returned to a special key box.
NEW LEADERSHIP AT STRIP TECHNOLOGY
Strip Technology Inc., Fort Worth, Texas, a world leader in the manufacturing of cable processing equipment for recycling and industrial markets, has announced that the firm’s day-to-day management has been transferred from founder Bill Alexander Sr. to his twin sons, Bob and Bill Jr., as well as Bill’s brother Ron.
"The new management team took the helm 18 months ago and has done a remarkable job," comments Bill Alexander Sr. on the new team’s performance. "In the first five months of 2002 they have sold more units than were sold in all of 2001."
The new team attributes the success to aggressive marketing efforts they embarked on in 2001. "We committed to an aggressive marketing program that included industry trade magazine advertising, trade shows and the establishment of sales agents," says Bill, Jr. "Our marketing and sales efforts have resulted in significant orders from large businesses such as Southwire and Commercial Metals as well as many smaller, independent yards," adds Bob Alexander. "We’ve also established a domestic sales agent network that includes respected agents such as BE Equipment, BSS Enterprises and Quality Recycling" notes Bob.
In continuing its growth plans, Strip Technology has recently announced the availability of international franchises on its standard wire strippers. "Our goal is to sell wire strippers all over the globe with this new initiative," says Ron Alexander.
Strip Technology has been a maker of cable processing equipment since 1985. The company manufactures a range of standard, specialty and custom wire stripping machines. It also offers repair services for alligator shears, balers, sorting systems and other equipment. Through its affiliated companies, Strip Technology is also able to offer industrial blade sharpening and custom machining, as well as manufacturing services.
INSTALLATIONS
-
Baler Installed in Atlanta
A model AT-1080/HS-100S baler made by IPS Balers, Baxley, Ga., has been installed at the Visy Recycling facility near Atlanta.
The large-volume IPS baler with its large hopper was essential because of the large boxes and packed clumps of material that come into the plant, according to Sidney Wildes of IPS. Wildes notes that normal baler hoppers would have had difficulties with "bridging" of materials.
The newly-installed machine is baling packer truck waste and recyclables that are so heavy that the collection trucks are often nearly overloaded when they reach the Visy plant.
-
Silver Dollar Gets Back to Shredding
Silver Dollar Recycling, North Las Vegas, Nev., has revved up production on its 98/115 shredder built by the Harris Shredder Division and installed early this year.
The metals shredder, the second U.S. shredder plant made by Harris, Peachtree City, Ga., began operating from seven to 10 hours per day this spring to begin chewing through inventory collected during the installation downtime. The motor on Silver Dollar’s previous shredder, a Newell Industries plant, gave out in June of 2001.
"The machine has been fantastic," says Jim Brewer, operations manager of Silver Dollar Recycling. Brewer has been impressed with the quietness of the plant and the innovative design of the reject door, which allows unshreddables to be rejected quickly, before any damage is done and with almost no blocking of material flow through the plant.
Brewer says Harris sales, service and installation personnel acted quickly to get the shredder up and running after their existing plant shut down. He singles out project manager Javier Herrera as having been especially responsive in meeting deadlines and troubleshooting to resolve installation issues quickly.
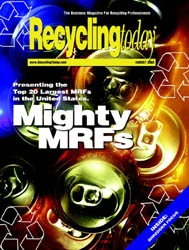
Explore the August 2002 Issue
Check out more from this issue and find your next story to read.
Latest from Recycling Today
- Athens Services terminates contract with San Marino, California
- Partners develop specialty response vehicles for LIB fires
- Sonoco cites OCC shortage for price hike in Europe
- British Steel mill’s future up in the air
- Tomra applies GAINnext AI technology to upgrade wrought aluminum scrap
- Redwood Materials partners with Isuzu Commercial Truck
- The push for more supply
- ReMA PSI Chapter adds 7 members