TELSMITH, KOLBERG NAME NEW PRESIDENTS
Richard A. Patek has been appointed president of Telsmith Inc., Mequon, Wisc. He was formerly president of Kolberg-Pioneer Inc., Yankton, S.D., which is also a division of Astec, Memphis, Tenn.
To fill Patek’s role at Kolberg-Pioneer, Joseph P. Vig has been promoted to president.
Patek has been working in the aggregates industry for more than two decades, and at Kolberg-Pioneer focused on executing programs that resulted in sales and earnings growth for the company.
Vig, who has a civil engineering degree from the South Dakota School of Mines, joined Kolberg-Pioneer in 1994. He is a registered professional engineer in South Dakota and has helped organize and manage the technical aspects of Kolberg-Pioneer’s operations.
CROWLEY NAMED TO CBI POST
John Crowley has been hired by Continental Biomass Industries Inc., Newton, N.H., as District Sales & Marketing Manager for the south central United States.
Crowley, formerly Director of Sales and Marketing for Granutech-Saturn Systems Corp., Grand Prairie, Texas, brings more than 13 years of experience in capital equipment sales to his new position.
“I am extremely happy to be able to contribute to CBI’s efforts to broaden the reach of its high-quality wood waste processing systems. The south central United States in general—and the Dallas-Ft. Worth metroplex in particular—offers some of the fastest developing areas in the country. That growth, obviously, results in a great deal of land clearing and, subsequent to development, a good deal of C&D waste that needs addressing. I feel strongly that the CBI product line is best-suited to meet those needs and look forward to increasing their presence in this area.”
Crowley will represent CBI to customers in the states of Texas, Louisiana, Arkansas, Oklahoma and New Mexico. According to CBI owner Anders Ragnarsson, the addition of Crowley to the CBI sales team is a definite plus for both the company and its customers.
“John’s 13 years experience dealing with customers in industries similar to ours will undoubtedly prove invaluable in our sales efforts,” says Ragnarsson. “In addition, his track record of going the extra mile to ensure customer satisfaction blends well with our own corporate philosophy. We are very pleased to have him on board.”
CBI manufacturers portable and stationary biomass recovery systems including horizontal grinders, stump shears and screening equipment.
LIPPMANN FILLS OUT IMPACT CRUSHER LINE
Lippmann-Milwaukee Inc., a Cudahy, Wisc.-based manufacturer of crushing machinery for the aggregate and recycling industries, has added to its line of impact crushing plants. The line now includes the following models: 4248LP, 4248CC, 5165LP, 5165LS, 5860LP and special application 4236LS and 5196LS models.
“Our engineers have developed a comprehensive line of quality impact crushing plants designed to address most every aggregate and recycle crushing application need. With this new line of rugged equipment, we’ve built in more features and greater value for less capital outlay,” says Robert Turner, Lippmann’s president.
The company says the 4800 Series Impact Crushing Plants are completely self-contained, easy to transport crushing plants that offer features contractors require, like a larger crusher feed opening that devours concrete full of rebar, ripped asphalt and other C&D debris. The heart of the plant is a Lippmann 4248LP Impact Crusher that features a “heavy duty rotor built to handle the daily punishment of recycled materials,” according to a company news release.
The company says the 4800 Series plant is engineered for maximum efficiency, performance, ease of transportability and easy set-up and tear down and is suitable for small to medium size crushing projects. The company is positioning its other models for different applications:
• Lippmann’s 6500 Series of portable impact crushing plants are engineered for high performance, ease of transportability, operation and versatility.
• The Lippmann 5165LP primary portable crushing plant is a standard, cost-effective unit for primary recycling of concrete or asphalt. Various lengths of Lippmann feeders are available, as well as a discharge pan feeder under the crusher.
• The Lippmann 5165LS is a secondary recycle or aggregate plant that teams up with Lippmann¹s 3062 Jaw Plant in a two-stage recycle crushing application, or with a Lippmann 3048 Jaw Plant in a two-stage aggregate crushing operation.
Plants sold into recycling applications are equipped with magnetic separators, reinforced belting, special wear alloys and other options to suit customer requirements.
STANLEY LABOUNTY ADDS TO RECYCLING PLANT LINE
Stanley LaBounty, Two Harbors, Minn., has introduced the RM 80 Rubble Master track-mounted crushing plant. Recycling plants are a newer product for the long-time maker of excavator and material handler attachments.
“The machine will allow contractors to perform cost-effective recycling of concrete, brick, rock, asphalt and other materials on site in order to avoid hauling and dumping expenses,” says Uwe Kausch, Stanley LaBounty product line manager.
The track-mounted impactor can produce from 80 to 150 tons of material per hour while being fed through a 34 inches by 23 inches inlet opening. A magnetic separator is standard, and a built-in pre-screen can remove contaminants at the front end of the process.
Get curated news on YOUR industry.
Enter your email to receive our newsletters.
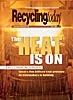
Explore the July 2001 Issue
Check out more from this issue and find your next story to read.
Latest from Recycling Today
- Green Cubes unveils forklift battery line
- Rebar association points to trade turmoil
- LumiCup offers single-use plastic alternative
- European project yields recycled-content ABS
- ICM to host colocated events in Shanghai
- Astera runs into NIMBY concerns in Colorado
- ReMA opposes European efforts seeking export restrictions for recyclables
- Fresh Perspective: Raj Bagaria