
Founded in 1912 by H. Berger, who collected scrap using a horse and wagon, Berger Recycling, based in Pawtucket, Rhode Island, has grown into a full-service recycling firm. Today, Berger Recycling operates a modern, automated facility and provides turnkey solutions for collecting and purchasing recyclables in Rhode Island, Massachusetts and Connecticut. The company specializes in scrap metal, paper, electronics, plastic, insulated wire, batteries, textiles and new paper rolls.
Berger Recycling is still owned and operated by the third and fourth generations of the Berger family. The company has been recognized as the United States Small Business Administration Family Owned Business of the Year for the Rhode Island and New England region.
Berger Recycling first partnered with M&G Materials Handling Co. in 2005 when it was time to purchase new material handling equipment for its operation.
Headquartered in East Providence, Rhode Island, M&G Materials Handling Co. supplies material handling equipment to the southern New England area. Established in 1966, M&G Materials Handling serves customers in Pawtucket, Cranston, Woonsocket and Warwick, Rhode Island, and in Taunton, New Bedford, Attleboro, Brockton and Rehoboth, Massachusetts.
Challenge
As a scrap metal and recovered paper facility, Berger Recycling suffered from two material handling issues that resulted in extended periods of downtime. The first problem was that the dust created by scrap paper interfered with the transmissions of the company’s lift trucks. The second issue was brake contamination. Berger Recycling’s scrap, corrugated and paper products are strapped together with baling wire. The baling wire can slip off of the product and, if left on the ground, can become wrapped around lift truck axles and shear brake lines.

Aware that its lift trucks weren’t performing to its requirements, Berger Recycling reached out to Ken MacDonald at M&G Materials Handling for assistance when shopping for new lift trucks for its operation.
Solution
After meeting with Berger Recycling and assessing the company’s lift truck needs, M&G Materials Handling paired the recycling company with 6,000-pound-capacity Yale Veracitor GP060VX lift trucks.
“The sealed bearings and wet disc brakes on the Veracitor eliminated our issue of baling wire damaging or shearing the braking system,” says Adam Sinel, vice president of operations, Berger Recycling. “I am also proud to say that our Veracitor has never overheated.
“The Veracitor’s features are absolutely imperative to keeping our business up and running—and the fact that they come standard helps our bottom line,” he adds.

The lift truck’s sealed alternator eliminated dirt contamination that could cause damage, while its heavy-duty Combi-Cooler radiator prevented corrugated dust from entering the machine’s air system.
The vented hood on the GP060VX created less of a vacuum pull off the undercarriage, resulting in less paper and scrap contaminant draw and increasing the amount of clean air brought into the engine. The Veracitor also was equipped with a high-air intake and precleaner to reduce pulling in dirty or contaminated air. This feature is designed to help extend engine and filter life while increasing fuel economy, Yale says.
The Veracitor’s Techtronix transmission, with its Controlled Power reversal feature and smooth electronic inching, greatly reduced Berger Recycling’s tire costs. The standard Auto Deceleration System also helps extend brake life by automatically slowing the truck when the accelerator pedal is released, minimizing brake usage requirements and reducing overall brake maintenance costs, the manufacturer says.
“After utilizing various lift truck brands, we realize that these features help minimize tire spin, which increases their life span,” Sinel says. “The Veracitor has dummy-proofed itself by not allowing operators to throw the lift truck from forward to reverse—improving the lift truck’s overall longevity.”
Impact
Throughout their partnership with M&G Materials Handling, Berger Recycling has trimmed its operating costs.
“Since our partnership with M&G Materials Handling Co., our operating costs have been substantially reduced,” Sinel says. “We have not incurred the expenses that we did with other lift truck suppliers. For example, our previous lift truck went through three transmissions in a six-month period.
“I am confident that M&G Materials Handling Co. is looking out for the best interests of my company, associates and customers,” he states.
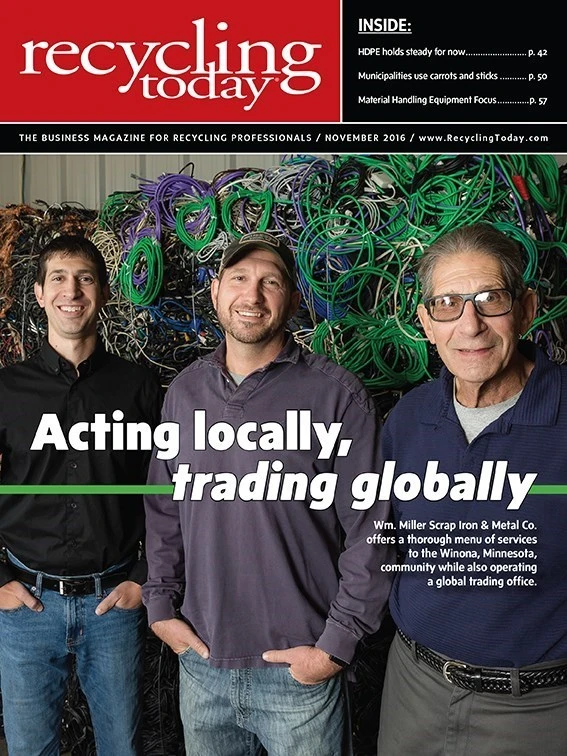
Explore the November 2016 Issue
Check out more from this issue and find your next story to read.
Latest from Recycling Today
- Magnomer joins Canada Plastics Pact
- Electra names new CFO
- WM of Pennsylvania awarded RNG vehicle funding
- Nucor receives West Virginia funding assist
- Ferrous market ends 2024 in familiar rut
- Aqua Metals secures $1.5M loan, reports operational strides
- AF&PA urges veto of NY bill
- Aluminum Association includes recycling among 2025 policy priorities