Conventional wisdom may instruct one to "begin at the beginning," but the beginning isn’t always the best place to start, especially when it comes to setting up a tire recycling system.
For a tire recycler, the end—or the final saleable product that comes from recycling old passenger and truck tires—is the best place to start when configuring a processing system, since that end market determines what specifications a product must meet.
Furthermore, with today’s scrap metal prices, many tire recyclers have come to see the steel wire pulled from recycled tires not as a mere byproduct, but as an additional revenue stream.
END GAME.
"It all depends on the end use," says Brian Radtke, production manager at Silver Lining Tire Recycling of Wyandotte, Mich. "Depending on what kind of product, what you want to produce or make, that determines your equipment. You start at the end and work backwards."A 2-inch-minus tire derived fuel (TDF) product, which it sells to the local power plant as an alternative fuel, is what Silver Lining is after. The specs required by its power plant customer determine how the company sets up its processing system. That system consists of a primary shredder and a chipper from Columbus McKinnon Corp., Sarasota, Fla., which are connected by a series of conveyors and screens. "We have a primary shredder that takes us from whole [tires] to thirds, which then goes across a shaker table," Radtke describes.
INDIANA COUNTY GETS GRANT FOR RUBBERIZED ROADS |
More rubberized asphalt is coming to Perry County, Ind., with help from a grant from the Indiana Department of Environmental Management, according to a news item in the Perry County News (Tell City, Ind.). The material will be used to pave more of the Perry County Solid Waste Management District’s recycling site and a nearby area in Cannelton, Ind. A $15,045 grant from the Department of Environmental Management will build on a 2006 pilot project that paved part of the processing drop-off center, according to the report. According to the report, a track at Tell City High School was also paved with the rubber asphalt mix. The material incorporates crumb rubber with regular asphalt. According to the report, in addition to more of the recycling site, a road leading to a sewage-pump station will be paved with the mix when weather conditions permit. |
The material then goes across a 40-foot action screen then up another conveyor to the chipper, which has the smallest configuration of knives. "Material gets recycled through the chipper and shaker table until it’s the size that will fall through the screen," Radtke says. "We get about 10-12 tons per hour making 2-inch chip," he says.
Silver Lining has magnets set up at the end of its system, right before the final product, to remove any remaining steel, which Radtke says works well for the kind of product the company is making. "We have the magnets at the end, because if you were to put them before, the material is too large to get anything," he says. "In our particular application, they have to be where they are."
However, different end products can call for different magnet configurations. For instance, State Rubber in Denver City, Texas, which makes a crumb rubber product for several industries, including asphalt, molding and equestrian applications, has several series of magnets throughout its Granutech Saturn Systems, Grand Prairie, Texas, system.
"We take whole tires and drop them into a shredder, which does the initial cut," says Dan Swanson of State Rubber. Following the initial cut to a 3-inch-nominal size, the material then goes to a model 80 Grizzly, where it is cut a second time to "around popcorn size," according to Swanson. The material encounters a first set of magnets following the second cut and also goes through air aspiration to begin to remove the fluff.
MICHIGAN DEQ IMPLEMENTS CHANGES TO TIRE PROGRAM |
The Michigan Department of Environmental Quality (DEQ) has implemented changes to its scrap tire program that are expected to reduce the burdens in handling, processing and recycling scrap tires. The changes are a result of a package of bills signed into law by Michigan’s Gov. Jennifer Granholm. One of the changes classifies certain types of high value scrap tire materials such as tire derived fuel as a commodity largely exempt from regulation as a scrap tire in an effort to facilitate the processing of these commodity materials. Other major changes include: • Providing the local fire chief the authority to deter- • Prohibiting scrap tires from being placed in open • Simplifing the manifest requirements by allowing a • Requiring owners of a portable shredding operation • Exempting retreaders from hauler registration re- • Extends the sunset on Scrap Tire Program funding A complete list of the changes to Michigan’s scrap tire program is available at www.RecyclingToday.com. |
Following that separation, material then goes to a granulator where it is cut to a quarter inch, Swanson describes. "When it comes out of that, it passes through another magnet and we really start removing the fiber," he says.
Before a final product is created, crumb rubber passes through a total of four sets of magnets spread throughout the system, according to Swanson. Placing magnets throughout is a necessity at State Rubber, he says, because of the demands from its customers. "Most everybody we deal with requires steel-free, fiber-free material," he says.
Magnets are also placed throughout the Granutech system in place at Utah Tire Recycling in Salt Lake City, according to Vice President Rob Jahris. Utah Tire Recycling makes several products that meet a variety of specifications to satisfy different end markets, from the less-stringent TDF market to the asphalt and mulch markets that demand cleaner material.
Material that is destined for the TDF market goes through only part of the process, while crumb rubber bound for higher-end destinations goes through a series of shredders, granulators, screens and magnets. "All the way through we’re magnetically separating steel and aspirating nylon," Jahris says of the crumb rubber line.
No matter how a system is arranged, tire recyclers seem to agree that a certain degree of flexibility within a system is critical to success.
MARKET-ORIENTED.
After 17 years in the business, Swanson of State Rubber has seen the tire recycling industry change into a market-driven business. "It has changed a lot," he says of the industry. "Initially, there virtually were no markets."Today, rubber reclaimed from old tires—not to mention the steel wire pulled from the tires—has many profitable end-use markets, and tire recyclers would be wise to set up their processing systems to serve more than just one of them.
"The markets for crumb rubber I’ve seen have developed from nothing into different markets," Swanson says. "The material they’re using right now may change, so flexibility is really a key."
Swanson adds that he sees the largest growth potential in the higher-end segments of the market, such as crumb rubber for asphalt and athletic fields.
"Athletic is big," agrees Jarhis, saying that applications like football fields and running tracks represent growth potential for tire recyclers looking to break into some higher end-use markets.
KOMEI SELECTS ECOSYSTEM AS U.K. SALES AGENT |
Ecosystem Ltd., Surrey, U.K., has been appointed as the sole agent for the range of tire recycling equipment manufacturered by Komei, based in Padova, Italy. Komei’s 16,500 kilogram KG-1R granulator is designed specifically for shredding used tires. It is fitted with a heat exchanger to keep the rotor and counter blade support at a low temperature. An 180- kiliwatt motor drives the machine and it is CE certified. Ecosystem is also the exclusive distributor of Eva-shred shredding machines, manufactured by New Zealand-based F.V. Evans & Sons. The Komei tire recycling plants use Evashred debeaders and pre-shredders on truck or car tyres prior to granulation. Additional information on Komei and Eva-shred tire recycling equipment is available online at www.komeimacchine.com and www.evashred.co.uk, respectively. |
Landscaping mulch represents another avenue of growth potential in the tire recycling industry, according to Radtke, and is a market Silver Lining is on the path to pursuing in the coming year.
"Landscaping rubber is really growing," he says. "It’s very popular right now." Landscaping rubber aims to replace its wood equivalent, boasting a longer life span. "Instead of spending $3 or $4 on red cedar mulch, which breaks down so every spring you’ve got to add to it, with rubber mulch, you don’t have to do that," Radtke says.
"It’s probably about $10 more per bag compared to what you’d normally buy, but in a three year period, you’re actually paying less for it because you don’t have to add to it, you just have to re-rake it."
However, no matter what end product a recycler has his eye on, Jarhis advises recyclers to keep their options open and to set up their equipment to do the same. "We have a lot of markets and we have the ability to hone in on where the demand is," he says.
Swanson agrees that it pays to be flexible when setting up a processing line. "It’s a lot cheaper to build your plant with the flexibility in it initially than to set out to serve one specific market," he says. "The crumb rubber market is so variable; you’ve got to be able to produce that material for that high-end market without actually changing equipment, but adjusting the equipment you already have."
Building flexibility into a system at the outset goes a long way in helping a tire recycler stay viable in an evolving market. However, the key to the optimum processing system still lies with starting with an end product in mind.
"The first thing somebody needs to do is identify the market, find out everything they can," says Swanson. "Their equipment needs to be tailored to what they want to make."
The author is associate editor of Recycling Today and can be contacted at jgubeno@gie.net.
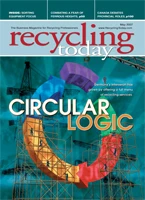
Explore the May 2007 Issue
Check out more from this issue and find your next story to read.
Latest from Recycling Today
- Nucor receives West Virginia funding assist
- Ferrous market ends 2024 in familiar rut
- Aqua Metals secures $1.5M loan, reports operational strides
- AF&PA urges veto of NY bill
- Aluminum Association includes recycling among 2025 policy priorities
- AISI applauds waterways spending bill
- Lux Research questions hydrogen’s transportation role
- Sonoco selling thermoformed, flexible packaging business to Toppan for $1.8B