Multi-national technology company IBM, Armonk, N.Y., has been manufacturing computer equipment for as long as almost any company in the world and, therefore, has been faced with how to best handle end-of-life electronics for as long as any other company.
For the past 12 years, IBM’s Global Asset Recovery Service (GARS) has been the key division within IBM tasked with effectively managing the wide range of end-of-life equipment yielded globally by IBM’s manufacturing plants, offices and leasing operations.
According to GARS Senior Engineer and Senior Program Manager Ed Grenchus, IBM has learned a great deal about cost-effectively and responsibly handling end-of-life electronics, but the learning process does not stop since technology changes so rapidly.
SEVERAL GOALS
GARS, Grenchus says, is part of IBM Global Financing (IGF), and part of GAR’s mission is to contribute to IGF’s overall financial performance.
IGF is responsible for leasing equipment to IBM’s large customers and clients. When these leases expire, equipment is returned to GARS for end-of-life management and dispositioning, Grenchus explains.
“We also get IBM’s end-of-life internal machines from IBM offices and other locations throughout the world,” he adds.
The operations of GARS, like those of IBM, are indeed global. “We’ve got locations in what we consider all our major geographies—the Americas, Europe, portions of Africa, the Middle East and our Asia/Pacific Group,” says Grenchus. “We divided it out by regions and then we have a number of centers—de-manufacturing and scrap—in each region.”
In keeping with IGF’s goals, GARS’ objective is to capture the best residual value of the equipment it is sent. Thus, equipment could go through channels that will lead to a combination of remanufacturing, re-use and resale, or it could go toward de-manufacturing and scrap recycling disposition.
Equipment handled by GARS is sent either to its remanufacturing/repair centers to prepare it for that market or to de-manufacturing plants also operated by GARS. “Between both operations, we handle an estimated 35,000 machines per week globally.”
While cost-benefit models dictate the resale vs. recycling decision, Grenchus says other considerations are common to either end-of-life scenario. “In either case, GARS focuses on asset protection, data security and ensuring environmental compliance,” he states.
Through its decades of experience and establishing best practices, the GARS division of IBM has become adept at achieving high re-use and recycling rates, Grenchus says.
“We focus on trying to recover all units at the highest level, but if it can’t get recycled or recovered, then we do have some that is landfilled or incineration,” he comments. “But for 2010, IBM landfilled or incinerated less than 1 percent of its waste stream. GARS was a big part of helping the company reach that ratio,” he adds.
MULTIPLE FACTORS
Part of the institutional knowledge GARS has accumulated through its years of experience includes knowing the fixed and variable factors that help it make decisions when determining whether units will be re-used or de-manufactured and recycled.
Units destined for re-use must meet certain criteria, Grenchus says. “GARS product managers will look at secondary market demand and they’ll look at the technology of the piece of equipment,” he adds.
Factors in this decision can include “where the product is in its life cycle,” says Grenchus. “And certainly, we look at financials—do we have to invest in refurbishment and, if so, will we recoup that investment?”
After looking at these criteria, he continues, “If the return is positive, it will be remanufactured, refurbished and sold into the secondary market. If it doesn’t pass that criteria—it requires too much investment to make it marketable or it’s simply broken—then it goes to a de-manufacturing and scrap location.”
Consignment to a disassembly plant does not end the quest to maximize return and re-use possibilities, Grenchus notes. Parts can be harvested either for IBM internal re-use or wider resale at these locations. The GARS staff as well as the employees of the de-manufacturing plants know which IBM components are on a “save list,” so operators can pull out those specific parts and, based on direction from the service organization, and send them for testing or cleaning. Grenchus says GARS also knows if there are industry-standard parts (not proprietary to IBM), such as some memory components, that can go for resale through outside channels.
It is only after this process is complete that GARS and its employees begin to consider the secondary commodity values of its end-of-life material stream. “In some cases, there is a very suitable robust commodity structure,” says Grenchus, referring to metals and some plastics. “We’ll work with our recycling and recovery suppliers to see how much disassembly we can perform to either make a pure commodity or a commingled portion.”
As of 2011, GARS is not processing recyclables via capital-intensive shredding or sorting operations but instead is working with allied recyclers. “We’re not recycling, as in making pellets and flakes, but we’ll dismantle and do some sorting of plastic parts. We’ll work with the recyclers in the regions in which we operate to get them what they need. We prefer to have our downstream scrap commodities handled by the experts—recyclers and smelters and processors.”
FAR FROM STATIC
Although Grenchus and others at GARS have learned plenty about when to opt for re-use and when to de-manufacture and recycle, many of the factors are variable and can change quickly.
“There are always supply-demand considerations and the technology is changing—thus so are the different criteria used to reach a decision point,” says Grenchus of the re-use vs. recycle decision-making process.
GRAVITATING TOWARD RECYCLING |
Ed Grenchus, senior engineer and senior program manager with the Global Asset Recovery Service (GARS) division of IBM, Armonk, N.Y., did not join the multi-national computer company as its recycling expert. “I started out with IBM in 1978 on the technology side,” he says. “For about 18 years I was focused on printed circuit boards and components, in the manufacturing and quality engineering areas.” The opportunity to try something else emerged in 1996, when Grenchus says he “decided to make a switch and do something entirely different by getting into asset recovery.” For IBM at that time, “It was a new area we were getting into.” Now, 15 years later, Grenchus is a relative veteran in the electronics recycling sector. He has been involved in organizing a recycling conference hosted by the IEEE (Institute of Electrical and Electronic Engineers) as its conference chair and has helped shape GARS as the IBM division that is focused on product end-of-life management. |
Also changing are the legal, regulatory and operating standards that can affect the decisions being made. “IBM has an environmental management system that is ISO 14001 certified, and GARS is part of that,” Grenchus says. “GARS works with the other IBM internal organizations to really identify, interpret and analyze the regulations and new pieces of legislation. Based on that teamwork, we come up with a comprehensive plan to make sure we’re compliant with, say, the WEEE (Waste Electrical and Electronic Equipment) or RoHS (Restriction of Hazardous Substances) directives in Europe. RoHS means working with the manufacturing arm, but we come to the forefront when we get to the WEEE component.”
The fact that what GARS does is global but that the depth of the recycling infrastructure can vary greatly by region also presents challenges. “Some decisions are based on the local recycling infrastructure or the regional infrastructure,” Grenchus says. “It can be hard in a small, emerging market to find a local recycling source. You may have to ship things a longer distance. In a place like the United States, we can work with smelters and other facilities nearby.”
Geography also can affect the way IBM and GARS ship end-of-life units within or between their operating regions. “History has shown that when people or companies don’t care or don’t pay attention [end-of-life electronics] get dumped in places they shouldn’t go,” Grenchus says. “We’re working to let folks know that there are companies like IBM and organizations like GARS that have products and controls in place that can bring re-used equipment to a market in a way that is safe and so the technology is affordable.”
One of the gratifying changes Grenchus says he has seen during his 15 years with GARS is the increased number of recycling options for plastic scrap. “The ability to recycle plastic has improved,” he says, noting that some of the improvement stems from designing for easier recycling. “When you look at a lot of businesses in the IT industry, we used to use a wider variety of resins. I think the de-manufacturing centers fed back to the designers to minimize the number of plastics being used, and then the better our chances are for recovery.
“Generally, when you’re working with a plastics recycler, they prefer high volumes of like material,” Grenchus continues. “It is much harder to get a relationship going with a recycler when you have small quantities of 20 different resins.”
It has helped GARS find more ways to avoid landfilling material, which is one of the things Grenchus says he is proud of during his tenure with GARS. Although, he says he remains a fan of re-use and redeployment of entire units as a valuable way to conserve resources and to help IBM be profitable.
“We do a lot for recycling and recovery at the commodity level, but the biggest bang for the buck is in the refurbishment and remanufacturing center. That’s where we’re getting the best value for the product in its life cycle. Through aggressive refurbishment, we can extend its useful life. We can bring more value to the Global Financing division and to IBM through that method.”
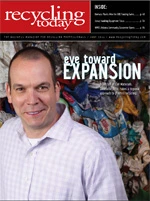
Explore the June 2011 Issue
Check out more from this issue and find your next story to read.
Latest from Recycling Today
- AF&PA report shows decrease in packaging paper shipments
- GreenMantra names new CEO
- Agilyx says Styrenyx technology reduces carbon footprint in styrene production
- SABIC’s Trucircle PE used for greenhouse roofing
- Hydro to add wire rod casthouse in Norway
- Hindalco to invest in copper, aluminum business in India
- Recycled steel price crosses $500 per ton threshold
- Smithers report looks at PCR plastic’s near-term prospects