The U.S. Environmental Protection Agency (EPA) estimates that more than 130 million tons of building-related C&D debris is generated yearly in the U.S. This material results from the construction, renovation or demolition of structures.
Historically, most C&D material has been placed in landfills with other types of solid waste. However, as available landfill capacity has decreased throughout the country, unused space has become increasingly valuable, and a significant emphasis is now placed on diverting portions of the solid waste stream from landfills.
This has led to the construction of many facilities designed to specifically process C&D debris. While these facilities usually provide the environmental benefit of conserving landfill space, they have not always been successful business ventures.
HARVESTING RECYCLABLE WOOD
The Environmental Resource Return Corp. (ERRCO) C&D processing facility was built in 1995. The ERRCO facility is located on an 80-acre site in Epping, N.H., and utilizes an extensive processing system that includes multiple picking stations, shredders, floatation tanks and screens.
The ERRCO system can process more than 600 tons per day in a two-shift operation. Since it commenced operations, ERRCO has processed about 1 million tons of C&D debris into a number of marketable end products.
ERRCO’s primary feedstock has historically consisted of demolition-based debris usually delivered in 100-yard trailers from sites throughout New England and construction or renovation-based material normally delivered in roll-off containers from sites within a 30-mile radius of the facility.
ERRCO’s two primary feedstock materials have different general compositions that can influence the pace and the results of processing. From a processing standpoint, the construction-based material generates considerably more residual (i.e. non-recyclable) material than the demolition-based stream. This influences operation costs as well as the processing pace
However, these effects are somewhat offset by the higher tipping fee that can be charged for the construction based material.
C&D debris of all types contains many different materials that ultimately have value if they can be economically recovered. However, operating a business that seeks to profit from that value is often quite difficult. Many processing facilities have failed or have not lived up to expectations because they did not recognize the economic and technical reality the business requires. To be successful, a C&D processing facility has to be operated as a manufacturing plant creating products that must satisfy competitive market conditions.
Processing C&D as a business requires a clear understanding and, to the degree possible, control of the factors that influence the input and output end of the business. These factors are governed by three simple logical principles:
• You can’t process anything unless you can get in the door to process.
• You must have reliable markets for the derived products if you don’t want your stockpile to exceed permitted levels.
• Tipping fees and product sale revenues are a function of competing alternatives for the processing service and the derived products.
The way that a facility deals with each of these principles determines the viability of its business structure.
TIPPING THE BALANCE
A C&D processing facility needs to charge its service customers a tipping fee low enough to attract material. Suppliers will evaluate an offered tipping fee along with the associated cost of transporting the material to the facility in making decisions as to where to send their material.
High landfill tipping fees in New England, for example, have led some C&D suppliers to consider rail hauling or trucking of C&D considerable distances to other states where tipping fees are considerably lower. These lower tipping fees compensate for the increased transportation costs.
Alternative disposal locations for C&D can consist of landfills and competing processing facilities. If landfill tipping fees are generally high, the C&D processing facility can logically charge a higher tipping fee than a similar facility in a region where competing landfill tipping fees are low. As a result, prevailing landfill tipping fees significantly influence what a processing facility can charge C&D suppliers. This may, in turn, determine whether a given region can economically support a C&D processing facility.
Other waste management dynamics can also affect the C&D processing tipping fee. For example, Massachusetts is seeking to implement a landfill ban on wood, separating it from the waste stream for recycling. As overall landfill capacity in the region is decreasing, such a ban may be justified. ERRCO views this new regulatory mandate as a definite business opportunity in that tipping fees would be expected to increase as a result of the elimination of landfills as a competing alternative.
A PROFITABLE MIX
Through its processing of demolition-based C&D, ERRCO generates the following end products:
• Wood fuel—Wood is used as a fuel in a number of biomass plants in the region. In its marketing, ERRCO gives preference (and a lower tipping fee) to C&D sources with significant wood content because of its focus on wood-fuel supply.
• Metal—Metal is manually or magnetically separated throughout ERRCO's processing system and sold to a salvage yard.
• Aggregate—Rocks, bricks and concrete are separated during various stages of processing. They are accumulated until a sufficient quantity justifies rental of a rock crusher to convert the material into crushed aggregate that can be used in a variety of construction applications.
• Dirt—Dirt is separated during processing and used as daily or intermediate cover at a number of landfills.
• Residual—After all components with value have been captured, residuals such as dirty paper, plastic, etc., remain that must be shipped to a licensed landfill for disposal.
Based on ERRCO’s experience, the relative proportion of the above components resulting from the processing of the demolition-based mixed C&D stream shows wood comprising 50 percent of the overall stream. This is followed by 22 percent of the material that can be used as landfill cover; 15 percent clean aggregate and 5 percent mixed post-float-tank aggregate; 5 percent mixed metals; and finally just 3 percent residual material.
While each load of material received for processing varies in composition, this general component mix has been consistent throughout ERRCO’s operating history for site demolition. The addition of renovation- and construction-based material has increased the relative proportions of residual material.
In ERRCO’s business model, most of ERRCO’s revenues are from tipping fees for the material to be processed.
Generally, output products do have economic value. However, in some cases, the revenue derived from selling the products does not even pay for the transportation required to get the products to markets.
For example, ERRCO’s historical sale of wood fuel has normally required a financial "push," as the cost of transportation to the biomass plants is often more than the unit revenue paid by the biomass plants.
Since more than 50 percent of ERRCO’s output material is wood fuel, its cash flow structure is somewhat tied to the economic structure of the biomass plants.
THE BIOMASS SCENE
Biomass power capacity currently represents about 7,800 megawatts installed at more than 350 locations throughout the U.S. This is about 3 percent of total U.S. electricity generation capacity.
The biomass power industry is located primarily in the Northeast, Southeast and West Coast regions of the U.S because these are the regions of the country where most of the wood resources are located. Biomass generation economics are not only driven by regional power costs and availability, but also by the availability of nearby wood fuels.
Many of the current plants in New England were built in the mid-1980s to 1990s as a result of federal legislation (the Public Utility Regulatory Policies Act [PURPA] of 1978). PURPA enabled long-term contracts guaranteeing that renewable power would be purchased at set rates.
Unfortunately, these contracts were generally advantageous to producers but not to power markets in the 1990s. As a result, many biomass plants had their contracts bought out and, in some cases, were shut down.
What biomass plants are willing to pay for wood fuel is a function of the revenue that they can derive for generated electricity and the competing prices and availability of other wood fuels, such as mill residue and whole tree chips. The value of electricity generated by the biomass plants has changed in recent years as a result of deregulation and other dynamics that have affected the value of electricity in the region.
The biomass facilities that have purchased ERRCO’s wood fuel over the years have been drawn to its relatively low cost and its low moisture content as compared to alternative fuels. The lower moisture content reduces the amount of fuel that must be combusted to generate a fixed amount of electricity. C&D wood fuel is usually combusted with other fuels.
The typical fuels used at wood-fired power plants include:
• Whole-tree chips
• Wood residues
• Mill residues
• Sawdust
• Forest residues
• Urban wood including C&D
The biomass power plants that combust C&D derived fuel must be able to deal with other issues created in combusting this type of fuel, however. These issues include:
• Increased fuel contaminants
• Non-combustible components
• Painted surfaces
• Treated wood content
• Ash disposal (Wood ash has often been land spread. However, because of the increase lead content in the ash as a result of the C&D fuel, it may have to be brought to a landfill for disposal.)
• Air emissions (Because air emissions are a function of fuel composition, the introduction of C&D wood fuel has often required stack testing to verify that air emissions are within acceptable limits.)
Irrespective of these issues, a number of factors motivate use of biomass for electrical generation. For example, the use of biomass can affect climate change issues because of a net reduction in carbon dioxide emissions results as compared to coal.
In addition, many states are adopting Renewable Portfolio Standards (RPS) aimed at requiring a minimum level of renewable power generation in their jurisdiction. Maine (the state where most of ERRCO’s wood fuel is shipped) is a leader in this effort by establishing a 30 percent renewable power standard.
In addition, Senators Snowe (Maine) and Jeffords (Vermont) recently introduced legislation promoting a national RPS to help address greenhouse gas emissions. Another factor influencing the attractiveness of biomass generation is the geopolitical situation reflecting the need for more home-grown fuel.
MAKING ADJUSTMENTS
Based on its experience, ERRCO believes that one of the fundamental issues associated with successful C&D processing is the need to maintain as much flexibility as possible to adjust operations to meet market conditions as they evolve.
If long-term contracts are not available for sale of recovered products, the value and stability of available markets may be questionable. However, with the ability to quickly change the business focus of the material recovered from processing, the proper business adaptability exists to "float" with the market conditions and to make adjustments as required.
For example, ERRCO has the ability to quickly convert its processing away from wood fuel generation if market conditions would warrant.
As would be expected in many material processing facilities, stockpile limitations exist in the ERRCO regulatory permit. These stockpile limitations must be managed closely and provide incentive to market and to continually ship end products.
A C&D processing facility must also be able to weather the seasonality normally experienced in its waste stream. This seasonality ties in closely with the normal construction season in a region. As a result, ERRCO has always had significant material to process during the warmer months, followed by a significant drop-off in material receipts during the winter months.
Because of the regular pattern of C&D availability in its service area, ERRCO can plan for operational adjustments (staffing, etc.) that are necessary to optimize costs during the slower months.
ERRCO believes that the following guiding principles apply in determining whether a profit can be made from processing of construction and demolition materials:
• To the degree possible, strong (contractual, if possible) relationships need to exist with major suppliers of material to be processed as well as with markets for the products derived through processing. If you can’t get contracts, maintain close contact and treat your customers well.
• Processing facilities must have the flexibility to adjust their operations to prevailing supply and market conditions such as a regular seasonal downturn.
• A C&D processing facility must rigidly hold to the terms and conditions of its solid waste operating permit. This will affect the long-term viability the facility as well as the public perception of its effectiveness.
• For health, safety and regulatory reasons, a C&D processing facility must guard against receiving materials such as asbestos. If asbestos is received, contingency plans must be in effect to safely manage the material. (For health and safety reasons, ERRCO has six certified asbestos inspectors on staff. These people normally function as equipment operators or supervisors, but also have the responsibility of inspecting all C&D loads received for processing.)
• ERRCO believes that support of effective wood fuel markets in the future requires working closely with biomass power producers so that they understand C&D processors’ technical and economic problems and we understand theirs.
The authors, Leo R. Larochelle P.E. and Byron Philbrick, are the Facility General Manager and Controller of ERRCO, Epping, N.H.
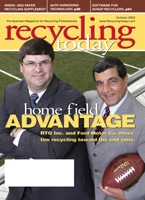
Explore the October 2003 Issue
Check out more from this issue and find your next story to read.
Latest from Recycling Today
- Nucor receives West Virginia funding assist
- Ferrous market ends 2024 in familiar rut
- Aqua Metals secures $1.5M loan, reports operational strides
- AF&PA urges veto of NY bill
- Aluminum Association includes recycling among 2025 policy priorities
- AISI applauds waterways spending bill
- Lux Research questions hydrogen’s transportation role
- Sonoco selling thermoformed, flexible packaging business to Toppan for $1.8B