
Change is good. When the idled FutureMark mill, now owned by UP Paper LLC, restarted in Manistique, Michigan, in June 2016 after being closed for more than a year, UP Paper President and CEO Lars Dannberg says change was fundamental to the mill’s progress.
Some changes were considerable: The paper mill switched from producing multiple printing and writing grades of paper to just one grade: a lightweight, 100 percent recycled kraft paper.
Rather than purchase feedstock from across the country, UP Paper is determined to buy recovered fiber for the mill from a couple sources that primarily are located in the Midwest, he says.
“We’re focusing on getting material from one or two sources, which we call our partners, not buying it from all over the U.S.,” Dannberg says. “We are not going to be buying from East Coast to West Coast, which is different than in the past.”
He says converting to kraft paper production allows UP Paper to operate with less equipment than was required to produce printing and writing grades. This resulted in at least 20 percent savings in energy costs, Dannberg says.
UP Paper also will end up employing about 40 fewer people than the former mill’s 140 workers. However, Dannberg notes that most positions under the previous owner were administrative.
“We are running the company different than the previous owners,” he says. “We’re trying to make it as simple as possible, running as lean as possible.”
_fmt.png)
UP Paper converted the mill’s existing newsprint machines to produce other paper products, joining numerous companies in the newsprint sector that have converted their operations or shut down their newsprint machines.
Rooted in newsprint
The UP Paper mill’s roots are in newsprint. Opened in 1920 as Manistique Papers Inc., the pulp and paper mill was a longtime dream of W. J. Murphy, who owned the Minneapolis Tribune, according to a 2011 write-up on the company’s history that Dannberg provided. The site was purchased from the Consolidated Lumber Co. and sits along the Manistique River.
The mill began recycling fiber in 1959. In 1984, Manistique Papers shut down its wood processing operations and converted to 100 percent recycled paper furnish, the write-up states.
The mill changed hands several times over its nearly century-old history. In 1991, Montreal-based Kruger Inc. acquired the mill and completed a $13 million upgrade to a deinked pulping system. Fifteen years later, Kruger sold Manistique Papers to a holding company made up of private equity firm Merit Capital Partners, as well as of minority shareholders DDFKD Investments LP, owned by Don and Dennis Kramer, who also owned Remark Paper Co. Inc. The Kramers filed for Chapter 11 bankruptcy protection in 2011.
“They went into bankruptcy because the waste paper prices had skyrocketed, and they didn’t have enough cash to continue,” Dannberg says.
The write-up clarifies his point: “The cost of raw material had increased $1 million per month, impacting the bottom line of the company. During the same period, economic conditions caused our orders to drop below the budgeted levels.”
This decline in orders resulted in excess inventory and lost revenue, the write-up states.
Local management then sought a lender. They found their solution in mBank, a local bank that agreed to purchase the debt from the existing lender, RBS Citizens, along with financial support from the state of Michigan and the Michigan Economic Development Corp. (MEDC). MEDC provided up to $5 million in loans.
The Pioneer Tribune reported in 2012 that seven months after the bankruptcy filing, Manistique Papers agreed to sell to Watermill Group, a Boston-area private investment firm that also owned FutureMark. Watermill Group, Pioneer Tribune reported, had been involved in more than 100 transactions at the time with a total value of more than $4.1 billion.
The company also operated the FutureMark Alsip, Illinois, paper mill, which was shuttered in 2014. At the time of its indefinite closing, Stephen Silver, CEO of FutureMark, cited challenging market conditions in the North American coated paper market as the key reason for closing the mill.
In announcing the closure plans, FutureMark said Alsip was the only facility in North America making coated publication and printing papers predominantly from recycled materials.
“We explored many options to avoid this action,” Silver said, “but the brutal reality for all coated paper manufacturers today is that falling demand and pricing pressure from lower-quality uncoated substitutes has driven prices to near historic lows. Combined with massive increases in energy costs over the winter, this pricing pressure has made it impossible for us to continue our Alsip operations at this time.”
Dannberg points to inefficiencies under this ownership structure that led to the end of FutureMark’s Manistique mill in spring 2015. “They tried to do everything for everyone … Manistique tried to produce yellow paper in the morning, blue or white paper at night, so they had very poor uptime and poor yield then,” he says.
“Sometimes it’s good to take a step back and take your time.”
Successful startup
UP Paper opened in June 2016. The mill has the capacity to produce about 120,000 tons of kraft paper products per year. Dannberg, who refers to the plant as “a diamond in the rough,” says the mill has achieved 93 percent uptime. It runs around the clock, with workers managing three shifts, and plans to move to four shifts soon.
“We have had a tremendous, good startup,” he assures. “We started out slow, and that was also in our plan. We’ve steadily increased volumes, and we’ve mainly produced for orders, not inventory.”
_fmt.png)
Incoming doubled-lined kraft (DLK) and old corrugated containers (OCC) arrive by truck or by rail. Material moves by conveyor to the pulper, then to the dispersion system before being pumped into a chest that goes into the paper machine.
Dannberg explains, “On the paper machine we produce paper, and then we go into the packaging area and make a roll of it, put the label on it and bar code it and send it by truck or rail to our customers.”
UP Paper has more than 70 converters currently buying its brown paper. (“Which is huge in less than a year,” Dannberg says, considering the company had to build a new customer base.) These converters make products such as brown bags used in fast food packaging as well as packaging that is used in place of expanded polystyrene (EPS) foam for shipping. When people shop at Nordstrom Inc., they leave carrying a bag with twisted handles that are made from UP’s kraft paper.
“The bag itself is heavier and is not made from our paper,” Dannberg clarifies.
Looking positively ahead
As for what’s next for UP Paper, Dannberg is optimistic. He has a vision for creating a closed loop system in which UP would pick up scrap paper generated by its customers, drive the truckloads to Manistique to produce more kraft paper to transport to its customers. Transportation costs are important, he says, and a closed loop setup would minimize these costs by allowing the company to backhaul furnish for its mill.
He says he also sees growth potential in the packaging sector and in UP Paper’s niche grade. “I think this paper grade will be growing with the population in North America,” Dannberg says.
Much of UP Paper’s success Dannberg credits to the company’s employees. The former FutureMark paper mill was a significant source of employment for the city of Manistique. When it suddenly closed, the community felt the effects, he says.
“We started out slow, and that was also in our plan. We’ve steadily increased volumes, and we’ve mainly produced for orders, not inventory.” – Lars Dannberg, UP Paper
“It was a big disaster for the community when it closed,” Dannberg says of the FutureMark mill.
“The people are unbelievable,” he says of the UP Paper’s staff who worked for the former mill. “They showed up in April [2016], didn’t ask what they were going to get in salary and just asked what are they going to do.”
Dannberg adds, “The biggest asset is the workers.”
Many of the mill’s current 80 workers have worked in the mill for years under its previous ownership.
With supportive, hardworking employees and a proven kraft grade, Dannberg says the future is positive—so long as UP Paper can increase its sales levels.
He says, “Going through 2017, we want to be at full capacity and fine-tune things so we can make some real money because in the end this is not a social service, this is a company that wants to take care of the community, but we also want to make money.”
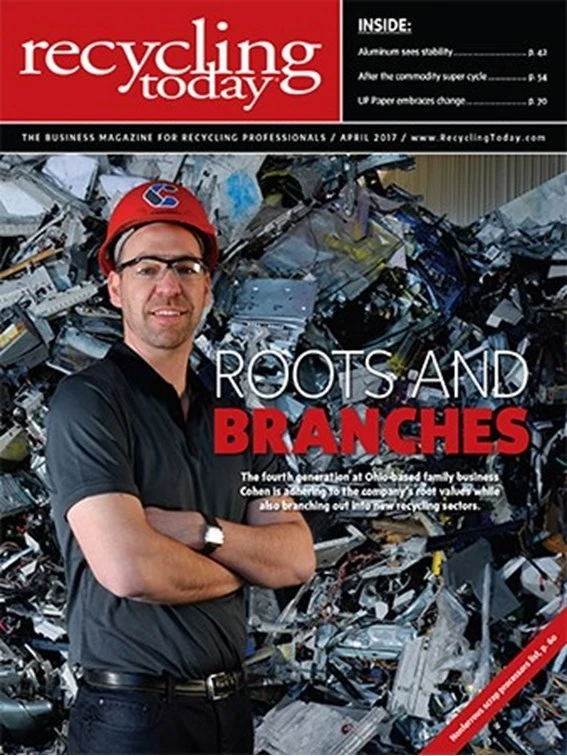
Explore the April 2017 Issue
Check out more from this issue and find your next story to read.
Latest from Recycling Today
- AmSty recorded first sales of PolyRenew Styrene in 2024
- PRE says EU’s plastic recycling industry at a breaking point
- Call2Recycle Canada, Staples Professional expand partnership
- Circular Services breaks ground on north Texas MRF
- Tariff uncertainty results in choppy nonferrous scrap flows
- CATL, Ellen MacArthur Foundation establish battery partnership
- Greif announces price hike for all grades of URB products
- Ascend Elements appoints new president, CEO