
Because of its light weight, durability and malleability, aluminum is highly used in consumer goods, electronics and vehicles. According to Statista, an international research and analysis firm, 62.4 million metric tons of aluminum are expected to be consumed in 2021. Use of the metal is projected to grow at an annual compound rate of 2.6 percent through 2029.
Ellwood Group, an iron castings company based in Ellwood, Pennsylvania, is looking to capitalize on aluminum’s growth. Recently, the company opened a $72 million factory in Hubbard, Ohio, under the name Ellwood Aluminum. The factory produces large-diameter aluminum ingot and billet, rectangular slab and cast plate largely from scrap for customers in the automotive, aerospace and construction industries worldwide. Ellwood Aluminum says it supplies these customers with aluminum ingots, billets and slabs that other producers cannot.
“We’re always looking to reinvest in our company,” says Patrick Callihan, president of Ellwood Aluminum and Ellwood Engineered Castings. “In the last five years, we invested $500 million back into our company to improve operations and expand our company’s reach.”
It started with iron
Brothers David and Jonathon Evans founded the Ellwood Group in 1910. The company started out by forging iron, which it still does. In 1980, the Ellwood Group began expanding its operations with the formation of Ellwood Quality Steels, New Castle, Pennsylvania.
Today, the Ellwood Group employs more than 1,800 people across 10 business units and 25 locations in the U.S., Canada, and Mexico. The company’s business units create products for several industries, including defense, automotive and locomotive. Some of the Ellwood Group’s products include crankshafts, rolled rings and steel.
The privately owned company is run by Bentraum D. Huffman, who assumed the role of president and CEO in 2019.
Ellwood Aluminum is the organization’s newest company. Its plant is a two-phase expansion project next to Ellwood Engineered Castings in Hubbard. The 120,000-square-foot factory can process between 100 million and 120 million pounds (50,000 tons to 60,000 tons) of aluminum scrap annually. The second expansion, which is in the engineering and design phase, will add 180 million pounds (90,000 tons) of melting capacity, Callihan says.
“This plant was built with the aerospace industry in mind,” he says. “So, we produce a lot of aerospace-quality material for planes and rocket ships.”
As of this summer, Ellwood Aluminum employs 30 people and hopes to hire an additional 20 employees, Callihan says. The company has seven metallurgists on staff, including Callihan, to ensure quality.
Running a 12-hour day shift and 12-hour night shift, Ellwood Aluminum uses an automated charging car and skimmer designed by RIA Cast House Engineering, a foundry equipment manufacturer based in Fort Wayne, Indiana, to ensure the safety of its employees.
Ellwood Aluminum produces what it describes as the largest aluminum ingots and billets in North America in addition to rectangular slabs and aluminum cast plates. With dedicated melting and holding furnaces, a casting pit capable of casting product to a length of 360 inches and two 40-ton cranes, the company says it can cast 2,000-, 5,000-, 6,000- and 7,000-series alloys using scrap that it sources directly from scrap yards nationally. Using 1,000- to 7,000-series aluminum scrap, the factory makes aluminum castings that contain 80 percent scrap and 20 percent primary aluminum.

A rocky start
In 2018, the company’s expansion was approved by Hubbard township, and work began on the project’s first phase in 2019.
However, during that time, one of the company’s biggest clients, Boeing, halted production of its 737 Max.
On top of that, the pandemic began just before the facility was completed, which delayed the start of production by three months. Additionally, a saw the company needed to cut the aluminum castings did not arrive at the time of the plant’s opening because it was made by Sermas, a company based in France, and shipping was delayed because of the pandemic. Callihan adds that this delay forced Ellwood Aluminum to rely on other businesses in the area to cut the aluminum castings to size.
When the saw arrived, he says, Ellwood Aluminum employees had issues assembling it because a Sermas representative was unable to travel to Hubbard to oversee the assembly.
As demand for aerospace aluminum rapidly declined in light of the pandemic and its effect on air travel, demand for different grades of aluminum from different sectors sharply increased.
Extrusion companies such as Zarbana Industries in Columbiana, Ohio, were Ellwood Aluminum’s primary customers during the pandemic because of the increase in over-the-road shipping. Zarbana’s extrusions are used to make trailers and tractors, Callihan says.
While demand for aerospace aluminum has increased as air travel rebounds from the lows seen during the pandemic, the company still faces obstacles.
“One of the biggest issues we’re seeing right now is how hard it is to find laborers,” Callihan says. “We have 30 skilled workers, and that’s still below where I would like this plant to be operating. It’s hard right now to find workers, though.”
Callihan says proposed federal legislation, such as the Green New Deal, also concerns him. This is because he’s unsure of the impact such legislation would have on the industry and the changes it would necessitate.
Picking up steam

While the company works to increase staffing at its factory, Callihan says Ellwood Aluminum will continue with the second phase of its development. He says that second phase will include adding a second furnace and casting equipment that will more than double production.
Callihan says Ellwood Aluminum also wants to develop new partnerships in the various industries it serves. It is looking into partnerships to develop aluminum sheeting for the automotive industry as electric vehicle production expands, he says, though it is unclear what form such a partnership could take.
The company also is looking into developing new aluminum alloys to improve material quality for its clients.
“We’re an engineer-driven company,” Callihan says. “We pride ourselves in investing in new equipment that gives us the edge over our competitors.”
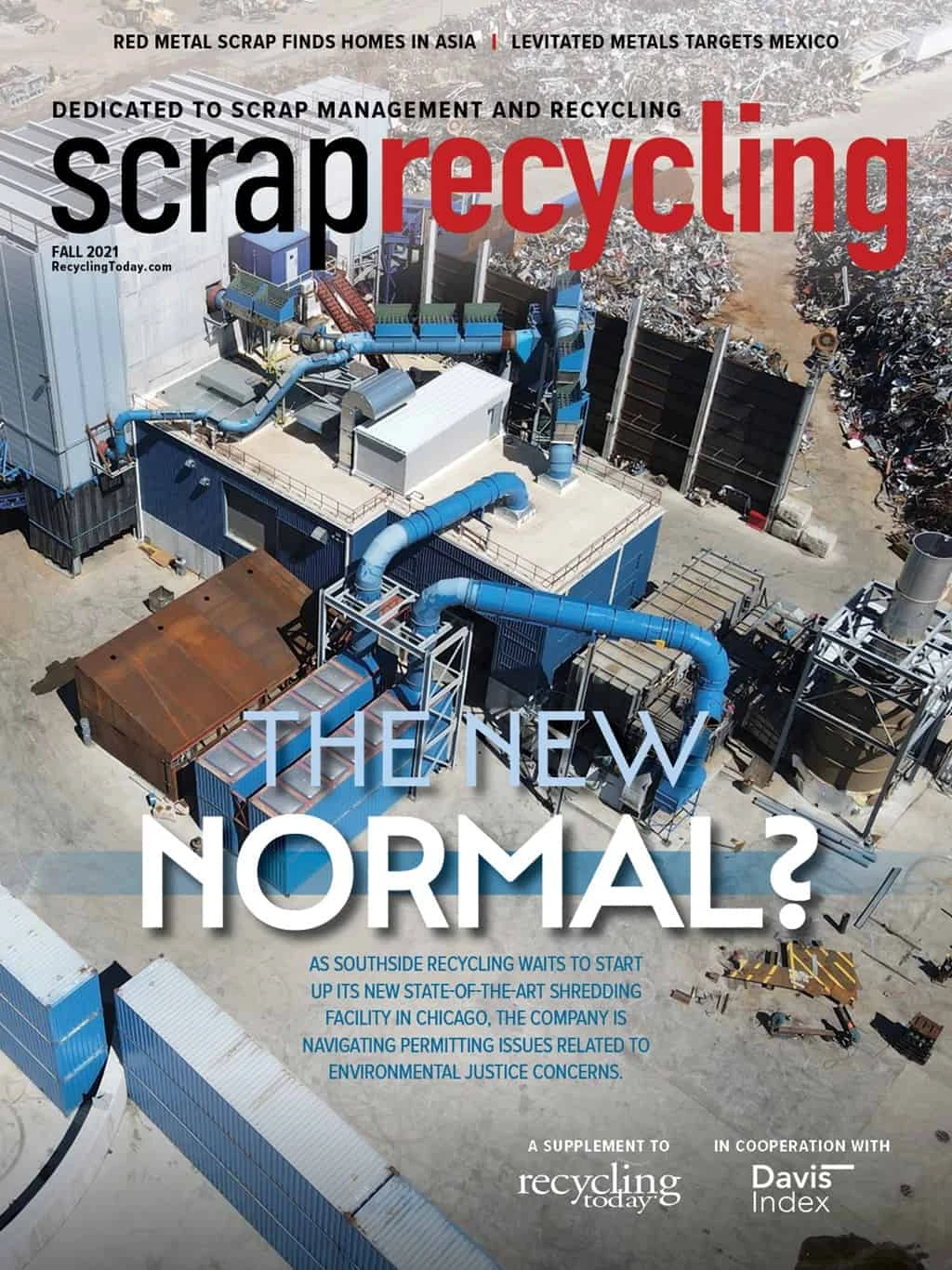
Explore the Fall 2021 Scrap Recycling Issue
Check out more from this issue and find your next story to read.
Latest from Recycling Today
- Lautenbach Recycling names business development manager
- Sebright Products partners with German waste management equipment company
- WasteExpo transitions to biennial format for enhanced experiences
- Study highlights progress, challenges in meeting PCR goals for packaging
- Washington legislature passes EPR bill
- PureCycle makes progress on use of PureFive resin in film trials
- New copper alloy achieves unprecedented high-temperature performance
- Gränges boosts profits and sales volume in Q1 2025