RPlanet Earth opens plastics recovery, recycling plant

RPlanet Earth, previously headquartered in El Segundo, California, has opened its 302,000-square-foot plastics recovery and production facility in Vernon, California, which also now serves as its headquarters. The plant is designed to produce 80 million pounds of food and drink packaging annually using a bottle-grade flake production system supplied by Germany-based Krones that includes a front-end bottle sorting system supplied by Bulk Handling Systems (BHS), Eugene, Oregon.
RPlanet Earth does not sell recycled flake or pellets but processes PET bales and converts them in-house into bottle preforms, extruded sheet and thermoform packaging.
“We really are a technology company,” says rPlanet Earth co-CEO Bob Daviduk. “We’re going to bring technology to bear to improve the way that postconsumer PET is recycled. We’ll have the lowest carbon footprint of any packaging in the marketplace because of the way we’ve put the plant together.”
Earlier this year, the California Department of Resources Recycling and Recovery (CalRecycle) approved a $2 million California Climate Investment loan to rPlanet Los Angeles LLC to help pay for the PET recycling infrastructure at its new facility in Vernon.
Financing from CalRecycle’s Greenhouse Gas Reduction Loan Program will allow rPlanet to transform 1,000 tons of plastic scrap into packaging each year, create 52 new jobs and reduce the equivalent of 1,500 metric tons worth of CO2 greenhouse gas emissions annually.
The automated BHS system processes more than 6 tons per hour (tph) of baled postconsumer polyethylene terephthalate (PET) and runs nearly 24 hours a day, according to a news release issued by BHS.
BHS says the system employs BHS screens, Nihot air, NRT optical and Max-AI robotic sorting technologies to produce a clear PET product for further processing. Five NRT optical sorters with In-Flight Sorting technology remove metals, mixed plastics and colored PET and positively sort clear PET. The Max-AI AQC-2, an artificial intelligence-directed robotic sorter, uses a camera, neural networks and two robots to autonomously perform the final quality control (QC) process.
BHS also supplied the plant with its recently launched Total Intelligence Platform, which automatically processes information from the system’s controls system and motors, optical and Max-AI equipment, scales, baler and other sensors to provide an information and analytics platform.
The plant recovers aluminum and other metals and mixed plastics for further processing by other companies.

Agilyx, AmSty plan joint venture
Agilyx, an environmental technology and development company in Tigard, Oregon, has signed a letter of intent with AmSty, a The Woodlands, Texas-based integrated producer of polystyrene and styrene monomer. According to an Agilyx news release, the companies plan to form a joint venture that will assume operations of Agilyx’s polystyrene (PS) recycling facility in Tigard and pursue the development of a 50-ton-per-day PS recycling facility at a location to be determined.
The Agilyx process converts used PS products back into their original liquid styrene monomer form. Agilyx reports that new PS products can be made from this recycled styrene monomer without degradation of quality or value.
In August 2017, AmSty and Agilyx announced an agreement to process recycled styrene monomer from Agilyx’s Tigard facility and AmSty’s styrene monomer plant in St. James, Louisiana.
“Agilyx is very excited to expand our relationship with AmSty,” says Joe Vaillancourt, CEO of Agilyx. “This joint venture will greatly advance the circular economy for postconsumer polystyrene waste and reflects the confidence and support by industry for our technology platform.”
“We are excited to work with Agilyx as we continue to improve our PolyUsable process, assuring polystyrene remains a viable and growing component of the circular economy,” says Brad Crocker, president and CEO of AmSty.
Schupan invests $10.1 million in expansion
Kalamazoo, Michigan-based Schupan & Sons Inc. is expanding at two locations in that city, investing an expected $10.1 million.
The project will increase manufacturing capacities and add office space to Schupan Aluminum & Plastic Sales’ current location.
Kendra Townsend, Schupan’s marketing and communications manager, says the sales division expects to add more than 40,000 square feet and an additional 50 employees over the next three years.
The aluminum and plastic service center specializes in a full line of new aluminum and plastic mill products. The manufacturing department “utilizes state-of-the-art technology, producing complex components for the medical device, aerospace and office furniture industries,” according to the company.
Schupan Electronics Recycling also will be expanding its Kalamazoo footprint, adding 80,000 square feet of processing space and an additional 30 employees over the next three years.
The electronics recycler is nearly tripling its current size, with room to add more processing equipment as it expands services to its growing customer base.
Get curated news on YOUR industry.
Enter your email to receive our newsletters.
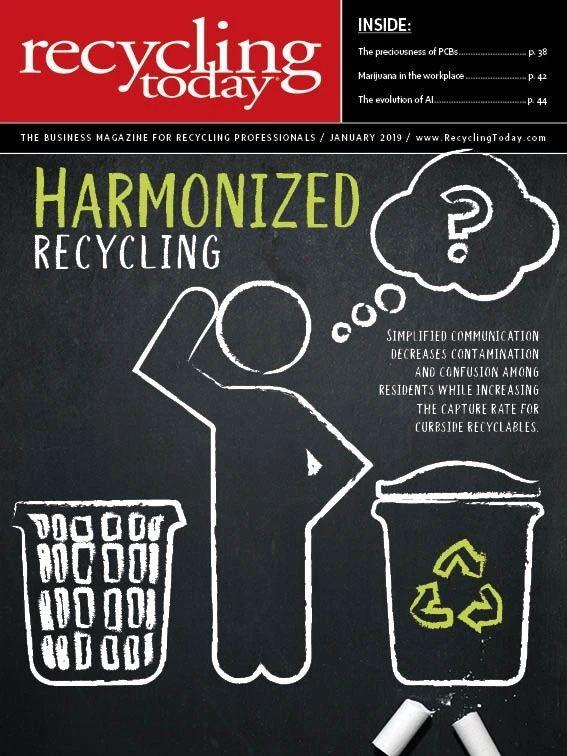
Explore the January 2019 Issue
Check out more from this issue and find your next story to read.
Latest from Recycling Today
- ReMA opposes European efforts seeking export restrictions for recyclables
- Fresh Perspective: Raj Bagaria
- Saica announces plans for second US site
- Update: Novelis produces first aluminum coil made fully from recycled end-of-life automotive scrap
- Aimplas doubles online course offerings
- Radius to be acquired by Toyota subsidiary
- Algoma EAF to start in April
- Erema sees strong demand for high-volume PET systems