
Change can be hard, but that hasn’t stopped Ecovery LLC and CEO Brock Norris.
The family-owned and -operated company got its start in 2008 as an electronic scrap recycler before reinventing itself into a global player in aluminum and copper processing, enjoying steady growth over 16 years from its 65-acre campus in Loxley, Alabama.
The company’s campus houses multiple processing lines, fabrication and melt shops, with Ecovery recently opening an X-ray sorting plant for aluminum. In October, it commissioned a 60,000-pound-capacity secondary aluminum furnace—its second on-site—to meet the growing need for remelt scrap ingot (RSI), dross processing and aluminum tolling services.
In addition to its processing capabilities, Ecovery has a trading division that helps connect suppliers and consumers of various scrap metals across multiple continents. The company’s proximity to Alabama’s Port of Mobile, a 15-minute drive from its headquarters, has allowed for the large-scale growth of physical material being imported to and exported from the Loxley campus. Also, Norris says Ecovery’s positioning, adjacent to the intersection of two major highways, has made East-West and North-South domestic shipping easy for suppliers and consumers.
A fourth-generation entrepreneur whose roots trace back to 1931, when his family founded Assumption, Illinois-based John Deere farming equipment dealer Sloan Implement and diversified into manufacturing products such as chicken feeders, plastics and decking, Norris says his family’s proven track record in manufacturing has helped inform Ecovery’s shift.
“We’ve always run Ecovery with the mindset of adaptability to change where there is opportunity,” Norris says. “Being an entrepreneur is not the easiest, that’s for sure. Adjusting to changing markets and plans can definitely be scary, and there’s plenty of risk, but there’s calculated risk with that as well. And we’ve got a proven track record. ... I think the family expertise in manufacturing has been huge for us on the operations side of things, and that’s really allowed us to scale this business.”
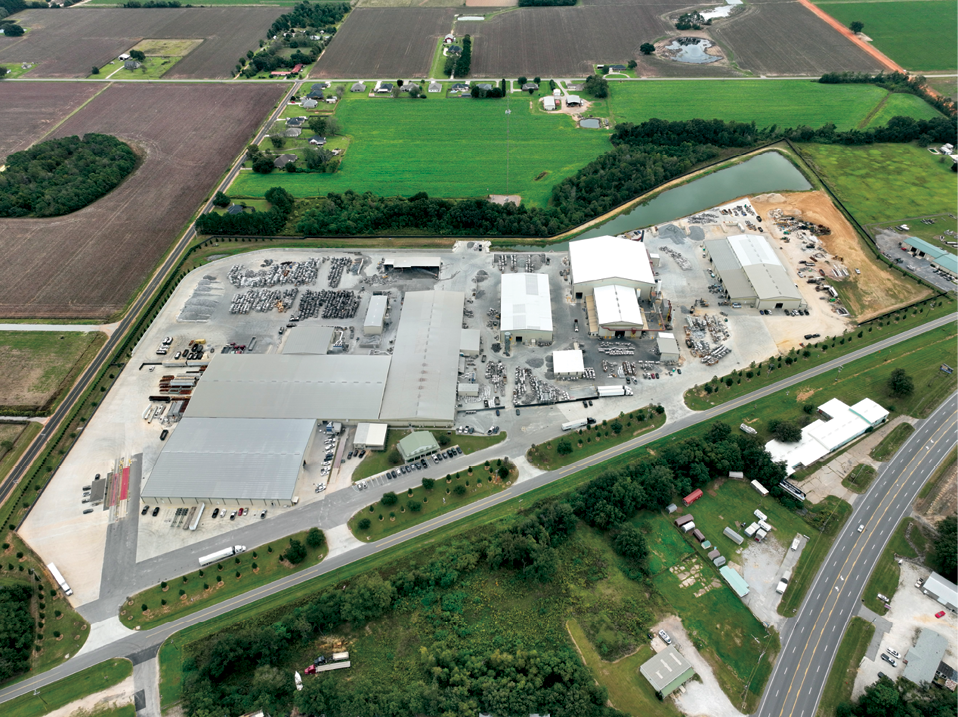
Making transitions
Ecovery began in 2008 as a seller of European scrap recycling equipment that also processed e-scrap using those same machines. Until 2013, the company regularly processed items such as computers, printers, fax machines, TVs and more sourced primarily from customers based in the Midwestern and southeastern U.S.
Seeing limited scalability and opportunity in the e-scrap market, the time came for a change in the business model. In 2013, Ecovery began to move away from processing e-scrap and started processing nonferrous metals, with aluminum copper radiators (ACRs) serving as the primary input.
“At that point in time, we had to figure out who we were going to be and how we were going to not only survive but thrive in this industry,” Norris says. “By 2014, we 100 percent got away from processing e-scrap and dedicated ourselves to processing ACRs, which were mostly all being exported overseas at the time.”
However, 2015 brought difficult scrap market conditions, and Ecovery chose to diversify the company’s offerings from its two products, copper chops and aluminum shred, adding a melt shop to provide RSI to aluminum mills that were no longer eager to buy aluminum shred. The 20,000-square-foot plant was commissioned in 2016.
By 2017, Norris says the company’s focus was to be one of the biggest ACR consumers in the U.S. and globally. “We were increasing our processing lines, increasing our capacity; we were able to really provide the forms and products mills wanted and needed,” he adds.
The plan was a success, and in 2019, Norris expanded Ecovery’s commercial team while, for the first time, capitalizing on international markets with the help of the nearby Port of Mobile.
“Prior to 2019, we hadn’t engaged in any international activities,” Norris says. “The Port of Mobile is only 15 minutes west of us and is a pathway to offer our products and services to Asia, Europe and South America. There were so many other markets that we could explore around the world. ... That was super pivotal to us because that gave us so many opportunities to geographically expand our supplier reach and diversify our consumers.”
However, in 2020, Norris noticed two issues of concern: Ecovery had scaled its business significantly over the years, but its focus was only on ACRs.
“That started becoming a little concerning to me for the sheer fact that when you’re dealing with one input raw material and market conditions or supply and demand weaken, there could be some concerns or challenges,” he says. Additionally, Ecovery saw a decrease in the yield of radiators because of original equipment manufacturer substitution. With copper rising on the terminal markets, the metal was a big cost factor for radiator manufacturers and engineers looking for ways to create them at lower input costs.
“We started seeing that aluminum copper radiators going into HVAC units were being replaced with aluminum radiators or lower-copper-content tubing,” Norris says. “We wanted to really start thinking forward with how we would further reinvent this company, what the company would look like in 2024, 2028, 2030 and how we would continue to scale this campus.”
By 2021, with a broad domestic and international footprint, Ecovery looked to help its suppliers and consumers find solutions for their scrap by establishing a trading division.
Earlier this year, the company commissioned its 25,000-square-foot aluminum X-ray plant, and in October it commissioned its second rotary furnace, which is housed in an additional 40,000-square-foot melt shop.
By 2026, Norris says Ecovery plans to add a third furnace.
“We anticipate demand and opportunities ahead, and we’re going to want to be able to see those opportunities through. We’ve developed this campus with a focus on diversification, and our goal is to collaborate with and support our existing customers as well as the many domestic mills that are currently operational or will soon be.” – Brock Norris, CEO of Ecovery LLC
Current scope
Using 400,000 square feet of processing space across its growing campus staffed by 125 team members, Ecovery now is able to take the variety of material it procures from around the world to produce a wide variety of aluminum and copper products and alloys based on customer demand.
It provides products to a number of different sectors of the recycling industry, including No. 1 copper chops; 3000, 6000 and 2000/7000 aluminum shreds; deox 70 and deox 95 briquettes; aluminum pucks; and 1100, 3000 and 380 RSI. Materials the company purchases include clean and irony ACRs and radiator ends; clean and irony all-aluminum radiators; mixed and painted low-copper clips; painted aluminum siding; 1100-, 3000-, 5000- and 6000-grade scrap; used beverage containers (UBCs) and material recovery facility UBCs; white dross; zorba; and twitch, among others.
To perform its work, Ecovery uses an array of shredders, processing lines, X-ray technology, furnaces, pucking machines and briquette lines.
“That’s some pretty cool technology, and it seems to continue to be growing on a regular basis,” Norris says of the X-ray sorting plant, which is designed to supply furnace-ready aluminum shred to rolling mills in the Southeast and Midwest. “We’ve had some fun with that one. So far, so good.”
Ecovery uses its fabrication shop as a research and development (R&D) hub, where it builds much of its own equipment, such as hammermills, granulators and conveyors, as well as fabricating its own processing lines.
“We have 15 team members at the fab shop not only consistently working on our equipment but continuously making process improvements to reduce downtime, costs and improve results of our products,” Norris says. “It’s truly R&D for us, which we have found to be very beneficial.”
As a scrap metals importer and product exporter with customers in the U.S. and abroad, Ecovery also uses its own fleet of trucks, vans and chassis to help many of its materials reach their destinations.
With the commissioning of its new rotary furnace, the company will be able to increase its melting capacity and expand the dross processing and toll conversion services it can offer its customers.
Norris says the company’s diversification has come at a great time as new aluminum production capacity is set to come online in the U.S. For example, Atlanta-based aluminum manufacturer and recycler Novelis Inc. is constructing a rolling and recycling plant in Bay Minette, Alabama—about 20 minutes from Ecovery’s campus. Approximately four hours away from Ecovery’s location, in Columbus, Mississippi, Steel Dynamics Inc. is building its first recycled-content flat-rolled aluminum mill.
“We anticipate demand and opportunities ahead, and we’re going to want to be able to see those opportunities through,” Norris says. “We’ve developed this campus with a focus on diversification, and our goal is to collaborate with and support our existing customers as well as the many domestic mills that are currently operational or will soon be.”

Family and the future
Ecovery’s structure is family-oriented. Norris’ uncle, Kevin Sloan, serves as chairman of the board; and his father, Walter Norris, manages its processing plant. Brock’s brother, Nathan Norris, is the company’s chief operating officer; and his cousin, Ethan Sloan, manages the melt shop. His nieces and nephews also have entered the business in accounting and quality, health, environmental and safety roles at Ecovery.
“It’s really great,” Brock says of his family members’ involvement. “Everybody has their place, and everybody has their expertise, and we all respect that. We’ll have a common theme and common goal, and all the team members do, too.
“It’s a small, family-owned business, and there’s quite a bit of family members [on staff]. But every single one of the people who works with us is on a mission to help grow this company, and we’re all in it together, which is pretty cool.”
Though Ecovery aims to install a third rotary furnace in 2026, its current plan is to focus on R&D and continue ramping up production in its newly commissioned furnace and X-ray plant.
To Norris, the company’s versatility and forward-thinking mindset, developed over years of reinvention, have helped set it apart in the industry.
“Our goal is to provide our customers with any shape or alloy they want,” he says. “We want to be supportive in the [customer] relationship and scale that relationship with the consumer so that we can supply them with recycled materials and provide a scrap/dross tolling service at the same time. A true partnership. We aspire to be a partner with the mills, supporting them as they scale their operations.”
![]() | The Garden Center Conference & Expo, presented by Garden Center magazine, is the leading event where garden retailers come together to learn from each other, get inspired and move the industry forward. Be sure to register by April 17 to get the lowest rates for the 2025 show in Kansas City, Missouri, Aug. 5-7.
|
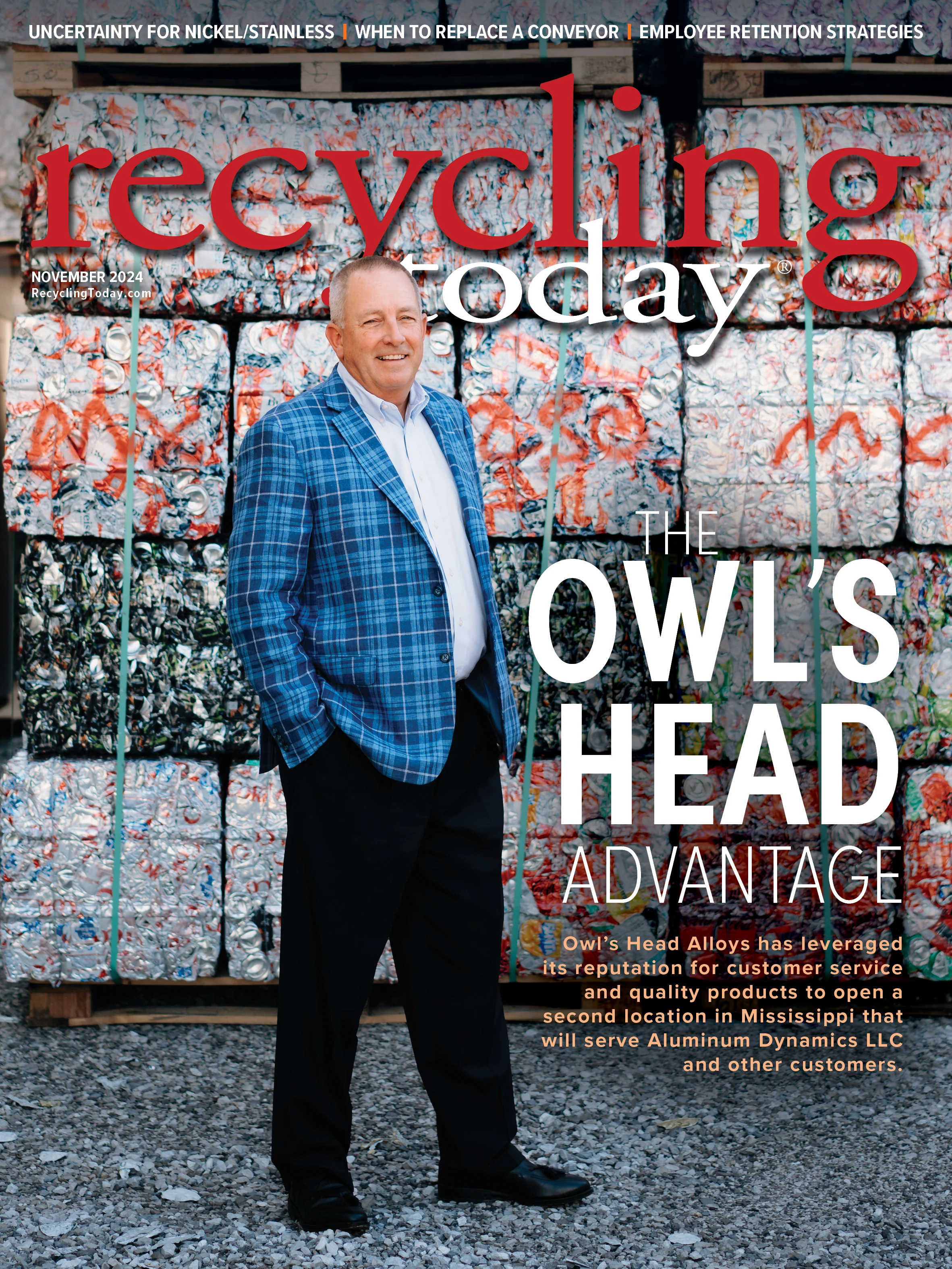
Explore the November 2024 Issue
Check out more from this issue and find your next story to read.
Latest from Recycling Today
- ReMA board to consider changes to residential dual-, single-stream MRF specifications
- Trump’s ‘liberation day’ results in retaliatory tariffs
- Commentary: Waste, CPG industries must lean into data to make sustainable packaging a reality
- DPI acquires Concept Plastics Co.
- Stadler develops second Republic Services Polymer Center
- Japanese scrap can feed its EAF sector, study finds
- IRG cancels plans for Pennsylvania PRF
- WIH Resource Group celebrates 20th anniversary