
Ecobat, based in Texas, has roots that trace back more than 100 years to battery production and recycling sites in Europe, North America and other parts of the world. Its assets in the United States include lead-acid battery plants operated by the former RSR Corp.—one of Ecobat’s many predecessor firms.
Although much of the company’s history involved lead-acid battery production and recycling, as early as 2005, Ecobat began collecting and recycling other types of batteries, including lithium-ion units.
Thea Soule, chief commercial officer of the global company, tells Recycling Today Ecobat has been making significant investments to diversify the company.
Soule, who has an MBA from Northwestern University’s Kellogg School of Management, also has 15 years of experience navigating global commodity markets in a previous role at a large agribusiness, having focused on investments and divestments, risk management, capital structure and allocations, process improvement and supply chain system implementation.
Soule makes it clear that Ecobat does not intend to leave lithium-ion battery recycling solely to venture capitalists. Instead, it is investing to secure a lasting role as it applies its institutional metals recycling and reverse logistics knowledge to the electric vehicle (EV) battery materials recycling sector.
Recycling Today (RT): What portion of the lithium-ion battery stream does Ecobat intend to address with a circular model? EV battery packs specifically, or also smaller batteries?

Thea Soule (TS): Ecobat is the most integrated battery recycling service provider in Europe today. We currently perform in-house collection of critical and end-of-life batteries, which includes transportation, diagnostic/discharge and shredding. We dismantle, reengineer and shred collected materials, turning them into black mass that can be reused in the market.
Ecobat’s process is designed to accept all formats of lithium-ion batteries. With global efforts to meet Paris Agreement commitments, EV batteries are likely to soon represent the largest category of used batteries. Ecobat enables circularity of the complete lithium-ion supply chain by recovering valuable materials from any type of lithium pack.
RT: To what extent is Ecobat applying knowledge gained in the lead-acid battery collection and recycling process to lithium-ion batteries?
TS: Ecobat has been operating in the lead battery recycling industry for nearly 90 years, and today we fully recycle over 120 million used batteries each year. There are logistical challenges for operations at this scale, and much of it can only be solved with experience.
Ecobat continues to be the world’s leading lead-acid battery recycler, and we are applying our knowledge and systems to batteries of other chemistries, such as lithium-ion batteries, that power everyday lives more efficiently. Our unique knowledge and experience around metal extraction and transporting hazardous waste position us to be leaders in the fast-growing lithium-ion battery recycling space.
RT: To what extent will Ecobat’s initial recycling activities be focused on Europe, or to what extent are efforts already underway in North America?
TS: Ecobat has facilities all over the world, having operated for nearly a century in the battery recycling space.
Ecobat’s fastest growing business segment is lithium-ion battery recycling. We have lithium-ion battery recycling facilities in the United Kingdom and Germany, as well as a state-of-the-art research and development facility in Dallas. More lead and lithium-ion battery recycling facilities are forthcoming to help us address growing demand.
We began lithium-ion battery recycling in Europe as it was the logical geographic choice to focus, based on the local maturation of the EV market.
RT: Does Ecobat see several different types of recycling and refining technologies as necessary for a thoroughly closed loop? If so, how many techniques is it piloting or testing?
TS: The lithium-ion recycling industry is in its infancy, and new, innovative technologies emerge on a regular basis. As these technologies are commercialized and scaled, Ecobat’s focus is on maximizing the recovery of materials.
As part of Ecobat’s technology portfolio, we can measure the health of end-of-life batteries, keeping batteries in operation longer for second-life applications.When a battery can no longer be used practically and safely, Ecobat’s proprietary process separates the valuable materials into a high-purity output stream that is processed using any number of innovative refining techniques. The rest of the battery’s recovered materials (aluminum, copper, steel) are separated and sorted into their own streams and are recycled by traditional metal smelting.
Ecobat can choose the most efficient process to achieve maximum recovery rates for all lithium-ion batteries.
RT: Does Ecobat have alliances with collection networks, technology providers and other collaborators in North America? What time frame is needed to meet the region’s needs?
TS: Through our leadership in the [Chicago-based Battery Council International], along with our partners at the U.S. Department of Energy, Ecobat is at the forefront of battery life research and development efforts. We are also part of the Consortium for Battery Innovation and work alongside the industry’s best and brightest. We operate alongside our partners with 2030 to 2040 EV and utility infrastructure-related benchmarks in mind, set out by EV-focused regions throughout the U.S. and Canada, in addition to 2050 EV- related goals for new and existing vehicles and grid-related infrastructure.
We are introducing best practices to our partners to provide safe and efficient transportation of batteries, even without uniform regulations across the U.S.
We strongly believe sustainable and responsible battery recycling is critical to create a circular energy economy.
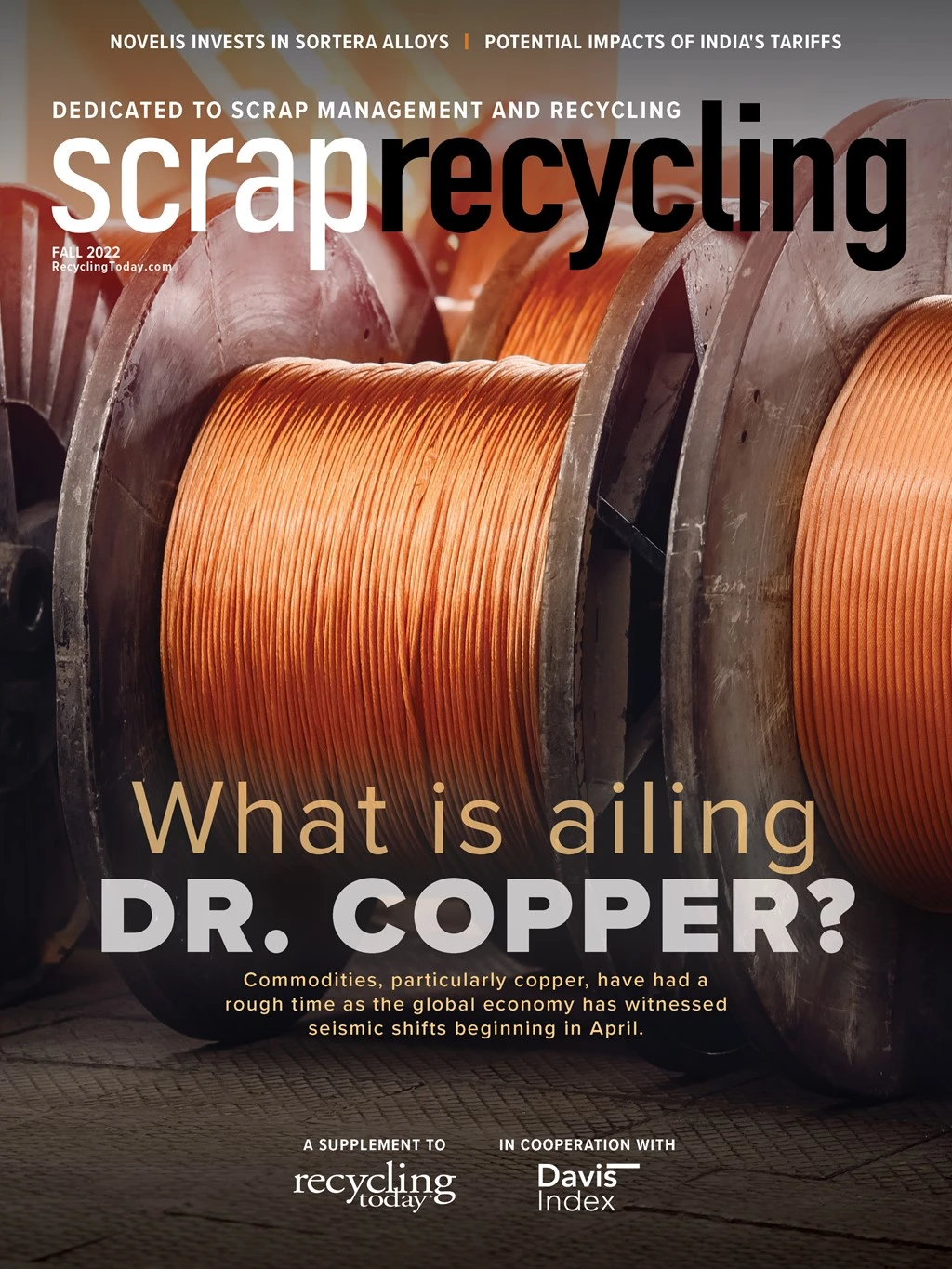
Explore the Fall 2022 Scrap Recycling Issue
Check out more from this issue and find your next story to read.
Latest from Recycling Today
- Green Cubes unveils forklift battery line
- Rebar association points to trade turmoil
- LumiCup offers single-use plastic alternative
- European project yields recycled-content ABS
- ICM to host colocated events in Shanghai
- Astera runs into NIMBY concerns in Colorado
- ReMA opposes European efforts seeking export restrictions for recyclables
- Fresh Perspective: Raj Bagaria