
The consumption of copper is set to grow exponentially over the medium term as the thrust toward renewable energy, electric vehicles and other sustainable initiatives increases. In fact, a recent report by Goldman Sachs estimates copper prices could rise as much as 66 percent to $15,000 per metric ton ($6.80 per pound) by 2025 fueled by increased demand and tight supply of the red metal.
The resultant increase also would brush off on brass, an alloy that mostly consists of copper, zinc and other metals, such as lead. Still, the use of brass could be limited in new environmentally friendly initiatives because of its composition—metals like lead, while recyclable, are deemed to be extremely dangerous especially if not mixed in the right amount.
This is where Eco Brass, an alloy that was first made by Japan’s Mitsubishi in 2000 for rod brass, could prove to be a game-changer.
The beginnings
Up until 2000, brass alloys mostly were bismuth-enhanced and contained lead. Silicon-based alloys were introduced in 2005 but were not well-received by smelters, despite being free of lead.
On the other hand, Mitsubishi realized that Eco Brass, which is also known as 87850 silicon alloy, could be used for the casting process. Still, U.S. smelters chose to ignore this alloy because it was patented, and they would have to pay a license fee to use it.
All this changed in 2005 when Chase Brass, Montpelier, Ohio, bought a master license for the U.S. and let smelters use it, provided they paid a royalty fee. Some producers, such as Los Angeles-based California Metal-X (CMX), did so and have been producing Eco Brass ever since.
Tim Strelitz, owner of CMX, says demand for Eco Brass was slow to pick up, even though its benefits in applications such as producing nonlead rod brass alloys to transport potable water were immediately visible. For example, C360 rod brass has 2 to 4 percent lead compared with zero lead in Eco Brass.
Eco Brass is 76 percent copper, 21 percent zinc, 3 percent silicon and 0.15 percent phosphorous. An alloy that comes close in terms of composition is 87610, which is 90 percent copper, 5 percent zinc and 5 percent silicon.
For five years after Chase Brass, now known as Wieland Chase LLC, first bought the master license for Eco Brass, demand for the alloy remained niche and resulted in extremely slow growth. However, in 2010 the McWane Group-owned Clow Valve, Oskaloosa, Iowa, one of the largest ductile valve producers, allowed CMX to supply Eco Brass as a test.
Strelitz says that on testing, Clow Valve realized not only the environmental benefits of using Eco Brass but also the cost efficiencies of using the alloy—Eco Brass saves from $1 to $1.50 per pound for a component maker.
The benefits not only extended to creating water pipes that did not use lead but also in reduced costs for producers. For example, Eco Brass is around 7 percent less dense than bismuth, which results in a 15 to 20 percent gain on margin and melt cost for producers, Strelitz says. Recoverywise too, Eco Brass scored over bismuth alloys, with the former reporting a 98 to 99 percent recovery with virtually no slag against 92 percent for the latter.
Early adoption challenges
The alloy’s patent meant that producers had to pay more than 2 to 5 cents per pound in royalty and license fees. This increased the cost of Eco Brass by roughly 35 cents per pound compared with bismuth or red brass for the end consumer.
For comparison, when the industry moved to bismuth alloys in 2008-09, they cost around 35 to 40 cents more per pound to produce compared with silicon alloys and 70 cents more per pound than leaded alloys.
The industry also moved to bismuth to save production costs as traditional red brass, which is 85 percent copper, 5 percent tin, 5 percent lead and 5 percent zinc, is more expensive to produce.
Strelitz says that despite the patent costs associated with it, Eco Brass saves millions of dollars when running approximately 500,000 pounds per month. He adds that the net benefit of using this alloy is more than $1 per pound.
Another factor that hurt Eco Brass’ adoption early on was its name. The term brass denotes a higher zinc content compared with tin, whereas in bronze the composition of tin is higher than zinc and, as a result, the latter is considered stronger. Strelitz says this obsession with the word “bronze” continues even today. For example, “aluminum bronze” is a misleading name as the alloy does not have zinc or tin but is perceived to be stronger only because of its name, which has the word “bronze” in it.
Key applications
Today, Eco Brass is mainly used to manufacture water pipes through the casting process. When casting a bismuth alloy, in light of the immense amount of heat generated, the sand used in the process tends to break down quickly. However, while making silicon alloys, the sand runs cold and can last up to three times longer.
Additionally, the phosphorous content in Eco Brass negates the effects of the higher zinc content, allaying the fears that the 21 percent zinc composition of Eco Brass could be harmful, as was previously seen with yellow brass.
The Denver-based American Water Works Association represents between 40,000 to 50,000 power and water facilities in the United States that consume pipes for water, Strelitz says. He adds that these facilities consume approximately 15 million pounds of copper-based alloys per month, of which only 1 million pounds consist of Eco Brass, with CMX, Ontario-based Ingot Metal Co. Ltd. and Wieland Chase producing most of this volume. He says some others produce a tiny percentage of other silicon alloys, such as 875, for the association’s members, with 878 being another silicon alloy that is being produced.
The benefits of Eco Brass
Components for potable drinking water are allowed to contain a maximum of 0.25 lead based on the C903 specification, with the most popular grade for such an alloy being 89833, which mostly carries 0.09 lead and can tolerate up to 0.25 lead.
The 89833 alloy contains 86 to 90 percent copper, 4 to 6 percent tin, 2 to 6 percent zinc and 1.7 to 2.7 percent bismuth, which only comes from lead mining. Most bismuth is sourced from China, which also raises supply chain concerns.
Thus, because of its nonlead composition, Eco Brass is growing in popularity. Strelitz says the market could be looking at a zero-bismuth environment in five to 10 years, especially since the patent for Eco Brass has ended, which will allow more producers to embrace the alloy.
Future demand
The production of Eco Brass is slated to grow as more manufacturers discover its benefits over bismuth and other silicon alloys, the prime examples being manufacturers in Japan as well as Clow Valve in the U.S. that have been successfully using it for over a decade.
It also is well-known by now that the production of silicon-based alloys is much more economical for smelters, and the products made from it, especially water pipes, are the safest to use.Given that Eco Brass uses the same material that is used to cast bismuth and red brass alloys, Strelitz says he believes it will be easy for foundries to switch their operations to use this alloy without spending millions of dollars.
He also says he expects demand for the Eco Brass alloy to grow as more companies, such as competitors of Clow Valve, realize the benefits of using the material and make the switch. Additionally, the large possible outlay in infrastructure spending announced by the U.S. government would benefit Eco Brass users in the waterways, power and renewable energy industries.
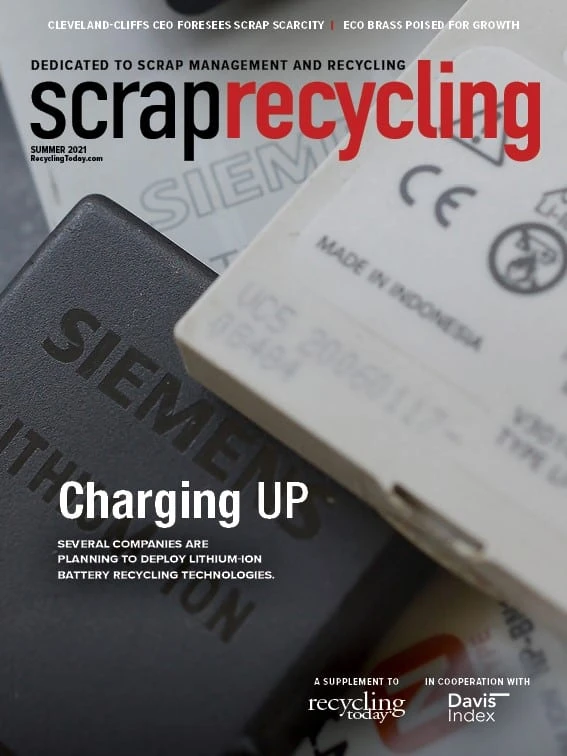
Explore the Summer 2021 Scrap Recycling Issue
Check out more from this issue and find your next story to read.
Latest from Recycling Today
- Redwood partnership targets recycling of medium-format batteries
- Enfinite forms Hazardous & Specialty Waste Management Council
- Combined DRS, EPR legislation introduced in Rhode Island
- Eureka Recycling starts up newly upgraded MRF
- Reconomy Close the Gap campaign highlights need for circularity
- Nickel carbonate added to Aqua Metals’ portfolio
- EuRIC, FEAD say End-Of-Life Vehicle Regulation presents opportunity for recyclers
- Recyclers likely to feel effects of US-China trade war