For many small businesses and municipalities, the decision to recycle is an easy one. After all, it makes sound economic and environmental sense. What’s not so easy is finding a convenient, cost-effective method for temporarily storing and picking up recyclable material.
One recycling company is solving that problem by offering its commercial customers a system in which recyclables are placed in recycling containers that are serviced by front-loader collection vehicles. Though front loaders have long been used to gather solid waste, harnessing them to the task of picking up recyclables is proving popular and is helping account in part for the surging expansion of recycling programs.
ECONOMIES OF SCALE. "Front loaders are being used more and more for collecting recyclables as businesses and others have discovered their convenience," says Michael Benedetto, vice president of TFC Recycling, a family owned enterprise that is based in Chesapeake, Va., and serves areas throughout Virginia and North Carolina.Established in 1973, TFC started using front loaders for recyclable collection a number of years ago to make it easier for commercial customers to recycle. "There are so many situations where a front loader is the ideal piece of equipment to use. They provide a solution for our customers’ needs," Benedetto says. The use of front loaders in recycling has doubled industry-wide, particularly among smaller businesses, school districts and municipalities, he adds.
Before front loaders were adopted for recyclable material pickup, commercial and governmental entities that wanted to recycle often used 30-yard or 40-yard roll-off containers for collecting recyclable material such as cardboard and paper. Although roll offs are still an effective solution in many applications, they’re not always an ideal fit—literally.
A 30-yard roll-off container measures approximately 24 feet long by 8 feet wide by 7 feet high. That kind of bulk demands ample space, something not all operations possess. Roll-off containers also require additional room to permit trucks to get in to pick them up and haul them away. There are other potential disadvantages, too. For example, roll-off containers cost from $3,500 to $4,000 each, and the compactors that are often used in conjunction with them cost about $15,000.
Plus, the compactors require an electrical feed to power them and they need regular maintenance and repair to keep them operating safely and at peak capacity. The sharp blades and powerful rams that allow compactors to perform their job can be dangerous. For some industrial and business situations, that isn’t a problem. But for governmental entities such as school districts, where it might be hard to keep the public away from sites that house roll-off containers and compactors, it’s a safety concern.
These issues are helping to make front-loader recyclable pickup an increasingly popular alternative. The eight-yard containers used in this system cost from $800 to $1,000 each, considerably less than a roll-off container. Much smaller than roll offs, these containers can be placed just about anywhere.
When it’s time to collect the recyclables, front loaders can maneuver into tight spots, and the driver never has to leave the comfort of the cab. He or she can stay behind the wheel while operating the hydraulic fork-arm controls that dump the container and set it back down, ready for immediate re-use. A complete cycle takes less than one minute.
Another benefit offered by front loaders is that they compact the load as they go, permitting about 10 tons of recyclable material to be hauled in one collection vehicle. Though only one roll-off container can be picked up at a time, a single front loader can service many eight-yard bins, potentially making every collection trip more efficient.
OUT IN FRONT. Efficiency isn’t the only attribute of the system. It can be educational, too, as witnessed by the Virginia Beach City Public Schools, a district that serves nearly 71,000 students and features 57 elementary schools, 15 middle schools and 11 high schools. Having previously recycled using 30-yard, closed-top roll-off containers, school officials wanted to convert to a recycling program that would be easier to use and would teach students the value of recycling by directly involving them in the practice.Working with TFC, the district established a pilot recycling program in spring 2006 that was anchored by the use of containers that can be serviced using a front loader. In each classroom are small containers into which students toss paper, cardboard, cans and bottles. At the end of the day, the custodial staff gathers the contents of the containers and deposits them into eight-yard bins for front loader pickup.
The single-stream recycling technology and equipment used by TFC since 1997 permits bottles, cans and paper to be mixed in the same pickup container. The materials are later sorted at the company’s material recovery facility. Students and teachers enthusiastically participate in the program, which was converted to full-scale, system-wide use within months after the pilot project started.
"It gives the students a consistent message," Benedetto says. "It teaches them that you recycle at school, at home, everywhere. And that’s a message that many of them are sharing with their parents."
TFC’s front-loader fleet has blossomed along with the rising popularity of using the equipment for recycling programs. The company relies mostly on Heil Half/Pack front loaders. TFC added two Heil Half/Packs to meet the demands of the Virginia Beach school district program. The company bought another pair of Half/Packs so it could expand commercial recyclable pickup services in the Richmond, Va., and Durham, N.C., marketplace.
TFC’s front-loader fleet now numbers 15 vehicles, and there’s a reason why the majority are from Heil Environmental, Chattanooga, Tenn. "They’re very dependable and reliable," Benedetto says. "Plus, Heil stands behind what it sells, and we’ve gotten great service from our Heil distributor, Mid-Atlantic Waste Systems."
Servicing several hundred commercial customers’ recycling programs with front loaders is a key aspect of TFC’s operations, but that’s not all the company does. The bulk of the company’s business consists of picking up recyclable material from more than half a million homes in its two-state service area. For this task, the company uses 10 rear loaders and 90 side loaders equipped for either manual or automated pickup. TFC collects solid waste, too.
TFC didn’t always rely on the latest high-tech equipment. The Benedetto family got its start in the business in 19th century New York City, using pushcarts to collect rags, newspaper and trash. Today, TFC employs more than 325 people at three plants in Virginia and one in Durham, N.C., too. Each facility serves as a destination for the recyclable materials collected by TFC from businesses, residences and municipalities. TFC’s plants sort and process the material into a state where it can be shipped to end-users domestically and overseas.
TFC stands for Tidewater Fibre Corp., a name that’s based on the company’s original recycling venture, which centered on collecting scrap paper. When the company moved to single-stream collection, it started using the name "TFC Recycling" to reflect the broadened scope, Benedetto explains.
TFC’s business continues to grow.
"We’re now seeing more companies starting recycling programs than we ever have, and I expect the trend to continue," Benedetto says. Front-loader recyclable collection systems are playing an invaluable role in this growth by making recycling convenient and enhancing its cost-effectiveness.
This feature was submitted on behalf of Heil Environmental.
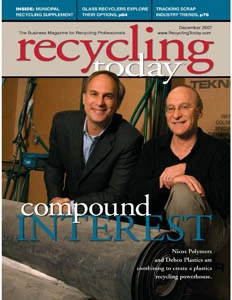
Explore the December 2007 Issue
Check out more from this issue and find your next story to read.
Latest from Recycling Today
- IDTechEx sees electric-powered construction equipment growth
- Global steel output recedes in November
- Fitch Ratings sees reasons for steel optimism in 2025
- P+PB adds new board members
- BlueScope, BHP & Rio Tinto select site for electric smelting furnace pilot plant
- Magnomer joins Canada Plastics Pact
- Out of touch with reality
- Electra names new CFO