There are doomsayers concerning the future of manufacturing in America and there are also optimists. In between are those who see changes that are creating good news for some sectors and regions and difficult times for others.
Scrap recyclers can fall into any of these categories, but no matter where their opinions may lie, they are almost certainly informed opinions.
Driving South? |
The year 1985 may seem like yesterday to fans who recall when the San Francisco 49ers and the Kansas City Royals were at the top of the standings in their respective sports. Or it may seem like eons ago to those who remember when a reformer named Mikhail Gorbachev came to power in a nation called the Soviet Union was headline news. For scrap recyclers, it may be noteworthy because it marked a time when states such as Tennessee, Alabama and Cohuila (Mexico) were not among the top 10 assemblers of passenger vehicles. In 1985, transplant companies were just barely on the map, with Honda’s Marysville, Ohio, plant helping the Buckeye State finish second overall by producing some 1.9 million vehicles that year (behind only Michigan), according to figures collected by Wards-Auto.com, Southfield, Mich. Ten years later, with additional Honda plants as well as Nissan and Toyota assembly complexes online, Kentucky’s vehicle production doubled to nearly 1 million, allowing it to move to No. 4 on the list. Tennessee was now in the top 10 at No. 6, and California was also visible at No. 9. By 2004, Cohuila had entered the top 10 at No. 8, while Kentucky was now producing more than 1.1 million vehicles annually. The big news in 2004 was Michigan falling out of its traditional No. 1 spot—but not to a Sun Belt state. Rather, the province of Ontario, benefiting in part from a weak Canadian dollar, produced 2.7 million vehicles to grab the top spot. By 2008, Alabama is projected to enter the top 10, as production ramps up at transplant factories in that state. |
Serving industrial accounts is a critical activity for most recyclers. The manufacturing sector produces grades of scrap that are clean and desirable for steel mills, foundries and smelters as well as tons of old corrugated containers that are a bankable bulk commodity for paper recyclers.
Often, the biggest source of concern for recyclers has been the flight of manufacturing from within the United States to other parts of the world. The same recyclers who were losing industrial accounts because of plants relocating to Mexico during the 1980s and 1990s are now seeing other customers move to China.
The causes and effects of this condition are subjects of debate carried out regularly in the media (and of previous features in this magazine) and they mirror a similar perceived migration within the United States.
The Sun Belt vs. Rust Belt economic phenomenon has been observed for decades. Statistics are available, and so are the informed opinions of scrap recyclers who take part in these industrial markets each day.
Both the statistics and the experience of recyclers help indicate to what extent the geographic center of the scrap industry in the United States has moved perceptibly south in the past several decades.
No Spin Zone |
In addition to automobiles, the production of large appliances generates steel stampings and other industrial scrap that can flow through the yards of scrap recyclers—often in Northern states like Iowa, Ohio and Michigan. As the production of household electronics has migrated overseas in the last three decades, recyclers must be wondering how vulnerable the large appliance segment is as well. To what extent Asian goods could potentially supplant large appliances made domestically by familiar household names in this sector became an issue in 2005 with the proposed purchase of Maytag Corp., Newton, Iowa, by the Quingdao Haier Group, China’s largest appliance maker. Subsequently, Maytag has instead agreed to merge with Whirlpool Corp., Benton Harbor, Mich., in a deal that is still being examined by the U.S. Justice Department for anti-trust ramifications. The aforementioned Haier Group is, in the meantime, building a $40 million factory in Camden, S.C., (a Sun Belt locale) to produce refrigerators for the North American market. |
SOUTHERN HOSPITALITY. History textbooks covering the U.S. Civil War often observe that while the Southern side had better tactical commanders, and in fact won far more battles than it lost, it ultimately could not overcome the overwhelming industrial might of the North.
Since very early on in English-speaking settlement patterns, the Southern colonies (and then states) focused on agriculture to take advantage of a longer growing season while the Northern colonies embraced the metallurgical and production advances of the Industrial Revolution as they happened.
These roots created an imbalance in manufacturing infrastructure that lasted well beyond the Civil War and into the post-World War II era.
But in the past several decades, capital has worked its way south in search of non-union labor and access to growing population centers in the South, creating a pattern of industrial growth in many parts of the South and stagnation (or even retreat) in the North.
As one might expect, the geography of the scrap industry has changed as part of the wider pattern.
Statistics don’t necessarily point to an all-out Southern victory over the North for industrial production, but they certainly point to some notable trends.
In just the brief period from 1997 to 2004, which covered two upswings in the overall economy with a couple of leaner years in the middle, regional disparities can be spotted.
A West Coast View |
A look at Rust Belt vs. Sun Belt economies provides a filter through which to examine the Eastern half of the United States, but where does the Pacific Coast fit into this conversation? John Sacco, president of Sierra International Machinery LLC and also an officer of Sierra Recycling & Demolition Inc., Bakersfield, Calif., says California has not benefited from its location as a gateway to Asia to the extent that it should because of its less-than-hospitable business climate. While noting that the state has an "export-based economy," especially as a provider of scrap, Sacco also notes that Asian companies have not chosen California as a preferred spot to set up U.S. manufacturing operations. "The Chinese are not opening plants here—there is not competitive reason to do so," he says bluntly. Sacco, who is also the current secretary-treasurer of the Institute of Scrap Recycling Industries Inc. (ISRI), says a variety of factors make California a spot that many manufacturers avoid: land is prohibitively expensive, tax rates are high, insurance costs are higher than in other states, and the regulatory climate is oppressive. "It’s not a pro-business mentality here," he remarks. "California is a place where there is regulation at every turn." Additionally, companies entering the U.S. market and locating a first manufacturing facility logically conclude that California is not a central spot through which to tie into the U.S. transportation grid. "They want to be able to easily ship goods north, south east and west," Sacco comments. Despite the obstacles, manufacturing is not dormant in California, and the dollar output of durable goods has grown throughout the past several years. Toyota has assembled more than 4 million vehicles in the state since beginning operations there in 1986. |
But using the value of durable goods produced as a barometer, statistics from the U.S. Department of Commerce show that the regional picture is not one showing prosperity vs. deprivation. (Durable goods include finished products such as autos and appliances as well as some basic materials such as coils of steel.)
Rather, while the Sun Belt regions of the Southeast (17.8 percent growth) and Far West (21 percent) have indeed enjoyed tremendous growth in durable goods activity, regions such as the Great Lakes (12.3 percent) and the Mid-Atlantic (5 percent) are also growing—just not as fast.
If all scrap is indeed local, as many dealers are fond of saying, then breaking durable goods manufacturing activity down by state reveals further winners and losers in recent years.
Among states showing health in this sector, the appearance of mid-South states such as Virginia, Tennessee and South Carolina is no surprise, as these states are perceived as offering manufacturers the combination of available land, non-union labor and a less hostile regulatory environment that they are seeking. Perhaps more surprising is the fact that California remains a net gainer, since many business owners in the Golden State have long complained about the relative hostility of its state government toward manufacturers.
States whose industrial production appears to have stalled includes a couple that may fit the stereotypical Rust Belt geography (Pennsylvania and Illinois), but also a few surprises, including Kentucky—the home of several Toyota plants.
Stating the Differences |
In the span from 1997 to 2004, very few states declined in their production of durable goods, but some have been stagnant. The Revved Up . . . States with marked increases in durable goods manufacturing activity, 1997-2004 State 1997 2004 % increaseIdaho $2.3 billion $4.3 billion 86.0% South Carolina $9.7 billion $13.9 billion 44.3% Virginia $10.7 billion $15.0 billion 40.3% Nevada $1.5 billion $2.1 billion 39.7% Indiana $32.3 billion $42.5 billion 31.6% California $89.5 billion $109.9 billion 22.8% Tennessee $18.2 billion $22.0 billion 21.1% Texas $50.2 billion $59.0 billion 17.7% . . . and the Stalled States with decreases or flat production of durable goods, 1997-2004 State 1997 2004 % increase(decrease) New Mexico $9.0 billion $4.3 billion (52.3%) New Hampshire $6.2 billion $4.8 billion (22.5%) Oklahoma $7.9 billion $7.3 billion ( 7.9%) Kentucky $17.6 $17.4 ( 1.2%) Colorado $9.0 billion $9.0 billion ( 0.4%) Maryland $6.4 billion $6.4 billion ( 0.1%) Illinois $38.7 billion $39.0 billion 0.9% Pennsylvania $34.0 billion $34.4 billion 1.1% |
This recent seven-year window of activity paints a brighter industrial picture for the Sun Belt vs. its Rust Belt counterpart, but not to
This recent seven-year window of activity paints a brighter industrial picture for the Sun Belt vs. its Rust Belt counterpart, but not to an extent that is alarming.
There are concerns, though, that the next few years could demonstrate greater contrast.
NORTHERN EXPOSURE. While many traditional manufacturing regions seem to be remaining viable into this decade, there are new concerns on the horizon because of the struggles of two traditional powerhouses: General Motors and Ford Motor Co.
In 2005, much of the business media attention focused on Ford Motor Co. and whether its CEO William Ford Jr. would be able to help the company avoid bankruptcy.
That question remains in mind for many auto industry watchers, but has been joined in early 2006 by another: Can current General Motors CEO Rick Wagoner avoid a bankruptcy filing for that mammoth company?
The fate of the two companies is a concern for many business owners, but particularly those with a presence in the Great Lakes region, where the fortunes of America’s automakers has long been tied to the health of the overall business climate.
While the bailout of the Chrysler Corp. in the late 1970s may have been a newsworthy development for Americans at that time, it was particularly critical for the company’s workers and suppliers (including scrap service providers) in Michigan and Ohio where Chrysler had a deep presence.
Those same two states, along with several others such as Indiana, Illinois and the province of Ontario, also have the greatest interest in the fate of Ford and GM.
The operations of both companies are global, but their roots and their greatest employment and industrial production presence remains in the Great Lakes region. When market share falls for these two companies, it can have the greatest impact in that region. Conversely, when market share for Toyota, Honda and Nissan increases, it can boost scrap activity in other parts of the nation.
Thus, when a February issue of Fortune magazine carries a cover story entitled "The Tragedy of General Motors," scrap recyclers in the Great Lakes region probably take the greatest interest.
The feature story’s author states, "the evidence points, with increasing certitude, to bankruptcy." Author Carol Loomis concludes that even GM’s late 2005 restructuring plans to close down 12 factories and reduce payroll by 30,000 jobs between now and 2008 cannot overcome the burdens of pension and health care obligations to workers as well as long-term obligations to its dealer network.
Even if progress is made on the cost-cutting front, Loomis writes, "there is a bleak awareness that no companies have ever turned around because of cost cutting alone. The essential partner is revenue growth."
Such a rebound in market share for GM will be tough at a time when SUVs and pick-up trucks are falling out of favor.
Ford Motor Co., meanwhile, has announced a restructuring plan of its own that also involves cutting back employment (25,000 to 30,000 jobs) and plant capacity (up to 14 plants.)
The details of the plant cutbacks are being watched closely by individual scrap recyclers in those market regions. The overall impact of such announcements, however, can be a little more difficult to determine.
In the same issue of Fortune magazine that details the woes of GM and Ford, a full-page ad placed by Toyota Motor Sales U.S.A. is headlined, "The Story of the Plant that Never Stopped Growing."
The plant being referred to is an engine plant in Buffalo, W.Va., which Toyota opened in 1996 that has since tripled in size. As the company notes in the same ad, it is just one of 10 factories now operated by Toyota in the United States, part of $13 billion worth of investment in plant and equipment by the Japanese auto maker.
Lean and Mean |
Without question, the drive for the efficiency needed to compete has been very tough on manufacturing payrolls. The number of jobs provided by the manufacturing sector continues to make up a smaller percentage compared to the service, administrative and professional sectors, even when overall manufacturing production is stable or increasing. While globalization and automation-based efficiency are pointed to as threats to employment, advocates say that embracing these trends is what keeps American manufacturers vital—and thus continuing to produce scrap for the recycling market. In terms of globalization, a 2004 study by economists at Columbia University, New York, and Creighton University, Omaha, Neb., concludes that states that attracted foreign capital greatly helped the manufacturing output totals in their states as well as state economic growth overall. Using data from the year 1999, the study’s authors found that overseas companies did not cluster their capital into Atlantic or Pacific coastal regions. Rather, the states with the highest level of foreign capital as a percentage of gross state product included inland states such as Kentucky, Indiana and Alabama. In the time period studied (1987 to 1999), the states with the slowest economic growth over that period (this included Louisiana, Maine and Alaska) were also in the bottom half in terms of percentage growth in foreign capital. The correlation between manufacturing efficiency and continued health for a business can be seen in looking at another industry with which scrap recyclers are familiar—the steel industry. |
According to the Toyota.com/usa Web site, since moving some of its production operations to America, Toyota has assembled some 4.4 million Camry units, 2.2 million Corollas, 1.8 million Tacoma pick-ups and some 2.6 million other vehicles at plants in California, Indiana and Kentucky.
A similar story can be told by Honda of America, which has booming assembly, components production and supplier plants in Central Ohio, Northern Alabama and other states.
Americans are buying 16 million or more passenger vehicles each year, and most of them are being assembled here, whether the plants are operated by GM and Ford or by Toyota and Honda.
For the scrap industry, that means exterior parts stamping and other activities that generate scrap have continued, although the opportunities can be very different.
As detailed in a story in the December 2005 issue of Recycling Today, ("Blueprint for Success"), several Toyota subsidiaries have joint ownership in Green Metals Inc., a scrap recycler that specializes in serving Toyota facilities in the United States.
Such a closed-loop system can be difficult for traditional recycling firms to penetrate, but the overall picture of how scrap is handled in the "transplant" chain is more diverse.
Forged Steel |
The market share of electric arc furnace (EAF) steelmakers in the United States has improved as these facilities have benefited from a number of factors—including a more flexible labor climate that has allowed them to drive down the number of labor hours needed per ton of steel created. Scrap recyclers have had a front-row seat to the resulting shakeout that this change in technology and efficiency has created within the industry, and to at least one of these observers, what the auto industry is going through now is reminiscent of the steel industry’s recent past. “I spent a lot of my formative years watching Northeast Ohio go through steel industry cuts in the late 1970s that really lasted all the way through the mid-1990s,” says Chip Hering. “And the companies that suffered did so for some of the same reasons that are causing automakers to struggle: very difficult legacy costs compared to their competition, and competition from newer facilities in the South that could hire younger people with lower health care costs and using more flexible work rules. It’s very similar.” The steel industry that has emerged is more consolidated and seemingly more financially fit, but it was not achieved without the reduction of pension and health care benefits and other hardships. “How much of that is going to happen in the auto industry?” asks Hering. “Most folks believe some of the worse side effects can be avoided, but there is going to be some trauma. For the Midwest, it could be even tougher than the last couple of downturns. I think an awful lot of people are holding their breath to see how successful the restructurings at Ford and GM will be.” But Hering says the wrenching changes are necessary. “Overall, manufacturing is viable. We will continue to have a very vibrant auto industry up here. It will just look very different.” |
A.G. (Chip) Hering, executive vice president with Ferrous Processing & Trading Co. (FPT), Detroit, notes that Japanese automakers at first had a tendency to import entire components or to help Japanese-based supplier companies set up a plant near their North American assembly operations. "Initially, transplants brought their own stampers over," he says. "But now they are more accustomed to doing business with North American companies, and you see a greater comfort level."
COMMON GROUND.The automotive plants operated by non-U.S.-based companies have largely been placed away from the Great Lakes corridor, with most of the recent locations being south of the Mason-Dixon line (i.e. BMW in South Carolina, Mercedes-Benz in Alabama and Honda in Lincoln, Ala.)
"[Domestic] tier one stampers who want to see growth are saying that’s where they see it happening—in the South," says Hering.
Joel Denbo, current chair of the Institute of Scrap Recycling Industries Inc. (ISRI) and also vice president of Tennessee Valley Recycling, Decatur, Ala., says processors in his region have benefited from the tendency of transplant automakers to locate their factories in the South. These factories then draw the suppliers who can improve scrap generation.
"Obviously, there has been a shift in industrial production from North to South," says Denbo. He adds, "There has also been an organic growth of industrial production in the South."
He describes manufacturing in the South as being a "mixed bag," since, like the North, the region also has older traditional manufacturing plants that are trying to compete with offshore manufacturers with much lower wages and overhead costs.
"Some of our old-line customers are suffering the same ills as their Northern counterparts because of globalization," says Denbo, "and we’re very concerned about those types of customers. I guess I would say the overall optimism I have for the manufacturing sector is guarded by companies being able to adjust to the current business trends."
Whether competing with Mexico as a manufacturing location in the 1990s or with China in this decade, holding onto manufacturing plants remains a challenge shared by states in the North and the South.
Says Hering, "For the Midwest, it could be even tougher than the last couple of downturns. I think an awful lot of people are holding their breath to see how successful the restructurings at Ford and GM will be."
But Hering says the wrenching changes are necessary. "Overall, manufacturing is viable. We will continue to have a vibrant auto industry up here. It will just look very different."
The author is editor of Recycling Today and can be contacted at btaylor@gie.net.
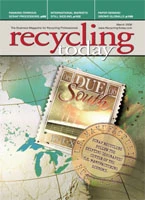
Explore the March 2006 Issue
Check out more from this issue and find your next story to read.
Latest from Recycling Today
- Radius experiences sixth consecutive quarterly loss
- US ferrous market exhibits upward pricing pressure: Davis Index
- Glass Packaging Institute applauds regulation change
- Engcon adds to Tiltorotator line
- Paper recycling is focus of two January webinars
- Disruption likely for material flows in mid-January
- Blue Whale Materials to expand Oklahoma lithium-ion battery recycling plant
- CARI names new president and CEO