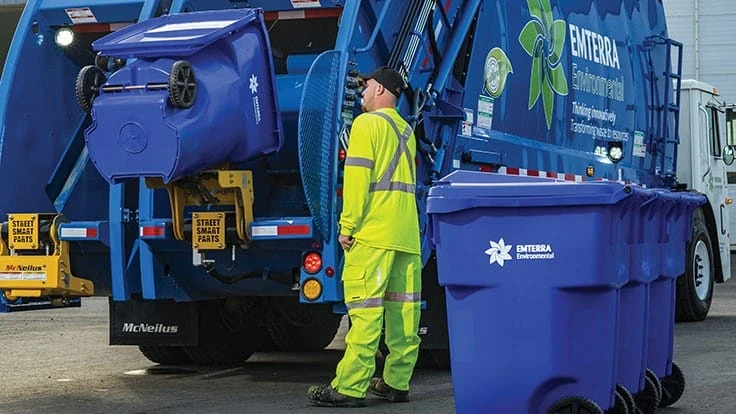
Emterra Group

Emterra Group, a Burlington, Ontario-based waste management and recycling company, says it prioritizes the safety of its employees, customers and members of the communities it serves. This is perhaps most visible when it comes to the hauling services the company provides. Emterra Group has a fleet of nearly 700 trucks and a similar number of drivers who are out on the roadways collecting and transporting waste and recyclables from businesses and residences: a task that comes with considerable risk.
Roger Davis, corporate director of risk management for Emterra Group, is tasked with helping the company manage this risk. He also ensures everyone knows the processes Emterra has adopted. “That is where the training comes in.”
He is supported by a team of four regional risk managers, who work with drivers that need help with on-the-road skills training.
From the start
Davis says, “Waste management is unique and not just like driving a truck to Florida,” referencing the congested areas and people who Emterra’s drivers encounter along their routes. “The risk is significantly high.”
Recruitment and orientation training are key factors in the company’s successful safety record in this area, he says. Emterra has dedicated recruiters for this purpose, with many of the company’s drivers coming from other waste companies, long-haul trucking, medical waste hauling or busing. “We are looking for prior experience,” Davis says. “Our insurance company is pretty adamant about that as well.”
Emterra requires all potential recruits to follow an existing driver so they can observe what a day on the job might look like. He says this happens relatively early in the hiring process. If the job candidate is still interested, the process continues with an interview, license review and drug and alcohol testing.
From classroom to road
“Training is certainly a big component of risk management programs,” Davis says.
Emterra uses a multifaceted approach to driver training that includes classroom training, drive-alongs and online courses.
New drivers with Emterra have a classroom orientation training and are assigned training in CarriersEdge, an Ontario-based provider of online driver training for the trucking industry featuring a library of safety and compliance courses. Davis says defensive driving and equipment operation are focused on in the classroom training. In addition to defensive driving, the online training courses include hours of service, trip inspection and load security.

The company’s regional risk managers have access to the scores that drivers receive in CarriersEdge and can assist those who are struggling in certain areas.
Next comes a 10-day orientation period that involves training with a driver trainer in a truck. This on-road training focuses on specific skills such as backing in, tight turns and on-highway driving. It also addresses operating the trucks’ hydraulics.
The company’s drivers are retrained according to a training matrix that Emterra uses. CarriersEdge automatically assigns the trainings based on the matrix, and certain lessons must be retaken on regular intervals, Davis says.
Emterra also does an on-the-job behavior analysis (OBA) of all its drivers. “Every driver and loader has to have an OBA on file,” he says. Depending on the position, the OBAs are conducted yearly, but most are done quarterly.
Additional trainings for a driver are based on the results of the OBA as well as performance monitoring of speed, hard braking, idling and excessive cornering using the trucks’ GPS, Davis says. “We track that daily and send out reports daily to take action on those things.”
The company’s response to the information captured through the trucks’ GPS amplifies based on recurrence, he says, with the initial response being a discussion with the driver followed by training and then disciplinary action. “It starts with a conversation, and we may have the driver trainer go out and coach.”
“Training is certainly a big component of risk management programs.” – Roger Davis, corporate director of risk management, Emterra Group
Emterra reacts to every incident that is reported through GPS by interviewing the driver, he adds.
Davis says within three months of implementing this approach, the company went from multiple instances that required intervention with the driver to one incident across Emterra’s fleet.
For added safety, Emterra’s vehicles, which include front, rear and side loaders as well as roll-off trucks, are equipped with alarms, collision avoidance technology and backup and side cameras.
From the top
Davis says getting insurance for the company’s vehicle fleet has been challenging, which has been the case for many fleet operators in the waste and recycling sector. Therefore, the safety measures Emterra has taken are viewed as a “prerequisite” by many insurers that “allows them to take the risk of underwriting the business,” he adds.
From Davis’ perspective, he knows Emterra’s approach to driver training has been successful because the company’s related losses have been reduced. Emterra’s carrier profile has improved across Canada, he says, and the company has seen a drop in workers’ compensation cases since Davis joined the company in 2018.
Emterra Group’s safety program is supported from the top down, Davis says, adding that the company is focused on measuring the results of its risk management programs. “Measurement keeps management engaged,” he adds. “When the boss thinks it’s important, it’s important.”
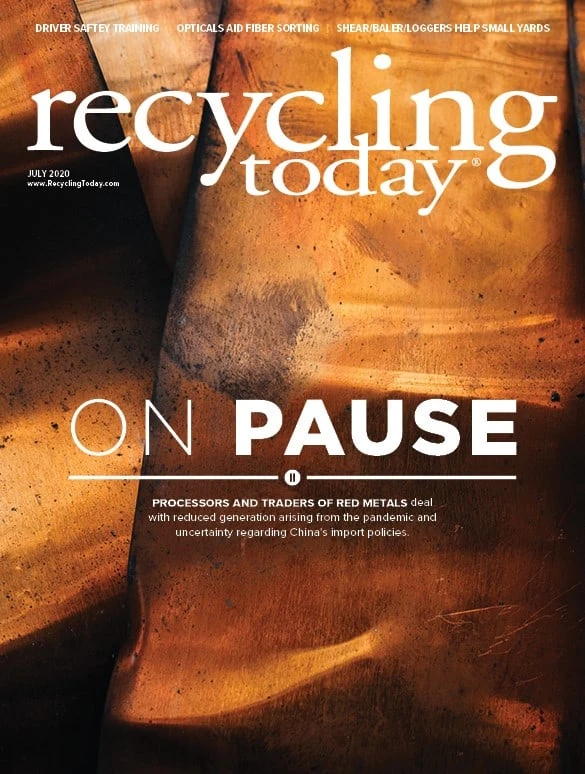
Explore the July 2020 Issue
Check out more from this issue and find your next story to read.
Latest from Recycling Today
- Research claims lower environmental impact for PE packaging over other materials
- Scrap metals included in emergency tariffs on Canada, Mexico
- OSC announces 2025 Packaging Innovation Award winners
- Tight supply poised to keep recycled steel prices buoyant
- Tariff reactions mixed, but reshoring advocates see positive signs
- AF&PA responds to tariffs on Canada, Mexico
- Wastequip appoints CFO
- Watercycle Technologies, Primobius partner on battery recycling