
Years ago, before the oil boom took over the prairies of western North Dakota, Will Chamley was a solitary businessman roaming the oil fields, renting power swivels and mud pumps for servicing cased oil wells.
“[The year] 2005 was a quiet time,” Chamley recalls. “Not much was going on. I started to see discarded scrap metal on the ground around the oil well sites and, looking for some additional income, I began to collect the material on weekends. I cut the scrap metal with a torch, put it in a small dump trailer and sold the iron. Eventually, it turned into a full-time job.”
The enterprising Chamley was able to recognize this opportunity because everyone else working in the area was so focused on oil that there was almost no interest in collecting garbage and scrap iron.
“There did not seem to be anyone who wanted to clean up job sites and remove the junk,” he says. “Nobody likes that type of work. My take, however, is that if there is money to be made, I am interested.”
Booming businesses

As the oil boom vaulted North Dakota up the rankings to become the second highest crude-oil-producing state in the United States, most businesses around the Williston area prospered—home builders, plumbers, electricians, restaurants, hotels, retail stores and equipment dealers. They, and others, all did very well as the oil flowed and workers flocked to the area. The population of Williston increased by 41 percent between April 2010 and 2013, climbing above 20,800 residents, according to the U.S. Census Bureau.
For comparison, the North Dakota Department of Mineral Resources reports that 252 wells were producing in the Bakken region of North Dakota in December 2005. Fast forward to December 2014, and the Bakken region had 8,944 wells producing more than 1 million barrels of crude oil daily. Even with the steep drop in crude oil prices, the number of wells eclipsed 9,000 in early 2015.
Away from the bright lights shining on all the spectacular economic growth, Chamley Pipe & Salvage, headquartered in Williston, North Dakota, was quietly building a profitable business cleaning up and recycling the oil industry’s scrap.
“When I started working here about four-and-a-half years ago, the company had five employees, two trucks and 20 roll-off containers,” says Mitchell Phillips, yard foreman for Chamley Pipe & Salvage. “Today the company has 50 employees, 15 trucks and 850 roll-off containers. That is almost exclusively the result of the oil industry and associated businesses.”
By constantly adapting and growing to meet the demands of the oil-related activities around Williston, Chamley Pipe & Salvage is picking up 10 to 20 loads of scrap metal and sometimes up to 20 to 30 loads of trash per day. Much of the material is dumped into the company’s open-top 20- and 30-yard roll-off containers or into Chamley’s 20-yard lid-style containers. The latter model is said to be suited to the disposal needs of “man camps,” where groups of men who work in the oil fields live together. About 50 percent of the company’s roll-offs haul scrap metal, while the other half collect garbage.
All the collected material is delivered to the company’s 10-acre site for processing, but Chamley says a new 40-acre lot is in the works. Scrap metal is the only material the company accepts from the public at its yard. Five Bobcat skid-steer loaders outfitted with attachments sort and move incoming material into different areas around the yard.
On the rails

Although Chamley Pipe & Salvage recycles almost everything it can, there is no doubt that scrap metal is the No. 1 material the company handles. “We typically handle 12,000 to 15,000 tons of scrap metal a year,” Chamley says. “That total will likely grow this year because we have a large job, chopping up 18 old drilling rigs.”
Once the scrap metal is cut into smaller pieces at the yard, it is put into special 15-ton-capacity roll-off containers for delivery to a railroad-loading site approximately 30 miles away. These are the same east-west tracks that run through North Dakota, hauling crude oil and agricultural crops. The tracks also carry Amtrak passenger trains.
While the travel distance for the containers of scrap metal is an inconvenience, the loading process has become more efficient this year with the addition of a new DX225MH-3 material handler from Doosan Infracore North America LLC, headquartered in Suwanee, Georgia. The 166-horsepower machine features an optional hydraulic 6.5-foot cab riser for enhanced operator visibility.
Chamley leases space from another company that has a rail spur off the main track. The outgoing scrap metal is placed in 90-ton piles until railcars are available. At that point, Phillips travels to the rail site to operate the material handler. He loads most of the 90 tons of iron that each car holds with a grapple attachment. He switches to a 48-inch magnet to clean up the remainder of the scrap metal on the ground. With both the grapple and magnet, Phillips has up to 35 feet and 5 inches of reach to efficiently load the railcars.
“The DX225MH-3 has made this job so much more efficient,” Phillips says. “Compared to the excavator with bucket and clamp I previously used, this machine grabs more material and holds it better. Because I can see into the railcar, I can do a better job of placement. I can identify gaps in the load and fill in material where needed. With the excavator, I relied on someone to guide me in positioning the scrap metal. Sometimes the lack of clear vision would cause me to stack the material above the railcar sides. That is not permitted, so I would have to spend time using the bucket on the excavator to pack it down.”
The time-wasting practices have been eliminated with the DX225MH-3.
“Everything is so simple,” Phillips says. “All I have to do is flip a switch to raise the cab in order to see right where I am placing material. It only takes a couple of hours to load a railcar.”
Chamley adds, “When Mitchell was loading the railcars with the excavator, he was sort of operating blind. The Doosan material handler makes his job 100 percent easier.”
Phillips and Chamley rate the DX225MH-3 high in operator comfort, easy-to-operate controls, cab design and fuel efficiency. “I can run it for 10 hours a day and barely use a quarter-tank of diesel fuel,” Phillips says.
More than scrap metal

The material handler also is used to load the company’s 700-horsepower wood chipper. Old pallets are turned into landscape mulch and livestock bedding. The material handler operator has a good view of what he is loading into the chipper and can spot unwanted items, such as metal.
Along with scrap metal and wood, Chamley also handles paper, plastic and pipe. The company sends the best old oil field pipe to the North Dakota state penitentiary, where inmates turn it into corral panels for farmers and ranchers. Chamley Pipe & Salvage markets those products on its website.
No end in sight
While falling oil prices have reduced the amount of drilling, the impact on Chamley Pipe & Salvage has been negligible.
“I think we have actually picked up more work as some firms move out of the area,” Phillips says. “They are cleaning up their sites, getting rid of trash and throwing away scrap metal. There is still plenty of production going on, and that means pulling out pipe, putting in new and redoing locations. All that is keeping us busy.”
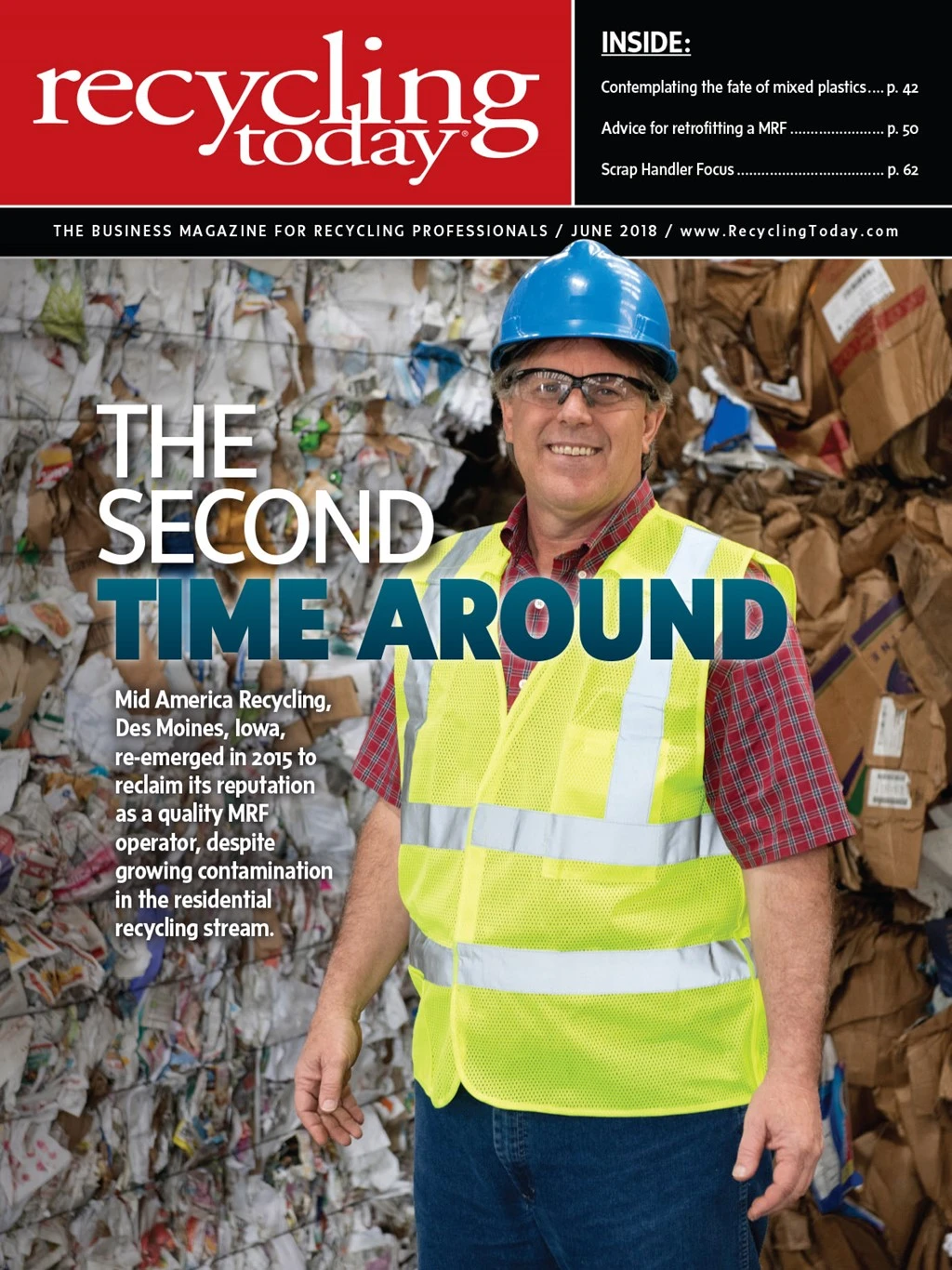
Explore the June 2018 Issue
Check out more from this issue and find your next story to read.
Latest from Recycling Today
- Lautenbach Recycling names business development manager
- Sebright Products partners with German waste management equipment company
- WasteExpo transitions to biennial format for enhanced experiences
- Study highlights progress, challenges in meeting PCR goals for packaging
- Washington legislature passes EPR bill
- PureCycle makes progress on use of PureFive resin in film trials
- New copper alloy achieves unprecedented high-temperature performance
- Gränges boosts profits and sales volume in Q1 2025