Companies that buy bales of plastic scrap to make recycled pellets have horror stories about what they’ve found in bales—concrete blocks, chunks of metal and even dead animals.
But most recyclers learn of trustworthy suppliers that provide acceptable bales needed to make recycled resin for their customers.
That seems like a workable business model, but a recent report commissioned by the Alliance to End Plastic Waste argues that model is broken because it does not include standards for bale and recycled pellet content.
Knowing what’s in a bale is necessary for recyclers to efficiently create flake or pellets that meet high-quality content standards. The recyclers’ current business model of mostly designing one bespoke resin for a specific customer instead of a resin that is standardized for a specific product holds back the use of recycled plastic, according to the report.
What is a good-quality bale? It must support the end use of the resin but might include knowing nonpolyolefin content, nonplastic content, moisture, color and level of impurities.
What is a quality pellet? It depends on the application, but characteristics may include ash content, density, filtration, melt index, moisture content, odor, pellet color, polyethylene or polypropylene content, flex modulus and tensile strength.
The study, which uses the European plastic recycling industry as an example, suggests if the industry can decide on specific recyclate standards for various applications, recyclers will have more customers and improved circularity.
What would such a strategy mean for U.S. recyclers? Scott Trenor, technical director at the Washington-based Association of Plastic Recyclers (APR), says transparency in the recycling marketplace benefits everyone, but there are problems with the model.
“If you go to recyclers’ websites, some have their material specifications listed and others just say, ‘Contact us,’” Trenor says. “That makes it difficult for purchasing agents and product designers to find suitable recycled content that meets their requirements. Meeting a universal standard for some recycled resin would depend on where the recycler is on the spectrum of reclaimers—one who takes bales and pelletizes the resin to those on the other end of the spectrum who take bales and compound the resin. It is easier to meet specifications for those on the blending and compounding side.”
He says recyclers who buy bales and process pellets might have difficulty meeting content specifications without investing in additional equipment, and adding specific requirements for resin content might give brand owners another reason not to use recycled content.
Is this proposed model just a solution looking for a problem? It has some of those characteristics. The study projects a 4 percent to 20 percent price improvement for recycled resin, which Trenor says probably would not pay for recyclers’ needed investment.
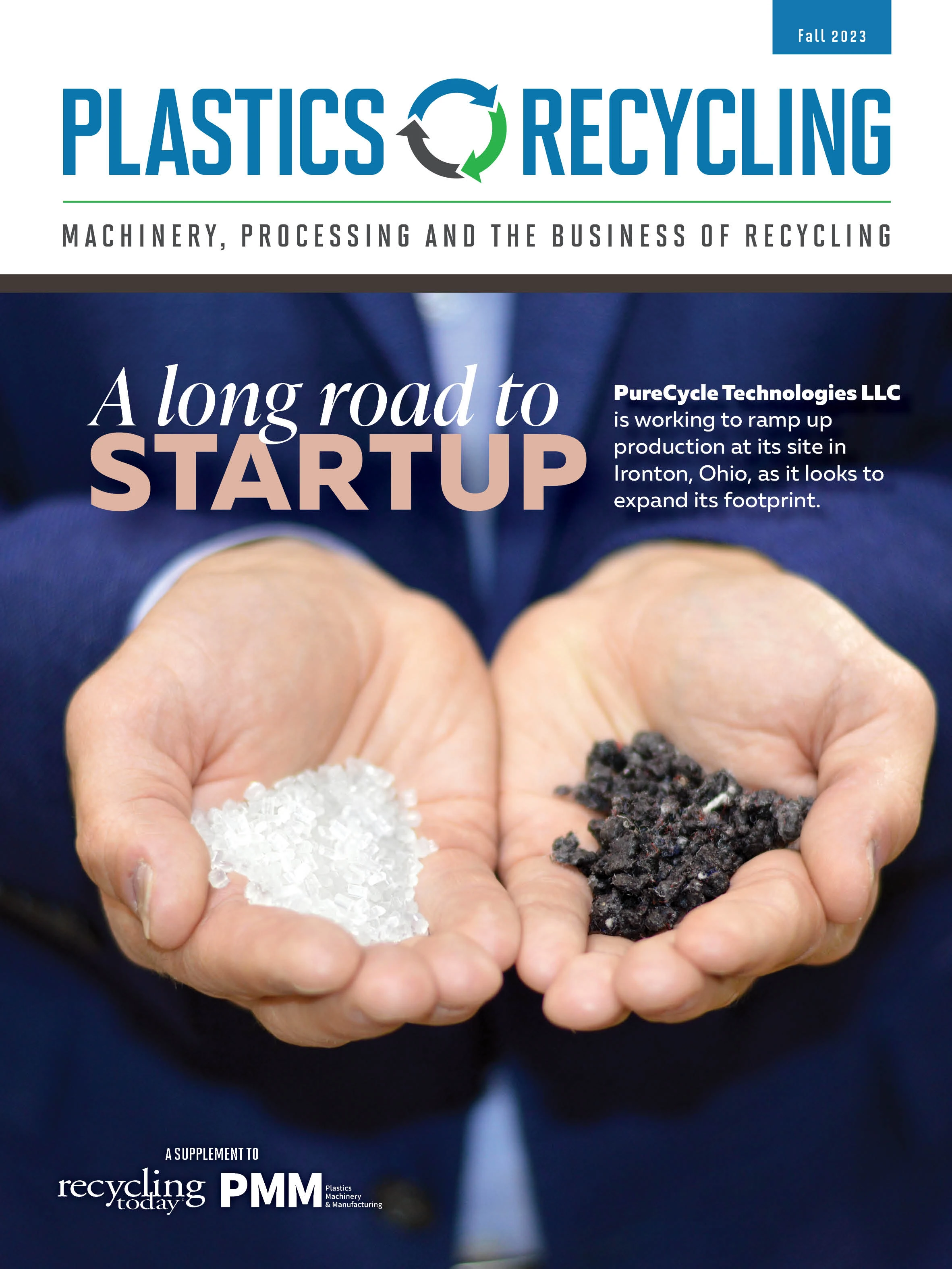
Explore the Fall 2023 Plastics Recycling Issue
Check out more from this issue and find your next story to read.
Latest from Recycling Today
- British Steel mill’s future up in the air
- Tomra applies GAINnext AI technology to upgrade wrought aluminum scrap
- Redwood Materials partners with Isuzu Commercial Truck
- The push for more supply
- ReMA PSI Chapter adds 7 members
- Joe Ursuy elected to NWRA Hall of Fame
- RRS adds to ownership team
- S3 Recycling Solutions acquires Electronics Recycling Solutions