_(1)_fmt.png)
Yerecic Label has been designing and manufacturing labels for the consumer goods, grocery and perishable foods industries since 1969. The company, based in New Kensington, Pennsylvania, just north of Pittsburgh, practices what it says is lean manufacturing, an ideal set forth by its founder, Art Yerecic Sr.
GOING LEAN
The company is now under the direction of Art’s son, Arthur M. Yerecic, who continues to uphold the values that were set forth by his father.
Yerecic Label defines lean manufacturing on its website as a systematic methodology for implementing rapid change through elimination of waste. “We continually examine our process looking at the seven types of waste (defects, overproduction, movement of materials, motion, waiting, inventory and overprocessing) found in organizations to be sure every process adds value to our customers,” the company’s website states.
Brian Hurst, Yerecic Label vice president of manufacturing, says the search to find a landfill alternative for the label backing began in 2010.
Yerecic Label’s 45,000-square-foot print facility was designed for lean, cellular manufacturing. Its presses are designed to reduce setup time and to make the company’s waste generation less than half of the industry average, according to the company.
In addition to high-tech presses equipped with a vision inspection system that scans every label to catch possible defects, including blemishes, missing print or registration issues, automatic roll changers keep the press running, eliminating downtime and reducing waste. Rewinders allow the company to print exact order quantities, eliminating overruns and underruns.
FINDING ALTERNATIVES
Yerecic has streamlined its production processes to reduce the volume of waste it generates; however, printed labels have a backing that remains once the labels are attached to a product. The company was sending hundreds of thousands of pounds of this material to the landfill each year because it could not be recycled.
Brian Hurst, Yerecic Label vice president of manufacturing, says the search to find a landfill alternative for the label backing began in 2010. “It was not an easy search,” he says. “When it comes to materials that we have in our industry, there are no local outlets for it.”
He describes the material as pressure-sensitive paper attached to a silicone-based liner. The backing material also contains acrylic and/or hot-melt adhesive.
Hurst finally found a home for this material at a cement kiln about 150 miles away from Yerecic’s New Kensington plant. The cement manufacturer uses the backing as a coal alternative in its kilns. According to Hurst, the label backing burns at a higher British thermal unit (Btu) rate than coal.
“The cement kilns burn it at such a high heat, it melts the material away and evaporates it,” he says.
The company is now shipping 126,000 pounds of material per month to the cement kiln—material that used to go to the landfill. Yerecic sends about one truckload every two weeks to the kiln, which Hurst says is on the other side of the state. Transportation costs are the largest expense of the program, which he says, costs more than landfilling the material.
Despite the extra cost, he says Yerecic Label is committed to keeping the label backing material out of the landfill.
“The alternative fuels program actually costs about 30 percent more than landfilling, but with the millennial generation so focused on environmental consciousness, it is not only the right thing to do for the environment, but it goes a long way with our associates,” Hurst says.
INVESTING IN CHANGE
_fmt.png)
To more efficiently transport the label backing material to the cement kiln, Yerecic decided to invest in a baler that could effectively process the material. The company purchased a ProPAK60 baler from Maren Engineering, South Holland, Illinois, which was delivered and installed in February 2013.
Michael Blais, regional sales manager for Maren, recalls the application and material being different from that of the company’s typical customers.
“The Maren equipment was installed for an application where the commodity was not going to be sold to a recycler,” he says. “Instead, the bales are being shipped to a company that is using them as waste to energy.”
The label matrix is a resilient material, and the size of the matrix rolls varied from 1 pound to 50 pounds.
“We wanted to design a baler with the structural integrity to hold up under the point loading stress common with label matrix,” Blais recalls.
_(1)_fmt.png)
“The customer had a learning curve of getting the proper mix of large and small rolls to make a more stable bale,” he adds.
To tie the bales, some of the wire positions require two strands of wire. Blais said the ProPAK60 was able to easily accommodate this requirement because it features an operator tie-off instruction screen. “The screen is specific to each programmed commodity and lets the operator know how many wire strands to use in each of the six positions,” he says.
In addition, Hurst says the baler’s shear blade was able to cut through the rolls without any issues.
Yerecic Label is producing 1.5 bales per hour and 4.5 bales per day using its ProPAK60 baler. Each bale averages 2,000 pounds.
Blais estimates the ProPAK60 could bale about 3 tons per hour of the material.
The company is now shipping 126,000 pounds of material per month to the cement kiln.
While Yerecic Label may not be saving on landfill costs by sending its baled label matrix material for energy recovery, its waste hauler is making fewer trips to the plant because the majority of waste in the company’s compactor previously was made up of this material.
Hurst says, ultimately, Yerecic Label would like to find an opportunity to recycle the material; but, for now, working with the cement kiln has been the best available option.
Hurst says the environmental initiatives at Yerecic Label are supported from the very top of the company down.
“Our goal is to leave something for the next generation,” he continues. “By engaging in our recycling practices, we’ve been able to engage our millennials to work here. When you see their excitement about it, it makes everybody want to do a better job at it.”
Get curated news on YOUR industry.
Enter your email to receive our newsletters.
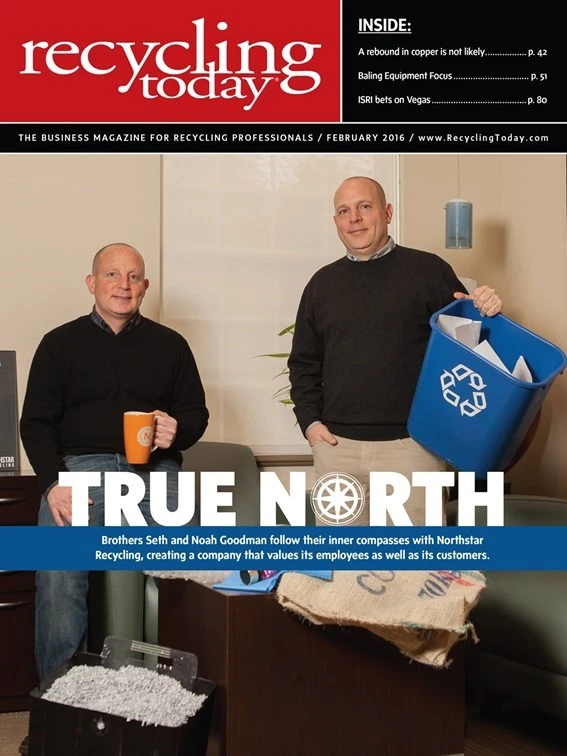
Explore the February 2016 Issue
Check out more from this issue and find your next story to read.
Latest from Recycling Today
- Recycled steel price crosses $500 per ton threshold
- Smithers report looks at PCR plastic’s near-term prospects
- Plastics association quantifies US-EU trade dispute impacts
- Nucor expects slimmer profits in early 2025
- CP Group announces new senior vice president
- APR publishes Design Guide in French
- AmSty recorded first sales of PolyRenew Styrene in 2024
- PRE says EU’s plastic recycling industry at a breaking point