
When it comes to egg cartons, there’s no question what comes first. Expanded polystyrene (EPS) foam has long been the material of choice for egg packaging. But, for one major egg supplier, outside-the-box thinking has led to both packaging improvements and to greater environmental sustainability.
Through a partnership between the egg processor and West Coast recycler Global Plastics, the 100 percent postconsumer polyethylene terephthalate (PET) Egg Package is now available to other egg sellers.
Buckeye, Arizona-based Hickman’s Family Farms processes between 36 million and 60 million eggs per week. The company depends on robotics to place its eggs in cartons, and flaws in the EPS and fiber cartons it was using hamstrung automation—a problem that inspired Hickman’s to look beyond the suppliers it was using.
“With California outlawing some of the foam in some of their cities now, we needed to look at a different type of carton,” says Jerry Hall, processing coordinator for Hickman’s.
With its need for perfectly identical cartons and a desire for more environmentally sustainable packaging, Hickman’s was receptive to proposals made by Global Plastics, a Perris, California, company that turns about 4 million bottles per day into packaging using in-house equipment.
“We wanted to get into the egg packaging business because we see an opportunity with [PS foam] going away,” says Dan Bahou, vice president of business development for Global Plastics. “So, we approached Hickman’s farms and said, ‘Hey, we would like to make an egg package out of recycled PET.’”
To create the new egg carton for Hickman’s made entirely from recycled PET (rPET), Global Plastics contributed a full spectrum of expertise—everything from recycling PET bottles to designing a mold for the new carton to thermoforming the final product.
“Global Plastics would make a prototype, and we would take it out to their facility, and we would test it,” Bahou says, explaining that the two companies collaborated to be sure the trial cartons worked well with Hickman’s automation.
He continues, “And we’d go through the whole thing and we’d go, ‘OK. There’s a small issue with de-nesting here, the hinge isn’t closing quite right, the locks aren’t perfect,’ and so we would go back to the drawing board, and we would make some changes.”
The entire process took many iterations over a couple years, Bahou adds.
“There’s a number of issues associated with PET and their [carton filling] equipment,” Bahou says. “Eggs are heavy. PET is sort of a lightweight item,” he adds.
Production of the carton begins on Global Plastics’ PET recycling lines.
Every day, the company accepts bales of millions of bottles from California’s buy-back program. It sorts, grinds and washes the bottles, with a portion of green bottles going toward eventual production of green-tinted egg cartons. The company also uses brown bottles to some degree for production of brown-tinted egg cartons.
Machinery maker Amut Group, Novara, Italy, supplied most of Global Plastics’ recycling equipment, including its filters, wash lines and extruders, as well as the thermoforming machinery it uses for making packaging.
“On the washing side, what we’ve had to do is we’ve had to boost some new technology in the processes in general,” says Anthony Georges, the president of Amut North America, Vaughan, Ontario.
He adds that the equipment includes a turbo washer “to remove a lot more of the glass and inorganic elements that we now find in the bales.”
“As people stop the ability to use foam, they have to have an alternative. It’s really going to be PET or pulp.” – Dan Bahou, vice president of business development for Global Plastics
The clean PET flakes are then pelletized, using non-Amut equipment, and ready to be extruded into sheet for thermoforming. The process complies with direct-food-contact certifications.
To make the egg cartons, Global Plastics uses an ACF920 thermoformer from Amut.
“Global Plastics takes the bottle and recycles it all the way to the finished product,” Bahou says. “We are one of a few in North America vertically integrated all the way with that capability.”
The Amut thermoformer’s EASY advanced software, combined with a plug-assist option, allows continuous control during all thermoforming phases for the right material distribution—key for making egg cartons with identical, predictable characteristics.
Bahou says Global Plastics now produces most of Hickman’s egg cartons, but Hickman’s also has acquired a thermoformer to produce some itself, using sheet it purchases from Global Plastics.
It takes three bottles to make one 12-count egg carton and four bottles for an 18-count egg pack. A 24-count egg container requires five bottles.
“It’s a great solution to this issue. It’s a great cost solution, as well, since it’s recycled PET,” Bahou says. “It can’t compete with foam identically, right? But it can get pretty close to pulp.”
He adds, “As people stop the ability to use foam, they have to have an alternative. It’s really going to be PET or pulp.”
Hall says the carton changeover has made packaging eggs easier “because we’re able to tune the machinery to a much more stable type of carton. It doesn’t tend to bow or flex, or it doesn’t matter how it dries.”
It’s a move that’s made sense for Hickman’s. “We need to be into the PET,” Hall says. “And we’re able to tell the recycling story with it. The Costcos, the Walmarts, the big-name players in our industry really like the story of the recycled PET carton.”
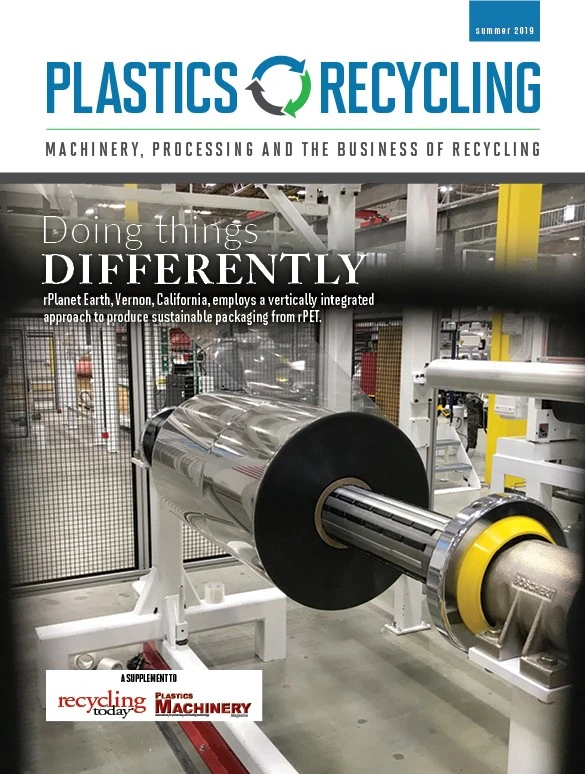
Explore the June 2019 Plastics Recycling Issue
Check out more from this issue and find your next story to read.
Latest from Recycling Today
- Aqua Metals secures $1.5M loan, reports operational strides
- AF&PA urges veto of NY bill
- Aluminum Association includes recycling among 2025 policy priorities
- AISI applauds waterways spending bill
- Lux Research questions hydrogen’s transportation role
- Sonoco selling thermoformed, flexible packaging business to Toppan for $1.8B
- ReMA offers Superfund informational reports
- Hyster-Yale commits to US production